Hotline
+86-136 8495 9862
Email:cennia@szmizhi.com
Add::104,Building 27,Third Industrial Zone, Longxi Community,Longgang District,Shenzhen,China.
Coil Forming & Handling Equipment
Surface Treatment Equipment
Solutions
Application
About Us
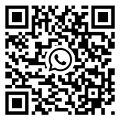
Welcome to MIZHI
For consultation/feedback, please call the service hotline: +86-136 8495 9862 Email:cennia@szmizhi.com
Metal roof panel machines play a crucial role in the construction industry, providing an efficient and cost-effective way to produce high-quality metal roofing panels. These machines are designed to transform flat metal sheets into various types of roof panels, offering durability, aesthetic appeal, and weather resistance. In this article, we will explore the different aspects of metal roof panel machines, including their types, features, working principles, applications, and benefits.
I. Introduction to Metal Roof Panel Machines
A metal roof panel machine is a specialized piece of equipment used in the manufacturing of metal roofing panels. These machines are capable of producing a wide range of panel profiles, including corrugated, trapezoidal, standing seam, and ribbed designs. The panels can be made from various metals such as steel, aluminum, and copper, depending on the specific requirements of the project.
Metal roof panel machines are typically used by roofing contractors, manufacturers, and builders who need to produce large quantities of panels for commercial, industrial, and residential buildings. These machines offer several advantages over traditional roofing methods, including faster installation times, lower labor costs, and enhanced durability.
II. Types of Metal Roof Panel Machines
There are several types of metal roof panel machines available in the market, each designed to produce specific panel profiles and sizes. Some of the common types include:
1. Corrugated Panel Machines
Corrugated panel machines are used to produce panels with a wavy or corrugated profile. These panels are widely used in industrial and agricultural buildings due to their strength and durability. Corrugated panels can be made from various materials, including steel, aluminum, and fiberglass.
2. Trapezoidal Panel Machines
Trapezoidal panel machines produce panels with a trapezoidal shape, which provides increased strength and stability. These panels are commonly used in commercial and industrial buildings, as well as in residential applications where a more modern look is desired. Trapezoidal panels can be made from steel, aluminum, or copper.
3. Standing Seam Panel Machines
Standing seam panel machines are designed to produce panels with a vertical seam that runs the length of the panel. These panels offer a sleek and modern look, as well as excellent weather resistance and durability. Standing seam panels are often used in high-end commercial and residential buildings.
4. Ribbed Panel Machines
Ribbed panel machines produce panels with a series of parallel ribs, which add strength and rigidity to the panel. Ribbed panels are commonly used in industrial and commercial buildings, as well as in agricultural applications.
III. Features of Metal Roof Panel Machines
Metal roof panel machines come with a variety of features that make them highly efficient and user-friendly. Some of the common features include:
1. Automated Operation
Most metal roof panel machines are fully automated, allowing for easy operation and high production rates. These machines can be programmed to produce specific panel profiles and sizes, reducing the need for manual labor and increasing productivity.
2. Adjustable Parameters
Metal roof panel machines often have adjustable parameters such as panel length, width, and height. This allows for customization of the panels to meet the specific requirements of different projects.
3. High-Quality Materials
The components of metal roof panel machines are typically made from high-quality materials such as steel and aluminum, ensuring durability and long service life. The machines are also designed to handle heavy loads and continuous operation.
4. Safety Features
Metal roof panel machines are equipped with safety features such as emergency stop buttons, safety guards, and interlocks to protect operators from accidents and injuries.
IV. Working Principle of Metal Roof Panel Machines
The working principle of a metal roof panel machine involves several steps. First, a flat metal sheet is fed into the machine through a series of rollers. The rollers then shape the metal sheet into the desired panel profile, using a combination of pressure and heat if necessary. Once the panel is formed, it is cut to the required length and ejected from the machine.
The specific working principle may vary depending on the type of metal roof panel machine. For example, corrugated panel machines use a series of rollers with different diameters to create the corrugated profile. Standing seam panel machines, on the other hand, use a combination of rollers and presses to form the vertical seam.
V. Applications of Metal Roof Panel Machines
Metal roof panel machines are used in a wide range of applications, including:
1. Commercial and Industrial Buildings
Metal roofing panels are commonly used in commercial and industrial buildings due to their durability, weather resistance, and low maintenance requirements. Metal roof panel machines can produce panels in large quantities, making them ideal for large-scale projects.
2. Residential Buildings
Metal roofing panels are also gaining popularity in residential applications due to their aesthetic appeal and long service life. Metal roof panel machines can produce panels in a variety of colors and styles, allowing homeowners to customize the look of their roofs.
3. Agricultural Buildings
Metal roofing panels are often used in agricultural buildings such as barns and sheds due to their strength and durability. Metal roof panel machines can produce panels that are resistant to harsh weather conditions and can withstand heavy loads.
4. Other Applications
Metal roof panel machines can also be used to produce panels for other applications such as carports, storage buildings, and outdoor shelters.
VI. Benefits of Metal Roof Panel Machines
Using metal roof panel machines offers several benefits, including:
1. Cost-Effective
Metal roof panel machines can produce panels at a lower cost than traditional roofing methods. The automated operation and high production rates of these machines reduce labor costs and increase efficiency.
2. Durable and Long-Lasting
Metal roofing panels produced by these machines are highly durable and can last for several decades. They are resistant to weathering, corrosion, and fire, making them a reliable choice for long-term use.
3. Energy-Efficient
Metal roofing panels can reflect sunlight and reduce heat absorption, making buildings more energy-efficient. This can lead to significant savings on cooling costs.
4. Environmentally Friendly
Metal roofing panels are recyclable, making them an environmentally friendly choice. Additionally, the long service life of metal roofing panels reduces the need for frequent replacements, reducing waste.
VII. Maintenance and Troubleshooting of Metal Roof Panel Machines
To ensure the smooth operation and long service life of metal roof panel machines, regular maintenance is essential. Some of the maintenance tasks include:
1. Cleaning
The machine should be cleaned regularly to remove dust, debris, and metal shavings. This can be done using compressed air or a vacuum cleaner.
2. Lubrication
The moving parts of the machine should be lubricated regularly to reduce friction and wear. This can be done using appropriate lubricants recommended by the manufacturer.
3. Inspection
The machine should be inspected regularly for signs of wear and damage. Any damaged or worn parts should be replaced immediately to prevent further damage.
4. Training
Operators should be trained on the proper use and maintenance of the machine to ensure safe and efficient operation.
In case of any problems or malfunctions, troubleshooting should be done immediately. Some common troubleshooting steps include:
1. Check for Power Supply
Make sure that the machine is properly connected to a power source and that there are no electrical issues.
2. Inspect the Rollers and Cutters
Check for any damage or misalignment of the rollers and cutters. Replace or adjust them if necessary.
3. Check the Control System
Inspect the control system for any errors or malfunctions. Reset or repair the control system if necessary.
4. Consult the Manual
If the problem persists, consult the manufacturer's manual for troubleshooting tips and solutions.
VIII. Future Trends in Metal Roof Panel Machines
The future of metal roof panel machines looks promising, with several trends emerging in the market. Some of these trends include:
1. Automation and Robotics
The use of automation and robotics in metal roof panel machines is expected to increase, leading to higher production rates and improved quality.
2. Digitalization
Digitalization of metal roof panel machines will enable real-time monitoring and control of the production process, improving efficiency and reducing waste.
3. Sustainability
There is a growing demand for sustainable building materials, and metal roof panel machines are likely to play a role in producing more environmentally friendly panels. This may include the use of recycled materials and energy-efficient production processes.
4. Customization
Customers are increasingly looking for customized roofing solutions, and metal roof panel machines will need to be able to produce panels in a variety of shapes, sizes, and colors to meet this demand.
metal roof panel machines are an essential tool in the construction industry, providing an efficient and cost-effective way to produce high-quality metal roofing panels. With their advanced features, wide range of applications, and numerous benefits, these machines are likely to continue to play a significant role in the future of roofing.