Hotline
+86-136 8495 9862
Email:cennia@szmizhi.com
Add::104,Building 27,Third Industrial Zone, Longxi Community,Longgang District,Shenzhen,China.
Coil Forming & Handling Equipment
Surface Treatment Equipment
Solutions
Application
About Us
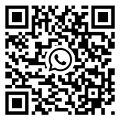
Welcome to MIZHI
For consultation/feedback, please call the service hotline: +86-136 8495 9862 Email:cennia@szmizhi.com
In the realm of industrial processes, surface preparation is a crucial step that can significantly impact the quality and durability of products. The industrial shot blaster has emerged as a powerful tool for achieving efficient and effective surface preparation, offering a wide range of benefits and applications across various industries. In this in-depth exploration, we will take a closer look at the industrial shot blaster, its features, working principles, advantages, applications, and future prospects.
I. Introduction
Surface preparation is essential for many industrial applications, including painting, coating, welding, and bonding. It involves removing contaminants, rust, scale, and old coatings from the surface to create a clean, smooth, and receptive substrate for further processing. The industrial shot blaster is designed to perform this task with precision and efficiency, using abrasive media such as steel shot, grit, or glass beads to impact the surface and achieve the desired results.
II. Features of Industrial Shot Blaster
1. High-Efficiency Blasting
The industrial shot blaster is capable of delivering a high volume of abrasive media at high velocities, resulting in rapid and thorough surface preparation. The powerful blasting action can remove even the toughest contaminants and coatings, leaving a clean and uniform surface.
2. Versatility
These shot blasters can be used on a wide variety of materials, including metal, concrete, wood, and composites. They can handle different surface profiles and sizes, making them suitable for a diverse range of industrial applications.
3. Adjustable Parameters
Industrial shot blasters often come with adjustable parameters such as blasting pressure, media flow rate, and nozzle distance. This allows operators to customize the blasting process according to the specific requirements of the surface being treated, ensuring optimal results.
4. Dust Collection System
To maintain a clean and safe working environment, industrial shot blasters are equipped with dust collection systems. These systems capture and filter the abrasive dust generated during the blasting process, reducing air pollution and protecting the health of operators.
5. Durable Construction
Built to withstand the rigors of industrial use, industrial shot blasters are constructed with high-quality materials and components. They are designed for long-term reliability and durability, minimizing downtime and maintenance costs.
III. Working Principles of Industrial Shot Blaster
The industrial shot blaster operates on the principle of propelling abrasive media onto the surface being treated. The abrasive media is typically fed into a blasting chamber, where it is accelerated by compressed air or a centrifugal force. The high-velocity abrasive particles then impact the surface, removing contaminants and creating a roughened texture.
The blasting process can be controlled by adjusting various parameters such as blasting pressure, media flow rate, and nozzle distance. These parameters determine the intensity and coverage of the blasting action, allowing operators to achieve the desired surface finish.
IV. Advantages of Industrial Shot Blaster
1. Enhanced Surface Quality
The industrial shot blaster provides a superior surface finish compared to traditional surface preparation methods. It removes contaminants and creates a clean, smooth, and uniform surface, enhancing the adhesion of coatings and improving the overall quality of the finished product.
2. Increased Productivity
With its high-efficiency blasting action, the industrial shot blaster can significantly increase productivity. It can quickly prepare large surfaces, reducing production time and costs. Additionally, the adjustable parameters allow for customization of the blasting process, optimizing it for different applications and materials.
3. Cost-Effective Solution
Investing in an industrial shot blaster can be a cost-effective solution in the long run. It reduces the need for manual labor and chemical cleaning methods, which can be expensive and time-consuming. Additionally, the durable construction and low maintenance requirements of these shot blasters minimize downtime and repair costs.
4. Environmental Friendliness
Industrial shot blasters are designed with environmental sustainability in mind. The dust collection systems reduce air pollution by capturing and filtering the abrasive dust generated during the blasting process. Additionally, some shot blasters use recycled abrasive media, reducing waste and conserving resources.
5. Versatility and Flexibility
These shot blasters can be used on a wide variety of materials and surfaces, offering versatility and flexibility in industrial applications. They can be easily adjusted to meet different surface preparation requirements, making them suitable for a diverse range of industries.
V. Applications of Industrial Shot Blaster
1. Automotive Industry
In the automotive industry, industrial shot blasters are used for surface preparation of vehicle bodies, chassis, and engine parts. They remove rust, scale, and old coatings, providing a clean surface for painting and coating. The shot blaster can also be used for deburring and surface profiling of metal parts, ensuring proper fit and function.
2. Aerospace Industry
The aerospace industry requires high-quality surface preparation for aircraft components. Industrial shot blasters are used to clean and condition turbine blades, landing gears, and fuselage parts. They remove contaminants and create a smooth surface for bonding and coating, ensuring the integrity and performance of aircraft components.
3. Construction Industry
In the construction industry, industrial shot blasters are used for surface preparation of concrete, steel, and wood structures. They remove dirt, grease, and old coatings, providing a clean surface for painting and coating. The shot blaster can also be used for surface profiling of concrete to improve adhesion of coatings and overlays.
4. Manufacturing Industry
The manufacturing industry uses industrial shot blasters for surface preparation of various metal parts, such as castings, forgings, and machined components. It removes scale, rust, and burrs, improving the surface finish and quality of the parts. The shot blaster can also be used for surface hardening and stress relief of metal parts.
5. Foundry Industry
In the foundry industry, industrial shot blasters are used for cleaning and conditioning of castings. They remove sand, scale, and other contaminants, leaving a clean surface for inspection and further processing. The shot blaster can also be used for fettling and deburring of castings, improving their quality and appearance.
VI. Choosing the Right Industrial Shot Blaster
1. Consider Your Application
Before choosing an industrial shot blaster, it is essential to consider your specific application requirements. Determine the type of material you will be treating, the surface profile and size, and the desired surface finish. This will help you select the appropriate shot blaster model and configuration.
2. Evaluate Your Production Volume
Consider your production volume and throughput requirements. If you have a high volume of work, you may need a larger and more powerful shot blaster with a high capacity. On the other hand, if you have smaller batches or occasional jobs, a smaller and more portable model may be sufficient.
3. Assess Your Budget
Set a budget for your shot blaster purchase and consider the total cost of ownership. This includes the initial purchase price, installation costs, operating costs, and maintenance expenses. While it is important to find a cost-effective solution, do not sacrifice quality and performance for a lower price.
4. Look for Quality and Reliability
Choose an industrial shot blaster from a reputable manufacturer known for quality and reliability. Look for models with a proven track record of performance and durability. Read reviews and testimonials from other users to get an idea of the equipment's reliability and customer satisfaction.
5. Consider Service and Support
Ensure that the manufacturer offers comprehensive service and support. This includes installation, training, maintenance, and repair services. A good manufacturer will also have a network of authorized dealers and service centers to provide prompt assistance when needed.
VII. Maintenance and Operation of Industrial Shot Blaster
1. Regular Maintenance
To ensure the optimal performance and longevity of your industrial shot blaster, it is important to perform regular maintenance. This includes cleaning the equipment, inspecting and replacing worn parts, and lubricating moving components. Follow the manufacturer's recommended maintenance schedule and procedures.
2. Safe Operation
Operate the shot blaster safely by following all safety guidelines and procedures. Wear appropriate personal protective equipment, such as safety glasses, gloves, and ear protection. Ensure that the equipment is properly grounded and that all safety features are functioning properly.
3. Training and Education
Provide proper training and education to operators on how to use and maintain the industrial shot blaster. This includes understanding the blasting process, adjusting parameters, and performing routine maintenance. Operators should also be trained on safety procedures and emergency response.
4. Storage and Protection
When not in use, store the shot blaster in a clean and dry location. Protect it from moisture, dust, and extreme temperatures. Cover the equipment with a protective cover or store it in a cabinet to prevent damage.
VIII. Future Prospects of Industrial Shot Blaster
1. Automation and Robotics
The future of industrial shot blasting is likely to involve increased automation and robotics. Automated shot blasters with robotic arms and advanced control systems will be able to perform precise and consistent blasting operations, reducing labor costs and increasing productivity.
2. Advanced Materials and Abrasives
The development of new materials and abrasives will continue to improve the performance of industrial shot blasters. For example, advanced ceramic abrasives may offer better durability and cutting power, while recycled materials may reduce environmental impact.
3. Digitalization and Connectivity
The integration of digital technology and connectivity will enable real-time monitoring and optimization of the shot blasting process. Sensors and data analytics will provide insights into equipment performance, process parameters, and surface quality, allowing for proactive maintenance and process improvement.
4. Environmental Sustainability
As environmental concerns continue to grow, industrial shot blasters will become more environmentally friendly. This may involve the use of energy-efficient equipment, the reduction of dust emissions, and the recycling of abrasive media. Additionally, the development of water-based blasting systems may gain popularity.
IX. Conclusion
The industrial shot blaster is a powerful and versatile tool for surface preparation in various industries. With its high-efficiency blasting action, adjustable parameters, dust collection systems, and durable construction, it offers numerous advantages over traditional surface preparation methods. By choosing the right industrial shot blaster for your application, performing regular maintenance, and operating it safely, you can ensure optimal results and long-term reliability. As technology continues to advance, we can expect to see even more innovative features and capabilities in industrial shot blasters, further enhancing their value and impact in the industrial world.