Hotline
+86-136 8495 9862
Email:cennia@szmizhi.com
Add::104,Building 27,Third Industrial Zone, Longxi Community,Longgang District,Shenzhen,China.
Coil Forming & Handling Equipment
Surface Treatment Equipment
Solutions
Application
About Us
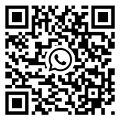
Welcome to MIZHI
For consultation/feedback, please call the service hotline: +86-136 8495 9862 Email:cennia@szmizhi.com
Roll forming tube is a highly efficient and widely used manufacturing process for producing tubes with various cross - sectional shapes and sizes. This process involves gradually deforming a flat strip of metal through a series of rolls to form a continuous tube. The versatility, precision, and cost - effectiveness of roll forming tube have made it an integral part of numerous industries, from construction and automotive to aerospace and furniture. This article will comprehensively explore the roll forming tube process, its applications, advantages, and key considerations in its implementation.
The Roll Forming Tube Process
Material Preparation
1. Selection of Metal Strips
The process begins with the careful selection of metal strips. Common materials used in roll forming tube include carbon steel, stainless steel, aluminum, and various alloys. The choice of material depends on the specific requirements of the final product. For example, in the automotive industry, where lightweight yet strong components are crucial, aluminum strips are often preferred. In contrast, for applications in harsh environments, such as in the oil and gas industry, stainless steel strips are selected for their corrosion resistance.
The thickness and width of the metal strips are also determined based on the dimensions and strength requirements of the tube. Thicker strips are used for applications that demand high - strength tubes, while wider strips can be used to produce larger - diameter tubes.
2. Surface Treatment
Before the roll forming process, the metal strips may undergo surface treatment. This can include processes such as degreasing to remove any contaminants, rust prevention treatments like galvanizing for steel strips, or pre - painting for aesthetic or corrosion - protection purposes. Surface treatment not only enhances the appearance of the final tube but also improves its durability and performance.
Roll Forming Operation
1. The Role of Roll Stations
The heart of the roll forming tube process lies in the series of roll stations. The flat metal strip is fed through a sequence of these stations, each of which imparts a specific deformation to the strip. The number of roll stations can vary depending on the complexity of the tube's cross - sectional shape. For a simple round - shaped tube, a relatively small number of stations may be sufficient, typically around 8 - 12. However, for more intricate shapes, such as square - shaped tubes with rounded corners or tubes with special flanges, the number of stations can increase to 15 - 20 or even more.
Each roll station consists of a set of upper and lower rolls. These rolls are precisely designed and machined to ensure that the metal strip is gradually and accurately formed into the desired shape. The rolls are usually made of high - quality steel or alloy materials to withstand the high pressures and frictional forces during the roll forming process.
2. Forming the Tube Shape
As the metal strip progresses through the roll stations, the initial flat shape is gradually transformed. In the case of round - tube formation, the strip is gradually curved until the edges meet. For square or rectangular tubes, the corners are formed through a combination of bending and shaping operations at specific roll stations. The process is carefully controlled to ensure that the tube has a uniform wall thickness and a consistent cross - sectional shape throughout its length.
The speed at which the metal strip is fed through the roll stations is also an important parameter. It needs to be carefully adjusted to ensure smooth and accurate forming. Too fast a feed speed may result in uneven deformation or defects in the tube, while too slow a speed can reduce production efficiency.
Welding (if applicable)
1. Types of Welding Methods
For many roll - formed tubes, especially those made from steel or stainless - steel strips, welding is an essential step to join the edges of the formed tube. The most common welding methods used in roll forming tube production are electric resistance welding (ERW) and high - frequency induction welding (HFIW).
In ERW, an electric current is passed through the edges of the metal strip as they are brought together. The resistance of the metal to the current generates heat, which melts the edges and fuses them together. HFIW, on the other hand, uses a high - frequency electromagnetic field to heat the edges of the strip. This method is known for its high - speed welding capabilities and the ability to produce high - quality welds with minimal heat - affected zones.
2. Weld Quality Control
Ensuring high - quality welds is crucial for the integrity of the roll - formed tube. Weld quality control measures include visual inspection for any visible defects such as cracks, porosity, or incomplete fusion. Non - destructive testing methods, such as ultrasonic testing and radiographic testing, are also often used to detect internal weld defects. In addition, the welding parameters, such as current, voltage, and welding speed, are carefully monitored and adjusted to achieve consistent and reliable welds.
Finishing Operations
1. Cutting to Length
After the tube is formed and welded (if required), it needs to be cut to the desired length. This is typically done using a cutting machine, such as a flying saw. The flying saw can cut the moving tube without stopping the production line, ensuring high - speed and accurate cutting. The length of the tubes can be customized according to the specific requirements of the end - user.
2. Deburring and Surface Finishing
The cut ends of the tube may have burrs, which need to be removed. Deburring operations can be manual, using tools like files or grinders, or automated, using specialized deburring machines. After deburring, the tube may undergo further surface finishing operations, such as polishing, sandblasting, or applying a protective coating. These finishing operations enhance the appearance of the tube and improve its corrosion resistance.
Applications of Roll - Formed Tubes
Construction Industry
1. Structural Components
Roll - formed tubes are widely used as structural components in the construction industry. Square and rectangular tubes are commonly used for building frames, columns, and beams. Their high strength - to - weight ratio makes them an ideal choice for supporting heavy loads while minimizing the overall weight of the structure. For example, in multi - story buildings, roll - formed steel tubes can be used to construct the vertical columns, providing stability and durability.
2. Roofing and Siding
Round and rectangular roll - formed tubes are also used in roofing and siding applications. They can be used as purlins to support the roof covering or as part of the framework for siding panels. The corrosion - resistant properties of materials like aluminum and stainless - steel tubes make them suitable for outdoor applications, protecting the building from weather elements.
Automotive Industry
1. Chassis and Frame Components
In the automotive industry, roll - formed tubes play a crucial role in the construction of chassis and frame components. Tubes made from high - strength steel or aluminum are used to form the structural backbone of vehicles. These tubes are designed to provide maximum strength and rigidity while minimizing weight, which is essential for improving fuel efficiency and vehicle performance. For example, the roll - formed tubes in a car's chassis help to absorb and distribute impact forces in the event of a collision, enhancing passenger safety.
2. Exhaust Systems
Roll - formed stainless - steel tubes are commonly used in automotive exhaust systems. The smooth inner surface of the tubes helps to reduce exhaust gas flow resistance, improving engine performance. The corrosion - resistant properties of stainless steel ensure the longevity of the exhaust system, which is exposed to harsh chemicals and high temperatures.
Aerospace Industry
1. Aircraft Structures
The aerospace industry demands materials and components with exceptional strength, lightweight characteristics, and high - quality manufacturing. Roll - formed tubes made from advanced aluminum alloys or titanium are used in aircraft structures, such as wing spars, fuselage frames, and landing gear components. These tubes are precision - formed to meet the strict tolerances required in aerospace applications, ensuring the safety and reliability of the aircraft.
2. Fluid Conduits
Roll - formed tubes are also used as fluid conduits in aircraft for transporting fuel, hydraulic fluids, and pneumatic gases. The seamless and smooth inner surface of the tubes helps to prevent leaks and ensure efficient fluid flow. The materials used are carefully selected to withstand the extreme conditions encountered in flight, such as high pressures, low temperatures, and vibration.
Furniture Industry
1. Frame Structures
In the furniture industry, roll - formed tubes are used to create the frame structures of various furniture pieces, such as chairs, tables, and beds. The versatility of the roll forming process allows for the creation of tubes with unique shapes and designs, adding aesthetic value to the furniture. For example, curved roll - formed tubes can be used to create stylish chair frames, while square tubes can provide a more modern and sturdy look for table frames.
2. Decorative Elements
Roll - formed tubes can also be used as decorative elements in furniture. Tubes with special surface finishes or coatings can enhance the visual appeal of the furniture. For instance, polished aluminum tubes can add a sleek and contemporary touch to a piece of furniture, while powder - coated steel tubes can be customized in different colors to match the overall decor.
Advantages of Roll Forming Tube
High - Volume Production Efficiency
1. Continuous Process
The roll forming tube process is a continuous operation, which allows for high - volume production. Once the setup is complete, the metal strip can be continuously fed through the roll stations, welded (if necessary), and cut to length, resulting in a high output rate. This makes roll forming tube highly suitable for mass - production applications, where large quantities of tubes are required in a short period.
2. Fast Production Speeds
Modern roll forming machines can operate at high speeds, especially when producing simple - shaped tubes. For example, in the production of standard round or square tubes, the feed speed of the metal strip can be adjusted to achieve production rates of several meters per minute. This fast production speed significantly reduces the production time and cost per unit, making roll - formed tubes cost - competitive in the market.
Precision and Consistency
1. Accurate Shape Formation
The roll forming process offers a high level of precision in shaping the metal strip into tubes. The carefully designed and machined rolls ensure that each tube produced has a consistent cross - sectional shape and dimensions. The tolerance levels that can be achieved in roll forming tube are often within very tight limits, making it suitable for applications where precise fit and performance are critical, such as in the aerospace and automotive industries.
2. Uniform Wall Thickness
During the roll forming process, the wall thickness of the tube remains relatively uniform throughout its length. This is important for ensuring the structural integrity and performance of the tube. Whether the tube is used for structural support or as a fluid conduit, a uniform wall thickness helps to distribute stresses evenly and prevent weak points in the tube.
Cost - Effectiveness
1. Reduced Material Waste
Roll forming tube is a relatively material - efficient process. The continuous nature of the process minimizes material waste compared to other manufacturing methods, such as casting or machining. The flat metal strip is gradually formed into the tube shape, with minimal trimming or cutting required. This not only reduces the cost of raw materials but also has environmental benefits by reducing waste.
2. Lower Tooling Costs
Compared to some other manufacturing processes that require complex and expensive tooling, roll forming tube typically has lower tooling costs. The rolls used in the process can be relatively simple in design for basic tube shapes, and they can be reused for multiple production runs. Even for more complex tube shapes, the cost of tooling is often more manageable compared to processes like injection molding or die - casting.
Key Considerations in Roll Forming Tube Production
Material Compatibility
1. Selecting the Right Material
As mentioned earlier, choosing the appropriate metal material is crucial for the success of the roll forming tube process. Different materials have different mechanical properties, such as yield strength, tensile strength, and ductility. These properties affect how the material will respond to the roll forming process. For example, some materials may be more prone to cracking during the bending process, while others may require higher forming pressures. It is essential to conduct thorough material testing and consult with material suppliers to ensure the selected material is suitable for the intended application and the roll forming process.
2. Material Thickness and Width Limitations
The thickness and width of the metal strip also need to be carefully considered. The roll forming machine has certain limitations in terms of the maximum thickness and width of the strip it can handle. Thicker strips may require more powerful roll forming machines and higher forming pressures, while wider strips may pose challenges in terms of maintaining consistent shape and alignment during the forming process. Understanding these limitations and working within them is key to achieving successful roll - formed tubes.
Machine Setup and Maintenance
1. Proper Setup for Different Tube Shapes
Setting up the roll forming machine correctly is essential for producing high - quality tubes. The rolls need to be precisely aligned and adjusted according to the specific tube shape and dimensions. This requires skilled operators who understand the mechanics of the roll forming process. Incorrect setup can lead to a variety of defects in the tubes, such as uneven bends, misaligned edges, or inconsistent wall thickness.
2. Regular Maintenance for Optimal Performance
Regular maintenance of the roll forming machine is necessary to ensure its long - term and optimal performance. This includes tasks such as lubricating the moving parts, inspecting and replacing worn - out rolls, and checking the alignment of the machine components. Well - maintained machines are less likely to experience breakdowns during production, which can disrupt the manufacturing process and increase costs.
Quality Control
1. In - Process Inspection
Implementing in - process inspection is crucial for detecting and correcting any defects early in the roll forming tube production process. This can include visual inspection of the tube as it is being formed, checking for any signs of surface defects, such as scratches or dents, and ensuring that the tube's shape and dimensions are within the specified tolerances. In - line sensors can also be used to monitor parameters such as wall thickness and weld quality in real - time.
2. Final Product Testing
After the tubes are fully formed and finished, they should undergo comprehensive final product testing. This can include mechanical testing, such as tensile strength and bend testing, to ensure that the tubes meet the required performance standards. Non - destructive testing methods, as mentioned earlier, are also used to detect any internal defects that may not be visible to the naked eye. Only tubes that pass these rigorous quality control tests should be released for use in various applications.
Conclusion
Roll forming tube is a versatile, efficient, and cost - effective manufacturing process with a wide range of applications across multiple industries. Its ability to produce high - quality tubes with precision and consistency, combined with its high - volume production capabilities, makes it a preferred choice for many manufacturers. By understanding the roll forming tube process, its applications, advantages, and key considerations, companies can make informed decisions when implementing this technology in their manufacturing operations. As technology continues to advance, the roll forming tube process is likely to see further improvements in terms of speed, precision, and the ability to work with new and advanced materials, opening up even more opportunities for innovation and growth in various industries.