Hotline
+86-136 8495 9862
Email:cennia@szmizhi.com
Add::104,Building 27,Third Industrial Zone, Longxi Community,Longgang District,Shenzhen,China.
Coil Forming & Handling Equipment
Surface Treatment Equipment
Solutions
Application
About Us
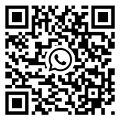
Welcome to MIZHI
For consultation/feedback, please call the service hotline: +86-136 8495 9862 Email:cennia@szmizhi.com
In the world of manufacturing and metalworking, achieving intricate and precise surface finishes is of utmost importance, especially when dealing with fine filigree patterns. The High Precision Wire Mesh Shot Blasting Machine has emerged as a game - changing solution in this regard. This advanced piece of equipment is designed to meet the stringent requirements of industries such as jewelry making, precision engineering, and decorative metalwork, where the preservation and enhancement of delicate patterns are crucial.
Understanding Filigree Patterns
Filigree patterns are characterized by their extremely delicate and intricate designs. These patterns are often crafted by twisting, bending, and soldering fine wires together to create elaborate motifs. In jewelry, for example, filigree work can add a touch of elegance and luxury. In precision engineering, filigree - like patterns might be used in components where lightweighting and aesthetic appeal are combined. However, these delicate patterns are vulnerable during surface treatment processes. Traditional surface treatment methods such as simple sandblasting can easily damage or distort these fine details.
The Need for High Precision in Shot Blasting
Shot blasting is a common surface treatment process that involves propelling small particles (shots) at the surface of a workpiece to clean, roughen, or peen the surface. When it comes to fine filigree patterns, standard shot blasting machines fall short. The force and imprecision of regular shot blasting can break the thin wires or flatten the raised patterns. A high - precision wire mesh shot blasting machine is essential to ensure that the shots are directed accurately and with the right amount of force. This machine allows for the removal of contaminants, oxidation, and the creation of a uniform surface finish without harming the intricate filigree work.
Working Principle of the High Precision Wire Mesh Shot Blasting Machine
1. Wire Mesh System
The core feature of this machine is its wire mesh system. The wire mesh is carefully designed with a specific aperture size that determines the size and trajectory of the shots. The mesh acts as a filter and a guide, ensuring that only shots of the appropriate size pass through and are directed towards the workpiece. This prevents larger, potentially damaging shots from reaching the filigree pattern. For example, in a machine designed for very fine filigree work in jewelry, the wire mesh might have an aperture size in the range of 0.1 - 0.5 mm, allowing only small, fine - grained shots to be used.
2. Shot Propulsion and Control
The machine uses a high - pressure air or mechanical system to propel the shots towards the workpiece. The pressure and speed of the shot propulsion can be precisely adjusted. In a modern high - precision wire mesh shot blasting machine, advanced control systems are in place. These systems can be programmed to vary the shot intensity based on different areas of the filigree pattern. For instance, areas with more delicate details can be treated with a lower shot pressure, while areas that can withstand more force can be subjected to a higher pressure for more efficient cleaning or surface modification.
3. Workpiece Handling and Rotation
To ensure even treatment of the entire filigree - patterned workpiece, the machine is equipped with a sophisticated workpiece handling and rotation mechanism. The workpiece is held securely in place, and it can be rotated or moved in a controlled manner during the shot blasting process. This ensures that every part of the filigree pattern is exposed to the shots evenly, without over - treating one area while under - treating another. In some cases, the machine can be integrated with robotic arms for even more precise movement and positioning of the workpiece.
Applications in Different Industries
1. Jewelry Industry
In the jewelry industry, filigree work is highly valued for its aesthetic appeal. High Precision Wire Mesh Shot Blasting Machines are used to clean and finish filigree - based jewelry pieces. For example, a necklace with intricate filigree pendants can be treated to remove any residue from the manufacturing process, such as polishing compounds or oxidation. The machine can enhance the luster of the metal while maintaining the integrity of the delicate wirework. This results in a more vibrant and refined final product, increasing its market value.
2. Precision Engineering
In precision engineering, components with filigree - like patterns are used in areas such as aerospace and micro - electronics. These patterns are often designed to reduce weight while maintaining structural integrity. The High Precision Wire Mesh Shot Blasting Machine can be used to clean and prepare these components for further processing, such as bonding or coating. By using this machine, manufacturers can ensure that the fine patterns on these critical components are not damaged, which is essential for their proper functioning.
3. Decorative Metalwork
Decorative metalwork, such as wrought iron gates or metal art installations with filigree patterns, also benefits from the use of this machine. The shot blasting process can remove rust, paint, or other contaminants from the surface, restoring the original beauty of the filigree. It can also be used to create a uniform texture on the surface, enhancing the overall visual appeal of the decorative piece.
Advantages over Traditional Surface Treatment Methods
1. Superior Precision
As mentioned earlier, the wire mesh system and precise shot control make this machine far more precise than traditional shot blasting or other surface treatment methods. It can target specific areas of the filigree pattern with a high degree of accuracy, ensuring that only the desired surface changes occur.
2. Reduced Damage Risk
Traditional methods like sandblasting or abrasive blasting with large - sized media can easily break or distort the fine wires in filigree patterns. The High Precision Wire Mesh Shot Blasting Machine, with its carefully selected shot size and controlled force, minimizes the risk of damage to the delicate patterns.
3. Consistent Results
The advanced control systems in the machine allow for consistent results across multiple workpieces. Whether it's a batch of jewelry pendants or a series of precision engineering components, the machine can replicate the same high - quality surface treatment every time, ensuring product uniformity.
Challenges and Solutions in Using High Precision Wire Mesh Shot Blasting Machines
1. Shot Clogging in the Wire Mesh
One potential challenge is shot clogging in the wire mesh. If the shots are not of uniform size or if there are contaminants in the shot material, they can get stuck in the mesh apertures. To solve this problem, manufacturers often use shot cleaning and sieving systems before loading the shots into the machine. Additionally, the wire mesh can be designed with self - cleaning features, such as vibrating mechanisms, to dislodge any stuck shots.
2. High Initial Cost
The high precision and advanced technology of these machines come with a relatively high initial cost. However, in the long run, the benefits in terms of reduced rework, higher product quality, and increased production efficiency can offset this cost. Manufacturers can also consider leasing options or investing in machines with modular designs that can be upgraded over time, reducing the initial financial burden.
Future Developments and Trends
1. Integration of Smart Technologies
In the future, High Precision Wire Mesh Shot Blasting Machines are likely to be integrated with more smart technologies. This could include sensors that can detect the condition of the wire mesh in real - time, automatically adjusting the shot blasting parameters if any wear or clogging is detected. Machine learning algorithms could also be used to optimize the shot blasting process based on the characteristics of different filigree patterns.
2. Miniaturization and Portability
There will be a trend towards miniaturization and portability of these machines. This would make them more accessible to small - scale manufacturers, such as independent jewelry makers or artisans. Miniature versions of the machines could be designed for bench - top use, while still maintaining the high - precision capabilities of their larger counterparts.
3. Environmentally Friendly Shots
As environmental concerns grow, there will be a push towards using more environmentally friendly shot materials. For example, biodegradable or recyclable shot materials could be developed for use in these machines. This would reduce the environmental impact of the shot blasting process without sacrificing the precision and effectiveness of the treatment.
In conclusion, the High Precision Wire Mesh Shot Blasting Machine is a remarkable innovation in the field of surface treatment for fine filigree patterns. It has already made a significant impact in various industries, and with continued technological advancements, it is set to become an even more indispensable tool in the manufacturing and metalworking sectors.