Hotline
+86-136 8495 9862
Email:cennia@szmizhi.com
Add::104,Building 27,Third Industrial Zone, Longxi Community,Longgang District,Shenzhen,China.
Coil Forming & Handling Equipment
Surface Treatment Equipment
Solutions
Application
About Us
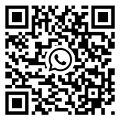
Welcome to MIZHI
For consultation/feedback, please call the service hotline: +86-136 8495 9862 Email:cennia@szmizhi.com
1. Introduction
Metal roll machines have emerged as indispensable tools in the modern manufacturing landscape. These machines are designed to transform flat metal sheets or coils into a wide variety of shaped products through a continuous and highly efficient rolling process. Their applications span across numerous industries, from construction and automotive to aerospace and packaging. The ability of metal roll machines to produce high - quality, consistent, and customized metal components has revolutionized the way products are manufactured, enabling greater precision, cost - effectiveness, and design flexibility. This article will comprehensively explore metal roll machines, covering their working principles, types, applications, advantages, and future trends.
2. Working Principle
2.1 Material Feeding
The operation of a metal roll machine commences with the feeding of raw material, typically in the form of metal coils or large sheets. For coil - fed machines, the metal coil is mounted on a decoiler. Advanced decoilers are equipped with tension control mechanisms to ensure a steady and uniform supply of the metal strip into the machine. This is crucial as any variation in the feed rate or tension can lead to defects in the final product. In the case of sheet - fed machines, large metal sheets are manually or mechanically loaded onto an input table. The sheets are then precisely positioned and fed into the initial stages of the rolling process.
2.2 The Rolling Process
Once the metal is fed into the machine, it enters the rolling section. This section consists of a series of rollers, which are the heart of the metal roll machine. The rollers are arranged in a specific configuration depending on the desired end - product shape. As the metal passes through these rollers, it is gradually bent, shaped, and formed into the required profile. The rollers are designed with precisely machined surfaces and specific geometries. For example, if the goal is to produce a circular tube, the rollers will be shaped to gradually curve the metal strip around a mandrel, ensuring a smooth and consistent circular cross - section. In the production of more complex shapes, such as those used in automotive body panels or architectural components, multiple sets of rollers with different profiles are used in a sequential manner. Each set of rollers contributes to a specific stage of the shaping process, gradually transforming the flat metal into the final, intricate shape.
2.3 Finishing Operations
After the main rolling process, the formed metal product may undergo several finishing operations. One common finishing operation is cutting. The metal roll machine is often equipped with a cutting mechanism, such as a shear or a saw, which cuts the continuously formed product into the desired lengths. In some cases, the machine may also be capable of performing additional operations like punching holes, notching, or adding flanges. These operations can be integrated into the machine's production line, allowing for a one - stop manufacturing process. For products that require a smooth surface finish or protection against corrosion, the machine may be linked to a finishing station where processes like polishing, painting, or galvanizing are carried out.
3. Types of Metal Roll Machines
3.1 Roll Bending Machines
Roll bending machines are designed primarily for bending metal sheets into curved shapes. They are relatively simple in design compared to some other types of metal roll machines. These machines typically have three or four rollers. In a three - roller machine, two of the rollers are parallel and serve as the driving rollers, while the third is adjustable. By changing the position of the adjustable roller, the operator can control the radius of the bend in the metal sheet. Four - roller machines offer more precise control over the bending process as they can better handle the metal's edges and reduce the likelihood of wrinkling. Roll bending machines are commonly used in applications where curved metal components are required, such as in the construction of pipes, arches, and circular tanks.
3.2 Roll Forming Machines
Roll forming machines are highly versatile and are used to produce a wide range of profile - shaped metal products. They consist of multiple sets of rollers, each set performing a specific stage of the shaping process. The metal strip is continuously fed through these roller sets, gradually taking on the desired shape. Roll forming machines can produce products with complex cross - sections, such as roofing panels, window frames, and automotive structural components. They are available in different sizes and configurations, with some being capable of handling large - scale industrial production, while others are more suitable for small - scale or custom manufacturing.
3.3 Tube and Pipe Roll Machines
Tube and pipe roll machines are specialized in manufacturing tubes and pipes from flat metal sheets or strips. These machines use a combination of rollers and a mandrel. The metal strip is first formed into a cylindrical shape around the mandrel by the rollers. Then, the edges of the strip are welded together (in the case of welded tubes) or joined using other methods such as crimping or seaming. Tube and pipe roll machines can produce tubes and pipes with different diameters, wall thicknesses, and materials. They are essential in industries such as oil and gas, plumbing, and automotive, where tubes and pipes are used for fluid transportation and structural applications.
3.4 Ring Roll Machines
Ring roll machines are designed to produce seamless rings from metal billets or pre - formed rings. The process involves placing the metal blank between two rollers, one of which is driven. As the driven roller rotates, it gradually expands the diameter of the ring while reducing its cross - sectional area. Ring roll machines can produce rings with a wide range of sizes and tolerances. These rings are used in various applications, including in the manufacturing of bearings, gears, and flanges, where high - strength and precise - fitting components are required.
4. Applications
4.1 Construction Industry
In the construction industry, metal roll machines play a crucial role. Roll forming machines are used to produce a variety of building materials. For example, roofing and siding panels are commonly manufactured using roll forming technology. These panels are available in different profiles, such as corrugated, trapezoidal, and standing seam, to meet the aesthetic and functional requirements of different buildings. Metal roll machines are also used to produce structural components like channels, angles, and I - beams. These components are essential for the framework of buildings, providing strength and stability. Additionally, in architectural applications, custom - shaped metal elements, such as decorative railings and ornamental grilles, are often created using metal roll machines, adding a touch of elegance and uniqueness to buildings.
4.2 Automotive Industry
The automotive industry heavily relies on metal roll machines for the production of numerous components. Roll - formed parts are used in vehicle bodies, such as door frames, roof rails, and bumper beams. These components need to be strong, lightweight, and precisely formed to meet the strict safety and performance standards of the automotive industry. Tube and pipe roll machines are used to produce exhaust systems, fuel lines, and hydraulic tubes. Ring roll machines may be used to manufacture components like bearing rings and gear blanks. The use of metal roll machines in the automotive industry allows for high - volume production of consistent and high - quality parts, which is essential for mass - produced vehicles.
4.3 Aerospace Industry
In the aerospace sector, where precision and reliability are of utmost importance, metal roll machines are used to produce critical components. Roll - formed parts are used in aircraft structures, such as fuselage frames, wing ribs, and landing gear components. These components must be made from high - strength, lightweight materials, such as aluminum alloys and titanium, and need to be formed with extremely tight tolerances. Metal roll machines are capable of meeting these stringent requirements, ensuring the safety and performance of aircraft. Tube and pipe roll machines are used to produce tubing for aircraft hydraulic systems, fuel lines, and pneumatic systems.
4.4 Packaging Industry
The packaging industry also benefits from metal roll machines. Metal roll machines are used to produce cans, drums, and other metal containers. Roll forming technology is used to create the bodies of these containers, while other operations, such as seaming and lid attachment, are often carried out in subsequent steps. The ability of metal roll machines to produce consistent and high - quality containers is crucial for ensuring the integrity of the packaged products, whether they are food, beverages, or industrial chemicals.
5. Advantages
5.1 High - Quality Output
One of the primary advantages of metal roll machines is the high - quality output they produce. The continuous and controlled rolling process ensures that each product has consistent dimensions and a uniform shape. The use of precision - machined rollers and advanced control systems minimizes the occurrence of defects such as wrinkles, cracks, and uneven bends. In contrast, manual or less - automated metal - shaping methods may result in more variability in product quality. The high - quality output of metal roll machines is essential for applications where precise fit and performance are critical, such as in the aerospace and automotive industries.
5.2 Cost - Efficiency
Metal roll machines offer significant cost - efficiency in the long run. Although the initial investment in purchasing a metal roll machine can be substantial, especially for large - scale or highly automated models, the high - speed and high - volume production capabilities of these machines lead to economies of scale. They can produce a large number of products in a relatively short time, reducing the cost per unit. Additionally, the automated nature of the process reduces the need for extensive manual labor, further cutting down on labor costs. Moreover, the ability to use raw materials more efficiently, minimizing waste, also contributes to overall cost savings.
5.3 Customization
Metal roll machines provide a high degree of customization. Different sets of rollers can be designed and installed to produce a wide variety of shapes and profiles. This allows manufacturers to meet the specific requirements of their customers, whether it's a unique architectural design in the construction industry or a specialized component for the aerospace industry. The customization options also extend to the choice of materials, as metal roll machines can work with different types of metals, including steel, aluminum, stainless steel, and copper, as well as alloys.
5.4 Productivity
The automation and continuous - production nature of metal roll machines significantly increase productivity. These machines can operate for long hours with minimal downtime, producing products at a much faster rate than traditional metal - working methods. For example, a roll forming machine can produce hundreds of feet of roofing panels in a single hour. The use of advanced control systems also allows for quick change - overs between different product runs, further enhancing productivity. This increased productivity is beneficial for manufacturers who need to meet high - volume orders and tight deadlines.
6. Future Trends
6.1 Technological Advancements
The future of metal roll machines will be characterized by continued technological advancements. Automation and robotics will be further integrated into these machines. For example, robotic arms may be used to load and unload raw materials, perform quality inspections, and even carry out some of the finishing operations. Artificial intelligence (AI) and machine learning (ML) will play an increasingly important role in optimizing the rolling process. AI - powered systems can analyze real - time production data, predict potential machine failures, and adjust the rolling parameters to ensure the highest quality output. New materials, such as advanced high - strength alloys and composite materials, will also drive the development of more specialized metal roll machines. These machines will need to be designed to handle the unique properties of these materials effectively.
6.2 Sustainability
Sustainability will be a key focus in the future of metal roll machines. Manufacturers will strive to develop machines that are more energy - efficient, reducing their environmental impact. This may involve the use of energy - recovery systems, more efficient motors, and better insulation of machine components. Additionally, there will be an increased emphasis on using recycled materials in the production process. Metal roll machines may be adapted to work with a higher percentage of recycled metals, helping to close the loop in the metal - manufacturing cycle.
6.3 Industry 4.0 Integration
Metal roll machines will become more closely integrated with the principles of Industry 4.0. This means they will be connected to the Internet of Things (IoT), allowing for remote monitoring and control. Operators will be able to access real - time data about the machine's performance, production output, and energy consumption from anywhere in the world. This connectivity will also enable predictive maintenance, where the machine can alert maintenance staff when a component is likely to fail, reducing unplanned downtime. Moreover, integration with other manufacturing systems, such as enterprise resource planning (ERP) and computer - aided design (CAD) software, will streamline the entire manufacturing process, from design to production.
In conclusion, metal roll machines are an integral part of modern manufacturing, enabling the production of a vast array of high - quality metal products. Their working principles, diverse types, wide - ranging applications, and numerous advantages make them essential tools across multiple industries. As technology continues to evolve, metal roll machines will adapt and innovate, further enhancing their performance, sustainability, and integration within the manufacturing ecosystem.