Hotline
+86-136 8495 9862
Email:cennia@szmizhi.com
Add::104,Building 27,Third Industrial Zone, Longxi Community,Longgang District,Shenzhen,China.
Coil Forming & Handling Equipment
Surface Treatment Equipment
Solutions
Application
About Us
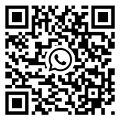
Welcome to MIZHI
For consultation/feedback, please call the service hotline: +86-136 8495 9862 Email:cennia@szmizhi.com
In modern manufacturing industries, the demand for high - efficiency and high - quality surface treatment processes is constantly increasing. Shot blasting is a widely used surface treatment method that can clean, strengthen, and finish the surfaces of various workpieces. A multi - station rotary table shot blasting machine is a remarkable innovation in this field, which enables simultaneous processing of multiple workpieces. This machine not only significantly improves production efficiency but also ensures consistent treatment quality across all workpieces.
Working Principle of the Multi - Station Rotary Table Shot Blasting Machine
Rotary Table Mechanism
The core of this machine is the rotary table. The table is designed to rotate continuously or intermittently, depending on the specific processing requirements. Multiple stations are evenly distributed around the circumference of the table. Each station is equipped with a fixture to hold the workpiece firmly in place during the shot - blasting process. As the table rotates, the workpieces move through different zones within the machine, including the loading zone, the shot - blasting zone, and the unloading zone.
Shot Blasting System
The shot - blasting system consists of shot blasting turbines or nozzles. These are strategically positioned around the shot - blasting zone to ensure comprehensive coverage of the workpieces. High - velocity shots are propelled from the turbines or nozzles onto the surfaces of the workpieces. The shots impact the workpieces, removing rust, scale, paint, and other contaminants. At the same time, they can also improve the surface roughness and fatigue resistance of the workpieces.
Shot Recovery and Recycling System
After the shots have hit the workpieces, they fall to the bottom of the machine. A shot recovery system is used to collect these used shots. This system typically includes a conveyor belt or a screw conveyor that transports the shots to a separator. The separator removes dust, debris, and broken shots from the collected shots. The clean and reusable shots are then sent back to the shot - blasting system for reuse, which reduces the cost of shot consumption and is environmentally friendly.
Advantages of Simultaneous Processing
Increased Production Efficiency
One of the most significant advantages of the multi - station rotary table shot - blasting machine is its ability to process multiple workpieces simultaneously. In a traditional single - station shot - blasting machine, only one workpiece can be processed at a time. In contrast, a multi - station machine can handle several workpieces concurrently. For example, a six - station rotary table machine can process six workpieces at the same time. This means that the production output per unit of time can be increased by a factor of six compared to a single - station machine. As a result, manufacturers can meet large - scale production demands more quickly and efficiently.
Consistent Treatment Quality
Since all workpieces on the rotary table are exposed to the same shot - blasting conditions, the treatment quality across all workpieces is highly consistent. The shot - blasting parameters, such as shot velocity, shot flow rate, and exposure time, are precisely controlled and applied uniformly to each workpiece. This ensures that every workpiece has the same level of surface cleanliness, roughness, and strength. In industries where product quality consistency is crucial, such as aerospace and automotive manufacturing, this feature is of great importance.
Reduced Labor Costs
With the ability to process multiple workpieces simultaneously, the need for manual labor is significantly reduced. Operators only need to load and unload the workpieces at the designated zones, rather than constantly monitoring and operating the machine for each individual workpiece. This not only saves labor but also reduces the potential for human errors. Additionally, the machine can operate continuously with minimal supervision, further optimizing labor utilization.
Applications in Different Industries
Automotive Industry
In the automotive industry, a large number of components need to be shot - blasted, including engine blocks, transmission parts, suspension components, and wheel hubs. The multi - station rotary table shot - blasting machine can handle these components efficiently. For engine blocks, the machine can remove the sand and scale left from the casting process, ensuring a clean surface for subsequent machining and assembly. The simultaneous processing capability allows automotive manufacturers to keep up with the high - volume production requirements of modern assembly lines.
Aerospace Industry
Aerospace components, such as turbine blades, landing gear parts, and structural frames, require high - precision surface treatment. The multi - station rotary table shot - blasting machine can provide the necessary surface quality and consistency. Turbine blades, for example, need to have a smooth and stress - relieved surface to ensure optimal performance and reliability. The machine can evenly blast the complex shapes of these blades, improving their fatigue life and aerodynamic properties.
General Manufacturing Industry
In general manufacturing, a wide variety of products, from small metal parts to large industrial equipment, can benefit from the multi - station rotary table shot - blasting machine. For small metal parts, such as bolts, nuts, and gears, the machine can quickly clean and strengthen their surfaces. For larger industrial equipment, such as machine tool frames and construction machinery components, the machine can remove rust and old paint, preparing them for painting or coating.
Design Considerations for Multi - Station Rotary Table Shot Blasting Machines
Number of Stations
The number of stations on the rotary table is an important design consideration. It depends on factors such as the size of the workpieces, the production volume requirements, and the available floor space. A larger number of stations can increase the production capacity, but it also requires a larger machine footprint and more complex control systems. For example, a small - scale manufacturer with limited space may choose a four - station machine, while a large - scale production facility may opt for an eight - or ten - station machine.
Workpiece Fixture Design
The design of the workpiece fixtures is crucial for ensuring the stability and proper positioning of the workpieces during the shot - blasting process. The fixtures need to be able to hold the workpieces firmly without interfering with the shot - blasting coverage. They should also be adjustable to accommodate different sizes and shapes of workpieces. For irregularly shaped workpieces, custom - designed fixtures may be required to ensure that all surfaces are exposed to the shots.
Shot Blasting Turbine or Nozzle Placement
The placement of the shot - blasting turbines or nozzles around the shot - blasting zone is carefully designed to achieve optimal shot - blasting coverage. The number, position, and angle of the turbines or nozzles are determined based on the shape and size of the workpieces. For example, for cylindrical workpieces, the turbines may be arranged in a circular pattern to ensure even blasting around the circumference. Computational fluid dynamics (CFD) simulations can be used to optimize the placement of the shot - blasting devices and improve the efficiency of the shot - blasting process.
Maintenance and Safety of Multi - Station Rotary Table Shot Blasting Machines
Maintenance Requirements
Regular maintenance is essential to ensure the reliable operation of the multi - station rotary table shot - blasting machine. This includes checking and lubricating the rotary table bearings, inspecting the shot - blasting turbines or nozzles for wear and damage, and cleaning the shot recovery and recycling system. The separator in the shot recovery system needs to be cleaned regularly to prevent clogging and ensure efficient separation of the shots. Additionally, the control system of the machine should be periodically calibrated to maintain accurate operation.
Safety Measures
Safety is of utmost importance when operating a multi - station rotary table shot - blasting machine. The machine should be equipped with safety guards around the rotary table and the shot - blasting zone to prevent operators from coming into contact with moving parts and flying shots. Emergency stop buttons should be easily accessible in case of any unexpected situations. Operators should also wear appropriate personal protective equipment (PPE), such as safety glasses, ear protection, and dust masks, to protect themselves from the noise, dust, and flying shots generated during the shot - blasting process.
Future Developments and Trends
Integration with Automation and Robotics
In the future, multi - station rotary table shot - blasting machines are likely to be integrated with automation and robotics systems. Automated loading and unloading systems can be used to further reduce labor costs and improve production efficiency. Robots can be used to handle the workpieces more precisely and place them in the correct positions on the rotary table. Additionally, robotic shot - blasting nozzles can be developed to adapt to different workpiece shapes and provide more targeted shot - blasting.
Advanced Control Systems
Advanced control systems will play an increasingly important role in the development of multi - station rotary table shot - blasting machines. These systems can use sensors to monitor the shot - blasting process in real - time, adjusting the shot - blasting parameters automatically based on the workpiece characteristics and the treatment requirements. For example, if the surface condition of a workpiece changes during the shot - blasting process, the control system can adjust the shot velocity or flow rate to ensure consistent treatment quality.
Environment - Friendly Shot Materials
There is a growing trend towards the use of environment - friendly shot materials in shot - blasting processes. In the future, multi - station rotary table shot - blasting machines may be designed to use more sustainable shot materials, such as recycled steel shots or biodegradable shots. These materials not only reduce the environmental impact but also may offer better performance in terms of shot - blasting efficiency and workpiece surface quality.
Conclusion
The multi - station rotary table shot - blasting machine for simultaneous processing is a revolutionary piece of equipment in the field of surface treatment. Its ability to process multiple workpieces at the same time, combined with its high - quality treatment results and efficiency, makes it an ideal choice for various industries. With continuous technological advancements in design, automation, and environmental friendliness, this machine is expected to play an even more important role in modern manufacturing in the future. Manufacturers who adopt this technology can gain a competitive edge in terms of production efficiency, product quality, and cost - effectiveness.