Hotline
+86-136 8495 9862
Email:cennia@szmizhi.com
Add::104,Building 27,Third Industrial Zone, Longxi Community,Longgang District,Shenzhen,China.
Coil Forming & Handling Equipment
Surface Treatment Equipment
Solutions
Application
About Us
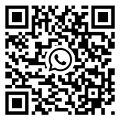
Welcome to MIZHI
For consultation/feedback, please call the service hotline: +86-136 8495 9862 Email:cennia@szmizhi.com
"New Horizons for Shot Blasting: Exploring the Potential of 3D Printing Integration"
"New Horizons for Shot Blasting: Exploring the Potential of 3D Printing Integration"
The integration of shot blasting with 3D printing is emerging as a transformative approach in modern manufacturing, offering significant benefits in surface quality, mechanical properties, and overall part performance. Here’s how this integration is opening new horizons for both industries:
1. Enhancing Surface Quality
3D-printed parts often exhibit rough surfaces and visible layer lines due to the additive manufacturing process. Shot blasting can effectively smooth these surfaces, removing imperfections and achieving a high-quality finish. This is particularly important for applications in industries like automotive and aerospace, where surface aesthetics and precision are critical.
2. Improving Mechanical Properties
Shot blasting, especially shot peening, has been shown to significantly enhance the mechanical properties of 3D-printed metal parts. Recent research indicates that shot peening can increase the fatigue strength of 3D-printed titanium alloy parts by up to 20 times, and maraging steel parts by up to 15 times. This improvement is attributed to the creation of a compressive residual stress layer on the surface, which enhances durability and resistance to wear and corrosion.
3. Post-Processing Efficiency
Integrating shot blasting into the 3D printing workflow streamlines post-processing. Traditional methods like manual grinding or chemical smoothing can be time-consuming and inconsistent. In contrast, shot blasting offers a more efficient and uniform approach, reducing the need for additional finishing steps.
4. Customization and Flexibility
3D printing allows for the production of highly customized and complex parts. Shot blasting can be tailored to match these unique geometries, ensuring consistent treatment across intricate designs. This flexibility is crucial for industries like medical device manufacturing, where personalized implants require both precision and durability.
5. Applications Across Industries
Automotive and Aerospace: Shot blasting enhances the surface finish and mechanical strength of 3D-printed components, making them more suitable for critical applications.
Medical: Improved surface quality and biocompatibility are essential for 3D-printed medical devices and implants.
Consumer Goods: Enhanced aesthetics and durability make shot blasting a valuable addition for 3D-printed products in the consumer market.
6. Future Trends and Innovations
As 3D printing continues to advance, the integration with shot blasting is expected to evolve further. For example, the development of specialized abrasives and more precise control systems will enable even better surface treatment. Additionally, the combination of AI-driven optimization and IoT integration can further enhance the efficiency and consistency of the process.
Conclusion
The integration of shot blasting with 3D printing is breaking new ground in manufacturing by combining the customization and complexity of additive manufacturing with the precision and efficiency of surface treatment. This synergy not only improves part quality and performance but also opens up new possibilities for industries seeking to leverage the benefits of both technologies. As innovations continue, the potential for this integration will only grow, driving further advancements in modern manufacturing.