Hotline
+86-136 8495 9862
Email:cennia@szmizhi.com
Add::104,Building 27,Third Industrial Zone, Longxi Community,Longgang District,Shenzhen,China.
Coil Forming & Handling Equipment
Surface Treatment Equipment
Solutions
Application
About Us
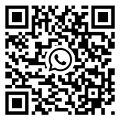
Welcome to MIZHI
For consultation/feedback, please call the service hotline: +86-136 8495 9862 Email:cennia@szmizhi.com
I. Introduction
Metal roofing has gained significant popularity in recent years due to its durability, aesthetic appeal, and energy efficiency. A metal roofing machine is an essential tool for manufacturers and contractors involved in the production and installation of metal roofs. In this article, we will explore the various aspects of metal roofing machines for sale, including their types, features, benefits, and considerations when purchasing one.
II. Types of Metal Roofing Machines
A. Roll Forming Machines
1. Description and Working Principle
Roll forming machines are the most common type of metal roofing machines. They work by gradually shaping a flat metal sheet into a specific profile through a series of rollers. The metal sheet is fed into the machine, and as it passes through the rollers, it is bent and formed into the desired shape.
2. Advantages
High production efficiency: Roll forming machines can produce large quantities of metal roofing panels in a short period.
Consistent quality: The automated process ensures uniform dimensions and quality of the panels.
Versatility: These machines can produce a wide range of metal roofing profiles, including corrugated, trapezoidal, and standing seam profiles.
3. Limitations
Initial investment: Roll forming machines can be relatively expensive, especially for high-capacity models.
Space requirements: They require a significant amount of floor space for installation and operation.
B. Standing Seam Machines
1. Description and Working Principle
Standing seam machines are designed specifically for the production of standing seam metal roofing panels. These panels have a concealed fastening system, which provides a sleek and seamless appearance. The machine forms the panels by folding and interlocking the edges of the metal sheet.
2. Advantages
Aesthetic appeal: Standing seam metal roofs offer a modern and elegant look.
Durability: The concealed fastening system provides enhanced resistance to wind uplift and water leakage.
Energy efficiency: The panels can be insulated, reducing heat transfer and energy consumption.
3. Limitations
Specialized application: Standing seam machines are only suitable for producing standing seam panels and cannot be used for other roofing profiles.
Higher cost: These machines are generally more expensive than roll forming machines.
C. Cut-to-Length Machines
1. Description and Working Principle
Cut-to-length machines are used to cut metal sheets into specific lengths for use in metal roofing applications. They typically consist of a feeding mechanism, a cutting device, and a stacking system. The metal sheet is fed into the machine, and the cutting device cuts it to the desired length.
2. Advantages
Flexibility: Cut-to-length machines can handle a variety of metal sheet thicknesses and widths.
Precise cutting: They provide accurate and consistent cuts, ensuring the quality of the roofing panels.
Cost-effective: These machines are relatively inexpensive compared to roll forming and standing seam machines.
3. Limitations
Limited functionality: Cut-to-length machines only perform the cutting function and cannot form the metal sheets into roofing profiles.
III. Features of Metal Roofing Machines
A. Automated Controls
1. Programmable Logic Controller (PLC)
Most modern metal roofing machines are equipped with a programmable logic controller (PLC). This allows for easy programming and adjustment of the machine's settings, ensuring consistent production and quality.
2. Touchscreen Interface
A touchscreen interface provides a user-friendly way to operate the machine. Operators can easily input parameters, monitor the production process, and diagnose any issues.
3. Automatic Feeding and Stacking
Some machines come with automatic feeding and stacking systems, which reduce labor requirements and improve production efficiency.
B. High-Quality Components
1. Durable Rollers
The rollers used in roll forming machines are made of high-quality steel or other durable materials to ensure long service life and consistent performance.
2. Precision Cutting Blades
Cut-to-length machines require precision cutting blades to ensure clean and accurate cuts. These blades are often made of hardened steel or carbide for durability.
3. Reliable Motors and Drives
Metal roofing machines are powered by reliable motors and drives to ensure smooth operation and high production speeds.
C. Safety Features
1. Emergency Stop Buttons
All metal roofing machines should be equipped with emergency stop buttons to quickly shut down the machine in case of an emergency.
2. Safety Guards
Safety guards are installed to protect operators from moving parts and potential hazards.
3. Warning Signals
Some machines may have warning signals, such as lights or buzzers, to alert operators to potential dangers.
IV. Benefits of Metal Roofing Machines
A. Increased Production Efficiency
1. Faster Production Speeds
Metal roofing machines can produce roofing panels at a much faster rate than manual methods. This allows manufacturers and contractors to complete projects more quickly and meet tight deadlines.
2. Reduced Labor Requirements
Automated machines reduce the need for manual labor, saving on labor costs and increasing productivity.
3. Consistent Quality
The automated process ensures that each panel is produced with consistent dimensions and quality, reducing waste and rework.
B. Cost Savings
1. Lower Material Waste
Precision cutting and forming processes reduce material waste, saving on material costs.
2. Reduced Installation Time
Metal roofing panels produced by machines are easier and faster to install, reducing labor costs and overall project costs.
3. Long-Term Durability
Metal roofs made with quality machines are more durable and require less maintenance over time, saving on repair and replacement costs.
C. Versatility and Customization
1. Production of Different Profiles
Metal roofing machines can produce a wide range of roofing profiles, allowing manufacturers and contractors to meet the diverse needs of their customers.
2. Customization Options
Some machines offer customization options, such as different colors, finishes, and insulation materials, to meet specific project requirements.
V. Considerations When Buying a Metal Roofing Machine
A. Production Requirements
1. Volume and Capacity
Consider the volume of metal roofing panels you need to produce and choose a machine with the appropriate capacity. Higher-capacity machines may be more expensive but can handle larger projects.
2. Profile Requirements
Determine the types of roofing profiles you will be producing and choose a machine that is capable of producing those profiles. Some machines are more versatile than others and can produce multiple profiles.
3. Material Compatibility
Ensure that the machine is compatible with the types of metal sheets you will be using, such as steel, aluminum, or copper.
B. Quality and Reliability
1. Brand Reputation
Research the reputation of different metal roofing machine manufacturers and choose a brand with a proven track record of quality and reliability.
2. Warranty and After-Sales Support
Look for machines that come with a warranty and good after-sales support. This will ensure that you can get assistance if any issues arise with the machine.
3. Testimonials and Reviews
Read testimonials and reviews from other customers to get an idea of the performance and reliability of the machine.
C. Cost and Budget
1. Initial Investment
Consider the initial cost of the machine, including any additional accessories or customization options. Make sure it fits within your budget.
2. Operating Costs
Take into account the operating costs of the machine, such as electricity consumption, maintenance, and replacement parts. These costs can add up over time and affect your overall profitability.
3. Return on Investment
Evaluate the potential return on investment of the machine by considering the increased production efficiency, cost savings, and other benefits it offers.
VI. Conclusion
A metal roofing machine can be a valuable investment for manufacturers and contractors involved in the metal roofing industry. By understanding the different types of machines, their features, benefits, and considerations when purchasing one, you can make an informed decision and choose the right machine for your specific needs. Whether you are looking for a roll forming machine, standing seam machine, or cut-to-length machine, there are many options available on the market. Consider your production requirements, quality and reliability needs, and budget to find the best metal roofing machine for your business.