Hotline
+86-136 8495 9862
Email:cennia@szmizhi.com
Add::104,Building 27,Third Industrial Zone, Longxi Community,Longgang District,Shenzhen,China.
Coil Forming & Handling Equipment
Surface Treatment Equipment
Solutions
Application
About Us
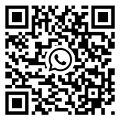
Welcome to MIZHI
For consultation/feedback, please call the service hotline: +86-136 8495 9862 Email:cennia@szmizhi.com
1. Introduction
In the dynamic and competitive landscape of the metal manufacturing industry, the Hot - Rolled (HR) coil slitting machine stands as a crucial piece of equipment. Hot - rolled coils are widely used in various sectors due to their cost - effectiveness and suitability for large - scale production. The HR coil slitting machine is designed to transform these large - diameter, thick - gauge coils into narrower strips, which are then further processed into a multitude of end - products. From construction materials to automotive components, the role of the HR coil slitting machine in enabling efficient production cannot be overstated. This in - depth exploration will cover its components, working principle, applications, advantages, challenges, and future trends.
2. Components of an HR Coil Slitting Machine
2.1 Uncoiler
The uncoiler is the starting point of the slitting process for HR coils. Given the large size and weight of HR coils, a robust uncoiler is essential. Hydraulic expandable mandrel uncoilers are commonly used. These can be adjusted to fit different inner diameters of the coils, providing flexibility in handling various coil sizes. The hydraulic system allows for quick and secure clamping of the coil. For example, in a steel manufacturing plant processing large - scale HR coils for construction applications, the uncoiler needs to be able to handle coils weighing several tons. The tension control system in the uncoiler is a vital component. It ensures that the hot - rolled strip is unwound at a consistent speed with the right amount of tension. If the tension is too low, the strip may sag, leading to misalignment during slitting. On the other hand, excessive tension can cause the strip to stretch or even break, especially considering the relatively soft and malleable nature of hot - rolled steel at the initial processing stage.
2.2 Leveler
After unwinding, the HR strip often has significant curvature and unevenness due to the hot - rolling and coiling processes. The leveler is tasked with straightening the strip. It consists of multiple rolls, usually made of hardened steel to withstand the high forces involved. The number of rolls can vary, but for HR coils, a larger number of rolls is often required compared to cold - rolled coil processing. For instance, a 21 - roll leveler might be used for thick - gauge HR strips. The rolls in the leveler are arranged in a specific pattern to apply a combination of bending and stretching forces to the strip. Some advanced levelers have adjustable roll - gap mechanisms. This feature allows operators to fine - tune the leveling process according to the thickness, hardness, and alloy composition of the HR strip. Precise leveling is crucial as it ensures that the strip is in a suitable condition for accurate slitting.
2.3 Slitting Unit
The slitting unit is the core of the HR coil slitting machine. It uses circular slitting knives to cut the wide HR strip into multiple narrower strips. These knives are made of high - quality tool steel, which is hardened and sharpened to withstand the tough cutting process of hot - rolled materials. The knives are mounted on a rigid shaft, and their spacing can be adjusted to achieve the desired strip widths. Shear slitting is the most common method for HR coil slitting. In shear slitting, the circular knives overlap slightly, and as the HR strip passes through, the knives shear the material, similar to the action of scissors. This method is effective for a wide range of HR strip thicknesses, typically from a few millimeters to several centimeters. The slitting unit also requires a powerful drive system to ensure smooth and continuous cutting, especially when processing thick HR coils.
2.4 Scrap Handling System
During the slitting process of HR coils, a significant amount of scrap is generated in the form of burrs and trimmings. The scrap handling system is designed to collect and manage this waste efficiently. It usually consists of scrap winders located at the sides of the slitting unit. These winders continuously collect the scrap and wind it into a compact form. In some cases, the scrap may be further processed for recycling. For example, the scrap from HR coil slitting can be melted down and reused in the steel - making process. Some advanced scrap handling systems are equipped with automatic tension - control mechanisms for the scrap, ensuring that it is wound up neatly and without causing any jamming or interference with the slitting process.
2.5 Take - up Reels
Once the HR strip is slit into multiple narrower strips, these strips need to be wound back into coils. Take - up reels are used for this purpose. Each take - up reel is designed to handle one of the slit strips. Given the large volume and weight of the slit HR strips, the take - up reels need to be driven by high - torque motors. These motors maintain a consistent tension on the strip during the winding process. Tension control during winding is crucial to ensure that the coils are tightly and evenly wound. If the tension is not properly controlled, the coils may have loose or uneven windings, which can affect the quality of the final product and cause problems during subsequent handling and processing.
2.6 Control System
The control system of an HR coil slitting machine is a sophisticated combination of hardware and software. It serves as the brain of the entire operation, coordinating the functions of all the components. The control system can be based on programmable logic controllers (PLCs) or more advanced computer - numerical - control (CNC) systems. These systems allow operators to set various parameters, such as the desired strip widths, the speed of the slitting machine, the tension levels for unwinding and winding, and the position of the slitting knives. The control system also provides real - time monitoring of the slitting process. It can detect any abnormal conditions, such as over - tension, under - tension, or misalignment of the slitting knives, and take immediate corrective actions. Some modern control systems are also equipped with remote - monitoring capabilities, allowing plant managers to monitor the operation of the slitting machine from a central control room or even remotely via the internet.
3. Working Principle
The operation of an HR coil slitting machine is a highly coordinated and sequential process.
1. Unwinding Phase: The HR coil is first loaded onto the expandable mandrel of the uncoiler. Once the coil is securely in place, the mandrel expands to grip the inner core of the coil firmly. The control system then activates the uncoiler motor, which starts to unwind the HR strip at a pre - set speed. The tension - control system continuously monitors and adjusts the tension of the strip to ensure a smooth unwinding operation. This is particularly important as the hot - rolled strip is still relatively soft and can be easily damaged if the tension is not properly managed.
2. Leveling Phase: As the unwound HR strip enters the leveler, it passes through the series of rolls. The rolls apply a combination of bending and stretching forces to the strip, gradually straightening it. The operator can adjust the roll - gap settings based on the thickness and material of the strip to achieve the optimal leveling effect. The leveling process is crucial as it ensures that the strip is flat and uniform before entering the slitting unit, which is essential for accurate slitting. In the case of HR coils, the leveling process may need to be more robust due to the greater initial curvature and unevenness of the strip.
3. Slitting Phase: After the strip is leveled, it enters the slitting unit. The circular slitting knives, which are set at the desired spacing according to the programmed strip widths, cut the wide strip into multiple narrower strips. The shear - slitting process involves the overlapping knives shearing through the HR strip. The high - speed rotation of the knives, combined with the forward movement of the strip, enables efficient cutting. The slitting unit operates at a speed that is carefully calibrated to match the thickness and material properties of the HR strip.
4. Scrap Handling Phase: While the slitting is taking place, the scrap generated at the edges of the cut strips is collected by the scrap winders. The scrap winders continuously wind up the scrap, keeping the work area clean and free from any obstructions that could disrupt the slitting process. The collected scrap is then either stored for recycling or further processed immediately, depending on the plant's recycling capabilities and production schedule.
5. Winding Phase: The slit strips then move towards the take - up reels. Each take - up reel winds one of the slit strips into a coil. The motors driving the take - up reels maintain a consistent tension on the strips during the winding process, ensuring that the coils are tightly and evenly wound. Once the coil reaches its desired diameter, the take - up reel stops, and the full coil can be transferred for further processing or storage.
4. Applications
4.1 Construction Industry
In the construction industry, HR coil slitting machines play a vital role. The construction sector requires large quantities of steel strips for various applications. For example, in the production of steel joists and trusses, HR strips are slit to specific widths and lengths. These strips are then formed and welded to create the structural components of buildings. The accurate slitting of HR coils ensures that the joists and trusses have the correct dimensions, which is crucial for the overall strength and stability of the construction. Additionally, HR slit strips are used for roofing and siding materials. They can be further processed into corrugated sheets, and the precise slitting allows for easy installation and a watertight fit. In large - scale infrastructure projects, such as bridges and industrial buildings, the high - volume production capabilities of HR coil slitting machines are essential to meet the demand for construction materials.
4.2 Automotive Industry
The automotive industry also benefits from HR coil slitting machines, although to a somewhat different extent compared to the construction industry. HR coils are used in the manufacturing of certain automotive components, such as the frames of heavy - duty trucks and some parts of the chassis. The slitting of HR coils into the appropriate strip widths and lengths enables the efficient production of these components. For example, the frame rails of trucks often require thick - gauge steel strips, which can be produced by slitting HR coils. The high - precision slitting ensures that the components fit together perfectly during the assembly process, contributing to the overall safety and durability of the vehicle.
4.3 Pipe Manufacturing
HR coil slitting machines are extensively used in the pipe - manufacturing industry. The slit HR strips are formed into pipes through a series of bending and welding processes. The width and thickness of the slit strips are precisely controlled to meet the specifications of different pipe sizes and applications. For example, in the production of large - diameter pipes for oil and gas transportation, the slitting of HR coils provides the raw material that can be shaped into the required pipe dimensions. The consistent quality of the slit strips, achieved through the accurate operation of the slitting machine, ensures the integrity and reliability of the pipes.
4.4 General Fabrication
In general metal fabrication workshops, HR coil slitting machines are used to produce a wide range of products. From metal furniture components to industrial machinery parts, the ability to slit HR coils into custom - sized strips allows fabricators to meet the diverse needs of their customers. For example, in the production of metal cabinets or storage units, HR slit strips can be cut and formed into the various panels and frames. The versatility of the HR coil slitting machine in handling different strip widths and thicknesses makes it a valuable asset in the general fabrication sector.
5. Advantages
5.1 High - Volume Production
HR coil slitting machines are designed for high - volume production. They can process large - diameter HR coils at a relatively high speed, significantly reducing the production time per unit of slit strip. The automated nature of the process, from unwinding to winding, minimizes the need for manual intervention, further enhancing productivity. In a large - scale steel - processing plant, an HR coil slitting machine can produce thousands of meters of slit strips per hour, meeting the high - demand requirements of industries such as construction and pipe manufacturing.
5.2 Cost - Efficiency
Using an HR coil slitting machine can be cost - efficient in the long run. By producing precisely cut strips, it reduces material waste. Instead of purchasing pre - cut steel strips, which may have a higher cost due to additional processing and handling, companies can slit HR coils in - house according to their exact needs. The high - volume production capabilities also spread the fixed costs of the slitting machine over a large number of units, reducing the per - unit production cost. Additionally, the ability to recycle the scrap generated during the slitting process further contributes to cost savings.
5.3 Material Compatibility
These machines are highly compatible with hot - rolled materials. They can handle different grades of hot - rolled steel, including carbon steel, alloy steel, and some stainless - steel grades. The robust construction and powerful cutting mechanisms of HR coil slitting machines are designed to deal with the relatively thick and tough nature of HR coils. Whether it is a low - carbon HR steel for general construction applications or a high - strength alloy HR steel for automotive or industrial components, the slitting machine can effectively process the material.
5.4 Precision and Quality
Despite the large - scale and high - volume nature of the production, HR coil slitting machines can achieve a high level of precision. The advanced control systems and precise slitting knives ensure that the slit strips have tight width tolerances. This precision is crucial for downstream processes, such as welding and forming. In applications where a perfect fit of components is required, such as in the construction of high - rise buildings or the manufacturing of complex automotive parts, the quality of the slit strips produced by the slitting machine is essential.
6. Challenges
6.1 High Initial Investment
The purchase and installation of an HR coil slitting machine represent a significant capital investment. The cost of the equipment can range from several hundred thousand dollars to millions, depending on its size, capabilities, and the level of automation. In addition to the cost of the slitting machine itself, there are also expenses associated with infrastructure development. This includes a suitable workshop space with high - load - bearing floors to support the heavy coils and equipment, a powerful electrical system to power the high - torque motors, and proper ventilation to dissipate heat generated during the slitting process. Small and medium - sized enterprises may find it difficult to afford such high - cost equipment, which can limit their growth and competitiveness in the market.
6.2 Maintenance and Calibration
To ensure the continued high - precision and efficient operation of the HR coil slitting machine, regular maintenance and calibration are essential. The slitting knives need to be sharpened or replaced regularly due to the wear and tear caused by cutting the tough HR materials. The rolls in the leveler and the tension - control systems also require periodic inspection and maintenance. Calibration of the measuring and control systems is crucial to ensure accurate strip - width settings and tension control. Any deviation in calibration can lead to inaccurate slitting and reduced product quality. Maintenance and calibration require skilled technicians and can be time - consuming and costly.
6.3 Skilled Labor Requirement
Operating and maintaining an HR coil slitting machine demands a high level of technical expertise. Workers need to be trained in setting up the machine, programming the control system, adjusting the slitting knives and tension levels, and troubleshooting any issues that may arise during operation. The shortage of skilled labor in some regions can pose a challenge to the efficient use of these machines. Employers may need to invest in comprehensive training programs or hire experienced technicians, which can add to the overall operational costs.
6.4 Quality Control
Ensuring consistent quality of the slit HR strips is a complex task. Variations in the HR coil material, such as differences in hardness, thickness, and chemical composition, can affect the slitting process and the quality of the final product. Any misalignment of the slitting knives, improper tension control, or wear and tear of the equipment can also lead to quality issues, such as uneven strip widths, burrs on the edges, and inconsistent coil winding. Implementing effective quality - control measures, such as regular inspections, in - line monitoring, and statistical process control, is essential but can be resource - intensive and time - consuming.
7. Future Trends
7.1 Integration of Smart Technologies
The future of HR coil slitting machines lies in the integration of smart technologies, such as the Internet of Things (IoT), artificial intelligence (AI), and machine learning (ML). IoT sensors can be installed on the slitting machine to monitor various parameters, such as temperature, vibration, and cutting forces, in real - time. This data can be transmitted to a central control system, where AI and ML algorithms can analyze it to predict equipment failures, optimize cutting parameters, and improve overall efficiency. For example, AI can adjust the cutting speed and tension based on the real - time condition of the HR strip and the cutting tool, reducing the risk of tool wear and improving the quality of the cuts.
7.2 Energy - Efficiency Improvements
As environmental concerns and energy - cost pressures increase, there will be a growing focus on improving the energy efficiency of HR coil slitting machines. This may involve the use of more energy - efficient motors, advanced control systems that optimize power consumption, and the development of innovative slitting technologies that require less energy. For example, new cutting - knife materials and designs may be developed to reduce the cutting forces required, thereby reducing the power consumption of the slitting unit.
7.3 Customization and Flexibility
In response to the increasing demand for customized products in various industries, HR coil slitting machines will likely become more customizable and flexible. Manufacturers will be able to adjust the slitting machine to produce a wider range of strip widths, thicknesses, and edge qualities. This will allow them to better meet the specific requirements of individual customers and serve niche markets more effectively. For example, in the production of specialized automotive components or high - end construction products, the ability to produce custom - sized HR slit strips will be a competitive advantage.
In conclusion, the HR coil slitting machine is an indispensable piece of equipment in the metal - processing industry, especially for applications involving hot - rolled materials. Its components, working principle, wide - ranging applications, numerous advantages, and the challenges it faces all contribute to its significance in modern manufacturing. With the advent of new technologies and the evolving demands of various industries, the HR coil slitting machine is set to undergo further advancements, continuing to play a pivotal role in the production of metal - based products.