Hotline
+86-136 8495 9862
Email:cennia@szmizhi.com
Add::104,Building 27,Third Industrial Zone, Longxi Community,Longgang District,Shenzhen,China.
Coil Forming & Handling Equipment
Surface Treatment Equipment
Solutions
Application
About Us
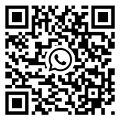
Welcome to MIZHI
For consultation/feedback, please call the service hotline: +86-136 8495 9862 Email:cennia@szmizhi.com
I. Introduction
The Goff shot blaster is a remarkable piece of equipment that has carved out a significant niche in the surface preparation industry. With its unique design and advanced features, it has become a preferred choice for many professionals dealing with surface treatment tasks. This extensive exploration will cover every aspect of the Goff shot blaster, starting from its working principles, the components that make it function, the various models available, its diverse applications, the advantages it offers, and the essential maintenance procedures required to keep it in optimal condition.
II. Working Principles of the Goff Shot Blaster
1.
Shot Blasting Mechanics
The fundamental principle behind the Goff shot blaster is shot blasting. This process involves the acceleration of abrasive particles, commonly known as shot, towards the surface that requires preparation. The shot used in Goff shot blasters can be of different materials such as steel, aluminum oxide, or other specialized abrasives, depending on the specific surface and the desired outcome. These abrasive particles are propelled at high speeds by a carefully engineered mechanism within the blaster. When the shot impacts the surface, it imparts kinetic energy. This energy transfer is what enables the removal of unwanted substances like rust, old paint, scale, and other contaminants. Additionally, the shot blasting action can also modify the surface texture by selectively removing small amounts of material, creating a more suitable surface for subsequent processes like painting, coating, or bonding.
2.
Controlled Shot Propulsion
The Goff shot blaster is designed with precision to control the propulsion of the abrasive shot. The velocity at which the shot is launched can be adjusted according to various factors. These include the type of surface being treated (whether it's a soft metal, a hard ceramic, or a brittle composite), the thickness and nature of the layer to be removed (for example, thick layers of industrial coatings or thin surface oxides), and the specific requirements of the finishing process. By having control over the shot velocity, the Goff shot blaster can ensure that the surface is prepared effectively without causing unnecessary damage to the substrate. The angle and direction of the shot can also be manipulated in some models, allowing for more targeted and efficient surface preparation in complex or hard - to - reach areas.
3.
Abrasive Recycling and Reuse
An outstanding feature of the Goff shot blaster is its efficient abrasive recycling and reuse system. After the abrasive shot has been projected onto the surface and completed its task of removing debris, it is collected through a dedicated recovery mechanism. This recovery system is designed to separate the used shot from the removed material, which may include dust, paint chips, and other waste products. The separated abrasive is then processed to remove any remaining contaminants and is recycled back into the system for reuse. This not only reduces the cost associated with purchasing new abrasive media but also minimizes waste, making the shot blasting process more environmentally friendly. The recycling process is carefully monitored and controlled to maintain the quality of the abrasive, ensuring consistent and effective surface preparation over multiple cycles.
III. Components of the Goff Shot Blaster
1.
Blasting Head and Nozzles
The blasting head and nozzles are critical components of the Goff shot blaster. The blasting head is the part where the abrasive shot is initially directed towards the surface. It is designed to handle the high - velocity flow of the shot and distribute it evenly. The nozzles, which are usually made from durable materials like carbide or ceramic, are attached to the blasting head. These nozzles are carefully engineered to control the shape and spread of the shot stream. The size and shape of the nozzles can vary depending on the model and the specific application. For instance, a narrow - angle nozzle might be used for precision work on small or intricate surfaces, while a wider - angle nozzle can cover a larger area more quickly for general surface preparation. The design of the blasting head and nozzles also ensures that the shot is directed accurately towards the target surface, minimizing any scattering or misdirection of the abrasive.
2.
Abrasive Storage and Delivery System
The abrasive storage and delivery system of the Goff shot blaster is responsible for storing the abrasive media and supplying it to the blasting head at the required rate. It typically consists of a storage hopper or container that can hold a significant amount of abrasive. The hopper is designed to keep the abrasive in a stable and accessible state. From the hopper, the abrasive is transported to the blasting head through a series of pipes, conveyors, or other transfer mechanisms. The delivery system is equipped with flow - control devices such as valves, augers, or pumps to ensure that the abrasive is metered accurately and delivered consistently. Some systems may also have sensors to monitor the level of abrasive in the hopper and trigger alerts or automatic refilling mechanisms when the supply is running low.
3.
Dust Collection and Filtration Unit
During the shot blasting process, a large amount of dust and debris is generated. The Goff shot blaster incorporates a highly efficient dust collection and filtration unit to handle this issue. The unit typically uses a combination of fans, vacuum systems, and filters to capture and remove the dust - laden air from the blasting area. The fans create a negative pressure environment that draws the dust - filled air towards the filtration system. The filters, which can be of various types such as cartridge filters, bag filters, or cyclone separators, are designed to trap the dust particles while allowing the clean air to pass through. The clean air can then be either recirculated back into the workspace or exhausted outside, depending on the specific design and requirements. This dust collection and filtration system not only improves the air quality in the working environment but also protects the internal components of the shot blaster from dust accumulation, which could affect its performance.
4.
Drive and Control System
The drive and control system of the Goff shot blaster is what enables the operator to manage the various functions of the equipment. The drive system is responsible for powering the movement of the blaster in some models, especially those that are self - propelled or have automated features. It consists of motors, gears, and wheels or tracks that allow the blaster to move smoothly across the surface being treated. The control system, on the other hand, provides the interface for the operator to adjust parameters such as the velocity of the abrasive shot, the flow rate of the abrasive, the operation time, and the speed and direction of movement (in mobile models). The control system may have a simple control panel with buttons and knobs or a more advanced touch - screen interface with programmable settings. It also incorporates safety features such as emergency stop buttons and interlocks to prevent accidental operation and protect the operator.
5.
Recovery and Separation System for Abrasive
The recovery and separation system for abrasive in the Goff shot blaster is a key element in its overall design. This system is responsible for collecting the used abrasive after it has been projected onto the surface. It has a collection mechanism that gathers the abrasive and the debris together. Once collected, the system uses mechanical and sometimes magnetic separation methods to separate the abrasive from the debris. For example, sieving or screening processes are used to remove larger debris particles, and magnetic separators can be employed if the abrasive or debris has magnetic properties. The recovered abrasive is then sent to a cleaning and conditioning process before being recycled back into the abrasive storage and delivery system. This ensures that the recycled abrasive is of high quality and can continue to provide effective surface preparation.
IV. Different Models of Goff Shot Blasters
1.
Hand - held Goff Shot Blasters
Hand - held Goff shot blasters are designed for applications that require precision and flexibility. These models are relatively small and lightweight, making them easy to handle by the operator. They are ideal for working on small - scale projects or in confined spaces. For example, they can be used for removing paint from small metal parts, cleaning delicate components in the electronics or jewelry industries, or preparing small sections of a larger workpiece for detailed finishing. The hand - held design gives the operator direct control over the blasting process, allowing them to adjust the angle and distance of the blasting head as needed. Despite their size, these models still incorporate essential features such as adjustable abrasive flow and shot velocity controls, as well as a dust collection mechanism to maintain a clean working environment.
2.
Walk - behind Goff Shot Blasters
Walk - behind Goff shot blasters are larger and more powerful than the hand - held models. They are designed for covering larger surface areas in a more efficient manner. These models are often self - propelled, with the operator guiding the blaster as it moves across the surface. They are commonly used in industrial settings, such as factories, warehouses, or construction sites, for preparing floors, walls, or large metal structures. The walk - behind design provides better stability and control during operation. They have a larger abrasive storage capacity and a more robust drive system compared to the hand - held models. The dust collection and filtration systems in these models are also more powerful to handle the increased dust generation during the larger - scale blasting operations.
3.
Ride - on Goff Shot Blasters
Ride - on Goff shot blasters are the most powerful and largest models available. They are designed for extremely large - scale surface preparation projects, such as those in airports, large industrial complexes, or extensive parking lots. These models feature a seat for the operator, allowing for comfortable operation during long - duration jobs. They have a very high - capacity abrasive delivery system and a highly efficient dust collection and filtration unit to handle the massive amount of material generated during the blasting process. The ride - on design provides excellent mobility and coverage speed, enabling the blaster to quickly cover vast areas. They also have advanced control systems with programmable features for precise operation and consistent surface preparation over large distances.
4.
Specialty Goff Shot Blasters
In addition to the standard models, Goff also offers specialty shot blasters designed for specific applications. These may include models with unique abrasive delivery systems for handling special types of abrasives or for achieving very high - precision surface preparation. For example, there could be models designed for use in the medical device manufacturing industry, where extremely clean and precise surface preparation is required. There are also specialty models with enhanced dust collection systems for use in environments with strict air quality requirements, such as in food processing plants or clean rooms. Some specialty models may have additional features like temperature - controlled blasting chambers for working with heat - sensitive materials or those that require specific temperature conditions during the blasting process.
V. Applications of the Goff Shot Blaster
1.
Automotive Industry Applications
In the automotive industry, the Goff shot blaster is used in various ways. It is crucial for preparing engine components such as cylinder heads, blocks, and crankshafts. The shot blasting process removes casting residues, rust, and old coatings from these parts, providing a clean and textured surface that is ideal for further machining and assembly. This helps in improving the adhesion of engine paints and coatings, enhancing the durability and performance of the components. Additionally, the Goff shot blaster is used for preparing body panels. By removing old paint and creating a suitable surface profile, it ensures better paint adhesion and a smooth finish, contributing to the overall quality of the vehicle's exterior. It can also be used for cleaning and preparing chassis components, suspension parts, and other metal parts in the automotive manufacturing process.
2.
Aerospace Industry Applications
The aerospace industry demands the highest level of precision and quality in surface preparation, and the Goff shot blaster meets these requirements. It is used to prepare various aerospace components, including turbine blades, landing gear parts, and fuselage sections. The shot blasting process removes surface contaminants such as oxides, machining marks, and other impurities that could affect the performance of these critical components. It also provides the necessary surface texture for the application of specialized coatings, such as anti - corrosion and thermal - barrier coatings. The ability to achieve a consistent and controlled surface finish is vital in aerospace applications to ensure the reliability and safety of the aircraft. The Goff shot blaster's precision and reliability make it an essential tool in this high - stakes industry.
3.
Metalworking and Manufacturing Applications
In metalworking and manufacturing, the Goff shot blaster is widely used for surface preparation of metal parts. It is used to clean and prepare raw materials before further processing, such as cutting, bending, or welding. The shot blasting removes rust, scale, and other impurities from the metal surface, improving the quality of the finished product. In addition, the equipment is used for preparing parts for plating, painting, or powder coating. By creating a uniform and clean surface, it ensures better adhesion of the coating, resulting in a more durable and aesthetically pleasing finish. The Goff shot blaster is also valuable in the production of small metal components, such as screws, nuts, and bolts, where a high - volume and efficient surface preparation process is required.
4.
Construction and Renovation Applications
In construction and renovation projects, the Goff shot blaster has numerous applications. It is used for preparing concrete surfaces for flooring applications. The shot blasting process removes laitance, grease, and old coatings from the concrete, creating a clean and rough surface that is perfect for the application of epoxy or other floor coatings. In renovation projects, it can be used to remove old paint from walls, ceilings, and metal structures. In historical building restorations, the Goff shot blaster can be used with great care to clean and prepare stone, brick, or metal surfaces without causing damage to the underlying structure. It is also used in preparing surfaces for the installation of new construction materials, such as tiles or siding.
5.
Surface Finishing in Decorative Arts Applications
In the decorative arts, the Goff shot blaster offers unique possibilities for surface finishing. It can be used to texture metal surfaces for decorative purposes, such as creating a matte or satin finish on jewelry, sculptures, or decorative metalwork. The ability to control the intensity and pattern of the shot blasting allows artists and craftsmen to achieve a wide variety of surface effects. For example, by using different types of abrasive media and blasting techniques, a smooth metal surface can be transformed into one with a hammered or brushed - like appearance, adding an element of artistry and uniqueness to the piece. The Goff shot blaster can also be used on other materials like wood or glass in certain decorative applications to create interesting and visually appealing textures.
VI. Advantages of the Goff Shot Blaster
1.
Superior Surface Preparation Quality
The Goff shot blaster is known for providing superior surface preparation quality. The combination of its well - designed blasting head and nozzles, precise control of abrasive shot velocity, and efficient abrasive delivery system ensures that surfaces are thoroughly cleaned and textured. The result is a surface that is free from contaminants and has the ideal profile for subsequent processes. This high - quality surface preparation leads to better adhesion of coatings, improved performance of components, and a more durable and aesthetically pleasing finish. The ability to achieve a consistent and uniform surface finish, regardless of the size or complexity of the surface, is a significant advantage in many applications.
2.
Versatility in Surface Treatment
One of the main advantages of the Goff shot blaster is its versatility. It can handle a wide variety of surfaces, including different types of metals (such as steel, aluminum, and copper), concrete, wood, and even some composite materials. The ability to use different types of abrasive media and adjust the blasting parameters allows it to be used for different levels of surface preparation, from light cleaning to heavy - duty material removal. This versatility makes it a valuable tool in many industries, from manufacturing to restoration. It can adapt to the specific requirements of each project, whether it's preparing a delicate electronic component or a large - scale industrial floor.
3.
Efficient and Time - saving
The Goff shot blaster is highly efficient in its operation. The automated and semi - automated models can process large volumes of workpieces in a relatively short time. The consistent and controlled blasting process reduces the need for rework or additional surface preparation steps. Even in the case of hand - held models, the well - designed abrasive delivery and dust collection systems, along with the ability to control the blasting parameters, ensure that the surface preparation is completed quickly and effectively. Compared to traditional surface preparation methods like manual sanding or chemical stripping, the Goff shot blaster can significantly reduce the overall project time, especially for large - scale or high - volume production runs.
4.
Cost - effective in the Long Run
Although the initial investment in a Goff shot blaster may be significant, it proves to be cost - effective in the long run. The efficient use of abrasive media, thanks to the recycling system, reduces the consumption of consumables. The reduction in labor time due to the fast and efficient blasting process also contributes to cost savings. Additionally, the high - quality surface preparation achieved by the shot blaster results in fewer rejects or failures in subsequent processes, such as coating or assembly, further reducing costs. The ability to handle a wide range of surface preparation tasks with a single machine also eliminates the need for multiple specialized tools, adding to the overall cost - effectiveness.
5.
Environmentally Friendly Design
The Goff shot blaster is designed with environmental considerations in mind. The abrasive recycling system reduces waste by reusing the abrasive media. The efficient dust collection and filtration units minimize the release of dust and debris into the environment, improving air quality in the workplace. Some models may also use eco - friendly abrasive materials or have features that reduce energy consumption during operation. These environmentally friendly aspects not only benefit the environment but also comply with increasingly strict environmental regulations in various industries.
VII. Maintenance of the Goff Shot Blaster
1.
Regular Cleaning of Equipment
Regular cleaning of the Goff shot blaster is essential for its proper functioning. The abrasive hopper should be emptied and cleaned regularly to remove any debris or clumps of abrasive that could affect the flow rate. The blasting head and nozzles should be inspected and cleaned frequently to ensure that they are free from blockages. Any buildup of abrasive or contaminants in the nozzles can disrupt the flow and direction of the abrasive shot, leading to uneven blasting. The dust collection and filtration system should also be cleaned regularly to maintain its efficiency. This includes cleaning or replacing filters as needed to ensure proper air circulation and dust removal. The entire machine, including the drive and control systems, should be wiped down to remove dust and debris that could affect its performance.
2.
Abrasive Media Management
Proper management of the abrasive media is crucial for the performance of the Goff shot blaster. The quality of the abrasive should be regularly checked. Over time, the abrasive may become worn, rounded, or contaminated. Worn - out abrasive may not provide effective surface preparation and can lead to sub - optimal results. If the abrasive is found to be in poor condition, it should be replaced. Additionally, the abrasive handling system should be inspected to ensure that the abrasive is being transported smoothly and that there are no issues with the valves, augers, or other components that control the flow. The recycling system should be maintained to ensure that the recovered abrasive is properly cleaned and ready for reuse.
3.
Inspection and Maintenance of Mechanical and Electrical Components
The mechanical and electrical components of the Goff shot blaster require regular inspection. This includes checking the motors, pumps, bearings, and other moving parts for signs of wear or damage. Lubrication of the moving parts should be carried out according to the manufacturer's instructions
If you are in the market for a concrete shot blaster for sale, there are several factors to consider to ensure you make the right purchase.
Types of Concrete Shot Blasters
-
Handheld Concrete Shot Blasters
: These are compact and lightweight, making them ideal for small-scale projects or areas with limited access. They are easy to maneuver and can be used for tasks such as removing rust, paint, or other coatings from concrete surfaces in tight spaces like corners or small rooms. Handheld models are usually less powerful compared to their larger counterparts but offer great flexibility for minor repair and maintenance work.
-
Walk-Behind Concrete Shot Blasters
: These are more suitable for medium-sized areas. They provide greater coverage and power than handheld blasters. Walk-behind shot blasters are often used in warehouses, parking lots, and smaller industrial floors where a larger machine might not be practical to operate. They offer good control and can be easily navigated by the operator, allowing for precise surface preparation.
-
Ride-On Concrete Shot Blasters
: For large-scale projects such as airport runways, major highways, or large industrial floors, ride-on concrete shot blasters are the best choice. These machines are highly powerful and can cover a large area in a short amount of time. They are equipped with advanced features like adjustable speed, variable shot intensity, and efficient dust collection systems to ensure optimal performance and a clean working environment.
Features to Look for in a Concrete Shot Blaster
-
Shot Blasting Media Compatibility
: Different concrete shot blasters are designed to work with specific types and sizes of shot blasting media, such as steel shots, steel grit, or abrasive beads. It is essential to choose a machine that is compatible with the media you plan to use. The right media can enhance the efficiency and quality of the surface preparation process.
-
Power and Performance
: The power of the machine is a crucial factor. A more powerful concrete shot blaster will be able to remove contaminants, coatings, and imperfections from the concrete surface more effectively. Look for machines with high-powered motors and efficient blasting systems to ensure optimal performance. Additionally, check the machine's blasting rate, which indicates how quickly it can clean a given area.
-
Dust Collection System
: A good dust collection system is essential to maintain a clean and safe working environment. Look for concrete shot blasters that come with efficient dust collectors that can capture and filter out the dust and debris generated during the blasting process. This not only helps to protect the operator's health but also reduces the amount of post-cleanup work required.
-
Adjustability and Control
: The ability to adjust the shot intensity, blasting angle, and speed is important to achieve the desired surface finish. Look for machines that offer a wide range of adjustability options, allowing you to customize the blasting process according to the specific requirements of the project. Additionally, a machine with easy-to-use controls and a user-friendly interface will make the operation more convenient and efficient.
-
Durability and Build Quality
: Since concrete shot blasters are subjected to heavy use and abrasive materials, they need to be built to last. Look for machines made of high-quality materials, such as heavy-duty steel frames, wear-resistant components, and reliable motors. A well-built machine will require less maintenance and have a longer lifespan, saving you money in the long run.
Where to Buy Concrete Shot Blasters
-
Manufacturers
: Buying directly from the manufacturer is a good option as you can get access to the latest models and technical support. Manufacturers often offer a wide range of products and can customize the machine according to your specific requirements. However, this option may require more research and time to find a reliable manufacturer.
-
Equipment Suppliers and Distributors
: Equipment suppliers and distributors usually have a wide selection of concrete shot blasters from different manufacturers. They can provide you with expert advice and help you choose the right machine for your needs. Additionally, they may offer after-sales support and maintenance services, making it a convenient option for many buyers.
-
Online Marketplaces
: Online marketplaces such as Alibaba, eBay, and Amazon offer a wide range of concrete shot blasters for sale. You can compare different models and prices from multiple sellers in one place. However, it is important to be cautious when buying from online marketplaces and ensure that you are dealing with a reliable seller. Read the product reviews and check the seller's reputation before making a purchase.
In conclusion, when looking for a concrete shot blaster for sale, consider the type of machine that suits your project size and requirements, the features that are important for your surface preparation process, and the source of purchase to ensure you get a high-quality and reliable machine. With the right concrete shot blaster, you can achieve excellent surface preparation results and enhance the durability and performance of your concrete surfaces.
If you are in the market for a concrete shot blaster for sale, there are several factors to consider to ensure you make the right purchase.