Hotline
+86-136 8495 9862
Email:cennia@szmizhi.com
Add::104,Building 27,Third Industrial Zone, Longxi Community,Longgang District,Shenzhen,China.
Coil Forming & Handling Equipment
Surface Treatment Equipment
Solutions
Application
About Us
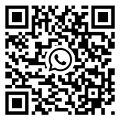
Welcome to MIZHI
For consultation/feedback, please call the service hotline: +86-136 8495 9862 Email:cennia@szmizhi.com
A shot blast kit is an essential toolset in the field of surface treatment and material preparation. It typically consists of various components that work together to achieve the efficient and effective removal of contaminants, rust, old coatings, and to create a desired surface profile on different materials. The kit is designed to be used with shot blasting equipment, which propels small abrasive particles, known as shot, at high velocities onto the surface of the workpiece.
Components of a Shot Blast Kit
Shot Blasting Machine: This is the core component of the kit. It comes in different types such as wheel blast machines and air blast machines. Wheel blast machines use a rotating wheel to accelerate the shot, while air blast machines use compressed air to propel the shot. The choice of machine depends on factors like the size and nature of the workpiece, the required cleaning or surface preparation intensity, and the production volume.
Abrasives: The abrasives used in a shot blast kit can vary widely. Common types include steel shot, steel grit, glass beads, and aluminum oxide. Steel shot is known for its durability and ability to provide a consistent finish. It is suitable for heavy-duty applications and can effectively remove thick layers of rust and coatings. Glass beads, on the other hand, are softer and are often used when a less aggressive finish is desired, such as for delicate or decorative surfaces. Aluminum oxide abrasives offer good cutting power and are commonly used for surface preparation before painting or coating.
Nozzles: Nozzles play a crucial role in directing the flow of shot onto the workpiece. They come in different shapes, sizes, and materials. Ceramic nozzles are popular due to their excellent wear resistance and ability to withstand the high-velocity impact of the shot. The size and shape of the nozzle can affect the coverage area and the intensity of the shot blasting process. A smaller nozzle may provide a more concentrated and intense blast, while a larger nozzle can cover a wider area with a less intense impact.
Hoses: High-quality hoses are required to transport the abrasives from the shot blasting machine to the nozzle. These hoses need to be durable, flexible, and able to withstand the abrasive nature of the shot and the pressure generated by the blasting process. They are usually made of reinforced rubber or other abrasion-resistant materials to ensure long-term use without leakage or rupture.
Filters and Separators: To maintain the efficiency of the shot blasting process and protect the equipment, filters and separators are often included in the kit. Filters help to remove dust and fine particles from the air, preventing them from contaminating the work environment and clogging the equipment. Separators are used to separate the used abrasives from the debris and contaminants, allowing the clean abrasives to be recycled and reused, which not only saves costs but also reduces waste.
Applications of Shot Blast Kit
Surface Preparation for Painting and Coating: One of the most common applications of a shot blast kit is to prepare surfaces for painting or coating. By removing rust, scale, and old paint, the shot blasting process creates a clean and rough surface that provides excellent adhesion for the new coating. This helps to ensure the longevity and durability of the painted or coated surface, preventing premature peeling or flaking.
Rust Removal: Shot blasting is highly effective in removing rust from metal surfaces. The high-velocity impact of the shot breaks down the rust layer and exposes the clean metal underneath. This is particularly useful for treating metal structures, machinery, and equipment that have been exposed to the elements and have developed significant rust buildup.
Deburring and Surface Smoothing: In manufacturing processes, shot blasting can be used to remove burrs and sharp edges from machined parts. It also helps to smooth the surface, improving the overall quality and appearance of the parts. This is beneficial for components that require precise fit and finish, such as automotive parts, aerospace components, and precision machinery.
Cleaning and Descaling: Shot blast kits are widely used for cleaning and descaling metal surfaces in industries such as steel, construction, and shipbuilding. They can quickly and efficiently remove dirt, grease, scale, and other contaminants, restoring the surface to its original condition or preparing it for further processing.
Surface Strengthening: In some cases, shot blasting can be used to strengthen the surface of materials. The impact of the shot causes plastic deformation of the surface layer, which induces compressive residual stresses. These residual stresses can improve the fatigue strength and wear resistance of the material, making it more suitable for applications where high mechanical strength is required.
Advantages of Using a Shot Blast Kit
Efficient and Time-Saving: Shot blasting is a rapid process compared to manual cleaning or other surface preparation methods. It can cover large surface areas in a relatively short time, increasing productivity and reducing labor costs, especially for large-scale projects or high-volume production runs.
High-Quality Finish: The shot blasting process provides a consistent and uniform surface finish, ensuring that the entire surface is properly cleaned or prepared. This results in better adhesion of coatings, improved paint durability, and a more aesthetically pleasing appearance.
Environmentally Friendly: When equipped with proper dust collection and filtration systems, shot blasting can be an environmentally friendly option. The filters capture the dust and debris generated during the process, preventing them from being released into the atmosphere and reducing environmental pollution. Additionally, the recycling of abrasives further minimizes waste generation.
Versatility: Shot blast kits can be used on a wide variety of materials, including steel, aluminum, concrete, wood, and plastic. This makes them suitable for different industries and applications, providing a flexible solution for surface treatment needs.
Cost-Effective: Although the initial investment in a shot blast kit may be significant, the long-term cost savings are considerable. The efficiency of the process reduces labor requirements, and the recyclability of abrasives cuts down on material costs. Moreover, the improved quality of the surface treatment can extend the lifespan of the workpiece or coating, reducing maintenance and replacement costs in the long run.
Safety Precautions
When using a shot blast kit, it is essential to follow strict safety precautions to prevent accidents and ensure the well-being of the operators. Operators should wear appropriate personal protective equipment, including safety glasses, ear protection, gloves, and protective clothing, to protect against flying debris and high noise levels. The shot blasting equipment should be regularly inspected and maintained to ensure its proper functioning and to prevent malfunctions that could lead to safety hazards. Additionally, the work area should be well-ventilated to remove dust and fumes generated during the process, and proper signage should be posted to indicate the presence of potential hazards.
Conclusion
In conclusion, a shot blast kit is a valuable asset in various industries for achieving efficient and high-quality surface treatment. Its components work synergistically to provide a powerful and versatile solution for rust removal, surface preparation, and cleaning. By understanding its applications, advantages, and safety considerations, operators can make the most of this toolset to enhance the quality and durability of their products and structures, while also ensuring a safe and environmentally friendly working environment. With continuous advancements in technology, shot blast kits are likely to become even more efficient, user-friendly, and adaptable to a wider range of applications in the future.