Hotline
+86-136 8495 9862
Email:cennia@szmizhi.com
Add::104,Building 27,Third Industrial Zone, Longxi Community,Longgang District,Shenzhen,China.
Coil Forming & Handling Equipment
Surface Treatment Equipment
Solutions
Application
About Us
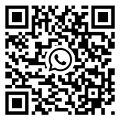
Welcome to MIZHI
For consultation/feedback, please call the service hotline: +86-136 8495 9862 Email:cennia@szmizhi.com
Roll forming is a highly efficient and versatile manufacturing process that has revolutionized the production of sheet metal components. This process involves continuously bending a long strip of sheet metal as it passes through a series of rollers. The result is a precisely formed profile with consistent cross - sectional dimensions.
The history of roll forming dates back several decades. It has evolved from simple manual operations to highly automated and computer - controlled systems. This evolution has been driven by the need for increased production rates, improved quality, and greater design flexibility. One of the key advantages of roll forming is its ability to produce complex shapes with high precision. The rollers can be custom - designed to create profiles with various curves, angles, and contours. This allows for the manufacturing of components that would be difficult or impossible to produce using other methods.
Sheet metal used in roll forming can vary in thickness, material type, and surface finish. Common materials include steel, aluminum, copper, and stainless steel. The choice of material depends on the specific requirements of the application, such as strength, corrosion resistance, and aesthetic appeal. Thicker sheet metal is typically used for structural components, while thinner gauges are suitable for decorative or lightweight applications.
The roll forming process begins with the preparation of the sheet metal strip. This may involve cutting the strip to the desired length, cleaning the surface to remove any contaminants, and applying a lubricant to reduce friction during the forming process. The prepared strip is then fed into the roll forming machine. The machine consists of a series of rollers arranged in a specific sequence. Each roller imparts a specific bend or deformation to the sheet metal as it passes through.
The number of rollers in a roll forming line can vary depending on the complexity of the profile being produced. Some simple profiles may require only a few rollers, while more complex shapes can involve dozens of rollers. The rollers are typically made of hardened steel to ensure durability and resistance to wear. They are carefully machined and polished to achieve the required surface finish and dimensional accuracy.
During the roll forming process, the sheet metal is gradually shaped into the desired profile. The speed at which the sheet metal passes through the rollers can be adjusted to control the rate of production. Higher speeds result in increased production rates but may require more precise control to ensure quality. The formed profile is then cut to the required lengths, either continuously or in discrete sections.
One of the major benefits of roll forming is its high production efficiency. Once the roll forming machine is set up and calibrated, it can produce large quantities of components with minimal operator intervention. This makes it ideal for high - volume production runs. Additionally, the process generates very little waste compared to other manufacturing methods such as stamping or cutting.
Roll - formed sheet metal components are widely used in various industries. In the automotive industry, they are used for manufacturing body panels, frames, and other structural components. The aerospace industry relies on roll - formed parts for aircraft fuselages, wings, and interior components. Roll - formed profiles are also common in the construction industry for making roofing, siding, and structural framing. In addition, they are used in the manufacturing of furniture, appliances, and many other consumer products.
Quality control is a crucial aspect of roll forming. During the production process, various parameters such as the dimensions of the profile, the surface finish, and the mechanical properties of the sheet metal are monitored. Any deviations from the specified requirements are detected and corrected promptly. This ensures that the final products meet the highest quality standards.
In conclusion, roll forming sheet metal is a sophisticated and efficient manufacturing process that offers numerous advantages. It enables the production of complex shapes with high precision, high production rates, and minimal waste. The wide range of applications in different industries demonstrates its versatility and importance in modern manufacturing. As technology continues to advance, we can expect further improvements in the roll forming process, leading to even more innovative and high - quality sheet metal products.