Hotline
+86-136 8495 9862
Email:cennia@szmizhi.com
Add::104,Building 27,Third Industrial Zone, Longxi Community,Longgang District,Shenzhen,China.
Coil Forming & Handling Equipment
Surface Treatment Equipment
Solutions
Application
About Us
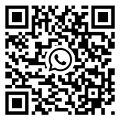
Welcome to MIZHI
For consultation/feedback, please call the service hotline: +86-136 8495 9862 Email:cennia@szmizhi.com
On - site roll forming represents a significant evolution in the metal fabrication and construction industries. This innovative approach involves the transformation of raw metal coils into finished, custom - profiled products directly at the project location, rather than in a remote manufacturing facility. By bringing the roll forming process to the site, on - site roll forming offers a plethora of advantages, ranging from enhanced flexibility and cost - effectiveness to improved quality control and reduced transportation complexities.
Working Mechanism of On - Site Roll Forming
1. Equipment Setup
The process commences with the transportation and setup of the roll forming equipment at the project site. The roll forming machine, which is typically a compact yet robust unit, is carefully positioned and leveled. It is accompanied by a coil reel for holding the metal coil, an uncoiler to feed the metal sheet smoothly, and often a power generator if the site lacks a stable electrical supply. For example, in a large - scale construction project in a remote area, a portable roll forming machine is brought in. The coil reel is loaded with a large - diameter steel coil, weighing several tons. The uncoiler is then adjusted to ensure a consistent and tension - controlled feed of the steel sheet into the roll forming machine.
2. Material Handling and Feeding
Once the equipment is set up, the metal coil is secured onto the coil reel. The uncoiler gradually unwinds the metal sheet, which is then fed into the roll forming machine. Advanced on - site roll forming systems often incorporate automated material - handling features. Sensors are used to monitor the tension of the metal sheet as it is fed, ensuring that it remains within the optimal range. This is crucial as improper tension can lead to wrinkling, buckling, or inaccurate profiling. For instance, in a roofing project, the steel sheet is fed into the roll forming machine at a precisely controlled speed. The sensors detect any fluctuations in tension and automatically adjust the uncoiler's speed to maintain a smooth and consistent feed.
3. Roll Forming Process Execution
The heart of on - site roll forming is the roll forming process itself. As the metal sheet enters the machine, it passes through a series of roll stations. Each roll station is designed to gradually shape the metal sheet into the desired profile. The rollers in these stations are custom - engineered based on the specific profile requirements. For a construction project that demands C - shaped purlins, the first few roll stations will initiate the gentle bending of the edges of the steel sheet. Subsequent roll stations will further increase the angle of the bend until the final C - shape is achieved. The number of roll stations can vary depending on the complexity of the profile, with more intricate profiles requiring a greater number of stations.
4. Cut - Off and Finishing Operations
After the metal sheet has been formed into the desired profile, it needs to be cut to the required length. On - site roll forming machines are equipped with cut - off mechanisms, which can be either mechanical shears or more advanced flying cut - off systems. A mechanical shear operates by using a blade to cut the profile at a fixed point when the desired length has been reached. In contrast, a flying cut - off system moves in synchronization with the moving profile, allowing for precise cutting while the machine is in continuous operation. This is particularly useful for high - speed production requirements. Once cut, the profiles may undergo basic finishing operations on - site, such as deburring to remove any sharp edges. However, more extensive finishing processes like painting or coating are often carried out later, depending on the project's requirements.
Advantages of On - Site Roll Forming
1. Cost - Efficiency
On - site roll forming offers substantial cost savings. Firstly, it eliminates the need for transporting pre - formed metal profiles from a manufacturing plant to the project site. The cost of shipping large, bulky metal products can be significant, especially for long - distance projects. By producing the profiles on - site, this transportation cost is completely eradicated. Additionally, on - site roll forming reduces inventory costs. Instead of storing a large stock of pre - formed profiles, which may not all be used and could potentially become obsolete, only the necessary metal coils are brought to the site. This just - in - time production approach minimizes the capital tied up in inventory. For a large - scale infrastructure project that requires a variety of custom - sized metal profiles, on - site roll forming can save thousands of dollars in transportation and inventory costs.
2. Flexibility and Customization
One of the most significant advantages of on - site roll forming is its unparalleled flexibility. The process allows for immediate adjustments to the profile design based on the project's changing needs. In a construction project, if there is a last - minute design modification that requires a slightly different shape or size of the metal profile, the on - site roll forming machine can be quickly reconfigured. The roll sets can be changed, and the machine's settings can be adjusted to produce the new profile. This level of customization is challenging to achieve with pre - fabricated profiles from a remote factory. For example, in a unique architectural project where the design calls for irregular - shaped metal roofing panels, on - site roll forming can easily accommodate these custom requirements, ensuring a perfect fit for the building's aesthetics.
3. Quality Control
On - site roll forming enables enhanced quality control. Since the production process is taking place at the project location, any issues or defects in the formed profiles can be immediately identified and rectified. The project team can closely monitor the roll forming process, ensuring that the profiles meet the exact specifications. In contrast, when profiles are produced in a factory far from the site, it can be difficult to detect and address quality issues until the products arrive at the project location, which may result in costly delays and rework. For a high - end commercial building project where the quality of the metal cladding is of utmost importance, on - site roll forming allows for real - time inspection and adjustment, guaranteeing that the final product meets the stringent quality standards.
4. Reduced Lead Times
By eliminating the need to order pre - formed profiles from a manufacturing facility and waiting for their delivery, on - site roll forming significantly reduces project lead times. In a time - sensitive construction project, every day of delay can incur substantial costs. With on - site roll forming, the production of metal profiles can start as soon as the materials and equipment are on - site. This quick - start capability means that the overall project timeline can be compressed, allowing for earlier completion. For example, in a disaster - relief housing project, where rapid construction is essential, on - site roll forming can ensure that the metal components for the shelters are produced and installed in a timely manner.
Applications of On - Site Roll Forming
1. Construction Industry
In the construction industry, on - site roll forming has a wide range of applications. It is extensively used in the production of roofing and siding materials. Roofing panels can be formed on - site to fit the exact dimensions of the building, eliminating the need for costly custom - made panels from a factory. Siding profiles can also be produced on - site, allowing for seamless integration with the building's design. Purlin and girt systems, which are crucial for providing structural support in buildings, are another area where on - site roll forming is highly beneficial. These components can be produced on - site in the required lengths and profiles, ensuring a perfect fit for the building's framework. In addition, on - site roll forming can be used to create metal decking for multi - story buildings, providing a cost - effective and efficient solution for flooring and formwork.
2. Infrastructure Projects
For infrastructure projects such as bridges, on - site roll forming can be used to produce components like bridge railings and structural supports. The ability to customize the profiles on - site ensures that they meet the specific requirements of the bridge design. In road construction, on - site roll forming can be applied to create guardrails and other safety components. The flexibility of on - site roll forming allows for quick adjustments to the design based on the terrain and traffic requirements. In large - scale industrial infrastructure projects, such as power plants and refineries, on - site roll forming can be used to produce various metal components, including ventilation ducts and structural frames, providing a more efficient and cost - effective production method.
3. Temporary Structures and Events
On - site roll forming is also well - suited for the creation of temporary structures and event - related infrastructure. In the event industry, for example, metal frames for exhibition booths, stages, and seating can be produced on - site. This offers the advantage of customization based on the layout and design of the event space. Temporary shelters for disaster - relief efforts can also be quickly constructed using on - site roll - formed components. The ability to produce the necessary metal parts on - site reduces the time required to set up these temporary structures, providing much - needed shelter and support in emergency situations.
Challenges and Solutions in On - Site Roll Forming
1. Equipment Mobility and Setup
One of the primary challenges in on - site roll forming is the mobility and setup of the equipment. The roll forming machines, along with the associated coil reels and power generators, can be large and heavy, making transportation and on - site setup a complex task. To address this, manufacturers are developing more compact and lightweight roll forming machines. These machines are designed to be easily transported in standard trucks and can be quickly assembled on - site. Additionally, advanced setup procedures and tools are being developed to simplify the installation process. For example, some roll forming machines now come with pre - assembled modules that can be quickly bolted together on - site, reducing the setup time significantly.
2. Power and Utility Requirements
On - site roll forming requires a reliable power source. In remote project locations, access to a stable electrical grid may be limited or non - existent. To overcome this challenge, many on - site roll forming setups are equipped with powerful diesel - powered generators. These generators can provide the necessary electrical power to run the roll forming machine, uncoiler, and other associated equipment. However, the use of generators also brings its own set of challenges, such as noise pollution and fuel consumption. To mitigate these issues, some projects are exploring the use of alternative power sources, such as solar - powered generators or hybrid power systems that combine solar and diesel power. These alternative power solutions can reduce the environmental impact and operating costs associated with on - site roll forming.
3. Skilled Labor Requirements
Operating an on - site roll forming machine requires skilled labor. The operators need to be proficient in setting up the machine, adjusting the roll sets, and monitoring the production process to ensure quality. Finding and training such skilled workers can be a challenge, especially in areas with a limited pool of experienced metal fabricators. To address this, manufacturers are providing comprehensive training programs for on - site roll forming operators. These programs cover everything from basic machine operation to advanced troubleshooting. In addition, some companies are using remote monitoring and support systems, where experienced technicians can provide real - time guidance to on - site operators via video conferencing and remote diagnostic tools.
Future Trends in On - Site Roll Forming
1. Automation and Smart Technology Integration
The future of on - site roll forming lies in increased automation and the integration of smart technologies. Automated material - handling systems will become more prevalent, with robots taking on tasks such as coil loading, sheet feeding, and finished product stacking. These automated systems will be equipped with advanced sensors and control algorithms to ensure precise and efficient operation. Smart technology integration will also enable real - time monitoring and adjustment of the roll forming process. For example, sensors can detect changes in the material properties, such as thickness or hardness, and automatically adjust the machine's settings to maintain consistent profile quality. Additionally, remote - controlled on - site roll forming machines may become a reality, allowing for operation and monitoring from a central control room, reducing the need for on - site personnel in some cases.
2. Sustainable and Green On - Site Roll Forming
Sustainability will be a key focus in the development of on - site roll forming. There will be an increased emphasis on using recycled metal materials in the roll forming process. By using recycled steel coils, on - site roll forming can contribute to reducing the environmental impact of metal fabrication. Additionally, efforts will be made to improve the energy efficiency of on - site roll forming equipment. This may involve the use of more energy - efficient motors, advanced drive systems, and optimized process parameters. The development of closed - loop production systems, where waste materials are recycled and reused within the on - site production process, will also be an area of growing interest.
3. Expansion of Application Areas
As on - site roll forming technology continues to advance, its application areas are likely to expand. In the aerospace industry, for example, on - site roll forming could potentially be used for the production of custom - sized and shaped metal components during aircraft maintenance and repair. In the marine industry, on - site roll forming could be applied to create components for ships and offshore structures. The ability to produce components on - site, close to where they are needed, can significantly reduce the time and cost associated with traditional manufacturing and transportation methods. This expansion of application areas will drive further innovation in on - site roll forming technology.
In conclusion, on - site roll forming has emerged as a game - changing technology in the metal fabrication and construction sectors. Its numerous advantages, including cost - efficiency, flexibility, quality control, and reduced lead times, make it an attractive option for a wide range of projects. While challenges exist, ongoing developments in equipment design, power solutions, and workforce training are addressing these issues. Looking to the future, on - site roll forming is set to become even more automated, sustainable, and versatile, opening up new possibilities across multiple industries.