Hotline
+86-136 8495 9862
Email:cennia@szmizhi.com
Add::104,Building 27,Third Industrial Zone, Longxi Community,Longgang District,Shenzhen,China.
Coil Forming & Handling Equipment
Surface Treatment Equipment
Solutions
Application
About Us
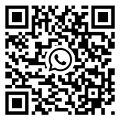
Welcome to MIZHI
For consultation/feedback, please call the service hotline: +86-136 8495 9862 Email:cennia@szmizhi.com
I. Introduction
In the dynamic world of modern manufacturing, the high-speed cut to length line has emerged as a game-changer. It represents a pinnacle of technological advancement in the metal processing industry, enabling manufacturers to meet the ever-increasing demands for efficiency, precision, and productivity. This sophisticated production system is designed to rapidly transform raw metal coils into accurately cut sheets or strips of predetermined lengths, catering to a wide array of industries such as automotive, electronics, construction, and appliance manufacturing.
II. Key Components and Their Functions
1. High-Power Uncoiling System
At the front end of the line, the high-power uncoiling system takes center stage. It is equipped with a heavy-duty mandrel or expansion shaft that can securely hold large and heavy metal coils, sometimes weighing several tons. The uncoiling speed is precisely controlled by advanced variable speed drives, which ensure a smooth and consistent unwinding of the metal strip. For instance, in an automotive stamping plant that requires a continuous supply of precisely cut steel sheets for body panel production, the uncoiling system must be able to handle high-capacity coils and maintain a steady feed rate to keep up with the downstream cutting operations.
Tension control mechanisms are of utmost importance. These utilize load cells and feedback control loops to monitor and adjust the tension on the unwinding metal. By maintaining the ideal tension, issues like strip wrinkling, sagging, or snapping are prevented. This is critical in the production of thin-gauge metal sheets for electronics components, where even the slightest deformation can lead to product failure.
2. Precision Leveling Unit
Once the metal strip is uncoiled, it enters the precision leveling unit. Metal coils, especially those stored for extended periods or transported over long distances, often develop internal stresses that result in warping or curling. The leveling unit employs a series of meticulously calibrated rollers, arranged in a specific pattern. These rollers apply controlled forces to flatten the metal, eliminating residual stresses and ensuring a perfectly flat surface. In the production of high-precision sheet metal for aerospace applications, where tight tolerances are essential, the leveling process can make the difference between a successful and a faulty component.
3. Ultra-Fast Cutting Unit
The ultra-fast cutting unit is the heart and soul of the high-speed cut to length line. Depending on the material characteristics and production requirements, various cutting technologies are employed. For thick metal sheets, high-capacity shearing machines are used. These machines can exert tremendous force to make clean, straight cuts at astonishing speeds. In the construction of heavy machinery, where thick steel plates are required, shearing-based cutting units prove their worth.
For thinner materials, advanced rotary cutters or high-power laser cutting systems dominate. Rotary cutters with razor-sharp blades rotating at extremely high RPMs can slice through metal with remarkable precision and speed. Laser cutting, on the other hand, offers unparalleled accuracy and the ability to create intricate shapes and patterns. In the electronics industry, where micro-sized components demand precise geometries, laser cutting is often the preferred choice. The cutting unit is synchronized with the upstream and downstream processes through state-of-the-art control systems, ensuring minimal waste and maximum accuracy.
4. High-Efficiency Stacking and Packaging Unit
After the metal sheets are cut to the desired lengths, they are quickly transferred to the high-efficiency stacking and packaging unit. Automated stacking mechanisms arrange the sheets in neat piles, optimizing space utilization. These stacks can then be bundled together using strong straps or shrink-wrapped for easy transportation and storage. In a busy steel service center, the stacking and packaging process must be streamlined to handle large volumes of cut sheets, ensuring they are protected and ready for shipment to customers.
III. Operation and Workflow
1. Pre-Operation Setup
Before commencing production, operators must carefully load the appropriate metal coil onto the uncoiling system. This involves precise alignment of the coil and proper engagement with the mandrel. The leveling, cutting, and stacking parameters are then configured based on the job specifications. For example, if manufacturing sheets for a particular smartphone model, the thickness, width, length, and even surface finish requirements are entered into the control system. The cutting unit's power, speed, and blade or laser settings are adjusted accordingly.
2. High-Speed Continuous Production
Once the setup is complete, the high-speed cut to length line springs into action. The metal coil unwinds rapidly, passes through the leveling unit to be flattened, and then reaches the cutting unit. Here, it is sliced into precise lengths at breakneck speeds. The cut sheets are immediately transferred to the stacking and packaging unit, where they are organized and prepared for further processing or shipment. Throughout this process, an array of sensors and feedback loops constantly monitor the quality of the metal strip, the cutting accuracy, and the stack height. Any deviations are detected and corrected in real-time, ensuring optimal performance.
3. Rigorous Quality Control
Quality control is an integral part of the high-speed cut to length line's operation. Advanced visual inspection systems, equipped with high-resolution cameras and image processing software, scan the metal sheets for surface defects such as scratches, dents, or discoloration. Dimensional measurement tools, like laser gauges and precision calipers, check the cut lengths, widths, and thicknesses against the tightest tolerances. In case of any non-compliance, the production line can be halted automatically, and an alarm raised to alert the operators. This ensures that only top-notch, accurately cut metal sheets are released for downstream use.
IV. Advantages of High-Speed Cut to Length Lines
1. Unmatched Productivity
The primary advantage of these lines is their ability to achieve extraordinary production rates. By operating at high speeds and with minimal downtime for coil changes or maintenance, they can churn out vast quantities of accurately cut metal sheets. In a large-scale appliance manufacturing facility, a high-speed cut to length line can meet the daily demand for thousands of metal components, significantly shortening production cycles and increasing overall output.
2. Exceptional Precision
Despite the high speeds, these lines do not compromise on precision. Thanks to advanced control systems and cutting technologies, the cut lengths and dimensions of the metal sheets are maintained within extremely tight tolerances. This is crucial in industries like aerospace and electronics, where the slightest deviation can lead to catastrophic failures or subpar performance. For example, in the production of satellite components, the precision of the cut metal parts directly impacts the functionality and reliability of the entire spacecraft.
3. Cost-Effectiveness
High-speed cut to length lines offer significant cost savings. The rapid production rate reduces labor costs per unit, as fewer operators are required to oversee the process. Moreover, the precise cutting and minimal waste generation mean that raw materials are used more efficiently. This not only cuts down on material costs but also reduces the environmental footprint associated with metal processing. In the long run, these lines prove to be a cost-effective investment for manufacturers.
V. Applications in Different Industries
1. Automotive Industry
In the automotive sector, high-speed cut to length lines are indispensable. They supply the precisely cut steel and aluminum sheets needed for body panels, chassis components, and engine parts. The ability to quickly produce high-quality metal parts at scale enables automotive manufacturers to meet the growing demand for vehicles while maintaining strict quality standards. For instance, in the production of a new car model, thousands of identically sized and shaped metal sheets are required, and these lines ensure a seamless supply.
2. Electronics Industry
For the electronics industry, the precision and speed of these lines are vital. They are used to cut thin metal sheets for circuit boards, casings, and connectors. The micro-sized components demand extremely tight tolerances, and the high-speed cut to length line can deliver. In the manufacture of smartphones, tablets, and other portable devices, the quality of the cut metal parts can directly affect the device's performance and durability.
3. Construction Industry
In construction, high-speed cut to length lines play a significant role in processing steel and other metal building materials. They can quickly produce the required lengths of metal studs, roofing sheets, and siding panels. This not only speeds up construction projects but also ensures the quality and consistency of the metal components used. For a large commercial building project, the line can provide the necessary metal materials in a timely manner, reducing construction delays.
VI. Maintenance and Safety Considerations
1. Maintenance
Regular maintenance is essential to keep the high-speed cut to length line operating at peak performance. The rollers in the uncoiling, leveling, and transport systems need to be lubricated and inspected for wear and tear. The cutting blades, whether shearing or rotary, must be sharpened or replaced frequently. The control systems and sensors require regular calibration to ensure accurate operation. Manufacturers typically provide detailed maintenance schedules and procedures, which operators should adhere to strictly.
2. Safety
Given the high speeds and powerful machinery involved, safety is a paramount concern. Safety guards are installed around all dangerous areas, including the uncoiling, leveling, and cutting units. Emergency stop buttons are strategically placed throughout the line, allowing for immediate shutdown in case of an emergency. Operators are trained in proper safety procedures and must wear appropriate personal protective equipment such as safety glasses, gloves, and hard hats. Additionally, safety interlocks prevent unauthorized access to the operating area while the line is running.
VII. Future Trends and Developments
As technology continues to advance, high-speed cut to length lines are expected to evolve further. New cutting technologies, such as fiber lasers with even higher power and precision, may be incorporated. The control systems will likely become more intelligent, with the ability to predict and prevent maintenance issues before they occur. Integration with other manufacturing processes, such as robotic assembly and automated warehousing, will also enhance overall productivity. Moreover, the lines will continue to adapt to the changing demands of emerging industries, such as renewable energy and advanced materials, ensuring their continued relevance and importance in the global manufacturing landscape.
VIII. Conclusion
The high-speed cut to length line has redefined metal processing. Its combination of speed, precision, and productivity has made it an essential tool in multiple industries. By enabling manufacturers to meet the demands of modern production, it has contributed to the growth and innovation of the global economy. As we look to the future, continued advancements in this technology will surely unlock new possibilities and drive further progress in manufacturing. Whether it's building the next generation of automobiles, electronics, or infrastructure, the high-speed cut to length line will be at the forefront, shaping the way we create and build.