Hotline
+86-136 8495 9862
Email:cennia@szmizhi.com
Add::104,Building 27,Third Industrial Zone, Longxi Community,Longgang District,Shenzhen,China.
Coil Forming & Handling Equipment
Surface Treatment Equipment
Solutions
Application
About Us
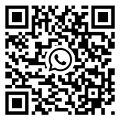
Welcome to MIZHI
For consultation/feedback, please call the service hotline: +86-136 8495 9862 Email:cennia@szmizhi.com
1. Introduction
In the manufacturing and industrial sectors, there is often a need to treat large - scale suspended workpieces, such as large metal structures, automotive body frames, and industrial machinery components. These workpieces require a comprehensive and efficient surface treatment process to ensure their quality, durability, and functionality. The high - capacity hanger hook shot blasting machine has been developed to meet these specific requirements. This specialized machine is designed to handle large - sized workpieces that are suspended from hanger hooks, providing an effective method of shot blasting to clean, strengthen, and prepare their surfaces.
2. Working Principle
2.1 Hanger Hook Suspension System
The hanger hook shot blasting machine features a robust and well - engineered hanger hook suspension system. This system consists of a series of strong and durable hooks that are attached to a conveyor mechanism. The hooks are designed to securely hold large - scale suspended workpieces of various shapes and weights. The conveyor can be either a monorail system, which allows for linear movement of the workpieces, or a more complex overhead trolley system that can provide multi - directional movement within the shot blasting chamber.
Workpieces are carefully loaded onto the hanger hooks at the loading station. Specialized fixtures or adaptors can be used to ensure a stable and secure attachment of the workpieces to the hooks. Once loaded, the conveyor system moves the suspended workpieces into the shot blasting chamber. The movement of the conveyor can be adjusted to control the speed at which the workpieces pass through the blasting area, allowing for customization based on the specific requirements of the surface treatment.
2.2 Shot Blasting Unit
The shot blasting unit is the core component responsible for the actual surface treatment of the suspended workpieces. This unit typically comprises multiple high - power centrifugal wheels or a combination of centrifugal wheels and high - pressure nozzles.
Centrifugal wheels are a common and highly effective component in the shot blasting process. These wheels are equipped with precision - engineered vanes. Abrasive media, such as metal or ceramic shots, are fed into the center of the centrifugal wheels. As the wheels rotate at high speeds, typically ranging from 1000 to 3000 revolutions per minute, the abrasive media is accelerated to extremely high velocities, often exceeding 100 meters per second. The high - speed shots are then flung outwards from the vanes of the centrifugal wheels, impacting the surface of the suspended workpieces with great force.
Multiple centrifugal wheels are strategically positioned around the area where the suspended workpieces move within the shot blasting chamber. This arrangement ensures that all surfaces of the workpieces, including complex geometries and hard - to - reach areas, are exposed to the abrasive media. The orientation and angle of the centrifugal wheels can be adjusted to target specific areas of the workpiece more effectively.
In some cases, high - pressure nozzles may be incorporated into the shot blasting unit. These nozzles can deliver a highly concentrated and focused stream of abrasive media at high pressures. They are particularly useful for treating areas that require more targeted or intensive surface treatment, such as corners, edges, or areas with thick coatings or contaminants.
2.3 Abrasive Media Recycling and Separation
Efficient use of abrasive media is crucial in large - scale operations to keep production costs down. The high - capacity hanger hook shot blasting machine is equipped with an advanced abrasive media recycling and separation system.
After the abrasive media impacts the surface of the suspended workpieces and falls to the bottom of the shot blasting chamber, it is collected through a series of chutes and conveyor belts. The used media is then passed through a separation process. This process typically involves a combination of mechanical sieving to remove large debris and magnetic separation (if the abrasive media is ferromagnetic) to extract any metal particles that may have been worn off the workpieces or the machine components during the blasting process.
The clean and reusable abrasive media is then recycled back into the shot blasting unit, ready for the next cycle of treatment. This closed - loop system not only reduces the cost of constantly purchasing new abrasive media but also minimizes environmental waste, making it an environmentally friendly and cost - effective solution for large - scale surface treatment operations.
3. Advantages for Large - Scale Suspended Workpieces
3.1 High - Capacity Handling
1. Accommodation of Large - Sized Workpieces: The hanger hook suspension system is designed to handle large - scale suspended workpieces with ease. Whether it's a massive industrial crane component that weighs several tons or a large - sized automotive body frame, the machine can securely hold and transport these workpieces through the shot blasting process. The robust construction of the hooks and the conveyor system ensures that even the largest and heaviest workpieces can be treated without any risk of instability or damage during handling.
2. Increased Throughput: In large - scale manufacturing and industrial applications, throughput is a critical factor. The high - capacity hanger hook shot blasting machine can process multiple workpieces simultaneously. By optimizing the movement of the conveyor system and the arrangement of the shot blasting units, the machine can achieve a high rate of production. For example, in a large - scale automotive manufacturing plant that produces hundreds of body frames per day, the machine can efficiently handle the volume, reducing the overall production time and increasing productivity.
3.2 Comprehensive Surface Treatment
1. Uniform Coverage: The strategic positioning of the centrifugal wheels and, if applicable, high - pressure nozzles around the path of the suspended workpieces ensures uniform coverage of the entire surface area. As the workpieces move through the shot blasting chamber, all sides, corners, and recessed areas are exposed to the abrasive media. This comprehensive coverage is essential for achieving a consistent surface finish and ensuring that all parts of the workpiece receive the necessary surface treatment. Whether it's a complex - shaped industrial machine part with intricate details or a simple - shaped but large - sized metal structure, the machine can provide a uniform treatment across the entire surface.
2. Customizable Treatment Intensity: The machine offers a high degree of control over the treatment intensity. Operators can adjust parameters such as the speed of the centrifugal wheels (which determines the velocity of the abrasive shots), the pressure of the high - pressure nozzles (if used), and the speed at which the workpieces move through the blasting area. This allows for customization of the surface treatment based on the specific requirements of the workpiece material, the existing surface condition, and the desired final surface finish. For example, for workpieces with thick rust or scale deposits, a more intense treatment can be applied, while for delicate or pre - finished surfaces, a gentler treatment can be achieved.
3.3 Cost - Efficiency
1. Reduced Labor Costs: The automated nature of the high - capacity hanger hook shot blasting machine significantly reduces the need for manual labor. In traditional surface treatment methods for large - scale workpieces, workers may need to manually apply abrasive media or use handheld tools for cleaning and surface preparation, which is extremely time - consuming and labor - intensive. With this machine, the only human intervention required is loading and unloading the workpieces, as well as monitoring the machine's operation. This not only cuts down on labor costs but also reduces the variability in the quality of surface treatment that may be associated with manual work, leading to more consistent product quality.
2. Efficient Abrasive Usage: The abrasive media recycling and separation system ensures that the abrasive media is used efficiently. In large - scale operations, the cost of abrasive media can be a significant expense. By recycling and reusing the shots, manufacturers can save a substantial amount of money over time. Additionally, the reduced need to dispose of used abrasive media also reduces environmental costs associated with waste management.
4. Applications in Different Industries
4.1 Automotive Industry
1. Body Frame Manufacturing: In the automotive industry, the production of body frames is a crucial process. Body frames are large - scale suspended workpieces that require a high - quality surface treatment. The hanger hook shot blasting machine can effectively clean the surface of body frames, removing any rust, welding splatter, or contaminants. The shot - peening effect of the blasting process also strengthens the surface, improving the structural integrity and durability of the body frame. This is essential for ensuring the safety and performance of the vehicle.
2. Large - Sized Automotive Components: There are various large - sized components in an automobile, such as suspension parts, engine cradles, and large - scale brackets. These components need to have a clean and corrosion - resistant surface. The high - capacity hanger hook shot blasting machine can handle these components, providing a uniform surface treatment that enhances their resistance to environmental factors and improves their lifespan.
4.2 Construction and Infrastructure Industry
1. Steel Bridge Components: The construction of steel bridges involves large - scale steel components such as beams, girders, and trusses. These components need to be thoroughly cleaned and surface - treated to prevent corrosion and ensure long - term structural integrity. The hanger hook shot blasting machine can handle the large size and weight of these components, effectively removing rust, mill scale, and other impurities. The surface roughness created by the shot blasting process also improves the adhesion of protective coatings, which are essential for protecting the steel components from the harsh environmental conditions.
2. Industrial Crane and Machinery Structures: Industrial cranes and large - scale machinery often have large metal structures that require regular surface treatment. The high - capacity hanger hook shot blasting machine can be used to clean and strengthen these structures. By removing rust and improving the surface quality, the machine helps to maintain the safety and reliability of these critical industrial equipment.
4.3 Shipbuilding Industry
1. Ship Hull Sections: Ship hull sections are massive suspended workpieces that need to be surface - treated to prevent corrosion in the harsh marine environment. The hanger hook shot blasting machine can effectively clean the surface of ship hull sections, removing any contaminants and preparing the surface for anti - corrosion coatings. The uniform surface treatment provided by the machine ensures that the entire hull section is protected, reducing the risk of corrosion - related damage and extending the lifespan of the ship.
2. Large - Scale Ship Components: Shipbuilding also involves the production of large - scale components such as propellers, rudders, and masts. These components require a high - quality surface treatment to ensure their proper functioning. The high - capacity hanger hook shot blasting machine can handle these components, providing a surface treatment that meets the strict requirements of the shipbuilding industry.
5. Operation and Maintenance
5.1 Operation
1. Initial Setup: Before starting the treatment of large - scale suspended workpieces, the machine needs to be carefully set up. This involves selecting the appropriate hanger hooks and fixtures for the specific workpieces. The speed of the conveyor system, the intensity of the shot blasting (by adjusting the speed of the centrifugal wheels or the pressure of the nozzles), and the type and size of abrasive media need to be adjusted according to the requirements of the workpiece. Safety checks must be carried out to ensure that all protective guards are in place and the machine is in proper working condition.
2. Loading and Unloading: Large - scale suspended workpieces are carefully loaded onto the hanger hooks at the loading station. The operator needs to ensure that the workpieces are securely attached to the hooks and are properly positioned for the shot blasting process. At the unloading station, the treated workpieces are carefully removed from the hooks. After unloading, the workpieces are inspected for quality. If any issues are detected, such as uneven surface treatment or damage, the machine settings may need to be adjusted for the next batch.
3. Monitoring: During the operation, the operator should continuously monitor the machine. This includes checking the performance of the shot blasting units, ensuring that the conveyor system is moving smoothly, and observing the quality of the treated workpieces. If any issues are detected, such as abnormal noise from the machine, inconsistent shot flow, or problems with the abrasive media recycling system, the machine should be stopped immediately for troubleshooting.
5.2 Maintenance
1. Regular Inspection: Regular inspection of the machine is essential to ensure its long - term reliable operation. Components such as the hanger hook suspension system, centrifugal wheels, nozzles (if applicable), and abrasive media recycling system should be inspected for wear and tear. The hooks and the conveyor system may need to be checked for any signs of fatigue or damage, especially when handling heavy workpieces. The vanes on the centrifugal wheels, which are subject to high - velocity impacts from the abrasive media, should be checked for erosion and replaced when necessary. The abrasive media recycling system should be inspected to ensure that there are no blockages in the chutes or conveyors.
2. Lubrication: Proper lubrication of moving parts is crucial for the smooth operation of the machine. The bearings on the conveyor system and the motors driving the shot - blasting units need to be lubricated regularly to reduce friction and prevent premature failure. This helps to maintain the accuracy and efficiency of the machine and reduces the risk of breakdowns during large - scale production.
3. Abrasive Media Management: The quality of the abrasive media also needs to be carefully managed. Over time, the abrasive shots may become worn or contaminated. The operator should periodically check the quality of the recycled abrasive and add new abrasive as needed to maintain the effectiveness of the shot blasting process. The type and size of the abrasive media may also need to be adjusted depending on the changing requirements of the workpiece production.
6. Conclusion
The high - capacity hanger hook shot blasting machine has emerged as an essential tool in industries that deal with large - scale suspended workpieces. Its unique combination of high - capacity handling, comprehensive surface treatment capabilities, and cost - efficiency makes it the preferred choice for surface treatment in these applications. By understanding its working principle, operation, and maintenance requirements, manufacturers and industrial operators can fully leverage the capabilities of this machine to enhance the quality and productivity of their large - scale workpiece production processes. As technology continues to advance, it is expected that further improvements will be made to the high - capacity hanger hook shot blasting machine, further expanding its applications and improving its performance in large - scale manufacturing and industrial operations.