Hotline
+86-136 8495 9862
Email:cennia@szmizhi.com
Add::104,Building 27,Third Industrial Zone, Longxi Community,Longgang District,Shenzhen,China.
Coil Forming & Handling Equipment
Surface Treatment Equipment
Solutions
Application
About Us
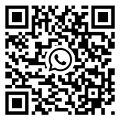
Welcome to MIZHI
For consultation/feedback, please call the service hotline: +86-136 8495 9862 Email:cennia@szmizhi.com
In the industrial sector, the processing of big - sized components presents unique challenges in surface treatment. Whether it is in heavy machinery manufacturing, shipbuilding, aerospace, or large - scale infrastructure construction, these oversized parts require a specialized approach to ensure thorough cleaning, descaling, and surface enhancement. The large - capacity rotary table shot blasting machine has emerged as a highly effective solution designed specifically to meet the demands of handling and treating big - sized components. This type of machine combines robust engineering, innovative design, and advanced technology to provide an efficient and reliable surface treatment process for components that are often too large or cumbersome for conventional shot blasting equipment.
Structural Design and Key Components
Rotary Table Assembly
The most distinctive feature of the large - capacity rotary table shot blasting machine is its rotary table assembly, which serves as the foundation for holding and rotating big - sized components during the blasting process. The rotary table is typically constructed from heavy - duty steel, engineered to withstand the significant weight and size of the components it supports. Its diameter can range from several meters to over ten meters, depending on the machine's capacity and the size requirements of the target components.
The table surface is often equipped with a series of mounting fixtures, such as adjustable clamps, brackets, and定位 pins. These fixtures are designed to securely hold the components in place, preventing any movement or shifting during rotation. For example, in the shipbuilding industry, when treating large hull sections, the mounting fixtures on the rotary table can be adjusted to accommodate the irregular shapes and sizes of the hull parts, ensuring they remain stable throughout the blasting operation. The rotary table is driven by a powerful motor - gearbox system, which allows for precise control of the rotation speed. This enables operators to optimize the blasting process by adjusting the rotation speed according to the specific surface treatment requirements of different components.
Blasting Chamber
The blasting chamber of a large - capacity rotary table shot blasting machine is a massive, enclosed structure designed to contain the shot media and protect the surrounding environment from the high - velocity impact of the shot. It is usually fabricated from thick, high - strength steel plates, with an interior lined with wear - resistant materials like manganese steel or special rubber liners. These liners not only protect the chamber walls from the erosive effects of the shot media but also help to reduce noise levels during operation.
Inside the blasting chamber, multiple high - performance blasting wheels are strategically positioned around the rotary table. The number of blasting wheels can vary from four to eight or more, depending on the size of the chamber and the complexity of the components being treated. These wheels are engineered to accelerate the shot media to extremely high speeds, ensuring that the big - sized components receive a powerful and uniform blast. The arrangement of the blasting wheels is carefully calculated to cover all surfaces of the rotating components, reaching even the most difficult - to - access areas. For instance, when treating large - scale wind turbine blades, the blasting wheels are positioned in a way that they can effectively blast the curved surfaces and the inner cavities of the blades, achieving comprehensive surface treatment.
Shot Recycling and Separation System
Similar to other shot blasting machines, a large - capacity rotary table shot blasting machine is equipped with an advanced shot recycling and separation system. Given the large volume of shot media used for treating big - sized components, an efficient recycling system is crucial for reducing operational costs and minimizing environmental impact.
After the shot media impacts the components and falls to the bottom of the blasting chamber, it is collected by a series of conveyors. These conveyors transport the used shot media to the separation unit, which typically consists of air washers, cyclones, and magnetic separators. The air washers remove the lighter contaminants, such as dust and small debris, by using a stream of air to carry them away. The cyclones then separate the shot media from any remaining fine particles through centrifugal force. Finally, the magnetic separators are used to extract ferrous contaminants from the shot, ensuring that only clean and reusable shot media is returned to the blasting process. This continuous recycling of shot media not only saves on the cost of purchasing new shot but also reduces the amount of waste generated, making the machine more environmentally friendly and cost - effective in the long run.
Operational Principles and Advantages for Big - Sized Components
Efficient Treatment of Oversized Parts
The large - capacity rotary table shot blasting machine offers unparalleled efficiency in treating big - sized components. Traditional shot blasting methods often struggle to handle components of large dimensions due to limitations in space and the inability to provide uniform treatment. In contrast, the rotary table design allows for the continuous rotation of these oversized parts, ensuring that all surfaces are exposed to the shot media.
For example, in the construction of large - scale industrial equipment, such as power plant turbines or large - diameter pipes, the components can be placed on the rotary table. As the table rotates, the blasting wheels can evenly blast the entire surface area of the component, removing rust, scale, and other contaminants. This eliminates the need for manual repositioning or multiple passes, significantly reducing the overall processing time and increasing productivity.
Uniform Surface Finish
One of the key advantages of using this type of machine for big - sized components is the ability to achieve a uniform surface finish. The precise control of the rotary table's rotation speed, combined with the strategic arrangement of the blasting wheels, ensures that each part of the component receives the same amount of blasting. This consistency is vital for components where surface quality directly affects their performance and lifespan.
In the aerospace industry, for instance, large - sized aircraft structural components require a flawless surface finish to meet strict safety and aerodynamic standards. The large - capacity rotary table shot blasting machine can guarantee that these components are treated uniformly, enhancing their strength, reducing the risk of fatigue failure, and improving their overall aerodynamic efficiency.
Cost - Effectiveness in Large - Scale Operations
Despite its large - scale design and advanced capabilities, the large - capacity rotary table shot blasting machine offers significant cost - effectiveness in large - scale operations. The high - capacity nature of the machine allows for the processing of multiple big - sized components in a single cycle, reducing the per - unit treatment cost. Additionally, the efficient shot recycling system minimizes the consumption of shot media, further lowering operational expenses.
Moreover, the machine's ability to complete the surface treatment process in a shorter time compared to traditional methods reduces labor costs associated with extended processing times. In industries where time is of the essence, such as shipbuilding and heavy equipment manufacturing, the cost savings achieved through increased productivity and reduced material consumption can have a substantial impact on the overall project budget.
Applications in Various Industries
Shipbuilding Industry
The shipbuilding industry is one of the major beneficiaries of the large - capacity rotary table shot blasting machine. Ship hulls, decks, and various large - scale ship components are constantly exposed to harsh marine environments, leading to the accumulation of rust, barnacles, and other contaminants. These machines are used to clean and prepare the surfaces of these components before painting and coating, ensuring a strong and durable bond between the surface and the protective layer.
For example, when constructing a new ship, the large - sized hull sections are placed on the rotary table for blasting. The machine can effectively remove all surface impurities, providing a clean and smooth surface that enhances the corrosion resistance of the ship. This not only extends the lifespan of the vessel but also reduces maintenance costs over its operational life.
Heavy Machinery Manufacturing
In the heavy machinery manufacturing sector, components such as large - scale excavator frames, crane booms, and bulldozer tracks are often of considerable size and weight. The large - capacity rotary table shot blasting machine is essential for preparing these components for further processing, such as welding, painting, and assembly.
By removing rust, scale, and other surface defects, the machine improves the quality of the components, ensuring better performance and reliability of the final machinery. For instance, the frame of a large - scale excavator needs to be strong and durable to withstand heavy loads. The surface treatment provided by the shot blasting machine enhances the frame's structural integrity, contributing to the overall efficiency and safety of the excavator.
Aerospace Industry
The aerospace industry demands the highest standards of quality and precision in component manufacturing. Large - sized components, such as aircraft fuselage sections, wing spars, and engine casings, require thorough surface treatment to meet stringent safety and performance requirements.
The large - capacity rotary table shot blasting machine can effectively clean and prepare these components, removing any contaminants that could potentially compromise their strength or aerodynamic properties. The uniform surface finish achieved by the machine also helps in the application of advanced coatings and composites, enhancing the overall performance and fuel efficiency of the aircraft.
Challenges and Future Developments
Challenges
While the large - capacity rotary table shot blasting machine offers numerous benefits, it also faces several challenges. One of the main challenges is the high initial investment required for purchasing and installing the machine. Due to its large size and complex design, the cost of acquiring and setting up this type of equipment can be substantial, which may pose a barrier for some small - and medium - sized enterprises.
Another challenge is the maintenance and operation of the machine. The large - scale components and the high - intensity operation of the machine mean that regular maintenance is crucial to ensure its optimal performance. Skilled technicians are required to perform maintenance tasks, such as replacing worn - out blasting wheels, checking the integrity of the rotary table, and maintaining the shot recycling system. This not only increases the labor cost but also requires a certain level of technical expertise that may not be readily available in all manufacturing facilities.
Future Developments
Looking towards the future, the large - capacity rotary table shot blasting machine is expected to witness significant technological advancements. One area of development is the integration of intelligent control systems. The use of sensors, artificial intelligence, and machine learning algorithms can enable the machine to monitor its own performance in real - time, adjust the blasting parameters automatically according to the characteristics of the components being treated, and predict maintenance needs. This will not only improve the efficiency and accuracy of the surface treatment process but also reduce downtime due to unexpected breakdowns.
Another potential development is the use of new materials and manufacturing techniques for the machine components. For example, the development of more advanced wear - resistant materials for the blasting wheels and the rotary table can extend their lifespan and reduce maintenance requirements. Additionally, 3D printing technology could be used to create custom - designed components, allowing for more efficient and cost - effective production and repair of the machine.
In conclusion, the large - capacity rotary table shot blasting machine is an indispensable tool for the surface treatment of big - sized components in various industries. Its unique design, efficient operational principles, and wide range of applications make it a key player in enhancing the quality and productivity of large - scale manufacturing. Although it faces challenges, ongoing technological developments are likely to further improve its performance, making it an even more valuable asset in the future of industrial surface treatment.