Hotline
+86-136 8495 9862
Email:cennia@szmizhi.com
Add::104,Building 27,Third Industrial Zone, Longxi Community,Longgang District,Shenzhen,China.
Coil Forming & Handling Equipment
Surface Treatment Equipment
Solutions
Application
About Us
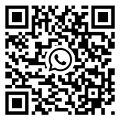
Welcome to MIZHI
For consultation/feedback, please call the service hotline: +86-136 8495 9862 Email:cennia@szmizhi.com
Introduction:
In the metalworking industry, the metal cut-to-length machine is an essential piece of equipment. This specialized machine is designed to accurately cut metal sheets or coils into specific lengths, providing a crucial step in the manufacturing process of various metal products. With its precision and efficiency, the metal cut-to-length machine plays a significant role in meeting the demands of different industries that rely on metal materials.
The metal cut-to-length machine combines advanced technology with robust construction to ensure accurate and reliable cutting. It is capable of handling a wide range of metal thicknesses and widths, making it a versatile tool for various applications. Whether it's for the automotive, aerospace, construction, or appliance industries, this machine offers a solution for cutting metal to the exact specifications required.
Design and Construction:
The design of a metal cut-to-length machine is a complex engineering feat. The machine typically consists of several key components, including a decoiler, a straightener, a shear, and a conveyor system.
The decoiler is used to unwind the metal coil and feed it into the machine. It is designed to handle different coil sizes and weights, ensuring a smooth and continuous supply of metal. The decoiler may be equipped with features such as automatic tension control and coil end detection to optimize the unwinding process.
The straightener is an important component that flattens the metal sheet to remove any curls or distortions. This is crucial for ensuring accurate cutting and a high-quality finished product. The straightener may consist of multiple rollers with adjustable pressure to achieve the desired degree of straightening.
The shear is the heart of the metal cut-to-length machine. It is responsible for cutting the metal sheet into the desired lengths. The shear can be of different types, such as a guillotine shear or a rotary shear. Guillotine shears offer high cutting force and accuracy, while rotary shears are known for their speed and continuous cutting capability.
The conveyor system is used to transport the metal sheet through the machine and deliver the cut pieces to the next stage of the production process. The conveyor may be equipped with features such as variable speed control and alignment guides to ensure smooth and accurate movement of the metal.
In addition to these main components, the metal cut-to-length machine may also include other features such as a control panel, safety guards, and dust collection systems. The control panel allows the operator to set and monitor various parameters such as cutting length, speed, and pressure. Safety guards are essential to protect the operator from potential hazards during the cutting process. Dust collection systems help to keep the work environment clean by removing metal chips and dust generated during cutting.
The construction of a metal cut-to-length machine is typically made of high-quality materials to ensure durability and stability. The frame is usually made of heavy-duty steel to withstand the forces generated during cutting. The components are carefully engineered and assembled to ensure smooth operation and accurate cutting.
Cutting Process:
The cutting process using a metal cut-to-length machine involves several steps.
1. Coil Loading:
The metal coil is loaded onto the decoiler. The operator ensures that the coil is properly positioned and secured to prevent any accidents during the unwinding process.
2. Unwinding:
The decoiler unwinds the metal coil and feeds it into the straightener. The automatic tension control system maintains a consistent tension on the metal to ensure smooth unwinding.
3. Straightening:
The metal sheet passes through the straightener, where the rollers flatten and straighten it. The operator may adjust the pressure and alignment of the rollers to achieve the desired degree of straightening.
4. Cutting:
Once the metal sheet is straightened, it enters the shear. The operator sets the cutting length on the control panel, and the shear cuts the metal sheet to the specified length. The cutting process can be either manual or automatic, depending on the machine's capabilities.
5. Conveying:
The cut pieces of metal are transported by the conveyor system to the next stage of the production process. The conveyor may be equipped with features such as sorting and stacking devices to facilitate the handling of the cut pieces.
6. Quality Control:
Throughout the cutting process, quality control measures are implemented to ensure that the cut pieces meet the required specifications. This may include inspections for dimensional accuracy, surface quality, and edge finish.
Advantages of Metal Cut-to-Length Machines:
1. Precision and Accuracy:
Metal cut-to-length machines are designed to provide highly accurate cuts, ensuring that the metal pieces are of the exact length and width required. This precision is crucial for applications where tight tolerances are necessary, such as in the automotive and aerospace industries.
2. Efficiency:
These machines are capable of cutting metal at high speeds, significantly increasing production efficiency. The automated nature of the cutting process reduces labor costs and minimizes the risk of human error.
3. Versatility:
Metal cut-to-length machines can handle a wide range of metal thicknesses and widths, making them suitable for various applications. They can also be adjusted to cut different lengths and shapes, providing flexibility in production.
4. Improved Quality:
The straightening and cutting processes of these machines result in clean and straight edges, improving the overall quality of the metal products. This is important for applications where appearance and functionality are critical.
5. Cost-Effective:
By reducing waste and improving production efficiency, metal cut-to-length machines can be a cost-effective solution for metalworking operations. The initial investment in a quality machine can be quickly recovered through savings in material costs and increased productivity.
Applications:
Metal cut-to-length machines are widely used in various industries for different applications. Some of the common applications include:
1. Automotive Industry:
In the automotive industry, metal cut-to-length machines are used to cut sheet metal for body panels, chassis components, and interior parts. The precision and efficiency of these machines are essential for meeting the strict quality standards of the automotive industry.
2. Aerospace Industry:
The aerospace industry requires high-precision cuts for aircraft components and structures. Metal cut-to-length machines play a crucial role in ensuring the accuracy and quality of these parts.
3. Construction Industry:
Sheet metal is used in the construction industry for roofing, siding, and ductwork. Metal cut-to-length machines are used to cut sheet metal to the appropriate lengths for these applications, saving time and labor.
4. Appliance Industry:
Sheet metal is used in the production of appliances such as refrigerators, washing machines, and ovens. Metal cut-to-length machines are used to cut sheet metal for the outer casings and internal components of these appliances.
5. Metal Fabrication:
In general metal fabrication, metal cut-to-length machines are used to cut sheet metal for a wide range of products, including furniture, cabinets, and machinery parts.
Conclusion:
The metal cut-to-length machine is an important tool in the metalworking industry. Its precision, efficiency, and versatility make it an essential piece of equipment for various applications. With continuous advancements in technology, these machines are becoming more advanced and capable of meeting the ever-increasing demands of different industries. Whether it's for large-scale production or custom fabrication, the metal cut-to-length machine offers a reliable and cost-effective solution for cutting metal to the exact specifications required.