Hotline
+86-136 8495 9862
Email:cennia@szmizhi.com
Add::104,Building 27,Third Industrial Zone, Longxi Community,Longgang District,Shenzhen,China.
Coil Forming & Handling Equipment
Surface Treatment Equipment
Solutions
Application
About Us
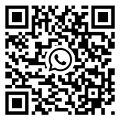
Welcome to MIZHI
For consultation/feedback, please call the service hotline: +86-136 8495 9862 Email:cennia@szmizhi.com
I. Introduction
The light gauge cut - to - length line is a crucial component in the manufacturing and processing of light - gauge materials. These materials, typically thin - walled metals such as steel or aluminum, are widely used in various industries, including construction, automotive, and appliance manufacturing. The cut - to - length line is designed to precisely cut these materials to the desired lengths, ensuring high - quality end products.
II. Components of a Light Gauge Cut - to - Length Line
A. Uncoiling System
The uncoiling system is the starting point of the cut - to - length line. It is responsible for unwinding the coiled light - gauge material. This system usually consists of a mandrel around which the coil is placed, and a motor - driven mechanism that rotates the mandrel to release the material. The uncoiling system must be able to handle different coil weights and diameters smoothly. It also often includes features to prevent the material from uncoiling too quickly or getting tangled, such as braking mechanisms and guide rollers.
B. Straightening Unit
Once the material is uncoiled, it may have some degree of curvature or deformation. The straightening unit is designed to correct this. It typically consists of a series of rollers arranged in a specific pattern. These rollers apply pressure to the material in different directions, gradually straightening it. The straightening process is crucial as it ensures that the material is in the proper shape for accurate cutting. Different types of light - gauge materials may require different levels of straightening force, so the straightening unit is often adjustable.
C. Measuring and Cutting Mechanism
1. Measuring
The measuring mechanism is responsible for determining the exact length of the material to be cut. There are various methods for measuring, such as using encoder wheels that rotate as the material passes through and calculate the length based on the number of rotations. Laser - based measurement systems are also becoming more common. These use lasers to detect the position of the material and calculate its length with high precision.
2. Cutting
The cutting mechanism can be of different types, depending on the nature of the material and the required cutting quality. Shear cutting is a common method for light - gauge materials. It involves a sharp blade that moves perpendicular to the direction of the material flow and cuts through it cleanly. Another option is laser cutting, which offers high precision and the ability to cut complex shapes. However, laser cutting is generally more expensive and may be slower for some applications. Plasma cutting can also be used for certain types of light - gauge metals, especially when dealing with thicker gauges within the light - gauge range.
D. Stacking and Bundling System
After the material is cut to length, it needs to be properly stacked or bundled for further processing or shipment. The stacking system can be automated, with robotic arms or conveyors that pick up the cut pieces and place them in an organized manner. Bundling systems are used to group multiple cut pieces together, often using straps or wire to hold them in place. This helps in easy handling and transportation of the cut materials.
III. Applications of Light Gauge Cut - to - Length Lines
A. Construction Industry
In the construction industry, light - gauge cut - to - length lines are used to produce components such as studs, joists, and roofing sheets. For example, steel studs of a specific length are cut using these lines and then used in the framing of buildings. The accurate cutting ensures that the building components fit together properly, which is essential for the structural integrity of the building. Additionally, aluminum roofing sheets cut to the right lengths can be easily installed on rooftops, reducing waste and installation time.
B. Automotive Sector
In the automotive industry, light - gauge metals are used for various parts, including body panels and interior components. The cut - to - length line is used to cut these materials to the precise dimensions required for manufacturing. For instance, thin - walled steel or aluminum sheets are cut to make car doors, fenders, or dashboard parts. This precision cutting helps in achieving the desired fit and finish of the automotive parts, as well as reducing material waste during the production process.
C. Appliance Manufacturing
Appliance manufacturers use light - gauge cut - to - length lines to produce parts for refrigerators, washing machines, and other household appliances. For example, the outer shells of refrigerators are often made from light - gauge steel sheets that are cut to the appropriate size. The accurate cutting of these materials ensures that the appliance parts are of the correct dimensions, which is crucial for proper assembly and functionality.
IV. Advantages of Using a Light Gauge Cut - to - Length Line
A. Precision
The ability to cut light - gauge materials to very precise lengths is one of the main advantages. This precision ensures that the end products fit together correctly, whether it is in construction, automotive, or appliance manufacturing. It also reduces the need for additional trimming or adjustment during the assembly process, saving time and labor costs.
B. Efficiency
These lines can operate at relatively high speeds, depending on the type of material and the complexity of the cutting operation. This high - speed operation, combined with the precision cutting, allows for efficient production of large quantities of cut - to - length materials. Additionally, the automated nature of many of the components, such as the stacking and bundling systems, further improves the overall efficiency of the production process.
C. Quality Control
The cut - to - length line often includes features for quality control. For example, the measuring mechanisms can be calibrated regularly to ensure accurate length measurements. The cutting mechanisms can also be adjusted to maintain a consistent cutting quality. This helps in producing high - quality end products that meet the required standards in different industries.
D. Material Savings
By accurately cutting the materials to the required lengths, there is less waste generated. This is especially important as light - gauge materials can be relatively expensive. Reducing waste not only saves costs but also has environmental benefits, as less material is being discarded.
V. Challenges and Future Developments
A. Challenges
1. Material Variability
Light - gauge materials can vary in terms of thickness, hardness, and surface quality. These variations can pose challenges for the cut - to - length line, as different materials may require different settings for optimal cutting. For example, a harder material may require more force during cutting, while a thinner material may be more prone to deformation during the straightening process.
2. Maintenance
The various components of the cut - to - length line, such as the rollers in the straightening unit and the cutting blades, require regular maintenance. Wear and tear can affect the performance of these components, leading to less accurate cutting or reduced efficiency. Finding the right balance between maintenance intervals and production requirements can be a challenge.
B. Future Developments
1. Integration with Industry 4.0
The future of light - gauge cut - to - length lines is likely to involve greater integration with Industry 4.0 concepts. This includes the use of sensors to monitor the performance of each component in real - time, allowing for predictive maintenance. Smart algorithms can be used to optimize the cutting process based on the characteristics of the material being processed and the production requirements.
2. Advanced Cutting Technologies
There is a continuous development in cutting technologies. For example, the improvement of laser - cutting techniques to make them more cost - effective and faster for light - gauge materials. Plasma cutting may also see advancements in terms of cut quality and energy efficiency. These developments will likely lead to more options for manufacturers when it comes to choosing the most suitable cutting method for their light - gauge materials.
In conclusion, the light gauge cut - to - length line is a vital part of the manufacturing process for light - gauge materials. It offers numerous advantages in terms of precision, efficiency, quality control, and material savings. However, it also faces challenges related to material variability and maintenance. With future developments in areas such as Industry 4.0 integration and advanced cutting technologies, the performance and capabilities of these lines are expected to improve further, meeting the evolving needs of different industries.