Hotline
+86-136 8495 9862
Email:cennia@szmizhi.com
Add::104,Building 27,Third Industrial Zone, Longxi Community,Longgang District,Shenzhen,China.
Coil Forming & Handling Equipment
Surface Treatment Equipment
Solutions
Application
About Us
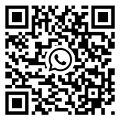
Welcome to MIZHI
For consultation/feedback, please call the service hotline: +86-136 8495 9862 Email:cennia@szmizhi.com
Introduction:
In the field of industrial manufacturing, the flying shear cutting machine is a crucial piece of equipment that offers high-speed and accurate cutting capabilities. This advanced machine is designed to cut various materials, such as metal sheets, strips, and wires, while they are in motion. With its precision and efficiency, the flying shear cutting machine plays a significant role in streamlining production processes and ensuring consistent product quality.
The flying shear cutting machine combines cutting-edge technology with robust construction to handle the demanding requirements of modern manufacturing. It is capable of performing rapid cuts with minimal waste, making it an ideal choice for high-volume production environments. Whether it's for the automotive, aerospace, construction, or electronics industry, this machine offers a reliable and efficient solution for cutting materials to specific lengths.
Design and Construction:
The design of a flying shear cutting machine is a complex engineering feat. The machine typically consists of several key components, including a cutting head, a drive system, a control system, and a material handling system.
The cutting head is the heart of the machine and is responsible for performing the actual cutting action. It usually consists of a pair of sharp blades that are driven by a powerful motor. The blades are designed to cut through the material quickly and cleanly, leaving a smooth edge.
The drive system is responsible for moving the cutting head at high speeds to match the speed of the material being cut. This can be achieved through various means, such as using electric motors, hydraulic systems, or pneumatic actuators. The drive system must be capable of providing precise control over the cutting head's speed and position to ensure accurate cuts.
The control system is the brain of the flying shear cutting machine. It is responsible for coordinating the operation of all the machine's components and ensuring that the cutting process is carried out smoothly and accurately. The control system may include programmable logic controllers (PLCs), human-machine interfaces (HMIs), and sensors to monitor the material's speed, position, and thickness.
The material handling system is responsible for feeding the material into the cutting area and removing the cut pieces. This can be done using conveyor belts, rollers, or other types of material handling equipment. The material handling system must be designed to handle the specific material being cut and ensure that it is properly aligned and positioned for cutting.
In addition to these main components, the flying shear cutting machine may also include other features such as safety guards, dust collection systems, and lubrication systems. Safety guards are essential to protect operators from the moving parts of the machine. Dust collection systems help to keep the work environment clean by removing dust and debris generated during the cutting process. Lubrication systems ensure that the machine's moving parts are properly lubricated to reduce wear and prolong the machine's lifespan.
Cutting Process:
The cutting process using a flying shear cutting machine typically involves several steps.
1. Material Feeding:
The material to be cut is fed into the machine using the material handling system. The material may be in the form of a continuous strip, sheet, or wire, and it is usually fed at a constant speed.
2. Speed Synchronization:
The cutting head is accelerated to match the speed of the material being cut. This is crucial to ensure that the cut is made accurately and without any distortion or damage to the material.
3. Cutting Action:
Once the cutting head is synchronized with the material's speed, the blades are activated to perform the cutting action. The cutting head moves across the material, cutting it into specific lengths or shapes as required.
4. Material Removal:
After the cut is made, the cut pieces are removed from the cutting area using the material handling system. The cut pieces may be stacked, sorted, or transferred to another processing station for further handling.
5. Quality Control:
Throughout the cutting process, quality control measures are implemented to ensure that the cuts are accurate and consistent. This may include using sensors to monitor the material's thickness, width, and length, as well as visual inspections to check for any defects or imperfections.
Advantages of Flying Shear Cutting Machines:
1. High-Speed Cutting:
Flying shear cutting machines are capable of performing extremely fast cuts, allowing for high-volume production. This is particularly beneficial in industries where time is of the essence and production rates need to be maximized.
2. Accuracy and Precision:
These machines offer high levels of accuracy and precision, ensuring that the cuts are made exactly to the required specifications. This is crucial for applications where tight tolerances are required, such as in the automotive and aerospace industries.
3. Minimal Waste:
The flying shear cutting process results in minimal waste, as the cuts are made while the material is in motion. This helps to reduce material costs and increase overall efficiency.
4. Versatility:
Flying shear cutting machines can handle a wide range of materials, including metals, plastics, and composites. They can also be adjusted to cut different thicknesses and widths, making them highly versatile and suitable for various applications.
5. Automated Operation:
Many flying shear cutting machines are equipped with advanced control systems that allow for automated operation. This reduces the need for manual labor and increases productivity while ensuring consistent quality.
Applications:
Flying shear cutting machines are widely used in various industries for different applications. Some of the common applications include:
1. Metal Processing:
In the metal processing industry, flying shear cutting machines are used to cut metal sheets, strips, and wires into specific lengths for further processing. This may include applications such as sheet metal fabrication, wire drawing, and tube manufacturing.
2. Automotive Industry:
The automotive industry uses flying shear cutting machines to cut metal parts for car bodies, chassis, and engine components. The high-speed cutting capabilities of these machines are essential for meeting the production demands of the automotive industry.
3. Aerospace Industry:
In the aerospace industry, flying shear cutting machines are used to cut lightweight materials such as aluminum and titanium alloys for aircraft components. The precision and accuracy of these machines are crucial for ensuring the quality and performance of aerospace parts.
4. Construction Industry:
The construction industry uses flying shear cutting machines to cut metal bars, pipes, and sheets for building structures and infrastructure projects. The versatility and high-speed cutting capabilities of these machines make them ideal for construction applications.
5. Electronics Industry:
In the electronics industry, flying shear cutting machines are used to cut thin metal foils and wires for printed circuit boards and electronic components. The precision and minimal waste of these machines are important for the production of high-quality electronic products.
Conclusion:
The flying shear cutting machine is a powerful and versatile piece of equipment that offers high-speed and accurate cutting capabilities. With its advanced design and construction, this machine is capable of handling a wide range of materials and applications, making it an essential tool in modern industrial manufacturing. Whether it's for cutting metal sheets, wires, or plastics, the flying shear cutting machine provides a reliable and efficient solution for streamlining production processes and ensuring consistent product quality.