Hotline
+86-136 8495 9862
Email:cennia@szmizhi.com
Add::104,Building 27,Third Industrial Zone, Longxi Community,Longgang District,Shenzhen,China.
Coil Forming & Handling Equipment
Surface Treatment Equipment
Solutions
Application
About Us
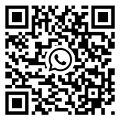
Welcome to MIZHI
For consultation/feedback, please call the service hotline: +86-136 8495 9862 Email:cennia@szmizhi.com
Roll forming machines are essential equipment in various industries, used to transform flat metal sheets into a wide range of profiled products. These machines play a crucial role in manufacturing everything from roofing and siding materials in the construction industry to automotive components and electrical conduits. When considering the acquisition of a roll forming machine, price is a significant factor that potential buyers must carefully evaluate. The price of a roll forming machine is influenced by numerous elements, and understanding these factors can help businesses make informed decisions.
Factors Affecting Roll Forming Machine Price
Machine Size and Capacity
1. Profile Dimensions
The size of the profiles that a roll forming machine can produce has a direct impact on its price. Machines designed to create large - scale profiles, such as those used for industrial - grade roofing panels with widths of several feet, require more substantial and robust components. The larger the profile dimensions, the heavier - duty the machine's frame, rollers, and drive system need to be. For example, a roll forming machine capable of producing 12 - foot - long and 4 - foot - wide roofing panels will be significantly more expensive than one that manufactures smaller, 2 - foot - long and 1 - foot - wide decorative metal strips.
2. Material Thickness and Strength
The ability to handle different thicknesses and types of materials also affects the price. Roll forming machines that can process thick and high - strength metals, like stainless steel or heavy - gauge aluminum, are more costly. These machines need more powerful motors to drive the rollers and overcome the resistance of the tough materials. A machine designed to roll 0.125 - inch - thick stainless steel sheets will be pricier than one for 0.03 - inch - thick mild steel sheets. Additionally, the machine may require specialized tooling and heat - treatment processes for the rollers to withstand the wear and tear from working with high - strength materials.
Production Speed
1. High - Speed vs. Standard - Speed Machines
Production speed is another determinant of the roll forming machine price. High - speed roll forming machines are designed to produce a large volume of products in a short time. These machines are equipped with advanced drive systems, precise control mechanisms, and high - performance motors. For instance, a high - speed roll forming machine in a large - scale manufacturing plant that can produce 100 linear feet of profiled material per minute will command a much higher price compared to a standard - speed machine that produces only 20 linear feet per minute. The faster - speed machine not only increases productivity but also requires more sophisticated engineering to ensure the quality of the formed profiles at high speeds.
2. Automation and Efficiency
Automation features that enhance production speed and efficiency also contribute to the cost. Machines with automated coil loading, feeding, and cut - off systems are more expensive. These automated functions reduce the need for manual labor, minimize production time, and improve overall productivity. For example, an automated roll forming machine with a robotic arm for coil handling and an integrated computer - controlled cutting system will be costlier than a basic manual - operation machine. The investment in automation technology pays off in the long run through increased production output and reduced labor costs, but it comes with a higher upfront price.
Machine Complexity and Customization
1. Number of Roll Stations
The number of roll stations in a roll forming machine is a key factor in its complexity and price. Each roll station plays a role in gradually shaping the metal sheet into the desired profile. Machines with a larger number of roll stations can create more complex profiles with multiple bends and intricate shapes. A simple roll forming machine for making basic C - channels may have 4 - 6 roll stations, while a machine for producing elaborate automotive body parts may have 12 - 15 roll stations. As the number of roll stations increases, so does the cost of the machine due to the additional tooling, precision engineering, and control systems required.
2. Custom Profile Requirements
Custom - designed roll forming machines for unique profile shapes are significantly more expensive than standard machines. When a business has specific profile requirements that are not commonly available in off - the - shelf machines, the manufacturer has to develop custom tooling, design specialized roll profiles, and program the machine's control system accordingly. For example, if a company needs a roll forming machine to produce a custom - shaped metal bracket for a new product line, the machine will be tailored to that specific design. The research, development, and manufacturing of custom - made machines involve a high level of engineering expertise and specialized production processes, which drive up the price.
Brand and Reputation
1. Established vs. New Brands
Well - established brands in the roll forming machine industry often command higher prices. These brands have built a reputation for quality, reliability, and innovation over time. They invest heavily in research and development to improve their machines' performance, durability, and technological features. For example, a machine from a long - standing, globally recognized brand may have better - engineered components, more precise control systems, and a longer lifespan compared to a machine from a new or lesser - known brand. Buyers are willing to pay a premium for the assurance of quality and the after - sales support that established brands offer.
2. Quality and Reliability
The quality and reliability of a roll forming machine are closely related to its brand reputation. High - quality machines are made with top - grade materials, undergo rigorous quality control processes during manufacturing, and are designed to withstand continuous and heavy use. A reliable machine reduces downtime due to breakdowns, which is crucial for maintaining production schedules and minimizing costs. For instance, a brand - name roll forming machine may use high - quality steel for its frame, precision - ground rollers, and advanced electronic control components. This higher quality construction not only contributes to the machine's performance but also justifies its higher price.
Accessories and Additional Features
1. Cut - Off Systems
The type of cut - off system included with the roll forming machine affects the price. Basic machines may have a simple manual cut - off mechanism, while more advanced models are equipped with automated flying cut - off systems. An automated flying cut - off system can precisely cut the formed profiles while the machine is in motion, ensuring accurate lengths and high - speed production. These advanced cut - off systems are more expensive due to their complex engineering and high - precision operation. For example, a roll forming machine with a computer - controlled flying cut - off system that can cut profiles to within ±0.01 - inch tolerance will be costlier than one with a manual, less - accurate cut - off device.
2. Material Handling Equipment
Additional material handling equipment, such as coil reels, uncoilers, and stackers, can also increase the price of the roll forming machine. A complete package with a high - capacity coil reel for holding large metal coils, an uncoiler that smoothly feeds the metal sheet into the machine, and a stacker for neatly piling up the finished profiles is more expensive than a machine sold without these accessories. These material handling components are designed to work in harmony with the roll forming machine, improving the overall production process. However, their inclusion adds to the total cost of the equipment.
Price Range of Roll Forming Machines
1. Entry - Level Machines
Entry - level roll forming machines are typically the most affordable option. These machines are suitable for small - scale operations or for producing simple profiles. They usually have a limited capacity in terms of profile size and material thickness. Entry - level machines may lack some of the advanced features found in higher - end models, such as automated material handling or high - speed production capabilities. For example, a basic roll forming machine for making simple metal brackets or small - scale roofing components may cost anywhere from $5,000 to $20,000. These machines are often manually operated, with a relatively small number of roll stations, and are made with more common and cost - effective materials.
2. Mid - Range Machines
Mid - range roll forming machines offer a balance between price and performance. They can handle a wider variety of materials and produce more complex profiles compared to entry - level machines. Mid - range machines may have some automated features, such as semi - automated cut - off systems or basic material feeding mechanisms. They are suitable for medium - sized manufacturing businesses that require a certain level of productivity and flexibility. The price of mid - range roll forming machines typically ranges from $20,000 to $80,000. These machines may have 6 - 10 roll stations, be able to process materials of moderate thickness, and offer better precision in profile formation.
3. High - End and Custom Machines
High - end roll forming machines are the most expensive. These machines are designed for large - scale industrial production, high - speed manufacturing, and for creating highly complex profiles. They come with advanced automation features, state - of - the - art control systems, and are built to handle high - strength and thick materials. Custom - made high - end machines, tailored to specific and unique production requirements, can be even more costly. High - end roll forming machines can cost upwards of $80,000, and custom - built models may reach several hundred thousand dollars. For example, a high - speed roll forming machine used in the automotive industry to produce complex body panels, with multiple automated material handling systems, precise roll stations, and advanced quality control sensors, will be at the upper end of the price spectrum.
Cost - Benefit Analysis
1. Long - Term vs. Short - Term Costs
When evaluating the price of a roll forming machine, it's important to consider both long - term and short - term costs. While a high - end machine may have a significant upfront cost, it can offer long - term savings in terms of productivity, reduced labor costs, and lower maintenance requirements. For example, a high - speed, automated roll forming machine may cost $100,000 initially, but over a 5 - year period, it can produce a much larger volume of products compared to a cheaper, slower machine. The increased production output can lead to higher revenues, and the reduced need for manual labor can cut down on labor costs. In contrast, a low - cost, entry - level machine may seem attractive in the short term, but it may require more frequent repairs, have a shorter lifespan, and limit production growth, resulting in higher long - term costs.
2. Return on Investment (ROI)
Calculating the return on investment is crucial in justifying the purchase of a roll forming machine. ROI takes into account the initial investment, the expected increase in production output, the cost savings in labor and other operational expenses, and the revenue generated from selling the additional products. For instance, if a business invests $50,000 in a mid - range roll forming machine and, as a result, is able to increase its monthly production by 20%, leading to an additional $10,000 in monthly revenue and a $2,000 reduction in labor costs, the ROI can be calculated. Over time, the positive ROI indicates that the investment in the roll forming machine is financially viable and can contribute to the business's growth and profitability.
Conclusion
The price of a roll forming machine is determined by a multitude of factors, including machine size and capacity, production speed, complexity and customization, brand reputation, and the inclusion of accessories and additional features. Potential buyers need to carefully assess their specific production requirements, budget constraints, and long - term business goals when considering the purchase of a roll forming machine. By understanding the relationship between these factors and the price, businesses can make an informed decision that balances cost with performance and productivity, ultimately leading to a successful investment in this essential manufacturing equipment. Whether it's an entry - level machine for a small - scale operation or a high - end, custom - built machine for a large - scale industrial plant, the right choice of roll forming machine can significantly impact a company's competitiveness and bottom line in the market.