Hotline
+86-136 8495 9862
Email:cennia@szmizhi.com
Add::104,Building 27,Third Industrial Zone, Longxi Community,Longgang District,Shenzhen,China.
Coil Forming & Handling Equipment
Surface Treatment Equipment
Solutions
Application
About Us
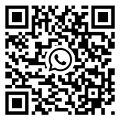
Welcome to MIZHI
For consultation/feedback, please call the service hotline: +86-136 8495 9862 Email:cennia@szmizhi.com
I. Introduction
In the world of surface preparation and finishing, Pangborn shot blasters have established themselves as a reliable and efficient solution. With a long history of innovation and quality, Pangborn has become a trusted name in the industry. In this in-depth exploration, we will take a closer look at Pangborn shot blasters, their features, benefits, applications, and the technology that sets them apart.
II. History and Evolution of Pangborn Shot Blasters
The Pangborn Corporation has a rich history dating back to the early 20th century. Founded by George Pangborn, the company initially focused on the development of sandblasting equipment for the foundry industry. Over the years, Pangborn has continuously evolved and expanded its product range to meet the changing needs of various industries.
Today, Pangborn shot blasters are known for their advanced technology, durability, and performance. The company's commitment to research and development has led to the introduction of innovative features and improvements, making Pangborn shot blasters a preferred choice for surface preparation tasks.
III. Features and Components of Pangborn Shot Blasters
1. Shot Blasting Technology: Pangborn shot blasters utilize a unique shot blasting process that combines high-velocity abrasive particles with controlled air flow. This process effectively removes contaminants, rust, and old coatings from surfaces, leaving them clean and ready for further processing.
2. Blast Wheels: The heart of a Pangborn shot blaster is its blast wheels. These wheels are designed to accelerate the abrasive particles to high speeds, ensuring efficient surface preparation. Pangborn's blast wheels are known for their durability and performance, and they can be customized to meet specific application requirements.
3. Abrasive Media: Pangborn shot blasters can use a variety of abrasive media, including steel shot, steel grit, and sand. The choice of abrasive media depends on the surface to be treated and the desired finish. Pangborn offers a wide range of abrasive media options to ensure optimal results.
4. Dust Collection System: To ensure a clean and safe working environment, Pangborn shot blasters are equipped with advanced dust collection systems. These systems capture and filter the dust generated during the shot blasting process, reducing air pollution and protecting the operator's health.
5. Control System: Pangborn shot blasters are equipped with a sophisticated control system that allows for easy operation and precise control of the blasting process. The control system can be customized to meet specific application requirements, and it provides real-time feedback on the machine's performance.
IV. Benefits of Using Pangborn Shot Blasters
1. Efficient Surface Preparation: Pangborn shot blasters are highly efficient in removing contaminants, rust, and old coatings from surfaces. This results in a clean and smooth surface that is ready for further processing, such as painting, coating, or welding.
2. Improved Surface Finish: The shot blasting process provided by Pangborn shot blasters creates a uniform and textured surface finish. This improves the adhesion of coatings and paints, resulting in a more durable and attractive finish.
3. Versatility: Pangborn shot blasters can be used on a wide range of materials, including metal, concrete, wood, and plastic. They are suitable for various applications, such as shipbuilding, automotive manufacturing, construction, and foundry work.
4. Cost-Effective: By efficiently removing contaminants and old coatings, Pangborn shot blasters can reduce the need for expensive chemical stripping or manual labor. This results in cost savings and increased productivity.
5. Environmental Friendliness: Pangborn's dust collection systems ensure that the shot blasting process is environmentally friendly by reducing air pollution. Additionally, the use of recyclable abrasive media can further reduce waste and environmental impact.
V. Applications of Pangborn Shot Blasters
1. Automotive Industry: Pangborn shot blasters are widely used in the automotive industry for surface preparation of car bodies, engine parts, and other components. The shot blasting process helps to remove rust, scale, and old paint, ensuring a clean and smooth surface for painting and coating.
2. Shipbuilding: In the shipbuilding industry, Pangborn shot blasters are used to prepare the hulls and decks of ships for painting and corrosion protection. The shot blasting process removes rust, marine growth, and old coatings, providing a durable and long-lasting finish.
3. Construction: Pangborn shot blasters are used in the construction industry for surface preparation of concrete floors, walls, and bridges. The shot blasting process creates a rough surface that improves the adhesion of coatings and overlays, resulting in a more durable and slip-resistant finish.
4. Foundry Work: In foundries, Pangborn shot blasters are used to clean and prepare castings for further processing. The shot blasting process removes sand, oxides, and other contaminants, leaving a clean and smooth surface for machining and finishing.
5. Aerospace Industry: Pangborn shot blasters are used in the aerospace industry for surface preparation of aircraft components, such as wings, fuselages, and engine parts. The shot blasting process helps to remove contaminants and create a uniform surface finish, ensuring the integrity and performance of the components.
VI. How to Choose the Right Pangborn Shot Blaster
When choosing a Pangborn shot blaster, several factors need to be considered to ensure that the machine meets your specific application requirements. Some of these factors include:
1. Surface Material: Consider the type of material you will be treating. Different materials require different abrasive media and shot blasting parameters.
2. Surface Size and Shape: Determine the size and shape of the surface to be treated. This will help you choose the appropriate size and configuration of the shot blaster.
3. Production Requirements: Consider your production volume and throughput requirements. Choose a shot blaster that can handle your production needs without sacrificing quality or efficiency.
4. Budget: Consider your budget constraints. Pangborn shot blasters come in a range of prices, so it's important to choose a machine that offers the best value for your money.
5. Service and Support: Consider the availability of service and support from the manufacturer. A reliable manufacturer will offer comprehensive after-sales service, including installation, training, and maintenance.
VII. Maintenance and Care of Pangborn Shot Blasters
Proper maintenance and care are essential to ensure the longevity and optimal performance of your Pangborn shot blaster. Here are some tips for maintaining your machine:
1. Regular Cleaning: Clean the shot blaster after each use to remove dust, debris, and abrasive media. Use a pressure washer or compressed air to clean the blast wheels, dust collection system, and other components.
2. Inspect Components: Regularly inspect the blast wheels, abrasive media, dust collection system, and other components for signs of wear and damage. Replace worn or damaged parts promptly to ensure optimal performance.
3. Lubrication: Lubricate the moving parts of the shot blaster regularly to reduce friction and wear. Follow the manufacturer's recommendations for lubrication intervals and types of lubricants.
4. Store Properly: When not in use, store the shot blaster in a dry, clean, and protected location. Cover the machine to prevent dust and moisture from entering.
5. Follow Manufacturer's Instructions: Always follow the manufacturer's instructions for operation, maintenance, and safety. This will help ensure that you are using the machine correctly and safely.
VIII. Safety Considerations When Using Pangborn Shot Blasters
Using a shot blaster can be a potentially hazardous activity if proper safety precautions are not taken. Here are some safety considerations to keep in mind when using a Pangborn shot blaster:
1. Personal Protective Equipment: Wear appropriate personal protective equipment, such as safety glasses, ear protection, a dust mask, and protective clothing. This will help protect you from flying debris, noise, and dust.
2. Training and Certification: Ensure that all operators are properly trained and certified to use the shot blaster. Follow all safety procedures and guidelines provided by the manufacturer.
3. Ventilation: Provide adequate ventilation in the work area to remove dust and fumes. Use exhaust fans or ventilation systems to ensure good air circulation.
4. Electrical Safety: Check the electrical connections and cords for damage before using the shot blaster. Use a ground fault circuit interrupter (GFCI) to protect against electrical shocks.
5. Lockout/Tagout: Follow proper lockout/tagout procedures when performing maintenance or repairs on the shot blaster. This will prevent accidental startup and ensure the safety of the operator.
IX. Future Trends in Pangborn Shot Blasting Technology
The field of shot blasting technology is constantly evolving, and Pangborn is at the forefront of innovation. Some of the future trends in Pangborn shot blasting technology include:
1. Automation and Robotics: As the demand for increased productivity and efficiency grows, we can expect to see more automated and robotic shot blasters. These machines will be able to perform complex tasks with precision and consistency, reducing the need for manual labor.
2. Environmental Sustainability: With growing concerns about environmental impact, Pangborn is likely to continue developing more environmentally friendly shot blasting solutions. This may include the use of recyclable abrasive media, energy-efficient motors, and improved dust collection systems.
3. Digitalization and Connectivity: The integration of digital technology and connectivity into shot blasters will allow for real-time monitoring, diagnostics, and optimization. This will improve productivity, reduce downtime, and enhance safety.
4. Customization and Specialization: As industries become more specialized, there will be a growing demand for customized shot blasting solutions. Pangborn is likely to continue developing machines that can be tailored to specific application requirements, offering unique features and capabilities.
Pangborn shot blasters are a reliable and efficient solution for surface preparation tasks. With their advanced technology, durability, and performance, they offer many benefits to various industries. By understanding the features, benefits, applications, and safety considerations of Pangborn shot blasters, you can make an informed decision when choosing a surface preparation solution. Additionally, by following proper maintenance and safety procedures, you can ensure the longevity and optimal performance of your Pangborn shot blaster. As the field of shot blasting technology continues to evolve, we can expect to see even more innovative solutions from Pangborn in the future.