Hotline
+86-136 8495 9862
Email:cennia@szmizhi.com
Add::104,Building 27,Third Industrial Zone, Longxi Community,Longgang District,Shenzhen,China.
Coil Forming & Handling Equipment
Surface Treatment Equipment
Solutions
Application
About Us
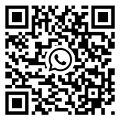
Welcome to MIZHI
For consultation/feedback, please call the service hotline: +86-136 8495 9862 Email:cennia@szmizhi.com
I. Introduction
In the world of surface preparation and restoration, the floor shot blaster has emerged as a powerful and indispensable tool. Whether it's for removing old coatings, roughening smooth surfaces, or preparing floors for new finishes, a floor shot blaster offers efficiency, precision, and durability. In this in-depth exploration, we will delve into the various aspects of floor shot blasters, including their history, types, features, benefits, applications, and maintenance.
II. History and Evolution of Floor Shot Blasters
The concept of using abrasive materials to clean and prepare surfaces dates back centuries. However, it wasn't until the early 20th century that mechanical shot blasting machines were developed for industrial applications. Initially, these machines were large and cumbersome, primarily used in shipyards and heavy industries.
Over time, advancements in technology led to the development of more compact and versatile floor shot blasters. These machines became popular in the construction and renovation industries, as they offered a faster and more effective alternative to traditional surface preparation methods such as sanding and grinding.
Today, floor shot blasters come in a wide range of sizes and configurations, from small portable units to large industrial machines. They are equipped with advanced features such as adjustable blasting pressure, variable speed controls, and dust collection systems, making them highly efficient and user-friendly.
III. Types of Floor Shot Blasters
There are several types of floor shot blasters available in the market, each designed for specific applications and surface types. Some of the common types include:
1. Walk-Behind Shot Blasters: These are small to medium-sized machines that can be operated by a single person. They are ideal for smaller areas or areas with limited access, such as corners and tight spaces. Walk-behind shot blasters are typically equipped with a handle for easy maneuverability and control.
2. Ride-On Shot Blasters: Larger and more powerful than walk-behind models, ride-on shot blasters are designed for large-scale surface preparation projects. These machines offer higher productivity and can cover large areas quickly. They are often used in industrial settings, warehouses, and parking garages.
3. Portable Shot Blasters: As the name suggests, portable shot blasters are lightweight and easy to transport. They are suitable for on-site jobs where mobility is essential. Portable shot blasters can be used on a variety of surfaces, including concrete, wood, and metal.
4. Automated Shot Blasters: These are highly advanced machines that are controlled by computer programs. They offer precise and consistent surface preparation, making them ideal for applications where uniformity is crucial, such as in the manufacturing of industrial floors.
IV. Features and Components of Floor Shot Blasters
A typical floor shot blaster consists of several key components that work together to achieve effective surface preparation. These components include:
1. Abrasive Media: The abrasive media is the material used to blast the surface. It can be made of steel shot, steel grit, sand, or other materials, depending on the surface type and the desired finish. The abrasive media is stored in a hopper and is fed into the blasting chamber through a metering device.
2. Blast Wheel: The blast wheel is the heart of the floor shot blaster. It consists of a rotating wheel with vanes that pick up the abrasive media and accelerate it to high speeds. The blast wheel projects the abrasive media onto the surface, removing old coatings, dirt, and other contaminants.
3. Dust Collection System: Floor shot blasters generate a significant amount of dust and debris during operation. A dust collection system is essential to capture and remove this dust, ensuring a clean and safe working environment. Dust collection systems can range from simple vacuum attachments to more complex integrated systems with filters and separators.
4. Control Panel: The control panel allows the operator to adjust various parameters of the shot blasting process, such as blasting pressure, feed rate, and speed. It also provides information on the machine's status and performance.
5. Mobility System: Depending on the type of floor shot blaster, it may be equipped with wheels, tracks, or skids for easy movement and positioning. Mobility is crucial for efficient surface preparation, as it allows the operator to access different areas of the work site without having to constantly move the machine manually.
V. Benefits of Using Floor Shot Blasters
There are several significant benefits to using floor shot blasters for surface preparation:
1. Efficient Surface Preparation: Floor shot blasters can quickly and effectively remove old coatings, rust, dirt, and other contaminants from floors. They offer a much faster alternative to traditional surface preparation methods, saving time and labor costs.
2. Improved Adhesion: By roughening the surface, floor shot blasters create a profile that enhances the adhesion of new coatings and finishes. This results in a more durable and long-lasting bond, reducing the risk of peeling and delamination.
3. Versatility: Floor shot blasters can be used on a wide variety of surfaces, including concrete, wood, metal, and asphalt. They can also handle different types of coatings and contaminants, making them a versatile tool for various applications.
4. Cost-Effective: Although the initial investment in a floor shot blaster may be higher than traditional surface preparation methods, the long-term cost savings can be significant. Floor shot blasters reduce the need for manual labor, minimize waste, and improve the quality of the finished surface, resulting in lower overall costs.
5. Environmentally Friendly: Many modern floor shot blasters are equipped with dust collection systems that capture and filter the dust generated during operation. This reduces dust emissions and makes the process more environmentally friendly. Additionally, by removing old coatings and contaminants, floor shot blasters can help reduce the amount of waste sent to landfills.
VI. Applications of Floor Shot Blasters
Floor shot blasters are used in a wide range of applications across different industries. Some of the common applications include:
1. Concrete Floor Preparation: Floor shot blasters are widely used in the preparation of concrete floors for coatings, overlays, and polishing. They can remove old coatings, sealers, and contaminants, creating a clean and rough surface that is ideal for adhesion. Concrete floor shot blasting is commonly used in warehouses, factories, parking garages, and commercial buildings.
2. Rust and Paint Removal: In industrial settings, floor shot blasters are used to remove rust and old paint from metal floors and surfaces. This helps to prevent corrosion and extends the lifespan of the structure. Floor shot blasting is also used in the restoration of historical buildings and structures where traditional methods may damage the substrate.
3. Wood Floor Refinishing: Floor shot blasters can be used to strip old finishes and prepare wood floors for refinishing. They offer a more efficient and less labor-intensive alternative to sanding, especially for large areas. Wood floor shot blasting is popular in residential and commercial settings.
4. Asphalt Surface Preparation: In the construction and maintenance of asphalt pavements, floor shot blasters are used to clean and roughen the surface before applying new coatings or overlays. This improves the adhesion and durability of the new layer, extending the lifespan of the pavement.
5. Industrial Cleaning: Floor shot blasters can be used for general industrial cleaning tasks, such as removing oil, grease, and dirt from floors and surfaces. They are particularly useful in areas where traditional cleaning methods are ineffective or time-consuming.
VII. How to Choose the Right Floor Shot Blaster
When choosing a floor shot blaster, there are several factors to consider to ensure that you select the right machine for your specific needs. Some of the key factors include:
1. Surface Type and Size: Consider the type of surface you will be working on and its size. Different floor shot blasters are designed for different surface types and sizes, so make sure to choose a machine that is suitable for your application. For example, a large ride-on shot blaster may be more appropriate for a warehouse floor, while a portable unit may be better for a small residential project.
2. Blasting Media: Determine the type of abrasive media you will be using. Different media have different properties and are suitable for different surface types. Consider factors such as hardness, size, and cost when choosing the blasting media.
3. Productivity Requirements: Consider your productivity requirements and the amount of work you need to complete. Larger machines generally offer higher productivity, but they may also be more expensive and difficult to maneuver. Consider your budget and the time available for the project when choosing a floor shot blaster.
4. Dust Collection System: A good dust collection system is essential for a clean and safe working environment. Look for a floor shot blaster with an effective dust collection system that can capture and filter the dust generated during operation. Consider the type of filters used and the capacity of the dust collector.
5. Brand and Reputation: Choose a floor shot blaster from a reputable brand with a proven track record of quality and reliability. Read reviews and ask for recommendations from other professionals in the industry to ensure that you are getting a high-quality machine.
VIII. Maintenance and Care of Floor Shot Blasters
Proper maintenance and care are essential to ensure the longevity and optimal performance of your floor shot blaster. Here are some tips for maintaining your machine:
1. Regular Cleaning: Clean the machine after each use to remove dust, debris, and abrasive media. Use a pressure washer or compressed air to clean the blast wheel, hopper, and dust collection system.
2. Inspect Components: Regularly inspect the machine's components for signs of wear and damage. Check the blast wheel vanes, bearings, belts, and filters for wear and replace them as needed. Inspect the hoses and connections for leaks and tighten them if necessary.
3. Lubrication: Lubricate the machine's moving parts according to the manufacturer's instructions. Use a high-quality lubricant to reduce friction and wear and extend the life of the components.
4. Store Properly: When not in use, store the floor shot blaster in a dry, clean location. Cover it to protect it from dust and moisture. Store the abrasive media in a sealed container to prevent moisture absorption.
5. Follow Manufacturer's Instructions: Always follow the manufacturer's instructions for operation, maintenance, and safety. This will help ensure that you are using the machine correctly and safely and that you are performing the necessary maintenance tasks.
IX. Safety Considerations When Using Floor Shot Blasters
Using a floor shot blaster can be a potentially hazardous activity if proper safety precautions are not taken. Here are some safety considerations to keep in mind:
1. Personal Protective Equipment: Wear appropriate personal protective equipment, such as safety glasses, ear protection, a dust mask, and protective clothing. This will help protect you from flying debris, dust, and noise.
2. Training and Certification: Ensure that you are properly trained and certified to operate the floor shot blaster. Follow all safety procedures and guidelines provided by the manufacturer and your employer.
3. Ventilation: Provide adequate ventilation in the work area to remove dust and fumes. Use fans or exhaust systems to ensure good air circulation.
4. Electrical Safety: Check the electrical connections and cords for damage before using the machine. Use a ground fault circuit interrupter (GFCI) to protect against electrical shocks.
5. Machine Maintenance: Regularly inspect and maintain the floor shot blaster to ensure that it is in good working condition. Report any safety issues or malfunctions immediately.
X. Future Trends in Floor Shot Blasting Technology
The field of floor shot blasting technology is constantly evolving, with new advancements and innovations emerging to meet the changing needs of the industry. Some of the future trends in floor shot blasting technology include:
1. Automation and Robotics: As technology advances, we can expect to see more automated and robotic floor shot blasters that can perform complex tasks with precision and efficiency. These machines will be able to navigate autonomously, adjust blasting parameters based on surface conditions, and communicate with other equipment and systems.
2. Green Technology: There is a growing demand for environmentally friendly floor shot blasting solutions that reduce dust emissions, consume less energy, and use sustainable abrasive media. We can expect to see the development of new technologies and materials that address these concerns.
3. Digitalization and Connectivity: Floor shot blasters may become more connected and integrated with digital technologies, allowing for remote monitoring, diagnostics, and optimization. This will improve productivity, reduce downtime, and enhance safety.
4. Customization and Specialization: As industries become more specialized, there will be a need for floor shot blasters that can be customized to meet specific surface preparation requirements. This may include machines with unique features and capabilities for specific applications, such as curved surfaces or delicate substrates.
XI. Conclusion
In conclusion, floor shot blasters are powerful tools for surface preparation that offer many benefits, including efficiency, precision, and durability. Whether you are working on a large industrial project or a small residential renovation, a floor shot blaster can help you achieve a clean and smooth surface for your new coating or finish. By understanding the different types of floor shot blasters, their features, benefits, and applications, you can choose the right machine for your specific needs and ensure that you are using it safely and effectively. With the continued evolution of floor shot blasting technology, we can expect to see even more advanced and efficient machines in the future, making surface preparation easier and more sustainable than ever before.
Guyson Shot Blaster
I. Introduction
The Guyson shot blaster is a prominent and reliable piece of equipment within the realm of surface preparation and finishing. It has earned a solid reputation for its ability to transform various surfaces with precision and efficiency. This comprehensive examination will explore the Guyson shot blaster in detail, covering its operational principles, diverse models, essential components, wide - ranging applications, notable advantages, and crucial maintenance practices.
II. Operational Principles of the Guyson Shot Blaster
1.
Shot Blasting Mechanics
At the heart of the Guyson shot blaster's operation is the shot blasting process. It involves the acceleration of small, abrasive media particles, often referred to as shot, towards the target surface. These particles are typically made from materials like steel grit, aluminum oxide, or glass beads, depending on the specific application requirements. The shot is propelled by a powerful mechanism within the blaster. When the abrasive shot impacts the surface, it imparts kinetic energy, which effectively removes unwanted substances such as rust, old paint, scale, and contaminants. This mechanical action also serves to roughen or texture the surface, preparing it for subsequent processes like painting, coating, or bonding.
2.
Abrasive Media Control and Delivery
Guyson shot blasters are engineered with sophisticated abrasive media control and delivery systems. The abrasive is stored in a hopper or reservoir within the equipment. From there, it is precisely metered and delivered to the blasting chamber or nozzle. The control mechanisms ensure that the flow rate of the abrasive is consistent and adjustable. This allows operators to tailor the intensity of the shot blasting according to the nature of the surface and the desired level of preparation. For instance, a delicate surface might require a lower abrasive flow rate to avoid over - blasting, while a heavily contaminated or corroded surface may need a higher flow for effective cleaning.
3.
Surface Coverage and Uniformity
To achieve a high - quality surface finish, the Guyson shot blaster is designed to provide excellent surface coverage and uniformity. The blasting nozzles and the overall design of the equipment are optimized to ensure that the abrasive shot is distributed evenly across the target area. The angle and orientation of the nozzles, along with the movement patterns of the blaster (in the case of automated or mobile models), are carefully calibrated. This results in a uniform removal of material from the surface, eliminating the risk of creating uneven patches or leaving behind areas with insufficient preparation. The ability to maintain consistent surface coverage is crucial for applications where the adhesion of coatings or the performance of subsequent processes depends on a uniform substrate.
III. Components of the Guyson Shot Blaster
1.
Blasting Cabinet (in Cabinet - type Models)
In cabinet - type Guyson shot blasters, the blasting cabinet is a key component. It provides a contained environment for the shot blasting process. The cabinet is usually made from heavy - duty materials to withstand the impact of the abrasive shot. It has access doors or openings that allow for loading and unloading of the workpieces. The interior of the cabinet is lined with wear - resistant materials to protect the structure from the abrasive action. The cabinet also features viewing windows or lights to enable operators to monitor the blasting process without interrupting it. Additionally, it has a dust collection port to remove the debris and used abrasive from the cabinet during operation.
2.
Nozzles and Blast Guns
The nozzles and blast guns are integral to the Guyson shot blaster's functionality. The nozzles are designed to direct the flow of abrasive shot onto the surface with precision. They are often made from durable materials such as carbide or ceramic to withstand the abrasive wear. The shape and size of the nozzles can vary depending on the model and the specific application. Blast guns, which hold the nozzles, are ergonomically designed for comfortable handling, especially in handheld or semi - automated models. The blast guns may have features like adjustable air pressure or abrasive flow controls to provide operators with greater control over the blasting process.
3.
Abrasive Media Handling System
The abrasive media handling system consists of several components. The abrasive hopper, as mentioned earlier, stores the abrasive media. It is equipped with level sensors to ensure that there is an adequate supply of abrasive during operation. From the hopper, the abrasive is transported to the nozzles via a conveyor system or pneumatic tubes in some models. There are also sieving or filtering mechanisms within the system to remove any debris or oversized particles from the abrasive before it reaches the nozzles. This helps to maintain the quality of the abrasive and the effectiveness of the shot blasting.
4.
Dust Collection and Filtration System
A robust dust collection and filtration system is an essential part of the Guyson shot blaster. During the shot blasting process, a significant amount of dust and debris is generated. The dust collection system uses powerful fans or vacuum pumps to draw the dust - laden air from the blasting area. The air then passes through a series of filters, such as cartridge filters or bag filters, which trap the dust particles. The filtered air is either recirculated back into the working environment or exhausted outside, depending on the design of the system. This not only keeps the working area clean but also protects the health of the operators and ensures the proper functioning of the equipment by preventing dust from clogging the internal components.
5.
Control Panel and Automation Features
The control panel of the Guyson shot blaster is the interface through which operators can manage the various parameters of the equipment. It allows for the adjustment of settings such as abrasive flow rate, air pressure, blasting time, and the operation mode (manual, semi - automated, or fully automated). In more advanced models, there may be programmable features that enable the storage and recall of specific blasting profiles for different jobs. Automation features can include conveyor systems for moving workpieces in and out of the blasting area, robotic arms for precise nozzle positioning, or automated indexing tables for handling multiple parts. These features enhance the efficiency and consistency of the shot blasting process.
IV. Different Models of Guyson Shot Blasters
1.
Handheld Shot Blasters
Handheld Guyson shot blasters are designed for small - scale and detailed surface preparation tasks. They are highly maneuverable and allow operators to target specific areas with precision. These models are often used for tasks such as removing paint from small metal parts, cleaning intricate components in the electronics or jewelry industries, or preparing small sections of a larger workpiece. The handheld design gives the operator direct control over the blasting process, enabling them to adjust the angle and distance of the blast gun as needed. They are usually lightweight and easy to handle, making them suitable for tasks that require a high degree of operator dexterity.
2.
Cabinet - type Shot Blasters
Cabinet - type Guyson shot blasters are ideal for processing small to medium - sized workpieces. The blasting cabinet provides a controlled environment for the shot blasting operation. Operators can place the workpieces inside the cabinet and close the doors to start the blasting process. These models are commonly used in job shops or small manufacturing facilities where there is a need to process a variety of parts. The cabinet - type design contains the abrasive and dust within the cabinet, reducing the mess and improving the working environment. They can be equipped with different types of nozzles and blasting systems to handle a wide range of surface preparation requirements.
3.
Automated and Robotic Shot Blasters
Automated and robotic Guyson shot blasters are designed for high - volume and high - precision surface preparation. These models incorporate advanced automation and robotic technology to handle large - scale production runs. They can be programmed to blast specific patterns on the surface of the workpiece, ensuring consistent and accurate results. In automotive manufacturing, for example, these shot blasters can be used to prepare engine blocks, transmission housings, or body panels. The robotic arms can move the nozzles with great precision, following complex paths to cover the entire surface of the workpiece. This type of equipment is also used in industries such as aerospace, where the quality and consistency of surface preparation are of utmost importance.
4.
Wheel - abrator Shot Blasters
Wheel - abrator Guyson shot blasters are a specialized type of equipment. They use a rotating wheel to accelerate the abrasive shot instead of the traditional air - pressure - based systems. The wheel - abrator design is highly efficient for processing large volumes of small parts or for treating surfaces that require a more aggressive blasting action. The abrasive is fed onto the high - speed rotating wheel, which then throws the shot at the workpiece. This type of shot blaster is often used in foundries for cleaning castings or in the manufacturing of small metal components where a uniform and thorough surface preparation is needed.
V. Applications of the Guyson Shot Blaster
1.
Automotive Industry
In the automotive industry, the Guyson shot blaster has numerous applications. It is used for preparing engine components such as cylinder heads, blocks, and crankshafts. The shot blasting process removes any casting residues, rust, or old coatings from these parts, providing a clean and textured surface for subsequent machining and assembly. It also helps in improving the adhesion of engine paints and coatings, enhancing the durability and appearance of the components. In addition, the Guyson shot blaster is used for preparing body panels. By removing old paint and creating a suitable surface profile, it ensures better paint adhesion and a smooth finish, contributing to the overall quality of the vehicle's exterior.
2.
Aerospace Industry
The aerospace industry demands the highest level of precision and quality in surface preparation. Guyson shot blasters are used to prepare various aerospace components, including turbine blades, landing gear parts, and fuselage sections. The shot blasting process removes any surface contaminants, such as oxides or machining marks, which could affect the performance of these critical components. It also provides the necessary surface texture for the application of specialized coatings, such as anti - corrosion and thermal - barrier coatings. The ability to achieve a consistent and controlled surface finish is vital in aerospace applications to ensure the reliability and safety of the aircraft.
3.
Metalworking and Manufacturing
In metalworking and manufacturing, Guyson shot blasters are widely used for surface preparation of metal parts. They are used to clean and prepare raw materials before further processing, such as cutting, bending, or welding. The shot blasting removes rust, scale, and other impurities from the metal surface, improving the quality of the finished product. In addition, the equipment is used for preparing parts for plating, painting, or powder coating. By creating a uniform and clean surface, it ensures better adhesion of the coating, resulting in a more durable and aesthetically pleasing finish. The Guyson shot blaster is also valuable in the production of small metal components, such as screws, nuts, and bolts, where a high - volume and efficient surface preparation process is required.
4.
Surface Finishing in the Decorative Arts
In the decorative arts, the Guyson shot blaster is used for creating unique surface finishes. It can be used to texture metal surfaces for decorative purposes, such as creating a matte or satin finish on jewelry, sculptures, or decorative metalwork. The ability to control the intensity and pattern of the shot blasting allows artists and craftsmen to achieve a wide variety of surface effects. For example, by using different types of abrasive media and blasting techniques, a smooth metal surface can be transformed into one with a hammered or brushed - like appearance, adding an element of artistry and uniqueness to the piece.
5.
Renovation and Restoration Projects
In renovation and restoration projects, Guyson shot blasters play a crucial role. They are used to remove old paint, varnish, or other coatings from surfaces such as walls, floors, and furniture. In the case of historical building restorations, the shot blaster can be used to carefully clean and prepare stone, brick, or metal surfaces without causing damage to the underlying structure. The equipment is also used in furniture restoration to remove old finishes and prepare the wood or metal surfaces for refinishing, bringing new life to antique or vintage pieces.
VI. Advantages of the Guyson Shot Blaster
1.
Superior Surface Preparation Quality
The Guyson shot blaster is renowned for its ability to provide superior surface preparation quality. The precise control of the abrasive media, combined with the well - designed nozzles and blasting systems, ensures that the surface is thoroughly cleaned and textured. The result is a surface that is free from contaminants and has the ideal profile for subsequent processes. This high - quality surface preparation leads to better adhesion of coatings, improved performance of components, and a more durable and aesthetically pleasing finish.
2.
Versatility in Surface Treatment
One of the significant advantages of the Guyson shot blaster is its versatility. It can handle a wide variety of surfaces, including metals, plastics, composites, and even some types of stone and wood. The ability to use different types of abrasive media and adjust the blasting parameters allows it to be used for different levels of surface preparation, from light cleaning to heavy - duty material removal. This versatility makes it a valuable tool in many industries, from manufacturing to restoration.
3.
Efficient and Time - saving
The Guyson shot blaster is highly efficient in its operation. The automated and semi - automated models can process large volumes of workpieces in a relatively short time. The consistent and controlled blasting process reduces the need for rework or additional surface preparation steps. In comparison to traditional surface preparation methods like manual sanding or chemical stripping, the shot blaster can significantly reduce the overall project time, especially for large - scale or high - volume production runs.
4.
Cost - effective in the Long Run
Although the initial investment in a Guyson shot blaster may be significant, it proves to be cost - effective in the long run. The efficient use of abrasive media, thanks to the recycling and control systems, reduces the consumption of consumables. The reduction in labor time due to the fast and efficient blasting process also contributes to cost savings. Additionally, the high - quality surface preparation achieved by the shot blaster results in fewer rejects or failures in subsequent processes, such as coating or assembly, further reducing costs.
5.
Environmentally Friendly Options
Many Guyson shot blaster models are designed with environmentally friendly features. The dust collection and filtration systems reduce the amount of dust and debris released into the environment. Some models also have options for recycling and reusing the abrasive media, minimizing waste. By using water - based or less - harmful abrasive materials, the equipment can further reduce its environmental impact, making it a more sustainable choice for surface preparation.
VII. Maintenance of the Guyson Shot Blaster
1.
Regular Cleaning of Components
Regular cleaning of the Guyson shot blaster's components is essential for its optimal performance. The abrasive hopper should be emptied and cleaned to remove any accumulated debris or clumps of abrasive. The nozzles and blast guns should be inspected and cleaned regularly to ensure that they are free from blockages. Any buildup of abrasive or contaminants in the nozzles can affect the flow and direction of the abrasive shot, leading to uneven blasting. The blasting cabinet (in cabinet - type models) should be cleaned to remove dust and spent abrasive from the interior walls and floors. This helps to maintain the integrity of the cabinet and prevent the abrasive from being recycled with debris.
2.
Abrasive Media Maintenance
The abrasive media used in the Guyson shot blaster requires proper maintenance. It is important to check the quality of the abrasive regularly. Over time, the abrasive may become worn, rounded, or contaminated. Worn - out abrasive may not provide effective surface preparation and can lead to sub - optimal results. If the abrasive is found to be in poor condition, it should be replaced. Additionally, the abrasive handling system should be inspected to ensure that the abrasive is being transported smoothly and that there are no issues with the sieving or filtering mechanisms.
3.
Inspection and Maintenance of Mechanical and Electrical Parts
The mechanical and electrical parts of the Guyson shot blaster need to be inspected regularly. This includes checking the motors, pumps, bearings, and other moving parts for signs of wear or damage. Lubrication of the moving parts should be carried out according to the manufacturer's instructions to ensure smooth operation and prevent premature wear. The electrical components, such as the control panel, sensors, and wiring, should be inspected for any loose connections, frayed wires, or signs of electrical malfunction. Any issues with the mechanical or electrical parts should be addressed promptly to avoid breakdowns during operation.
4.
Calibration and Testing of the Equipment
Periodic calibration of the Guyson shot blaster is necessary to ensure that it is operating at the correct settings. This includes calibrating the abrasive flow rate, air pressure, and other parameters related to the blasting process. Testing the equipment with sample surfaces or test pieces can help to identify any issues with the blasting pattern, surface coverage, or the effectiveness of the surface preparation. Calibration and testing should be performed by trained personnel using appropriate tools and techniques to ensure the accuracy of the results.
VIII. Conclusion
The Guyson shot blaster is a remarkable and versatile piece of equipment that has made significant contributions to various industries. Its well - defined operational principles, comprehensive range of components, diverse models, extensive applications, numerous advantages, and structured maintenance practices make it a top choice for surface preparation and finishing. Whether in the automotive, aerospace, metalworking, decorative arts, or renovation industries, the Guyson shot blaster has proven its worth by providing high - quality, efficient, and cost - effective surface treatment solutions. With proper maintenance and operation, this equipment will continue to play a vital role in meeting the surface preparation needs of different sectors, ensuring the quality and performance of the finished products.