Hotline
+86-136 8495 9862
Email:cennia@szmizhi.com
Add::104,Building 27,Third Industrial Zone, Longxi Community,Longgang District,Shenzhen,China.
Coil Forming & Handling Equipment
Surface Treatment Equipment
Solutions
Application
About Us
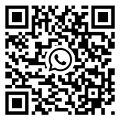
Welcome to MIZHI
For consultation/feedback, please call the service hotline: +86-136 8495 9862 Email:cennia@szmizhi.com
I. Introduction
A light gauge cut to length line is a specialized piece of equipment designed to process thin metal sheets with high precision and efficiency. In today's manufacturing landscape, where industries such as electronics, automotive interiors, and building components demand lightweight and accurately dimensioned metal parts, these lines have become indispensable. They are engineered to handle materials with a relatively small thickness, typically ranging from 0.2 mm to 3 mm, and convert metal coils into cut sheets of specific lengths, meeting the exact requirements of various end-products.
II. Key Components and Their Functions
1. Uncoiler
The uncoiler is the starting point of the light gauge cut to length line. It is responsible for holding the metal coil and unwinding it in a controlled manner. For light gauge materials, the uncoiler needs to have a gentle yet reliable mechanism to prevent any damage to the delicate sheets. It often features a mandrel that can be adjusted to fit different coil inner diameters precisely. The mandrel's surface is usually smooth to avoid scratching the metal. Additionally, a braking system is incorporated to regulate the unwinding speed, ensuring a steady feed of the material into the subsequent processing stages. For example, in the production of aluminum sheets for electronic enclosures, the uncoiler must unwind the coil at a speed that allows for smooth operation of the entire line while protecting the integrity of the thin metal.
2. Straightener
After uncoiling, the metal passes through a straightener. Given the propensity of light gauge sheets to have minor bends or curls, the straightener plays a crucial role in flattening them. It consists of multiple sets of rollers arranged in a specific pattern. These rollers apply pressure in different directions to eliminate any warping or distortion. The adjustment of the rollers is highly precise, as too much pressure can damage the thin metal, while too little won't achieve the desired straightening effect. In the manufacturing of stainless steel sheets for kitchen appliances, the straightener ensures that the metal is perfectly flat before further processing, which is essential for achieving a sleek and professional appearance.
3. Feeding Device
The feeding device is what drives the straightened metal forward at a consistent speed. It typically comprises a series of rollers that grip the metal firmly but gently. To prevent scratching or denting the light gauge material, the rollers are often made of a soft yet durable material or coated with a suitable substance. The speed control of the feeding device is of utmost importance, as it directly impacts the accuracy of the final cut lengths. Modern light gauge cut to length lines usually employ servo-motors and advanced control systems to achieve extremely precise speed regulation. This is vital in industries like automotive interiors, where the metal trim pieces need to be cut to exact dimensions for seamless assembly.
4. Cutting Unit
The cutting unit is the heart of the operation. For light gauge materials, several cutting methods can be employed.
Shearing: Shearing is a common method, where two blades move relative to each other to cut through the metal. However, for light gauge, the blades need to be extremely sharp and precisely aligned. The clearance between the blades is carefully adjusted to minimize burr formation. High-quality shearing blades are often made of hardened steel alloys and are regularly sharpened or replaced to maintain cutting performance.
Laser Cutting: Laser cutting has gained significant popularity for light gauge materials. It uses a high-energy laser beam to melt or vaporize the metal along the cutting line. This method offers unparalleled precision, allowing for the creation of complex shapes and intricate patterns. It is particularly useful in the production of decorative metal panels for architecture and signage, where fine details are required. Additionally, laser cutting produces a very smooth cut surface, reducing the need for further finishing operations.
5. Stacker or Conveyor
Once the metal is cut, it needs to be managed. A stacker is used to neatly pile up the cut sheets. It can be programmed to stack them in a particular order or pattern, which is beneficial for inventory management and subsequent handling. In some cases, a conveyor system is preferred. The conveyor can transport the cut pieces directly to the next stage of production, such as a welding station or a packaging area. For example, in a furniture manufacturing plant, the conveyor quickly moves the cut metal parts to the painting area, streamlining the production process.
III. Working Principle
The light gauge cut to length line operates in a sequential manner. First, the metal coil is loaded onto the uncoiler. As the uncoiler rotates, the metal is fed into the straightener. The straightened metal then moves through the feeding device, which propels it at a set speed. When it reaches the cutting unit, the cutting process is initiated based on the preset length parameters. These parameters are entered and controlled through a user-friendly interface. After cutting, the cut pieces are either stacked or conveyed as per the production requirements. The entire process is monitored and controlled by a central control system, which ensures the smooth running of the line and the accuracy of the output.
IV. Applications
1. Electronics Industry
In the electronics industry, light gauge cut to length lines are used to cut metal sheets for enclosures, heat sinks, and connectors. The precision cutting is essential to ensure a proper fit of components and to maintain the overall integrity of the electronic device. For example, the production of a smartphone casing requires the metal to be cut to exact dimensions to house all the internal components snugly.
2. Automotive Interiors
For automotive interiors, these lines are used to cut metal trim pieces, seat frames, and dashboard components. The ability to cut light gauge metals accurately allows for a seamless integration of these parts into the vehicle's interior design. The metal trim pieces, for instance, need to be cut precisely to match the curves and contours of the car's interior, enhancing the aesthetic appeal.
3. Building Components
In the construction sector, light gauge cut to length lines are employed to produce metal roofing sheets, siding panels, and ventilation ducts. The efficient cutting and stacking capabilities enable on-site installation to be carried out smoothly. Metal roofing sheets can be cut to the exact length required for a particular roof design, minimizing waste and installation effort.
4. Furniture Manufacturing
Furniture manufacturers use light gauge cut to length lines to cut metal parts for table legs, chair frames, and decorative accents. The precision cutting helps in achieving a professional and stylish look. For example, the legs of a modern coffee table need to be cut to the right length and angle to provide stability and visual harmony.
V. Advantages
1. High Precision
These lines are designed to offer extremely accurate cutting. The tolerances can be as low as a fraction of a millimeter, which is crucial for industries that demand exact dimensions. In the production of high-tech products like microelectronics, this precision ensures the proper functioning of the final product.
2. Efficiency
Light gauge cut to length lines can process metal coils at a relatively high speed. They reduce the time-consuming manual cutting and handling processes, increasing productivity. The automated operation also minimizes errors, leading to a more consistent output.
3. Versatility
They can handle a wide range of light gauge metal materials, including aluminum, steel, copper, and their alloys. Different cutting methods and adjustable components make them adaptable to various manufacturing requirements.
4. Quality of Cut Surface
Whether using shearing or laser cutting, the resulting cut surfaces are of high quality. Shearing can produce clean cuts with minimal burrs when properly maintained, and laser cutting offers a smooth, polished surface that often requires no further finishing in some applications.
VI. Maintenance and Safety Considerations
1. Maintenance
Regular maintenance is essential to keep the light gauge cut to length line in optimal condition. The blades of the cutting unit need to be sharpened or replaced frequently. The rollers of the straightener and feeding device should be checked for wear and tear and lubricated regularly. The control system and sensors also require periodic calibration to ensure accurate operation.
2. Safety
Safety is a paramount concern. The machine has moving parts such as the uncoiler, rollers, and cutting blades that can pose risks. Safety guards should be installed around the cutting area to prevent accidental contact. Operators should be trained to follow proper safety procedures, including wearing appropriate personal protective equipment and ensuring the machine is properly shut down and locked out during maintenance.
In conclusion, the light gauge cut to length line is a vital tool in modern manufacturing. Its ability to precisely and efficiently process light gauge metal materials makes it invaluable across multiple industries. With proper maintenance and safety measures, it can continue to deliver high-quality cut sheets and contribute to the success of various manufacturing processes.
Red Bud Cut to Length Line: An In-depth Overview
In the world of metal processing and fabrication, a cut to length line is an essential piece of equipment. The Red Bud cut to length line is known for its quality, precision, and efficiency. In this article, we will take an in-depth look at the Red Bud cut to length line, including its features, benefits, applications, and more.
I. Introduction
A cut to length line is a machine that is used to cut metal coils into flat sheets of specific lengths. These lines are commonly used in the steel, aluminum, and other metal industries. The Red Bud cut to length line is a high-quality option that offers a number of advantages over other cut to length lines on the market.
II. Features of the Red Bud Cut to Length Line
1. Precision Cutting
The Red Bud cut to length line is known for its precision cutting capabilities. It can cut metal coils with extreme accuracy, ensuring that each sheet is the exact length required.
This precision is achieved through the use of advanced cutting technology, such as high-speed shears and laser cutting systems.
2. High Production Capacity
Another feature of the Red Bud cut to length line is its high production capacity. It can process large volumes of metal coils quickly and efficiently, making it ideal for high-volume production environments.
The line is designed to run continuously, with minimal downtime for maintenance and setup.
3. Versatility
The Red Bud cut to length line is highly versatile, able to handle a wide range of metal coils and sheet thicknesses. It can cut coils of steel, aluminum, copper, and other metals, and can handle thicknesses ranging from thin gauge to heavy plate.
This versatility makes it a valuable asset for metal fabricators who work with a variety of materials and thicknesses.
4. Automation
Many Red Bud cut to length lines are fully automated, reducing the need for manual labor and increasing productivity. The lines can be programmed to cut specific lengths and widths, and can be integrated with other automated systems for seamless production.
Automation also improves safety by reducing the risk of operator error.
5. Quality Construction
Red Bud cut to length lines are built to last, with high-quality construction and durable components. The lines are designed to withstand the rigors of heavy-duty industrial use, and are backed by a reputation for reliability and performance.
III. Benefits of the Red Bud Cut to Length Line
1. Improved Efficiency
The precision cutting and high production capacity of the Red Bud cut to length line can lead to significant improvements in efficiency. By reducing waste and increasing productivity, metal fabricators can save time and money.
2. Consistent Quality
The consistent cutting accuracy of the Red Bud line ensures that each sheet is of uniform quality, reducing the risk of defects and rework. This can improve customer satisfaction and help build a reputation for quality.
3. Versatility and Flexibility
The ability to handle a wide range of materials and thicknesses gives metal fabricators the flexibility to take on a variety of projects. Whether working with thin gauge sheet metal or heavy plate, the Red Bud cut to length line can meet the needs of the job.
4. Automation and Safety
Automated cut to length lines can improve safety by reducing the risk of operator injury. They also free up operators to perform other tasks, increasing productivity and efficiency.
5. Cost Savings
By reducing waste and increasing productivity, the Red Bud cut to length line can lead to cost savings over time. Additionally, the quality construction and durability of the line can reduce maintenance and replacement costs.
IV. Applications of the Red Bud Cut to Length Line
1. Steel Fabrication
The Red Bud cut to length line is widely used in the steel fabrication industry. It can cut steel coils into sheets for use in construction, manufacturing, and other applications.
The line can handle a variety of steel grades and thicknesses, making it suitable for a wide range of projects.
2. Aluminum Fabrication
Aluminum is another common material processed on the Red Bud cut to length line. The line can cut aluminum coils into sheets for use in automotive, aerospace, and other industries.
The precision cutting and high production capacity of the line make it ideal for aluminum fabrication, where quality and efficiency are crucial.
3. Copper Fabrication
Copper is a valuable metal that is used in a variety of applications, including electrical wiring and plumbing. The Red Bud cut to length line can cut copper coils into sheets for use in these and other industries.
The line can handle different thicknesses of copper, ensuring that each sheet is cut to the correct specifications.
4. Other Metal Industries
The Red Bud cut to length line can also be used in the fabrication of other metals, such as brass, bronze, and stainless steel. The versatility of the line makes it suitable for a wide range of metal processing applications.
V. Choosing the Right Red Bud Cut to Length Line
1. Consider Your Needs
Before choosing a Red Bud cut to length line, it is important to consider your specific needs. Think about the types of materials you will be processing, the thicknesses you will be cutting, and the production volume you require.
This will help you determine which model of the line is best suited for your application.
2. Look for Quality and Reliability
Red Bud is known for its quality and reliability, but it is still important to do your research. Look for reviews and testimonials from other users, and consider the reputation of the manufacturer.
Choose a line that is built to last and backed by a strong warranty and support network.
3. Consider Automation Options
If you are looking to increase productivity and reduce labor costs, consider an automated Red Bud cut to length line. These lines can be programmed to cut specific lengths and widths, and can be integrated with other automated systems for seamless production.
4. Get a Demo
Before making a final decision, it is a good idea to get a demo of the Red Bud cut to length line you are considering. This will give you a chance to see the line in action and determine if it meets your needs.
Many manufacturers offer demos at their facilities or at trade shows.
VI. Maintenance and Operation of the Red Bud Cut to Length Line
1. Regular Maintenance
To ensure the longevity and performance of your Red Bud cut to length line, it is important to perform regular maintenance. This includes cleaning the line, lubricating moving parts, and checking for wear and tear.
Follow the manufacturer's recommended maintenance schedule and use only genuine replacement parts.
2. Operator Training
Proper operator training is essential for safe and efficient operation of the Red Bud cut to length line. Operators should be trained on all aspects of the line, including setup, operation, and maintenance.
Provide ongoing training and refresher courses to ensure that operators are up to date on the latest safety and operational procedures.
3. Safety Precautions
Cut to length lines can be dangerous if not operated properly. Always follow safety precautions, such as wearing appropriate personal protective equipment, keeping hands and feet away from moving parts, and following lockout/tagout procedures.
Make sure that all safety guards and devices are in place and functioning properly.
VII. Future Trends in Cut to Length Lines
1. Increased Automation
As technology continues to advance, we can expect to see increased automation in cut to length lines. This will include more advanced programming capabilities, integration with other automated systems, and the use of artificial intelligence and machine learning.
2. Improved Energy Efficiency
Energy efficiency is becoming an increasingly important consideration in the metal processing industry. Cut to length lines will likely become more energy-efficient, with features such as regenerative braking and energy-saving motors.
3. Enhanced Precision and Quality
With the demand for high-quality metal products continuing to grow, we can expect to see cut to length lines that offer even greater precision and quality. This may include the use of advanced cutting technologies and improved quality control systems.
4. Customization and Flexibility
Metal fabricators are increasingly looking for cut to length lines that can be customized to meet their specific needs. This may include options for different cutting lengths and widths, as well as the ability to handle a variety of materials and thicknesses.
VIII. Conclusion
The Red Bud cut to length line is a high-quality, precision-cutting machine that offers a number of benefits to metal fabricators. With its advanced features, high production capacity, and versatility, it is an ideal choice for a wide range of applications. When choosing a Red Bud cut to length line, consider your specific needs, look for quality and reliability, and consider automation options. With proper maintenance and operation, your Red Bud cut to length line can provide years of reliable service and help you improve your metal processing operations.