Hotline
+86-136 8495 9862
Email:cennia@szmizhi.com
Add::104,Building 27,Third Industrial Zone, Longxi Community,Longgang District,Shenzhen,China.
Coil Forming & Handling Equipment
Surface Treatment Equipment
Solutions
Application
About Us
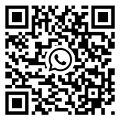
Welcome to MIZHI
For consultation/feedback, please call the service hotline: +86-136 8495 9862 Email:cennia@szmizhi.com
Introduction:
In the world of industrial manufacturing, high speed slitting lines are essential tools for processing large coils of various materials into narrower strips with precision and efficiency. These advanced machines play a crucial role in meeting the growing demand for customized materials in industries such as packaging, automotive, construction, and electronics.
The high speed slitting line combines cutting-edge technology with robust construction to ensure seamless operation and consistent quality output. With its ability to handle high volumes of material at rapid speeds, this equipment is a key driver of productivity and profitability for businesses across different sectors.
Design and Construction:
The design of a high speed slitting line is a complex engineering feat that takes into account multiple factors such as material properties, production requirements, and safety standards. The machine typically consists of several key components, including a decoiler, a slitting head, a tension control system, a recoiler, and various auxiliary equipment.
The decoiler is responsible for unwinding the large coil of material and feeding it into the slitting line. It is designed to handle different coil sizes and weights, and may be equipped with features such as automatic coil loading and unloading systems for increased efficiency.
The slitting head is the heart of the high speed slitting line. It consists of a set of circular knives or blades that cut the material into narrower strips. The design of the slitting head must ensure accurate and clean cuts, while also being able to handle high speeds and different material thicknesses. Advanced slitting heads may feature adjustable knife spacing, automatic knife sharpening systems, and precision alignment mechanisms to ensure optimal performance.
The tension control system is crucial for maintaining consistent tension on the material throughout the slitting process. This helps to ensure accurate cuts and prevent wrinkling or stretching of the material. The tension control system may consist of tension sensors, brake systems, and motor drives that work together to maintain the desired tension level.
The recoiler is responsible for rewinding the slit strips into smaller coils. It must be able to handle the high speeds and tensions generated during the slitting process, and may be equipped with features such as automatic coil changing systems and tension control feedback loops for increased productivity.
In addition to these main components, a high speed slitting line may also include various auxiliary equipment such as conveyors, stackers, and inspection systems. Conveyors are used to transport the material between different stages of the slitting process, while stackers are used to stack the slit coils for easy storage and transportation. Inspection systems may be used to detect defects or irregularities in the material, ensuring that only high-quality strips are produced.
The construction of a high speed slitting line is typically made of high-quality materials such as steel and aluminum to ensure durability and stability. The machine is designed to withstand the rigors of continuous operation at high speeds, and may be equipped with safety features such as guards, emergency stop buttons, and interlocks to protect operators and prevent accidents.
Slitting Process:
The slitting process using a high speed slitting line typically involves several steps.
1. Coil Loading:
The large coil of material is loaded onto the decoiler. The decoiler unwinds the coil and feeds the material into the slitting line.
2. Tension Control:
The tension control system is activated to maintain consistent tension on the material. This helps to ensure accurate cuts and prevent wrinkling or stretching of the material.
3. Slitting:
The material passes through the slitting head, where the circular knives or blades cut it into narrower strips. The slitting head is adjusted to the desired strip width and spacing.
4. Inspection:
The slit strips may be inspected for defects or irregularities using inspection systems such as vision systems or ultrasonic detectors. Any defective strips can be removed or marked for further processing.
5. Recoiling:
The slit strips are rewound onto smaller coils by the recoiler. The recoiler is adjusted to the desired coil size and tension.
6. Packaging and Storage:
The slit coils are packaged and stored for transportation or further processing.
Advantages of High Speed Slitting Lines:
1. High Production Capacity:
High speed slitting lines are capable of processing large volumes of material at rapid speeds, significantly increasing production capacity. This is especially beneficial for businesses with high demand for slit materials.
2. Precision and Accuracy:
These machines are designed to provide accurate and clean cuts, ensuring consistent strip widths and quality. Advanced slitting heads and tension control systems help to achieve high levels of precision.
3. Versatility:
High speed slitting lines can handle a wide range of materials, including metals, plastics, paper, and textiles. They can also be adjusted to produce different strip widths and thicknesses, providing flexibility in production.
4. Cost-Effective:
By processing large coils into narrower strips, high speed slitting lines can reduce material waste and increase efficiency. This can lead to cost savings in material procurement and production.
5. Automation and Control:
Modern high speed slitting lines are equipped with advanced automation and control systems, allowing for easy operation and monitoring. This reduces the need for manual labor and increases productivity.
Applications:
High speed slitting lines are widely used in various industries for different applications. Some of the common applications include:
1. Packaging Industry:
In the packaging industry, high speed slitting lines are used to produce narrow strips of paper, plastic film, and aluminum foil for packaging materials such as bags, boxes, and labels.
2. Automotive Industry:
The automotive industry uses high speed slitting lines to process metal strips for body panels, chassis components, and other parts. The precision and high production capacity of these machines are essential for meeting the demands of the automotive industry.
3. Construction Industry:
In the construction industry, high speed slitting lines are used to produce metal strips for roofing, siding, and other building materials. The versatility and cost-effectiveness of these machines make them suitable for various construction applications.
4. Electronics Industry:
The electronics industry uses high speed slitting lines to process thin films and foils for printed circuit boards, capacitors, and other electronic components. The precision and cleanliness of the slitting process are crucial for ensuring the quality of electronic products.
Conclusion:
High speed slitting lines are essential tools for industrial manufacturing, providing precision, efficiency, and high production capacity. With their advanced technology and robust construction, these machines are capable of handling a wide range of materials and applications. As the demand for customized materials continues to grow, high speed slitting lines will play an increasingly important role in meeting the needs of different industries.