Hotline
+86-136 8495 9862
Email:cennia@szmizhi.com
Add::104,Building 27,Third Industrial Zone, Longxi Community,Longgang District,Shenzhen,China.
Coil Forming & Handling Equipment
Surface Treatment Equipment
Solutions
Application
About Us
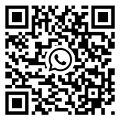
Welcome to MIZHI
For consultation/feedback, please call the service hotline: +86-136 8495 9862 Email:cennia@szmizhi.com
Metal roof forming machines have become an integral part of the roofing industry, offering a reliable and efficient way to manufacture metal roofing panels. These machines play a crucial role in producing high - quality roofing materials that are not only durable but also aesthetically pleasing.
The process of metal roof formation with these machines begins with the selection of the appropriate metal coil. Commonly used metals include steel, aluminum, and copper. Each metal has its own unique set of properties. Steel is known for its strength and is often the preferred choice for areas that experience heavy weather conditions or require a high level of structural integrity. Aluminum, on the other hand, is lightweight and highly resistant to corrosion, making it ideal for coastal regions or areas with high humidity. Copper offers a beautiful and distinctive appearance that can add a touch of elegance to a building.
The metal roof forming machine operates by feeding the metal coil through a series of rollers. These rollers are carefully designed and precisely machined to shape the metal into the desired roofing profile. The first set of rollers may start the initial bending process, gradually curving the flat metal sheet. As the metal passes through subsequent rollers, the profile becomes more defined. The number and configuration of the rollers can vary depending on the complexity of the roofing design.
One of the key advantages of metal roof forming machines is their ability to create custom roofing profiles. Whether it's a simple corrugated pattern or a more complex standing seam design, these machines can be adjusted to meet the specific requirements of a project. This flexibility allows for a wide range of architectural possibilities, enabling builders and designers to create unique and visually appealing roofs.
The control systems of modern metal roof forming machines are highly sophisticated. They are often computer - controlled, which provides precise control over the forming process. Operators can adjust parameters such as the speed at which the metal is fed through the rollers, the pressure applied by the rollers, and the overall dimensions of the roofing panel. This level of control ensures consistent quality and allows for quick and easy adjustments during production.
In addition to the standard roofing profiles, some metal roof forming machines are capable of incorporating additional features. For example, they can create perforations in the metal panels for ventilation purposes or add embossments for decorative effects. These added features can enhance the functionality and aesthetic appeal of the metal roof.
The production capacity of metal roof forming machines is another important aspect. Industrial - scale machines are designed to operate at high speeds and can produce a large number of roofing panels in a short period of time. This is essential for large - scale roofing projects where a significant amount of material is required. On the other hand, there are also smaller, portable metal roof forming machines available. These are ideal for on - site production, especially for smaller roofing jobs or in areas where access is limited.
During the manufacturing process, quality control is of utmost importance. This involves monitoring the thickness and quality of the metal coil, ensuring the proper alignment and functioning of the rollers, and verifying the accuracy of the formed roofing profile. Any defects or deviations from the specified standards can lead to problems such as leaks, poor fit, or reduced durability. Regular maintenance and inspection of the machine are necessary to ensure that it operates at its optimal level and produces high - quality roofing panels.
The installation of metal roofing panels produced by a forming machine is a relatively straightforward process. The panels are usually attached to the roof structure using screws, clips, or other fastening methods. The continuous nature of the panels produced by the machine allows for a smooth and seamless installation. This ensures a tight and weather - resistant seal, protecting the building from the elements.
In conclusion, metal roof forming machines are a vital component of the roofing industry. Their ability to produce custom - designed roofing panels with a high degree of precision and efficiency has made them an indispensable tool. The combination of advanced technology, flexible design options, and quality control offered by these machines ensures that they will continue to play a crucial role in the construction of metal roofs for years to come.