Hotline
+86-136 8495 9862
Email:cennia@szmizhi.com
Add::104,Building 27,Third Industrial Zone, Longxi Community,Longgang District,Shenzhen,China.
Coil Forming & Handling Equipment
Surface Treatment Equipment
Solutions
Application
About Us
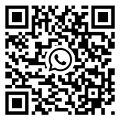
Welcome to MIZHI
For consultation/feedback, please call the service hotline: +86-136 8495 9862 Email:cennia@szmizhi.com
1. Introduction
In the world of modern manufacturing, the roll forming die stands as a cornerstone technology for producing a vast array of profile - shaped products. From the construction industry, where it is used to create structural components like steel studs and roofing sheets, to the automotive sector for manufacturing door frames and trim pieces, roll forming dies are integral to the production process. These dies enable the transformation of flat sheets of various materials, such as metals (steel, aluminum, copper), plastics, and even some composite materials, into precisely shaped, continuous profiles. The process is highly efficient, cost - effective for high - volume production, and offers a high degree of dimensional accuracy. Understanding the roll forming die, its design, manufacturing, and applications, is crucial for industries aiming to produce high - quality, consistent products at scale.
2. Working Principle of Roll Forming Dies
2.1 The Roll Forming Process
The roll forming process begins with a flat sheet of the raw material, which is fed into a series of rolls. These rolls are mounted on shafts and are arranged in multiple stations. Each station has a pair of rolls, with the upper and lower rolls working in tandem. As the sheet moves through the roll forming machine, the rolls gradually shape the sheet into the desired profile.
The first few stations are typically dedicated to initial bending and shaping operations. For example, in the production of a simple C - shaped steel profile for construction, the first station may slightly bend the edges of the flat sheet upwards. As the sheet progresses through subsequent stations, the degree of bending increases, and the shape becomes more defined. The final stations are designed to fine - tune the shape, ensuring that the profile meets the exact dimensional specifications.
2.2 Role of the Roll Forming Die
The roll forming die is essentially the set of rolls and associated components that perform the shaping operation. The design of the die is tailored to the specific profile being produced. The shape of the rolls in each station is carefully engineered to achieve the incremental shaping required. For instance, if the final product is a complex, multi - angled aluminum window frame profile, the rolls in different stations will have precisely calculated curvatures and angles. The die must also ensure that the material is evenly distributed during the forming process to prevent any thinning or thickening of the sheet in unwanted areas.
The rolls are made from high - strength materials, often hardened steel alloys, to withstand the significant forces exerted during the roll forming process. They are precisely machined to tight tolerances to ensure consistent shaping. In addition to the rolls, the die may also include guide elements, such as side guides and hold - down devices. Side guides keep the sheet centered as it moves through the rolls, while hold - down devices prevent the sheet from lifting or buckling during the shaping process.
3. Design Considerations for Roll Forming Dies
3.1 Material - Specific Design
The design of the roll forming die is highly influenced by the material being processed. Different materials have varying mechanical properties, such as hardness, ductility, and yield strength. For example, when working with stainless steel, which is relatively hard and has a high yield strength, the rolls need to be more robust and the die design may require higher forming forces. On the other hand, when forming soft materials like some plastics, the die design can be more delicate, and the forming forces need to be carefully controlled to prevent over - deformation or damage to the material.
The surface finish of the rolls also matters depending on the material. For materials that are sensitive to scratches or surface defects, such as aluminum sheets used for decorative applications, the rolls need to have an extremely smooth surface finish. This may involve precision grinding and polishing of the roll surfaces to ensure that the final product has an aesthetically pleasing appearance.
3.2 Profile Complexity
The complexity of the profile being produced is another crucial design factor. Simple profiles, like straight - sided channels or flat - topped angles, require a relatively straightforward die design. However, for complex profiles with multiple bends, curves, and intricate features, the die design becomes much more challenging.
In the case of a profile with sharp internal corners, the die design needs to account for the material's flow and potential cracking at the corners. Special techniques may be employed, such as using pre - notching or multiple - stage bending at the corners to reduce stress concentrations. For profiles with variable cross - sections along their length, the die design must incorporate mechanisms to adjust the shaping process continuously as the sheet moves through the rolls.
3.3 Production Volume and Speed
The intended production volume and speed also impact the die design. For high - volume production runs, the die needs to be designed for durability and long - term performance. This may involve using more expensive, high - quality materials for the rolls and implementing advanced heat - treatment processes to enhance their wear resistance.
If the production speed is high, the die design must ensure that the material can be formed quickly without sacrificing quality. This may require optimizing the roll - to - roll contact areas, reducing friction, and ensuring efficient transfer of the forming forces. In some cases, high - speed roll forming may also require additional cooling mechanisms for the rolls to prevent overheating, which can affect the material properties and the accuracy of the forming process.
4. Manufacturing of Roll Forming Dies
4.1 Precision Machining
Precision machining is the primary method for manufacturing roll forming dies. Computer - Numerical - Control (CNC) machining is widely used due to its ability to achieve high levels of accuracy. CNC mills, lathes, and grinders are employed to shape the rolls and other die components.
The process begins with the design of the die in a CAD (Computer - Aided Design) software. The CAD model is then transferred to the CNC machine, which interprets the design data and precisely cuts and shapes the raw material, typically a block of steel. The machining process may involve rough cutting to remove the majority of the excess material, followed by fine - finishing operations such as grinding and polishing to achieve the required surface finish and dimensional tolerances.
4.2 Heat Treatment
After machining, the roll forming die components often undergo heat treatment processes. Heat treatment is crucial for enhancing the mechanical properties of the die. For example, the rolls may be hardened through processes like quenching and tempering. Quenching involves rapidly cooling the heated rolls in a suitable medium, such as oil or water, to increase their hardness. Tempering is then carried out to reduce the brittleness caused by quenching and to achieve the desired balance of hardness and toughness.
In some cases, surface - hardening treatments like carburizing or nitriding may be applied. Carburizing involves diffusing carbon into the surface layer of the rolls, increasing their surface hardness and wear resistance. Nitriding, on the other hand, involves introducing nitrogen into the surface, which can improve the corrosion resistance and fatigue strength of the die components.
4.3 Assembly and Quality Control
Once the individual die components are manufactured and heat - treated, they are assembled into a complete roll forming die. The assembly process requires careful alignment and fastening of the rolls, guides, and other components. Precision alignment is crucial to ensure that the sheet is properly shaped as it moves through the die.
Quality control is an integral part of the die - manufacturing process. Various inspection techniques are used, including dimensional inspection using precision measuring instruments like coordinate - measuring machines (CMMs). CMMs can accurately measure the dimensions of the die components to ensure that they meet the design specifications. Surface finish inspection may also be carried out using optical profilometers or other surface - measurement devices. In addition, functional testing of the assembled die may be performed by running sample sheets through the roll forming machine to verify the accuracy of the profile shaping.
5. Applications of Roll Forming Dies
5.1 Construction Industry
The construction industry is one of the largest consumers of products produced using roll forming dies. Steel studs, which are used in the construction of walls, ceilings, and partitions, are typically made through roll forming. The roll forming die shapes flat steel sheets into the characteristic C - or U - shaped profiles of the studs. These studs offer high strength - to - weight ratios and are easy to install, making them a popular choice in modern construction.
Roofing sheets, both metal and some composite materials, are also produced using roll forming dies. The dies can create profiles with features such as corrugations or standing seams, which enhance the strength and waterproofing capabilities of the roofing. For example, standing - seam metal roofing is formed using roll forming dies that create the raised seams, which are interlocked during installation to provide a watertight seal.
5.2 Automotive Industry
In the automotive industry, roll forming dies are used for manufacturing a variety of components. Door frames, which need to be strong, lightweight, and have precise dimensions for proper fitment, are often roll - formed. The roll forming process can create the complex shapes required for door frames, including the curved sections and the flanges for attaching the door panels.
Automotive trim pieces, such as window surrounds and body - side moldings, are also produced using roll forming dies. These trim pieces not only add an aesthetic touch to the vehicle but also serve functional purposes, such as protecting the body from scratches and providing a seal around the windows. The roll forming process can produce these trim pieces with consistent quality and at a relatively low cost, making it suitable for high - volume automotive production.
5.3 Packaging and Consumer Goods Industry
In the packaging industry, roll forming dies are used to produce components such as metal cans and tubes. For example, aluminum beverage cans are formed from flat aluminum sheets using roll forming techniques. The die shapes the sheet into a cylindrical shape, and subsequent operations are carried out to form the ends and create the final can.
In the consumer goods industry, roll forming dies are used to manufacture items like metal furniture frames, such as those for chairs and tables. The roll forming process can create the tubular or angular profiles required for furniture frames, and the dies can be designed to produce different sizes and styles to meet consumer demands.
6. Advantages of Roll Forming Dies
6.1 High - Volume, Cost - Effective Production
Roll forming dies are highly suitable for high - volume production. Once the die is set up and the production process is optimized, the roll forming machine can produce a continuous stream of profiles at a relatively high speed. The cost per unit of production is low, especially when compared to other manufacturing methods like stamping or machining for large - scale production. This is because the roll forming process requires less material waste, as the flat sheet is gradually shaped without significant material removal.
6.2 High Dimensional Accuracy
Roll forming dies can achieve a high degree of dimensional accuracy. The precision machining and careful design of the die ensure that the profiles produced have consistent dimensions. For example, in the production of components for the aerospace industry, where tight tolerances are crucial, roll forming dies can be designed to produce profiles with dimensional tolerances in the range of ±0.1mm or even less. This accuracy is essential for ensuring proper fit and function of the components in the final product.
6.3 Versatility in Material and Profile Shapes
Roll forming dies can be used with a wide range of materials, from metals to plastics and composites. This versatility allows manufacturers to produce a diverse range of products. Moreover, the dies can be designed to create a vast variety of profile shapes, from simple geometric shapes to complex, custom - designed profiles. This makes roll forming a preferred method for producing components with unique shapes that may be difficult to achieve using other manufacturing techniques.
6.4 Energy - Efficient Process
The roll forming process is relatively energy - efficient. Since the material is gradually formed through a series of rolling operations, it requires less energy compared to processes that involve high - force impact or extensive material removal, such as forging or machining. This energy efficiency not only reduces the production cost but also has a positive environmental impact by minimizing the overall energy consumption of the manufacturing process.
7. Challenges and Solutions in Roll Forming Die Usage
7.1 Die Wear and Maintenance
One of the main challenges in using roll forming dies is die wear. The continuous contact between the rolls and the material, especially when processing hard materials or at high production speeds, can cause the rolls to wear out over time. Worn - out rolls can lead to inconsistent profile shapes, surface defects, and increased scrap rates.
To address this issue, regular maintenance of the roll forming die is essential. This includes periodic inspection of the rolls for signs of wear, such as grooves or uneven surfaces. When wear is detected, the rolls can be re - ground or replaced. Using high - quality, wear - resistant materials for the rolls, such as carbide - coated steel, can also significantly extend the die's lifespan. In addition, implementing proper lubrication systems during the roll forming process can reduce friction and wear between the rolls and the material.
7.2 Material Variability
Material variability can pose challenges in roll forming. Different batches of the same material may have slightly different mechanical properties, such as thickness variations or differences in yield strength. These variations can affect the roll forming process, leading to inconsistent profile shapes or even material failure during forming.
To overcome material variability, manufacturers can implement strict quality control measures for the incoming raw materials. This may include measuring the thickness and mechanical properties of each batch of material before processing. In addition, modern roll forming machines can be equipped with sensors that can detect the material properties in - line and adjust the roll forming process parameters, such as the forming force and speed, to compensate for the material variations.
7.3 Design Complexity for New Profiles
Designing roll forming dies for new or complex profiles can be a challenging task. It requires a deep understanding of material behavior, mechanical engineering principles, and the roll forming process itself. The design process may involve multiple iterations and simulations to ensure that the die can successfully form the desired profile.
To simplify the design process for new profiles, manufacturers can use advanced computer - aided engineering (CAE) software. CAE software can simulate the roll forming process, predicting the material flow, stress distribution, and potential forming defects. This allows designers to optimize the die design before manufacturing, reducing the risk of costly design errors and improving the overall efficiency of the die - development process.
8. Future Trends in Roll Forming Die Technology
8.1 Advanced Materials for Die Construction
The future of roll forming dies may see the use of more advanced materials for die construction. Nanocomposite materials, for example, offer the potential for improved wear resistance, strength, and toughness. These materials can be engineered at the nanoscale to have unique properties that can significantly enhance the performance of roll forming dies. In addition, the development of new, high - performance coatings for die components can further improve their durability and resistance to corrosion and wear.
8.2 Integration of Smart Technologies
Roll forming dies may become more integrated with smart technologies in the future. Sensors can be embedded in the die components to monitor various parameters, such as the temperature, pressure, and wear of the rolls. This real - time data can be used to optimize the roll forming process, predict maintenance needs, and ensure the quality of the produced profiles. In addition, the integration of artificial intelligence and machine learning algorithms can analyze the sensor data and automatically adjust the roll forming process parameters to achieve the best possible results.
8.3 Sustainable Manufacturing Practices
As environmental concerns become more prominent, the roll forming die industry is likely to adopt more sustainable manufacturing practices. This may include the use of recycled materials for die construction, reducing energy consumption during the die - manufacturing process, and optimizing the roll forming process to minimize material waste. In addition, the development of water - based lubricants or dry - forming techniques can reduce the environmental impact of the roll forming process.
In conclusion, the roll forming die is a vital technology in modern manufacturing, enabling the production of high - quality, consistent profiles across a wide range of industries. While there are challenges associated with its use, ongoing technological advancements and innovative solutions are continuously improving the performance and capabilities of roll forming dies. As industries continue to evolve, the roll forming die will play an increasingly important role in driving efficient, sustainable, and high - quality manufacturing processes.