Hotline
+86-136 8495 9862
Email:cennia@szmizhi.com
Add::104,Building 27,Third Industrial Zone, Longxi Community,Longgang District,Shenzhen,China.
Coil Forming & Handling Equipment
Surface Treatment Equipment
Solutions
Application
About Us
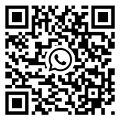
Welcome to MIZHI
For consultation/feedback, please call the service hotline: +86-136 8495 9862 Email:cennia@szmizhi.com
1. Introduction
In the complex and highly competitive world of metal processing, the Fagor slitting line has emerged as a remarkable solution, setting new standards for efficiency, precision, and reliability. Fagor, a well - respected name in the manufacturing technology domain, has engineered its slitting lines to meet the diverse and exacting demands of industries that rely on the transformation of large - width metal coils into precisely slit narrow strips. These industries span from automotive manufacturing, where precision - cut metal components are crucial for vehicle safety and performance, to the construction sector, which requires accurately sized metal sheets for roofing, siding, and structural applications. The Fagor slitting line represents a blend of advanced engineering, innovative technology, and a deep understanding of customer needs, making it a cornerstone in modern metal - processing operations.
2. Technical Components and Working Mechanism
2.1 Decoiling System
The Fagor slitting line commences its operation with a state - of - the - art decoiling system. This system is designed to handle a wide range of metal coil sizes and weights with utmost precision. It features a robust expandable mandrel that firmly grips the inner diameter of the coil. The mandrel is powered by high - torque motors, which are controlled by an advanced drive system. This drive system allows for smooth and adjustable decoiling speeds, ensuring a consistent and stable feed of the metal strip into the subsequent processing stages. For example, in the processing of thin - gauge steel coils used in the electronics industry, the decoiling system can precisely control the unwinding speed to prevent any stretching or wrinkling of the delicate metal strip. The decoiling unit also incorporates advanced tension control mechanisms. These mechanisms monitor and adjust the tension in the metal strip as it is unwound, maintaining optimal tension levels throughout the decoiling process. This is crucial as inconsistent tension can lead to defects in the slit strips, such as waviness or uneven widths.
2.2 Leveling and Straightening Section
After the metal strip is decoiled, it often has some inherent curvature or irregularities due to the coiling process. The Fagor slitting line's leveling and straightening section is specifically engineered to eliminate these imperfections. This section consists of a series of precision - ground rolls arranged in a carefully designed pattern. The rolls are made from high - quality, wear - resistant materials, ensuring long - term performance and accuracy. As the metal strip passes through the leveling rolls, they apply a controlled amount of pressure to gradually flatten and straighten the strip. The number of rolls and the pressure applied can be adjusted according to the thickness and type of the metal being processed. For instance, when processing thick - gauge aluminum coils for the construction industry, the leveling section can be configured to apply higher pressure to effectively straighten the stiff metal strip. The straightening process is not only about making the strip flat but also about ensuring that it has a consistent cross - sectional shape, which is essential for accurate slitting.
2.3 Slitting Section
The slitting section is the heart of the Fagor slitting line, where the actual cutting of the metal strip into narrower strips takes place. This section is equipped with high - precision circular slitting knives. These knives are made from premium - grade tool steel, heat - treated to achieve exceptional hardness and wear resistance. The knives are mounted on precisely machined arbors, and the distance between the knives can be adjusted with great accuracy. Fagor uses advanced digital control systems to manage the knife - setting process. Operators can input the desired strip widths into the control panel, and the system automatically adjusts the positions of the knives. This ensures that the slitting process is highly precise, with the ability to achieve very tight tolerances. For example, in the production of metal strips for the automotive stamping industry, the Fagor slitting line can slit metal coils into strips with width tolerances of ±0.1mm or even less. The slitting section also features a high - speed cutting mechanism, which allows for efficient processing of large volumes of metal. The cutting speed can be adjusted according to the thickness and type of the metal, ensuring optimal cutting performance and quality.
2.4 Scrap Rewinding and Strip Winding Units
As the metal strip is slit, the scrap material (the narrow strips that are not part of the final product) needs to be efficiently removed. The Fagor slitting line's scrap rewinding unit is designed to handle this task with ease. It quickly and neatly winds up the scrap into a coil, which can be easily disposed of or recycled. The strip winding units, on the other hand, are responsible for winding the slit strips into individual coils. These units are equipped with advanced tension control systems to ensure that the coils are wound tightly and evenly. The tension control is crucial as it affects the quality of the wound coils. If the tension is too high, the strip may be stretched or damaged; if it is too low, the coils may be loose and prone to tangling. The Fagor strip winding units can precisely adjust the tension based on the characteristics of the metal strip, ensuring high - quality coil winding.
3. Applications across Diverse Industries
3.1 Automotive Industry
In the automotive industry, the Fagor slitting line plays a vital role in the production of various components. Metal strips are used for manufacturing car body panels, engine parts, and chassis components. For car body panels, such as doors, hoods, and trunk lids, the Fagor slitting line provides the precision - cut metal strips required for stamping operations. The accurate widths and straight edges of the slit strips ensure that the stamped panels fit together perfectly during the assembly process. This not only improves the aesthetics of the vehicle but also enhances its structural integrity and safety. In the production of engine parts, such as cylinder heads and engine blocks, the Fagor slitting line cuts metal strips for the manufacturing of gaskets and other small components. The high - precision slitting ensures that these components have the correct dimensions, which is crucial for the proper functioning of the engine.
3.2 Construction Industry
The construction industry is another major beneficiary of the Fagor slitting line. Metal sheets are used extensively for roofing, siding, and structural components. For roofing applications, the Fagor slitting line can cut metal coils into strips of the exact width required for different roofing systems. This ensures a proper fit and reduces the need for on - site cutting and adjustments. In the case of siding, the precise slitting allows for the production of uniform - sized metal strips that can be easily installed to create a smooth and aesthetically pleasing exterior. For structural components, such as steel beams and columns, the Fagor slitting line can cut metal strips that are further processed into channels, angles, and other profiles. The accuracy of the slitting process contributes to the overall strength and stability of the construction structures.
3.3 Electrical and Electronics Industry
In the electrical and electronics industry, the Fagor slitting line is used for the production of components such as electrical enclosures, circuit boards, and connectors. For electrical enclosures, the slitting line cuts metal strips to the required widths for forming the enclosures. The precise slitting ensures that the enclosures have a tight - fitting and secure design, protecting the electrical components inside. In the production of circuit boards, the Fagor slitting line cuts metal strips for the manufacturing of conductive traces and other components. The high - precision slitting is essential for ensuring the proper electrical conductivity and functionality of the circuit boards. For connectors, the slitting line cuts metal strips into narrow widths that are used to make the contact points. The accuracy of the slitting process ensures that the connectors have a reliable and consistent connection.
4. Advantages of Fagor Slitting Lines
4.1 High Precision
One of the most significant advantages of the Fagor slitting line is its exceptional precision. The advanced control systems, high - quality components, and precise machining of the slitting line enable it to achieve extremely tight tolerances. This precision is crucial for industries where even the slightest deviation in the width of the slit strips can lead to significant problems. For example, in the aerospace industry, where metal components need to meet strict quality and safety standards, the Fagor slitting line's precision ensures that the slit metal strips used for manufacturing aircraft parts have the exact dimensions required. The high - precision slitting also reduces the need for secondary processing, such as trimming or re - sizing, which saves time and cost.
4.2 High - Speed Processing
Fagor slitting lines are designed for high - speed processing, allowing for efficient production of large volumes of slit metal strips. The powerful motors, advanced drive systems, and optimized cutting mechanisms enable the slitting line to operate at high speeds without sacrificing quality. This is especially important for industries with high - volume production requirements, such as the automotive and construction industries. For example, in a large - scale automotive manufacturing plant, the Fagor slitting line can quickly process metal coils into the required slit strips, keeping up with the production pace of the assembly lines. The high - speed processing also reduces the overall production time, enabling companies to bring their products to market faster.
4.3 Versatility
The Fagor slitting line is highly versatile, capable of handling a wide range of metal types, thicknesses, and widths. Whether it's processing thin - gauge aluminum for the packaging industry, thick - gauge steel for the heavy - machinery industry, or copper for the electrical industry, the Fagor slitting line can adjust its parameters to achieve optimal slitting results. The adjustable knife - setting mechanism and the flexible control systems allow for easy adaptation to different production requirements. This versatility makes the Fagor slitting line suitable for a diverse range of industries and applications, providing a single - solution for various metal - slitting needs.
4.4 Reliability and Durability
Fagor is known for its commitment to quality, and its slitting lines are built to last. The use of high - quality materials, robust construction, and rigorous quality control processes ensure the reliability and durability of the slitting line. The components, such as the motors, drives, rolls, and knives, are designed to withstand the harsh operating conditions of the metal - processing industry. This reduces the frequency of breakdowns and maintenance requirements, resulting in lower downtime and higher productivity. For example, in a continuous - operation metal - processing plant, the reliability of the Fagor slitting line ensures that the production process can run smoothly for long periods without interruptions, maximizing the plant's output.
5. Challenges and Solutions in Implementing Fagor Slitting Lines
5.1 Initial Investment and Cost - Benefit Analysis
One of the challenges in implementing a Fagor slitting line is the relatively high initial investment. The advanced technology and high - quality components of the slitting line come at a cost. However, companies need to conduct a comprehensive cost - benefit analysis. While the upfront cost may be significant, the long - term benefits, such as increased productivity, reduced waste, and higher - quality products, can outweigh the initial investment. For example, the high - precision slitting of the Fagor slitting line reduces material waste, which can result in substantial cost savings over time. Additionally, the high - speed processing capabilities can increase the production output, leading to higher revenues. Fagor also offers various financing options and after - sales support to help companies manage the initial investment.
5.2 Operator Training and Skill Requirements
Operating a Fagor slitting line requires a certain level of technical skills and knowledge. The advanced control systems and complex machinery need to be operated by trained personnel. Fagor addresses this challenge by providing comprehensive operator training programs. These programs cover everything from basic machine operation to advanced troubleshooting and maintenance. The training is often hands - on, allowing operators to gain practical experience with the slitting line. Fagor also provides ongoing technical support and updates to ensure that operators are up - to - date with the latest features and technologies of the slitting line.
5.3 Integration with Existing Production Systems
Integrating a Fagor slitting line into an existing production system can be a complex task. The slitting line needs to be compatible with other equipment, such as coil handling systems, downstream processing machinery, and quality control systems. Fagor works closely with its customers to ensure seamless integration. The company's engineers conduct site surveys and analyze the existing production processes to develop customized integration solutions. Fagor also uses standard communication protocols and interfaces in its slitting lines, making it easier to integrate with other equipment.
6. Future Developments and Trends for Fagor Slitting Lines
The future of Fagor slitting lines lies in increased智能化和自动化. Fagor is likely to incorporate more advanced artificial intelligence (AI) and machine learning (ML) algorithms into its slitting lines. These technologies can enable real - time monitoring of the slitting process, predictive maintenance, and automatic adjustment of cutting parameters based on the characteristics of the incoming metal coils. For example, AI - powered sensors can detect any anomalies in the metal strip, such as thickness variations or surface defects, and automatically adjust the slitting process to compensate for these issues. Automated material handling systems can also be integrated into the slitting line, further reducing the need for manual labor and increasing productivity.
6.2 Sustainable and Environmentally Friendly Features
As environmental concerns become more prominent, Fagor is expected to develop sustainable and environmentally friendly features for its slitting lines. This may include the use of energy - efficient motors and drives, recycling systems for scrap materials, and the reduction of lubricant and coolant usage. For example, Fagor could develop a closed - loop coolant system that recycles and purifies the coolant used in the slitting process, reducing the environmental impact and the cost of coolant disposal. The company may also focus on using more sustainable materials in the construction of the slitting line.
6.3 Expansion into New Markets and Applications
Fagor may explore new markets and applications for its slitting lines. With the growth of emerging industries, such as renewable energy and 3D printing, there is a potential demand for slitting lines that can process new types of materials, such as solar - grade silicon and metal powders for 3D printing. Fagor can leverage its expertise in metal processing to develop slitting lines that can meet the unique requirements of these emerging industries. This expansion into new markets can help Fagor diversify its business and increase its market share.
In conclusion, the Fagor slitting line is a remarkable piece of equipment that has made a significant impact in the metal - processing industry. Its high precision, high - speed processing, versatility, and reliability have made it a preferred choice for industries around the world. While there are challenges in implementing and operating Fagor slitting lines, the company's commitment to providing solutions and support ensures that these challenges can be overcome. As technology continues to evolve, Fagor slitting lines are likely to play an even more important role in the future of metal processing, driving innovation and productivity in the industry.