Hotline
+86-136 8495 9862
Email:cennia@szmizhi.com
Add::104,Building 27,Third Industrial Zone, Longxi Community,Longgang District,Shenzhen,China.
Coil Forming & Handling Equipment
Surface Treatment Equipment
Solutions
Application
About Us
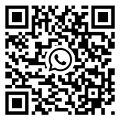
Welcome to MIZHI
For consultation/feedback, please call the service hotline: +86-136 8495 9862 Email:cennia@szmizhi.com
Metal roll forming equipment is a crucial part of the manufacturing process for a wide variety of metal products. This equipment is designed to transform flat metal sheets or strips into specific shapes by passing the material through a series of rollers.
The importance of metal roll forming equipment lies in its ability to produce high-quality, consistent products with precision and efficiency. It is widely used in industries such as construction, automotive, aerospace, and appliance manufacturing. In the construction industry, roll formed metal is used for roofing, siding, and structural components. In the automotive industry, it is used for body panels, frames, and exhaust systems. In the aerospace industry, roll formed parts are found in aircraft fuselages and wings. And in the appliance manufacturing industry, roll formed metal is used for cabinets, panels, and other components.
One of the key features of metal roll forming equipment is its versatility. It can be configured to produce a wide range of shapes and sizes, depending on the specific needs of the application. The equipment can be adjusted to handle different thicknesses and types of metal, as well as different production speeds and volumes. This makes it a flexible and cost-effective solution for manufacturers.
The components of metal roll forming equipment typically include decoilers, straighteners, feeders, roll formers, cut-off devices, and stackers. The decoiler is used to unwind the flat metal coil and feed it into the system. The straightener ensures that the metal is flat and free from wrinkles or distortions before entering the roll former. The feeder controls the speed and tension of the metal as it passes through the system. The roll former consists of a series of rollers that gradually shape the metal into the desired profile. The cut-off device cuts the formed metal to the required length, and the stacker organizes and stacks the finished products.
Roll forming equipment can be operated manually or automatically. Manual operation is suitable for small-scale production or when flexibility is required. Automatic operation, on the other hand, is ideal for high-volume production, as it offers greater speed and consistency. Automatic roll forming equipment is often equipped with advanced control systems that can monitor and adjust the production process in real time, ensuring optimal performance and quality.
In addition to the basic components, metal roll forming equipment may also include additional features such as lubrication systems, cooling systems, and quality control devices. Lubrication systems help to reduce friction between the rollers and the metal, prolonging the life of the equipment and improving the surface finish of the products. Cooling systems are used to prevent overheating of the rollers and the metal, ensuring stable production and high quality. Quality control devices such as sensors and cameras can be used to detect defects and ensure that only products that meet the required standards are produced.
The design and construction of metal roll forming equipment require a high level of engineering expertise. The rollers must be precisely machined and hardened to ensure accurate shaping of the metal. The frame and other structural components must be strong and rigid to withstand the forces generated during the roll forming process. Additionally, the equipment must be designed to be easy to operate, maintain, and repair.
In recent years, there have been significant advancements in metal roll forming technology. New materials and coatings are being developed to improve the performance and durability of roll formed products. Advanced control systems and automation technologies are being integrated into roll forming equipment to increase productivity and quality. And innovative designs are being introduced to meet the evolving needs of different industries.
In conclusion, metal roll forming equipment is an essential tool for manufacturers in a wide range of industries. It offers a reliable and efficient way to produce high-quality metal products with complex shapes and tight tolerances. With ongoing advancements in technology, this equipment is becoming more advanced, versatile, and automated, enabling manufacturers to stay competitive in the global marketplace.