Hotline
+86-136 8495 9862
Email:cennia@szmizhi.com
Add::104,Building 27,Third Industrial Zone, Longxi Community,Longgang District,Shenzhen,China.
Coil Forming & Handling Equipment
Surface Treatment Equipment
Solutions
Application
About Us
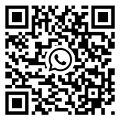
Welcome to MIZHI
For consultation/feedback, please call the service hotline: +86-136 8495 9862 Email:cennia@szmizhi.com
1. Introduction
In modern manufacturing, the production of small and delicate workpieces has become increasingly prevalent across various industries, including electronics, jewelry, and medical devices. These workpieces often require meticulous surface treatment to meet strict quality standards. The precision rotary table shot blasting machine has emerged as a highly specialized and effective solution for this purpose. This machine is designed to deliver a controlled and precise shot blasting process, ensuring that the delicate nature of these small components is preserved while achieving the desired surface modifications.
2. Working Principle
2.1 Rotary Table Mechanism
The core of the precision rotary table shot blasting machine is its rotary table. The table is engineered to rotate with high precision, typically controlled by an advanced servo - motor system. This allows for consistent and adjustable rotational speeds, ranging from very slow speeds suitable for extremely delicate workpieces to faster speeds for more robust treatments.
Small and delicate workpieces are securely mounted on fixtures placed on the rotary table. These fixtures are designed to hold the workpieces firmly in place during the blasting process, preventing any movement or displacement that could lead to uneven treatment or damage. The rotation of the table ensures that all surfaces of the workpiece are gradually and evenly exposed to the abrasive media, enabling a comprehensive and uniform surface treatment.
2.2 Shot Blasting System
Complementing the rotary table is the shot blasting system. This system consists of one or more high - pressure nozzles or centrifugal wheel - based shot - throwing units. In the case of nozzles, they are precisely calibrated to deliver a high - velocity stream of abrasive media, such as fine - grained metal or ceramic shots, onto the surface of the workpiece. The pressure and flow rate of the abrasive media can be finely tuned to match the specific requirements of the workpiece material and the desired surface finish.
For centrifugal wheel - based systems, the wheels accelerate the abrasive shots to high speeds and project them towards the workpiece. The orientation and position of these wheels are carefully arranged around the rotary table to ensure that the shot pattern covers all areas of the rotating workpiece. The speed of the centrifugal wheels can also be adjusted, allowing for precise control over the intensity of the shot blasting process.
2.3 Abrasive Media Recycling and Separation
Efficient use of abrasive media is crucial in any shot blasting operation, especially when dealing with small and delicate workpieces where the cost of media can be a significant factor. The precision rotary table shot blasting machine is equipped with an advanced abrasive media recycling and separation system.
After the abrasive media impacts the workpiece and falls to the bottom of the blasting chamber, it is collected through a series of chutes and conveyor belts. The used media is then passed through a separation process. This typically involves a combination of mechanical sieving to remove large debris and magnetic separation (if the abrasive media is ferromagnetic) to extract any metal particles that may have been worn off the workpieces or the machine components during the blasting process. The clean and reusable abrasive media is then recycled back into the shot blasting system, ready for the next cycle of treatment.
3. Advantages for Small and Delicate Workpieces
3.1 Gentle and Precise Treatment
1. Minimal Physical Damage: Small and delicate workpieces, such as micro - electronic components or intricate jewelry pieces, are highly susceptible to physical damage. The precision rotary table shot blasting machine's controlled rotation and adjustable shot blasting parameters ensure a gentle treatment. The slow and consistent rotation of the table allows for a gradual exposure of the workpiece to the abrasive media, minimizing the risk of sudden impacts that could cause scratches, dents, or fractures.
2. Precise Surface Modification: In many applications, such as the surface preparation of medical implants, a very precise surface finish is required. The machine enables operators to accurately control the intensity and duration of the shot blasting process. By adjusting parameters like the speed of the rotary table, the pressure of the abrasive media, and the type and size of the abrasive particles, manufacturers can achieve a highly precise surface roughness or texture, meeting the exacting standards of these industries.
3.2 Uniform Surface Finish
1. Comprehensive Coverage: The continuous rotation of the workpiece on the rotary table ensures that all surfaces, including complex geometries and hard - to - reach areas, are uniformly exposed to the abrasive media. This is particularly important for small and delicate workpieces with intricate designs, such as small gears or miniature sculptures. Unlike some other surface treatment methods that may miss certain areas, the precision rotary table shot blasting machine guarantees a consistent surface finish across the entire workpiece.
2. Consistent Results: The machine's ability to maintain precise control over the treatment process results in highly consistent surface finishes from one workpiece to the next. In mass production scenarios, where a large number of small and delicate components need to be treated, this consistency is invaluable. Whether it's a batch of 100 or 1000 small electronic connectors, each component will receive the same high - quality surface treatment, ensuring uniformity in performance and appearance.
3.3 High - Efficiency in Small - Scale Production
1. Time - Saving: Despite its precision - focused design, the precision rotary table shot blasting machine is also efficient in treating small workpieces. The continuous rotation of the table allows for a relatively fast treatment cycle. Compared to manual or semi - manual surface treatment methods, which may require individual handling and treatment of each workpiece, the machine can process multiple workpieces simultaneously (if the fixtures are designed accordingly), significantly reducing the overall processing time.
2. Flexible Batch Sizes: The machine is well - suited for both small - batch and large - scale production. For small - batch production, where the demand for a particular small and delicate workpiece may be limited, the machine can be quickly set up and adjusted to treat a few pieces at a time. In large - scale production, the consistent and efficient treatment process can be scaled up to meet high - volume requirements, making it a versatile solution for manufacturers with varying production needs.
3.4 Cost - Effectiveness
1. Reduced Labor Costs: The automated nature of the precision rotary table shot blasting machine reduces the need for extensive manual labor. In traditional surface treatment methods for small and delicate workpieces, workers may need to spend a significant amount of time carefully handling and treating each component. With this machine, the only human intervention required is loading and unloading the workpieces, as well as monitoring the machine's operation. This not only cuts down on labor costs but also reduces the variability in the quality of surface treatment that may be associated with manual work.
2. Efficient Abrasive Usage: As mentioned earlier, the abrasive media recycling and separation system in the machine ensures that the abrasive media is used efficiently. In the case of small and delicate workpieces, where the cost of high - quality abrasive media can be relatively high, this recycling feature can lead to substantial cost savings over time. By reusing the abrasive media, manufacturers can reduce their overall production costs without sacrificing the quality of the surface treatment.
4. Applications in Different Industries
4.1 Electronics Industry
1. Miniature Connectors and Components: In the electronics industry, small and delicate connectors, such as those used in smartphones, tablets, and wearables, require a clean and smooth surface for optimal electrical conductivity and soldering. The precision rotary table shot blasting machine can effectively remove any oxidation, impurities, or surface contaminants from these components. The gentle treatment ensures that the delicate metal surfaces are not damaged, while the uniform surface finish improves the reliability of electrical connections and the adhesion of solder during the assembly process.
2. Micro - electromechanical Systems (MEMS): MEMS devices, which combine mechanical and electrical components on a microscopic scale, demand extremely precise surface treatment. The machine can be used to etch or polish the surfaces of MEMS components, enhancing their performance and functionality. For example, in MEMS sensors, a well - treated surface can improve the sensitivity and accuracy of the device by reducing friction and ensuring proper movement of the mechanical parts.
4.2 Jewelry Industry
1. Fine Jewelry Pieces: The jewelry industry relies heavily on the creation of small and delicate pieces with intricate designs. The precision rotary table shot blasting machine can be used to enhance the surface finish of these jewelry items. Whether it's a small pendant, a delicate earring, or a detailed brooch, the machine can create a uniform satin - like or polished finish, enhancing the aesthetic appeal of the jewelry. The precise control over the shot blasting process allows jewelers to achieve the desired surface texture without damaging the delicate metal or gemstone settings.
2. Watch Components: Many watch components, such as small gears, watch cases, and bracelets, are small and require a high - quality surface treatment. The machine can be used to clean, strengthen, and polish these components. The shot - peening effect of the blasting process can improve the fatigue resistance of watch gears, ensuring smooth and accurate movement. For watch cases and bracelets, the uniform surface finish achieved by the machine adds to the overall luxury and durability of the timepiece.
4.3 Medical Device Industry
1. Surgical Implants and Instruments: Small and delicate surgical implants, such as screws, pins, and stents, need to have a biocompatible and smooth surface to minimize the risk of tissue rejection and ensure proper integration in the body. The precision rotary table shot blasting machine can be used to clean and polish the surfaces of these implants. The precise control over the surface roughness and texture is crucial for promoting cell adhesion and tissue growth around the implant. In the case of surgical instruments, the machine can improve the grip and durability of the instruments, enhancing the surgeon's control during procedures.
2. Diagnostic Equipment Components: Components used in diagnostic equipment, such as microfluidic chips for medical testing, often require a precise surface treatment. The machine can be used to clean and prepare the surfaces of these components for further processing, such as coating or bonding. The uniform surface finish achieved by the machine is essential for ensuring the proper flow of fluids and the accurate performance of diagnostic tests.
5. Operation and Maintenance
5.1 Operation
1. Initial Setup: Before starting the treatment of small and delicate workpieces, the machine needs to be carefully set up. This involves selecting the appropriate fixtures for the workpieces based on their size and shape. The speed of the rotary table, the pressure and flow rate of the abrasive media (if using nozzles), or the speed of the centrifugal wheels (if using a wheel - based system) need to be adjusted according to the specific requirements of the workpiece. Safety checks must also be carried out to ensure that all protective guards are in place and the machine is in proper working condition.
2. Loading and Unloading: Small and delicate workpieces are carefully loaded onto the fixtures on the rotary table. The operator needs to ensure that the workpieces are securely fastened to prevent any movement during the blasting process. At the end of the treatment cycle, the workpieces are unloaded and inspected for quality. If any workpieces show signs of improper treatment, such as uneven surface finish or damage, the machine settings may need to be adjusted for the next batch.
3. Monitoring: During the operation, the operator should continuously monitor the machine. This includes checking the performance of the shot blasting system, ensuring that the rotary table is rotating smoothly, and observing the quality of the treated workpieces. If any issues are detected, such as abnormal noise from the machine, inconsistent shot flow, or problems with the abrasive media recycling system, the machine should be stopped immediately for troubleshooting.
5.2 Maintenance
1. Regular Inspection: Regular inspection of the machine is essential to ensure its long - term reliable operation. Components such as the rotary table, nozzles (if applicable), centrifugal wheels, and abrasive media recycling system should be inspected for wear and tear. The rotary table bearings may need to be replaced periodically if they show signs of excessive wear. The nozzles or vanes on the centrifugal wheels, which are subject to high - velocity impacts from the abrasive media, should be checked for erosion and replaced when necessary. The abrasive media recycling system should be inspected to ensure that there are no blockages in the chutes or conveyors.
2. Lubrication: Proper lubrication of moving parts is crucial for the smooth operation of the machine. The bearings on the rotary table and the motors driving the shot - blasting units need to be lubricated regularly to reduce friction and prevent premature failure. This helps to maintain the accuracy and efficiency of the machine and reduces the risk of breakdowns during production.
3. Abrasive Media Management: The quality of the abrasive media also needs to be carefully managed. Over time, the abrasive particles may become worn or contaminated. The operator should periodically check the quality of the recycled abrasive and add new abrasive as needed to maintain the effectiveness of the shot blasting process. The type and size of the abrasive media may also need to be adjusted depending on the changing requirements of the workpiece production.
6. Conclusion
The precision rotary table shot blasting machine has proven to be an invaluable asset in the manufacturing of small and delicate workpieces across multiple industries. Its unique combination of gentle yet precise treatment, uniform surface finish, high - efficiency production, and cost - effectiveness makes it the preferred choice for surface treatment in these applications. By understanding its working principle, operation, and maintenance requirements, manufacturers can fully leverage the capabilities of this machine to enhance the quality and productivity of their small - workpiece production processes. As technology continues to advance, it is expected that further improvements will be made to the precision rotary table shot blasting machine, further expanding its applications and improving its performance in the treatment of small and delicate components.