Hotline
+86-136 8495 9862
Email:cennia@szmizhi.com
Add::104,Building 27,Third Industrial Zone, Longxi Community,Longgang District,Shenzhen,China.
Coil Forming & Handling Equipment
Surface Treatment Equipment
Solutions
Application
About Us
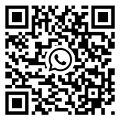
Welcome to MIZHI
For consultation/feedback, please call the service hotline: +86-136 8495 9862 Email:cennia@szmizhi.com
1. Introduction
In the complex world of industrial manufacturing and material processing, achieving the perfect surface finish is not only a matter of aesthetics but also crucial for the functionality and durability of products. The impact shot blaster has emerged as a vital piece of equipment in this pursuit. This powerful machine uses high velocity shots to bombard the surface of workpieces, effectively removing contaminants, improving surface properties, and enhancing the overall performance of materials. From the automotive industry, where components need to withstand extreme mechanical stress, to the aerospace sector, which demands the highest level of surface quality for safety critical parts, the impact shot blaster has found its niche in a wide range of applications.
2. Working Principle
2.1 Shot Propulsion Mechanism
At the heart of an impact shot blaster is the shot propulsion system. There are two primary methods for propelling the shots towards the workpiece: centrifugal wheels and compressed air. In centrifugal wheel based shot blasters, the shots are fed into the center of a high speed rotating wheel. As the wheel spins at speeds often reaching thousands of revolutions per minute, the shots are flung outwards along the vanes of the wheel. The centrifugal force generated by the spinning wheel accelerates the shots to high velocities, typically in the range of 50 150 meters per second. This high velocity stream of shots then impacts the surface of the workpiece, creating a powerful cleaning and surface modifying effect.
Compressed air driven shot blasters, on the other hand, use the force of compressed air to propel the shots. The shots are mixed with compressed air in a nozzle. The high pressure air, typically at pressures ranging from 2 10 bar, accelerates the shots through the nozzle and towards the workpiece. This method offers more precise control over the shot blasting process, as the operator can adjust the air pressure and the shot flow rate easily. It is often preferred for applications where a more delicate touch is required, such as when treating components with complex geometries or when the workpiece is made of a relatively soft material.
2.2 Impact and Surface Interaction
When the high velocity shots impact the surface of the workpiece, a series of physical processes occur. The kinetic energy of the shots is transferred to the surface, causing plastic deformation in the surface layer of the material. This plastic deformation leads to the generation of compressive stresses, which are highly beneficial for improving the fatigue resistance of the workpiece. For example, in a metal component that is subjected to cyclic loading, such as a crankshaft in an engine, the compressive stresses induced by shot blasting can prevent the initiation and propagation of fatigue cracks, significantly extending the component's lifespan.
The impact of the shots also serves to remove contaminants from the surface. Rust, scale, paint, and other coatings are effectively blasted away by the force of the shots. The continuous impact of multiple shots creates a micro roughened surface, which can improve the adhesion of subsequent coatings or finishes. In the case of preparing a surface for painting, the micro roughened texture provided by shot blasting ensures that the paint adheres firmly, resulting in a more durable and long lasting finish.
2.3 Shot Recycling and Dust Collection
Shot recycling is an essential aspect of the impact shot blasting process. After the shots have impacted the workpiece, they are collected and recycled for reuse. Most impact shot blasters are equipped with a shot recovery system, which typically includes a conveyor belt or a suction mechanism. The spent shots are separated from the debris and dust generated during the blasting process. A cyclone separator is often used to separate the larger debris from the shots, while finer dust particles are removed using filters. The recycled shots are then fed back into the shot propulsion system, reducing the cost of the shot blasting process and minimizing waste.
Dust collection is also crucial for maintaining a clean and safe working environment. The dust generated during shot blasting, which may contain metal particles, abrasive residues, and other contaminants, can be harmful to the health of the operators. High efficiency dust collection systems, such as bag filters or cartridge filters, are used to capture the dust particles. These filters can remove particles as small as a few microns, ensuring that the air in the working area is clean and free from harmful contaminants.
3. Types of Impact Shot Blasters
3.1 Cabinet Type Impact Shot Blasters
Cabinet type impact shot blasters are enclosed units that are suitable for small to medium sized workpieces. The workpiece is placed inside a cabinet, and the shot blasting process takes place within this enclosed space. This design offers several advantages, including better control over the shot blasting process and reduced environmental impact. The enclosed cabinet prevents the shots and dust from escaping into the surrounding area, making it a more environmentally friendly option. It also allows for better visibility of the blasting process, as the operator can observe the workpiece through a viewing window. Cabinet type shot blasters are often used in workshops and small scale manufacturing facilities for applications such as cleaning and surface treating small metal parts, automotive components, and jewelry.
3.2 Booth Type Impact Shot Blasters
Booth type impact shot blasters are larger in size and are designed to handle larger workpieces. They consist of a large, open fronted booth where the workpiece is positioned. The shot blasting equipment is mounted inside the booth, and the operator can access the workpiece from the front. Booth type shot blasters are suitable for applications such as treating large scale industrial components, construction machinery parts, and shipbuilding components. They offer more space for maneuvering large workpieces and can accommodate higher volume shot blasting operations. However, they may require more space in the facility and may have a higher initial cost compared to cabinet type shot blasters.
3.3 Automated Impact Shot Blasters
Automated impact shot blasters are equipped with advanced control systems and robotic arms to automate the shot blasting process. These machines are highly efficient and accurate, making them ideal for high volume production environments. The robotic arms can be programmed to move the workpiece in a specific pattern, ensuring that all areas of the surface are evenly blasted. Automated shot blasters can also be integrated into a production line, allowing for seamless integration with other manufacturing processes. For example, in an automotive manufacturing plant, automated impact shot blasters can be used to treat engine components continuously, reducing the need for manual labor and increasing productivity.
4. Applications across Industries
4.1 Automotive Industry
In the automotive industry, impact shot blasters are used extensively for various applications. Engine components, such as cylinder heads, engine blocks, and crankshafts, are often shot blasted to remove casting sand, rust, and scale. The high velocity shots not only clean the surface but also improve the fatigue resistance of these components. For example, a shot blasted crankshaft can withstand higher rotational speeds and mechanical stresses, reducing the risk of failure and improving the overall performance of the engine.
Automotive body parts, such as doors, hoods, and fenders, are also treated with impact shot blasters. The shot blasting process helps in removing any surface imperfections, such as scratches and dents, and prepares the surface for painting. A properly shot blasted surface provides better adhesion for the paint, resulting in a more durable and aesthetically pleasing finish. Additionally, shot blasting can be used to create a textured surface on certain automotive components, such as interior trim parts, to enhance their grip and appearance.
4.2 Aerospace Industry
The aerospace industry has extremely high quality standards, and impact shot blasters play a crucial role in meeting these requirements. Aerospace components, such as turbine blades, landing gear parts, and aircraft structural components, are subjected to shot blasting to improve their fatigue resistance and surface integrity. Turbine blades, which are exposed to high temperatures and mechanical stresses during flight, are shot blasted to induce compressive stresses that can prevent the formation of cracks. The high precision nature of impact shot blasters ensures that the surface of these components is treated uniformly, without causing any damage to the delicate geometries.
The surface finish of aerospace components is also critical for aerodynamic performance. Impact shot blasting can be used to create a smooth and uniform surface, reducing air resistance and improving the fuel efficiency of the aircraft. In addition, the process can be used to clean and prepare the surface of components for the application of protective coatings, which are essential for preventing corrosion in the harsh aerospace environment.
4.3 Metalworking and Manufacturing Industry
In the metalworking and manufacturing industry, impact shot blasters are used for a variety of applications. Metal forgings and castings often have surface imperfections and residual stresses. Impact shot blasting can remove these imperfections and relieve the residual stresses, improving the mechanical properties of the components. For example, in the production of metal gears, shot blasting can improve the tooth surface quality, reducing wear and improving the efficiency of power transmission.
Shot blasting can also be used to enhance the bonding strength of coatings and adhesives. By creating a rough and compressive stressed surface, impact shot blasting can improve the adhesion of paints, primers, and other coatings, ensuring a more durable and long lasting finish. This is particularly important in applications where the components are exposed to harsh environmental conditions, such as in the manufacturing of outdoor equipment and machinery.
5. Advantages of Impact Shot Blasters
5.1 Efficient Surface Cleaning
Impact shot blasters are highly efficient in removing contaminants from surfaces. The high velocity shots can quickly and effectively remove rust, scale, paint, and other coatings. Compared to manual cleaning methods, such as wire brushing or chemical cleaning, impact shot blasting can cover a larger surface area in a shorter time. For example, in a large scale metal processing plant, an impact shot blaster can clean hundreds of metal parts in a single batch, while manual cleaning would be extremely time consuming and labor intensive.
5.2 Surface Hardening and Fatigue Resistance Improvement
The impact of the shots on the surface of the workpiece causes work hardening, which increases the hardness of the surface layer. This surface hardening can improve the wear resistance and scratch resistance of the components. In addition, the generation of compressive stresses during shot blasting significantly improves the fatigue resistance of the components. This is particularly beneficial for components that are subjected to cyclic loading, such as mechanical parts in engines and machinery. The increased fatigue resistance can extend the lifespan of the components, reducing the need for frequent replacements and maintenance.
5.3 Cost Effectiveness in High Volume Production
For high volume production, impact shot blasters offer significant cost effectiveness. Once the initial investment in the equipment is made, the cost per unit of surface treatment is relatively low. The ability to recycle the shots and the high speed operation of the machines contribute to the overall cost efficiency. In addition, the improved quality of the components resulting from shot blasting can lead to cost savings in the long run, as it reduces the likelihood of component failure and the associated costs of repair or replacement.
5.4 Versatility
Impact shot blasters are highly versatile and can be used on a wide range of materials, including metals, plastics, and ceramics. They can also be adjusted to handle components of different sizes, shapes, and complexities. Whether it's a small, intricate metal part or a large, flat panel component, an impact shot blaster can be configured to achieve the desired surface treatment. This versatility makes it a valuable tool in many industries with diverse manufacturing needs.
6. Challenges and Solutions in Impact Shot Blaster Operation
6.1 Shot Wear and Contamination
Over time, the shots used in impact shot blasters can become worn or contaminated. Worn shots may have a reduced impact energy, leading to inconsistent surface treatment results. Contaminated shots, such as those that have picked up debris or oil from the workpiece, can also affect the quality of the shot blasting process. To address this challenge, regular inspection and maintenance of the shots are necessary. Shots should be periodically replaced when they show signs of excessive wear or contamination. In addition, shot cleaning systems can be used to remove debris and contaminants from the shots, ensuring their consistent performance.
6.2 Process Control and Quality Assurance
Maintaining consistent process control and quality assurance in impact shot blasting can be challenging. Factors such as shot velocity, shot flow rate, and the angle of impact can all affect the quality of the surface treatment. To ensure consistent results, it is important to use advanced control systems, such as programmable logic controllers (PLCs) and sensors. These systems can monitor and adjust the shot blasting parameters in real time, ensuring that the process is carried out within the specified tolerances. In addition, regular quality checks, such as hardness testing and surface roughness measurement, should be performed to verify the effectiveness of the shot blasting process.
6.3 Safety Concerns
Impact shot blasters involve high velocity shots and potentially harmful dust, posing safety risks to the operators. To address these safety concerns, proper safety measures must be implemented. The equipment should be equipped with safety guards and interlocks to prevent the operator from accidentally coming into contact with the moving parts or the high velocity shots. Respiratory protection, such as dust masks or respirators, should be provided to the operators to protect them from inhaling the dust generated during the shot blasting process. In addition, training programs should be conducted to educate the operators on the proper safety procedures and the potential hazards associated with impact shot blasting.
7. Future Trends in Impact Shot Blaster Technology
7.1 Advanced Process Monitoring and Control
The future of impact shot blasters lies in advanced process monitoring and control technologies. Sensors will be used to monitor the shot velocity, shot flow rate, and the surface condition of the workpiece in real time. This data will be used to adjust the shot blasting parameters automatically, ensuring consistent and optimal surface treatment results. In addition, artificial intelligence and machine learning algorithms may be applied to analyze the data and predict the performance of the shot blasting process, allowing for proactive maintenance and process optimization.
7.2 Development of New Shot Materials
New shot materials with improved properties are likely to be developed in the future. These materials may have higher hardness, better wear resistance, or unique chemical properties that can enhance the shot blasting process. For example, nanocomposite shot materials may be developed, which can combine the advantages of different materials at the nanoscale to achieve superior surface treatment performance. The development of new shot materials will open up new possibilities for impact shot blasting applications and improve the overall efficiency and effectiveness of the process.
7.3 Integration with Other Manufacturing Processes
Impact shot blasters are likely to be integrated more closely with other manufacturing processes in the future. For example, in a fully automated manufacturing line, the shot blasting process can be seamlessly integrated with the preceding and following processes, such as casting, machining, and coating. This integration will improve the overall efficiency of the manufacturing process, reduce the handling of components, and ensure a more consistent quality. In addition, the data from the shot blasting process can be shared with other processes, allowing for better overall process control and optimization.
In conclusion, the impact shot blaster is a powerful and versatile tool in the world of industrial manufacturing. Its ability to clean, harden, and improve the surface properties of components has made it an essential part of many industries. While there are challenges associated with its operation, ongoing technological advancements are addressing these issues and opening up new possibilities for the future. As industries continue to demand higher quality components, the impact shot blaster will undoubtedly play an even more significant role in driving innovation and improving product quality.