Hotline
+86-136 8495 9862
Email:cennia@szmizhi.com
Add::104,Building 27,Third Industrial Zone, Longxi Community,Longgang District,Shenzhen,China.
Coil Forming & Handling Equipment
Surface Treatment Equipment
Solutions
Application
About Us
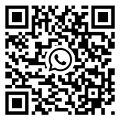
Welcome to MIZHI
For consultation/feedback, please call the service hotline: +86-136 8495 9862 Email:cennia@szmizhi.com
1. Introduction
In the dynamic realm of industrial manufacturing, the processing of coils into precisely cut strips is a fundamental operation that underpins countless industries. Georg, a name synonymous with innovation and quality in the manufacturing equipment sector, has made significant inroads with its slitting lines. These sophisticated machines are engineered to meet the diverse and exacting demands of industries such as automotive, construction, electronics, and metal service centers. By offering high - speed, high - precision cutting capabilities, Georg slitting lines have become a cornerstone for manufacturers aiming to optimize their production processes, reduce waste, and enhance product quality.
2. Key Features of Georg Slitting Lines
2.1. Exceptional Cutting Precision
Georg slitting lines are renowned for their high level of cutting accuracy. This is achieved through the use of high - precision knife shaft bearings. These bearings are designed to minimize any lateral movement of the cutter shaft, ensuring that the blades remain perfectly aligned during the cutting process. As a result, the cut widths of the slitted strips are extremely precise. For example, in applications where tight tolerances are required, such as in the production of components for the aerospace industry, Georg slitting lines can achieve width tolerances of up to ±0.001 inches. This level of precision is crucial as it reduces the need for secondary processing and ensures that the final products meet the strict quality standards of these industries. The high - precision shear design also contributes to a low - burr and low - camber slitting process. Burrs, which are small protrusions on the cut edges of the metal, can be a significant issue as they can affect the functionality and aesthetics of the final product. With Georg's optimized shear design, the blades cut through the material cleanly, minimizing the formation of burrs. Additionally, the low - camber slitting process ensures that the slitted strips are flat and straight, which is essential for applications where the strips need to be further processed or assembled.
2.2. High - Speed Processing
The ability to process materials at high speeds is a major advantage of Georg slitting lines. These lines are designed to operate at impressive speeds, with some models capable of reaching up to 600 m/min during the production of slitted coils. This high - speed processing is made possible by a combination of factors. The drive systems in Georg slitting lines are powerful and efficient, providing the necessary torque to move the coils and cut the material at high velocities. The slitting heads are also designed to withstand the high - speed operation, with robust construction and high - quality components. For instance, in a metal service center that needs to process large volumes of coils on a daily basis, the high - speed capabilities of Georg slitting lines can significantly increase productivity. The ability to process more coils in a shorter time frame means that the service center can meet the demands of its customers more quickly, gain a competitive edge in the market, and increase its overall profitability.
2.3. Adaptability to Diverse Materials
Georg slitting lines are highly versatile and can handle a wide range of materials. They are capable of processing materials with a material strength of more than 1,800 N/mm² and yield points up to 1,200 N/mm². This includes materials such as carbon steel, stainless steel, aluminum, and various alloys. Whether it's a thin, delicate aluminum strip for the electronics industry or a thick, high - strength steel coil for the construction industry, Georg slitting lines can handle the task with ease. The machine configurations can be adjusted to suit the specific properties of the material being processed. For example, when slitting aluminum, which is a relatively soft material, the cutting parameters such as blade speed, cutting force, and tension control can be optimized to ensure a clean and accurate cut without causing any damage to the material. In contrast, when processing high - strength steel, the machine can be configured to apply the necessary force to cut through the tough material while maintaining the desired precision.
2.4. High Winding Accuracy
The winding process in a slitting line is just as important as the cutting process, and Georg slitting lines excel in this area as well. They offer high winding accuracy, especially as the coil diameter increases. This is achieved through the use of a movable braking unit. The braking unit is designed to apply the right amount of tension to the slitted strip as it is being wound onto the recoiler. By carefully controlling the tension, the slitted strip is wound neatly and tightly, resulting in coils with a high degree of uniformity. In applications where the slitted coils need to be further processed or transported, the high winding accuracy ensures that the coils remain intact and in good condition. For example, in the automotive industry, where slitted metal coils are used to manufacture various components, the high - quality wound coils from Georg slitting lines can be easily fed into the next stage of the production process, such as stamping or forming, without any issues related to uneven winding.
2.5. Gentle Treatment of Sensitive Surfaces
Certain industries, such as the automotive and electronics industries, often deal with materials that have sensitive surfaces. For example, vehicle parts may have painted or coated surfaces, and annealed stainless steel is commonly used in the electronics industry. Georg slitting lines are designed to provide very gentle treatment to these highly sensitive surfaces. This is achieved through braking processes that are specifically adapted to the material surface. The braking systems can be adjusted to apply a gentle and consistent pressure on the material, preventing any scratches, dents, or other forms of surface damage. In the production of automotive parts, where the appearance and integrity of the surface are crucial for both aesthetic and functional reasons, the ability of Georg slitting lines to handle sensitive - surfaced materials is a significant advantage. It ensures that the final products meet the high - quality standards expected by consumers and automotive manufacturers alike.
2.6. Energy - Efficient Operation
In today's environmentally conscious and cost - sensitive manufacturing landscape, energy efficiency is a key consideration. Georg slitting lines are designed with modern regenerative systems and use drives of special efficiency grades, resulting in minimum power consumption. The regenerative systems are capable of capturing and reusing the energy that is typically wasted during the deceleration and braking phases of the machine. This not only reduces the overall energy consumption of the slitting line but also helps to lower the operating costs for the manufacturer. For example, in a large - scale manufacturing facility that operates multiple slitting lines, the energy savings achieved through the use of Georg's energy - efficient technology can be substantial over time. It also aligns with the industry's growing trend towards sustainable manufacturing practices, as reducing energy consumption helps to minimize the carbon footprint of the manufacturing process.
3. Technical Specifications
3.1. Coil - Related Specifications
Georg slitting lines are engineered to handle coils of varying sizes and weights. The maximum coil weight that these lines can accommodate is up to 40,000 kg. This makes them suitable for large - scale industrial applications where heavy coils are commonly used. For example, in steel mills or large - volume metal service centers, the ability to process such heavy coils is essential for efficient production. The strip width that can be processed ranges up to 2,800 mm. This wide range of strip widths allows for versatility in processing different types of products. Whether it's narrow strips for small - scale components or wide strips for large - format applications such as construction panels, Georg slitting lines can handle the task. The line thickness range is between 0.08 and 12.0 mm. This broad thickness range enables the processing of materials from thin foils, which are often used in the electronics industry, to thick metal sheets that are prevalent in the construction and heavy - machinery industries.
3.2. Line Speed and Slitting Capacity
The line speed of Georg slitting lines is an impressive feature. In the production of slitted coils, the lines can operate at speeds of up to 600 m/min. This high - speed operation significantly increases the productivity of the manufacturing process. Additionally, the number of slits that can be achieved is up to 50. This means that a single large coil can be efficiently divided into multiple narrower strips in one pass. For instance, in a packaging industry where multiple narrow plastic or metal strips are required for the production of bags or containers, the high slitting capacity of Georg slitting lines allows for quick and efficient production. The combination of high line speed and multiple slitting capabilities makes Georg slitting lines highly suitable for high - volume manufacturing environments.
3.3. Component - Level Specifications
At the component level, Georg uses only high - quality single components for their products. For example, the slitter arbors in the slitting heads are designed with precision in mind. In some models, like the ones with 160 - mm diameter arbors, they are made from high - strength materials to ensure durability and stability during the cutting process. The cutter diameter can be up to 250 mm, depending on the specific model and application requirements. These components are carefully selected and engineered to work in harmony, contributing to the overall high - performance and reliability of the slitting line. The use of high - quality components also reduces the need for frequent maintenance and replacement, further enhancing the cost - effectiveness of the machine over its lifespan.
4. Applications across Industries
4.1. Automotive Industry
In the automotive industry, precision and quality are of utmost importance. Georg slitting lines play a crucial role in the production of various automotive components. Metal strips are cut to exact widths for manufacturing car body panels, such as doors, hoods, and fenders. The high - precision cutting capabilities of Georg slitting lines ensure that the panels fit together perfectly during the assembly process. This not only improves the structural integrity of the vehicle but also enhances its aesthetic appearance. For example, in the production of luxury cars, where the fit and finish of the body panels are critical, the accurate cuts provided by Georg slitting lines contribute to the overall high - quality look and feel of the vehicle. Additionally, slitted strips are used for interior components like seat frames and dashboard supports. The ability to produce consistent and accurate strip widths is essential in the automotive industry, as any deviation can lead to problems in the assembly process and affect the functionality of the final product.
4.2. Construction Industry
The construction industry benefits significantly from Georg slitting lines. Metal strips are cut for a variety of applications, including roofing, wall cladding, and structural components. For roofing, the slitted strips need to be of precise width and length to ensure a proper fit and a watertight seal. Georg slitting lines can produce long, continuous strips that are easy to install, reducing the time and labor required for roofing projects. In the case of wall cladding, the accurate cutting ensures that the panels fit together tightly, providing a weather - resistant and aesthetically pleasing exterior for buildings. For structural components such as steel beams and columns, the slitting lines can produce metal strips with the right dimensions and quality. The ability to process thick and heavy materials makes Georg slitting lines suitable for large - scale construction projects. They can also be used to cut metal strips for decorative elements in construction, such as railing components and architectural accents, adding a touch of elegance and functionality to buildings.
4.3. Electronics Industry
The electronics industry requires high - precision processing of materials. Georg slitting lines are used to cut materials such as copper foils, insulating films, and printed circuit board (PCB) materials. Copper foils are slit into narrow strips for use in the production of electrical conductors in electronic devices. The precision of the cutting is crucial, as even the slightest deviation in the width of the copper strips can affect the electrical performance of the device. Insulating films are also slit to the appropriate widths for use in protecting and insulating electronic components. In the production of PCBs, the slitting lines can cut the large sheets of PCB materials into smaller, more manageable sizes. The high - speed and high - precision cutting capabilities of Georg slitting lines enable electronics manufacturers to meet the high - volume production requirements of the industry while maintaining strict quality control. For example, in the production of smartphones, where a large number of small - sized components are required, the efficient and accurate slitting provided by Georg slitting lines helps to ensure the smooth operation of the manufacturing process.
4.4. Metal Service Centers
Metal service centers are in the business of providing customized metal products to their customers. Georg slitting lines are ideal for these centers as they can quickly and accurately slit large coils of metal into the specific widths and lengths required by customers. The high - speed operation of the slitting lines allows for quick turnaround times, which is crucial for metal service centers to meet the demands of their customers promptly. The ability to handle a wide range of materials and coil sizes also makes Georg slitting lines highly versatile for metal service centers. They can serve customers in various industries, from small - scale fabricators to large - scale manufacturers, by providing them with precisely cut metal strips according to their specifications. This not only helps the metal service centers to expand their customer base but also to increase their competitiveness in the market.
5. Georg's Approach to Quality and Customer Support
5.1. Quality - Oriented Design and Manufacturing
Georg has a long - standing reputation for quality, and this is evident in the design and manufacturing of its slitting lines. The company follows strict quality control measures at every stage of the production process. From the selection of raw materials to the final assembly and testing of the slitting lines, each step is carefully monitored to ensure that the highest quality standards are met. The use of high - quality components, as mentioned earlier, is a key aspect of this quality - oriented approach. These components are sourced from reliable suppliers and are subjected to rigorous testing before being incorporated into the slitting lines. The manufacturing facilities are equipped with state - of - the - art machinery and technology, allowing for precise machining and assembly of the components. This attention to detail in the design and manufacturing process results in slitting lines that are not only highly efficient but also extremely reliable, with a long service life.
5.2. Georg Protection World - Life Cycle Quality Management
Georg offers a comprehensive service package called Georg Protection World, which is centered around life cycle quality management. This service is designed to provide customers with an all - round care - free package for the total life cycle of their machine or line. It includes services such as regular maintenance, prompt repair in case of breakdowns, and technical support. The regular maintenance service is carried out by trained technicians who follow a detailed maintenance schedule. They inspect all components of the slitting line, check for wear and tear, and perform necessary repairs and replacements. This proactive approach to maintenance helps to prevent major breakdowns and ensures that the slitting line operates at peak performance at all times. In the event of a breakdown, Georg's support team is available 24/7 to provide prompt assistance. They can diagnose the problem remotely in many cases and provide solutions to get the machine back up and running as quickly as possible. The life cycle quality management service also includes software updates and upgrades to keep the slitting line up - to - date with the latest technology and improvements. As a result, the operating costs of the slitting lines are reduced significantly, and the customer's profits are increased.
5.3. Customization and Technical Expertise
Georg understands that each customer has unique requirements. The company's team of engineers and experts works closely with customers to develop custom - tailored solutions for their specific applications and processes. Whether it's a new project or a modernization task, Georg provides technical expertise and guidance throughout the process. For example, if a customer has a specific material that is difficult to slit or a unique production requirement, Georg's engineers can design a special machine configuration or develop a customized cutting process to meet the customer's needs. The company also offers training to the customer's operators and maintenance staff to ensure that they can use and maintain the slitting line effectively. This level of customization and technical support not only helps customers to optimize their production processes but also builds long - term relationships based on trust and reliability.
6. Future Outlook and Innovations
As technology continues to evolve, Georg is expected to introduce further innovations in its slitting lines. One area of focus is likely to be the integration of advanced automation and artificial intelligence (AI) technologies. Automation can further reduce human error and increase the efficiency of the slitting process. For example, automated coil loading and unloading systems can save time and labor, while AI - powered quality control systems can detect even the slightest defects in the slitted strips in real - time. Another area of innovation could be in the development of more energy - efficient and sustainable technologies. With the increasing global focus on environmental sustainability, Georg may explore new ways to reduce the energy consumption of its slitting lines and minimize waste generation. Additionally, as new materials are developed and introduced in various industries, Georg will need to adapt its slitting line technology to handle these materials effectively. This could involve the development of new cutting tools and processes to ensure precise and clean cuts on advanced materials. Overall, Georg's commitment to innovation and quality positions it well to continue leading the way in the slitting line market in the future.