Hotline
+86-136 8495 9862
Email:cennia@szmizhi.com
Add::104,Building 27,Third Industrial Zone, Longxi Community,Longgang District,Shenzhen,China.
Coil Forming & Handling Equipment
Surface Treatment Equipment
Solutions
Application
About Us
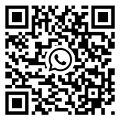
Welcome to MIZHI
For consultation/feedback, please call the service hotline: +86-136 8495 9862 Email:cennia@szmizhi.com
1. Introduction
In the dynamic world of manufacturing, roll forming has emerged as a crucial process for creating a wide array of metal products. Roll forming suppliers play a pivotal role in this ecosystem, providing the necessary equipment, services, and expertise to enable industries to transform raw materials into precisely shaped components. These suppliers are not only purveyors of machinery but also partners in the manufacturing journey, offering solutions tailored to diverse applications, from construction and automotive to furniture and electronics.
2. The Role of Roll Forming Suppliers in the Industry
2.1. Equipment Provision
At the heart of a roll forming supplier's offerings is the equipment itself. Roll forming machines come in various configurations, each designed to meet specific manufacturing requirements. Suppliers such as Hangzhou Roll Forming Technology Co., Ltd. have been at the forefront of designing and manufacturing roll forming, coil processing equipment, and tube/pipe mills for over a decade. Their product range includes cold roll forming machines, which gradually shape cold plates or strips into various sectional shapes as the material passes through consecutive rolls. This type of equipment is widely used in industries like automotive, construction, and building materials, where the need for consistent, high - quality profiles is paramount.
For instance, in the construction industry, roof and wall panel roll forming machines are essential for producing the panels that form the exterior of buildings. These machines can create panels with different profiles, such as corrugated or trapezoidal, which offer enhanced strength and weather resistance. Metal deck roll forming machines, another product in the lineup, are used to produce decks for floors in commercial and industrial buildings. These decks provide structural support and are often used in combination with concrete to create a durable and stable flooring system.
2.2. Customization Services
One of the key differentiators among roll forming suppliers is their ability to offer customization. Many industries have unique requirements for the profiles they need, and suppliers must be able to adapt their equipment and processes accordingly. M.P. Metal Products, Inc., an ISO 9001:2008 certified manufacturer, specializes in custom roll forming. They can run unique profiles in gauges ranging from 0.005" to 0.165" and widths up to 48" on 35 lines. This level of customization allows them to serve a wide range of markets, including furniture, electrical, material handling, recreation, and medical.
In the medical industry, for example, precise and customized roll - formed parts may be required for medical equipment. These parts need to meet strict quality and safety standards. The supplier works closely with the medical device manufacturer to understand the exact specifications, such as the shape, size, and material properties of the roll - formed components. They then use their expertise and advanced machinery to develop the tooling and set up the roll forming process to produce parts that meet these exacting requirements.
2.3. Technical Support and Training
A reliable roll forming supplier doesn't just sell equipment; they also provide ongoing technical support and training. This is crucial for ensuring that the customer can operate the equipment effectively and efficiently. Sheffield Metals, a distributor of new tech machinery (NTM) portable roll formers, offers access to technical support and training. NTM's portable roof panel, wall panel, and gutter machines can be used either on - site or in - plant, and the technical support ensures that any issues with the machine are quickly resolved.
Training provided by suppliers can cover a range of topics. It may include basic machine operation, such as how to start and stop the machine, adjust the speed, and load the raw material. Advanced training may focus on machine maintenance, including how to identify and replace worn - out parts, perform regular lubrication, and troubleshoot common problems. Additionally, suppliers may train customers on how to optimize the roll forming process for different materials and profiles, improving the quality of the final product and reducing waste.
2.4. Material and Component Sourcing
Some roll forming suppliers also assist with material and component sourcing. They have established relationships with raw material suppliers and can help their customers obtain the right materials for their roll forming projects. For example, when working with metals like steel, aluminum, copper, or brass, the supplier can recommend the most suitable grade and thickness based on the application requirements.
In the automotive industry, where lightweight yet strong materials are often preferred, a roll forming supplier may suggest aluminum alloys for components such as body frames or interior trim. The supplier can also source other components required for the roll forming process, such as specialized rolls, bearings, and control systems. This one - stop - shop approach simplifies the supply chain for the customer, reducing the time and effort required to source different elements of the roll forming operation.
3. Types of Roll Forming Suppliers
3.1. Equipment Manufacturers
Equipment manufacturers are the backbone of the roll forming supply chain. These companies design and build roll forming machines from the ground up. Roll Forming Machines LLC, based in Orlando, Florida, has been a trusted supplier since 2009. They manufacture a wide range of machines, including auto stackers, custom roll forming machines, deck roll forming machines, and drip edge roll forming machines.
Their manufacturing process involves a combination of precision engineering and advanced manufacturing techniques. The machines are designed to be robust and reliable, capable of withstanding the rigors of continuous use in industrial settings. For example, their high - speed roll forming machines are engineered to produce parts at a rapid pace without sacrificing quality. The company also offers demonstrations and technical consultations at their US - based facility, allowing potential customers to see the machines in action and discuss their specific needs with the sales team.
3.2. Distributors
Distributors play an important role in making roll forming equipment and related products accessible to a wider market. They act as intermediaries between the equipment manufacturers and the end - users. Sheffield Metals, as mentioned earlier, is a distributor of NTM's portable roll formers. They offer a range of benefits to customers, including reduced lead times. Since they have an inventory of machines, customers can often get their equipment more quickly compared to ordering directly from the manufacturer.
Distributors also provide value - added services such as installation and after - sales support. They may have a team of technicians who are trained to install the roll forming machines at the customer's site and ensure that they are up and running smoothly. In addition, they can offer maintenance contracts and spare parts, ensuring that the customer's machines are always in good working condition.
3.3. Service - Oriented Suppliers
Service - oriented suppliers focus on providing roll forming services rather than selling equipment. Companies like Johnson Bros. Roll Forming Co. are leading manufacturers in roll forming metals, both pre - finished and plain. They can produce a variety of profiles, including u - channels, c - channels, j - channels, hat channels, box channels, zee channels, strut channels, moldings, angles, and rings (bent inline).
These service - oriented suppliers have a high level of expertise in the roll forming process. They can take a customer's design concept and turn it into a finished product. Their capabilities extend beyond basic roll forming to include secondary operations such as notching, punching, and fabricating. For example, if a customer needs a roll - formed part with specific holes or notches for assembly purposes, Johnson Bros. can perform these operations as part of their service, providing a complete solution to the customer.
4. Key Considerations When Choosing a Roll Forming Supplier
4.1. Experience and Reputation
Experience is a crucial factor when selecting a roll forming supplier. A supplier with a long - standing presence in the industry is more likely to have encountered a wide range of challenges and developed effective solutions. United Roll Forming, Inc., with over 50 years of experience, has established a reputation for specializing in roll forming for a variety of industries. Their long - term success is a testament to their ability to adapt to changing market demands and technological advancements.
Reputation can be gauged through customer reviews, testimonials, and industry awards. For instance, Jobsite, an industry leader in engineering and manufacturing roll forming equipment since 1980, has earned a reputation for reliability. Their machines are built to last, with a design that aims for 10 + years of service without a service call. Customer testimonials often highlight the durability and performance of their equipment, giving potential customers confidence in their products.
4.2. Product Range and Customization Capabilities
The supplier's product range and customization capabilities should align with the customer's needs. Premier Products of Racine, Inc., a full - service company established in 1999, provides custom roll formed products for applications such as outdoor appliances, tanker trucks, and office furniture. They can handle materials like aluminum, copper, galvalume, carbon steel, and stainless steel, and their roll forming capabilities include cleaning, cut - off, in - line edge conditioning, embossing, and pre - notching.
A customer in the outdoor appliance industry may require a unique roll - formed profile for a barbecue grill. Premier Products of Racine would be able to use their extensive material options and customization techniques to create a profile that meets the aesthetic and functional requirements of the grill, such as providing a smooth surface for easy cleaning and a specific shape for proper heat distribution.
4.3. Quality Assurance and Certifications
Quality assurance is non - negotiable in the roll forming industry. Suppliers should have robust quality control processes in place. Some suppliers, like M.P. Metal Products, Inc., are ISO 9001:2008 certified. This certification indicates that the company has implemented a quality management system that meets international standards.
Quality control may involve inspections at various stages of the roll forming process, from the incoming raw materials to the finished product. For example, the supplier may check the thickness and flatness of the metal coils before they are fed into the roll forming machine. After the parts are formed, they may be inspected for dimensional accuracy, surface finish, and any signs of defects. Certifications and quality control measures give customers confidence that the products they receive will meet their quality expectations.
4.4. Cost - Effectiveness and Pricing
Cost - effectiveness is an important consideration. While the initial cost of equipment or services is a factor, it's also essential to consider the long - term costs, such as maintenance, operating costs, and the cost of any potential rework. Some suppliers may offer more affordable equipment upfront but have higher maintenance costs over time.
On the other hand, a supplier that offers a higher - quality, more expensive machine may prove to be more cost - effective in the long run if it has lower maintenance requirements and a longer lifespan. Service - oriented suppliers may also have different pricing models based on the complexity of the roll forming project, the quantity of parts required, and the materials used. Customers need to carefully evaluate these factors to determine the most cost - effective option for their specific needs.
5. Global Roll Forming Suppliers and Their Market Reach
5.1. North American Suppliers
In North America, there are numerous roll forming suppliers that serve both the domestic and international markets. Johnson Bros. Roll Forming Co. in Berkeley, Illinois, has a significant presence in the United States. They offer a wide range of roll - formed products and services, catering to industries such as construction, automotive, and manufacturing. Their location in the Midwest provides easy access to major transportation routes, allowing them to efficiently distribute their products across the country.
Another notable North American supplier is Roll Forming Machines LLC in Florida. Their strategic location in Orlando, a central hub in the state, enables them to serve customers not only in Florida but also in other parts of the United States and even internationally. They have a diverse customer base that includes small - and medium - sized enterprises as well as large corporations, all of which rely on their high - quality roll forming machines.
5.2. European Suppliers
In Europe, suppliers like Formit Ltd in Sandwell, United Kingdom, are making their mark. Formit specializes in supplying complete roll forming and coil processing lines, acting as a comprehensive turnkey supplier. They offer equipment design, installation, and maintenance services, providing a one - stop solution for customers in the region. Their services are sought after by industries such as automotive, aerospace, and construction, which are prominent in Europe.
European suppliers often adhere to strict European Union standards regarding product quality, safety, and environmental impact. This can be an advantage for customers who require products that meet these high - level standards. For example, in the aerospace industry, where safety and precision are of utmost importance, European roll forming suppliers can provide equipment and services that meet the stringent requirements of aircraft manufacturers.
5.3. Asian Suppliers
Asia is home to a large number of roll forming suppliers, many of which have become major players in the global market. Hangzhou Roll Forming Technology Co., Ltd. in China has been designing and manufacturing roll forming and related equipment for over 17 years. They have a wide product range and offer customized solutions for various industries, including aerospace, automotive, and oil & gas. Their products are exported to many countries around the world, taking advantage of China's position as a global manufacturing hub.
Another Chinese supplier, Botou Roll Forming Machine, has also made a name for itself in the industry. With a significant workforce and years of experience, they produce a variety of roll forming machines that are used in different applications. Asian suppliers often offer competitive pricing due to lower production costs in some regions, which can be attractive to customers looking for cost - effective solutions without sacrificing quality.
6. Future Trends and Innovations Among Roll Forming Suppliers
6.1. Automation and Smart Technology Integration
Roll forming suppliers are increasingly integrating automation and smart technology into their equipment and processes. Automated roll forming machines can operate with minimal human intervention, reducing the risk of human error and increasing production efficiency. These machines can be programmed to perform complex roll forming operations, adjust parameters in real - time based on sensor data, and even monitor their own performance for predictive maintenance.
For example, some modern roll forming machines are equipped with sensors that can detect the thickness of the material as it is being fed into the machine. If there are any variations in the thickness, the machine can automatically adjust the pressure of the rolls to ensure a consistent profile. Smart technology can also enable remote monitoring and control of the machines, allowing suppliers to provide better technical support and customers to manage their operations more efficiently.
6.2. Sustainable and Eco - Friendly Solutions
As environmental concerns grow, roll forming suppliers are focusing on developing sustainable and eco - friendly solutions. This includes using recycled materials in the roll forming process, reducing energy consumption in their equipment, and minimizing waste. Some suppliers are exploring the use of alternative energy sources, such as solar or wind power, to run their roll forming machines.
In addition, they are developing ways to recycle or reuse the scrap generated during the roll forming process. For example, instead of discarding metal scraps, they can be melted down and reformed into new raw materials for roll forming. Suppliers may also offer products and services that help customers reduce their environmental impact, such as providing more energy - efficient roll forming machines or advising on the use of sustainable materials.
6.3. Advanced Material Processing
The development of new materials is also driving innovation among roll forming suppliers. They are constantly adapting their equipment and processes to handle advanced materials, such as high - strength alloys, composites, and lightweight metals. For example, as the demand for lightweight components in the automotive and aerospace industries grows, suppliers are finding ways to roll form materials like carbon fiber - reinforced composites.
Processing these materials requires specialized knowledge and equipment. The rolls used in the roll forming machine may need to be made of different materials or have a unique design to handle the properties of the advanced materials. Suppliers are investing in research and development to stay at the forefront of advanced material processing, enabling their customers to use these new materials in their products.
7. Conclusion
Roll forming suppliers are an integral part of the manufacturing value chain, providing essential equipment, services, and expertise. Their ability to offer customization, technical support, and high - quality products makes them indispensable to industries ranging from construction to automotive. When choosing a roll forming supplier, customers need to carefully consider factors such as experience, product range, quality assurance, and cost - effectiveness. As the industry continues to evolve, suppliers are embracing trends such as automation, sustainability, and advanced material processing, ensuring that they can meet the changing needs of their customers and contribute to the growth and innovation of the manufacturing sector. Whether it's a small - scale project or a large - scale industrial operation, the right roll forming supplier can make a significant difference in the success of a manufacturing venture.