Hotline
+86-136 8495 9862
Email:cennia@szmizhi.com
Add::104,Building 27,Third Industrial Zone, Longxi Community,Longgang District,Shenzhen,China.
Coil Forming & Handling Equipment
Surface Treatment Equipment
Solutions
Application
About Us
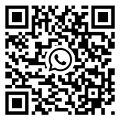
Welcome to MIZHI
For consultation/feedback, please call the service hotline: +86-136 8495 9862 Email:cennia@szmizhi.com
1. Introduction
In the vast and intricate world of manufacturing, roll forming tube has emerged as a fundamental and highly efficient method for producing tubular structures. Tubes are used in a multitude of applications across various industries, from construction and automotive to aerospace and plumbing. Roll forming, as a continuous manufacturing process, offers unique advantages in transforming flat - rolled metal sheets into seamless and precisely shaped tubes. This article delves deep into the roll - forming tube process, covering its components, working principles, applications, advantages, challenges, and future trends.
2. Components of a Roll - Forming Tube Machine
2.1 Uncoiler
The uncoiler serves as the starting point of the roll - forming tube production line. It is designed to hold and unwind the large roll of flat - rolled metal sheet, which is the raw material for tube formation. Uncoilers are typically equipped with expandable mandrels, often hydraulically or pneumatically operated. This allows them to accommodate different inner diameters of the metal coils. For example, in a large - scale steel tube manufacturing plant, the uncoiler needs to handle coils of various sizes, from small - diameter coils for thin - walled tubes used in the furniture industry to large - diameter coils for heavy - duty structural tubes in construction. The uncoiler is also equipped with a tension - control system. Maintaining consistent tension during the unwinding process is crucial. If the tension is too low, the metal sheet may sag, leading to misalignment during the roll - forming process. Conversely, excessive tension can cause the sheet to stretch or even tear, especially when dealing with brittle or thin - gauge materials.
2.2 Leveler
After unwinding, the flat - rolled metal sheet often has some curvature and unevenness due to the coiling process. The leveler is responsible for straightening the sheet to ensure a uniform starting point for tube formation. It consists of multiple rolls, usually made of hardened steel to withstand the forces exerted during the leveling process. The number of rolls can vary depending on the thickness and material of the metal sheet. For thinner materials like aluminum sheets used in the production of small - diameter tubes for heat exchangers, a 7 - roll leveler might be sufficient. However, for thicker steel sheets intended for large - diameter structural tubes, a 21 - roll leveler may be required. The leveler works by applying a combination of bending and stretching forces to the sheet, gradually eliminating any waves, curls, or bowing. Some advanced levelers have adjustable roll - gap settings, enabling operators to fine - tune the leveling process according to the specific characteristics of the metal sheet, such as its hardness and thickness.
2.3 Roll - Forming Stations
The roll - forming stations are the core components of the roll - forming tube machine. These stations are a series of paired rolls, each with a specific profile designed to gradually shape the flat - rolled metal sheet into a tubular structure. The number of roll - forming stations can range from a few for simple tube shapes to over a dozen for complex profiles. As the metal sheet progresses through the stations, each set of rolls makes incremental changes to the shape. For example, in the initial stations, the sheet may be gradually bent into a U - shape, and as it moves further, it is formed into a more circular or rectangular tubular shape. The rolls in the roll - forming stations are made of high - quality alloy steel, hardened and polished to ensure smooth and accurate shaping. They are also designed to withstand the significant forces required to deform the metal into the desired tube shape.
2.4 Welding Unit (for Seamless - like Tubes)
For some applications, seamless - like tubes are required. In such cases, a welding unit is an essential part of the roll - forming tube machine. After the metal sheet has been formed into a tubular shape, the edges need to be joined together. Resistance welding or high - frequency induction welding is commonly used. In resistance welding, an electric current is passed through the overlapping edges of the tube, generating heat that fuses the metal together. High - frequency induction welding, on the other hand, uses an electromagnetic field to heat the edges of the tube, achieving a strong and seamless - looking weld. The welding unit must be precisely calibrated to ensure a consistent and high - quality weld. Parameters such as welding current, voltage, and speed need to be carefully controlled to prevent issues like weak welds, over - welding, or porosity in the weld joint.
2.5 Sizing and Straightening Unit
Once the tube is formed and welded (if applicable), it may have some dimensional variations or minor bends. The sizing and straightening unit is used to ensure that the tube meets the required dimensional tolerances and is straight. This unit typically consists of a series of rolls that apply gentle pressure to the tube, adjusting its diameter and straightening any curvature. The rolls in the sizing and straightening unit can be adjusted to accommodate different tube sizes and shapes. For example, in the production of precision - engineered tubes for the automotive industry, the sizing and straightening unit plays a crucial role in ensuring that the tubes fit perfectly into the vehicle's frame or engine components.
2.6 Cut - off Unit
The cut - off unit is responsible for cutting the continuous roll - formed tube into individual lengths. There are different types of cut - off methods, with mechanical shearing and flying cut - off being the most common. Mechanical shearing uses sharp blades to cut the tube. This method is suitable for most standard applications and can handle a wide range of tube thicknesses. Flying cut - off, on the other hand, is used when high - speed production is required. In a flying cut - off system, the cutting tool moves in synchronization with the moving tube, allowing for continuous cutting without stopping the production line. This is especially useful in large - scale manufacturing plants that produce tubes in high volumes, such as those for the construction or plumbing industries.
2.7 Control System
The control system of a roll - forming tube machine is like the brain of the entire operation. It coordinates the functions of all the components, ensuring smooth and efficient production. The control system can be based on programmable logic controllers (PLCs) or more advanced computer - numerical - control (CNC) systems. These systems allow operators to set various parameters, such as the speed of the roll - forming process, the tension levels for unwinding, the roll - gap settings in the leveler and roll - forming stations, the welding parameters (if applicable), and the length of the cut - off tubes. The control system also provides real - time monitoring of the production process. It can detect any abnormal conditions, such as over - tension, misalignment of the rolls, welding defects, or cutting - tool wear, and take immediate corrective actions. Some modern control systems are also equipped with remote - monitoring capabilities, allowing plant managers to monitor the operation of the roll - forming tube machine from a central control room or even remotely via the internet.
3. Working Principle
The operation of a roll - forming tube machine is a highly coordinated and sequential process.
1. Unwinding: The metal coil is loaded onto the uncoiler. The mandrel of the uncoiler is expanded to grip the inner core of the coil firmly. The control system then activates the uncoiler motor, which starts to unwind the metal sheet at a controlled speed. The tension - control system continuously monitors and adjusts the tension of the sheet to ensure a smooth unwinding operation.
2. Leveling: As the unwound metal sheet enters the leveler, it passes through the series of rolls. The rolls apply a combination of bending and stretching forces to the sheet, gradually straightening it. The operator can adjust the roll - gap settings based on the thickness and material of the sheet to achieve the best leveling results. The leveling process is crucial as it ensures that the sheet is flat and uniform before entering the roll - forming stations, which is essential for accurate tube formation.
3. Roll - Forming: After the sheet is leveled, it enters the roll - forming stations. The paired rolls in each station gradually shape the metal sheet into a tubular structure. The sheet progresses through the stations, with each set of rolls making incremental changes to the shape. The process is continuous, and the speed of the roll - forming can be adjusted according to the complexity of the tube shape and the thickness of the metal.
4. Welding (if applicable): If a seamless - like tube is required, the formed tube then enters the welding unit. The overlapping edges of the tube are heated and fused together using either resistance welding or high - frequency induction welding. The welding parameters are carefully controlled to ensure a strong and high - quality weld.
5. Sizing and Straightening: Once the tube is formed and welded (if applicable), it passes through the sizing and straightening unit. The rolls in this unit apply gentle pressure to the tube, adjusting its diameter and straightening any curvature. This ensures that the tube meets the required dimensional tolerances.
6. Cut - off: Finally, the continuous roll - formed tube reaches the cut - off unit. The tube is cut into individual lengths according to the pre - set specifications. The cut - off method, whether mechanical shearing or flying cut - off, is determined by the production requirements.
4. Applications
4.1 Construction Industry
In the construction industry, roll - formed tubes are used extensively. Structural tubes, such as square and rectangular hollow sections, are commonly used in building frames, bridges, and industrial sheds. These tubes provide high strength - to - weight ratios, making them ideal for supporting heavy loads while keeping the overall weight of the structure in check. For example, in high - rise buildings, roll - formed steel tubes are used in the construction of the main structural columns and beams. They are also used for the construction of scaffolding, which needs to be strong, lightweight, and easy to assemble and disassemble. In addition, roll - formed tubes are used for the installation of plumbing and electrical systems within buildings. The precise dimensions and smooth inner surfaces of the tubes ensure efficient flow of water and easy installation of electrical conduits.
4.2 Automotive Industry
The automotive industry relies heavily on roll - formed tubes for various components. Exhaust systems are a prime example. Roll - formed steel tubes are used to create the complex shapes required for exhaust pipes, mufflers, and catalytic converters. The ability to form tubes with precise bends and diameters allows for optimal exhaust flow, reducing back - pressure and improving engine performance. In addition, roll - formed tubes are used in the construction of the vehicle's frame and suspension components. These tubes provide the necessary strength and rigidity while also helping to reduce the overall weight of the vehicle, which in turn improves fuel efficiency. For example, in modern lightweight vehicle designs, aluminum roll - formed tubes are increasingly being used in the chassis and suspension systems.
4.3 Aerospace Industry
The aerospace industry has strict requirements for materials and component quality. Roll - formed tubes play a crucial role in aircraft construction. Tubes are used in the aircraft's structural framework, such as the fuselage and wing spars. The high strength - to - weight ratio of roll - formed tubes, especially those made from advanced alloys like titanium and high - strength aluminum, is essential for reducing the weight of the aircraft while maintaining its structural integrity. In addition, roll - formed tubes are used in the aircraft's fuel and hydraulic systems. The precise dimensions and seamless - like construction (when welded) ensure reliable and leak - free operation, which is critical for the safety and performance of the aircraft.
4.4 Manufacturing and Industrial Equipment
In the manufacturing of industrial equipment, roll - formed tubes are used in a wide range of applications. Conveyor systems, for example, often use roll - formed tubes as the framework and support structures. The tubes can be easily customized to fit the specific requirements of the conveyor, such as length, diameter, and load - bearing capacity. Roll - formed tubes are also used in the production of agricultural machinery, such as tractors and combine harvesters. These tubes are used for the construction of the machine's frame, axles, and hydraulic systems. In the manufacturing of heavy - duty industrial machinery, such as cranes and excavators, roll - formed tubes provide the necessary strength and durability to withstand the harsh operating conditions.
5. Advantages
5.1 High - Precision Tube Production
One of the most significant advantages of roll - forming tube is its ability to achieve high - precision tube manufacturing. The roll - forming process can produce tubes with very tight dimensional tolerances, ensuring a perfect fit and consistent quality. In industries where precision is crucial, such as aerospace and automotive, this is essential. For example, in the production of aircraft components, the precise dimensions of the roll - formed tubes ensure proper assembly and optimal performance. The smooth inner and outer surfaces of the roll - formed tubes also contribute to their high quality, reducing friction and improving the flow of fluids or gases in applications such as plumbing and exhaust systems.
5.2 High - Volume and Continuous Production
Roll - forming is a continuous process, making it highly suitable for high - volume production. Once the roll - forming tube machine is set up, it can produce a large number of tubes in a short period. This is beneficial for industries with high - demand products, such as the construction and automotive industries. In a large - scale construction - materials manufacturing plant, a roll - forming tube machine can produce hundreds or even thousands of meters of tubes per day. The continuous production process also reduces the need for frequent stops and starts, which improves overall productivity and reduces production costs.
5.3 Material Efficiency
Roll - forming tube is a material - efficient process. Since the process is continuous and the shaping is gradual, there is minimal waste of metal material. The ability to produce tubes with the exact dimensions required reduces the need for additional machining or trimming, resulting in cost savings. In addition, the use of roll - forming allows for the efficient use of materials with different thicknesses and strengths, enabling manufacturers to optimize the material selection based on the specific requirements of the application. For example, in the production of lightweight automotive components, roll - formed aluminum tubes can be designed to use the minimum amount of material while still meeting the required strength and performance criteria.
5.4 Design Flexibility
Roll - forming offers a high degree of design flexibility. The shape of the roll - formed tubes can be easily customized by changing the profile of the rolls. This allows manufacturers to produce tubes with a wide range of cross - sectional shapes, from simple circular and rectangular to complex multi - sided profiles. In addition, the ability to create precise bends and curves in the tubes during the roll - forming process further expands the design possibilities. This design flexibility is particularly useful in industries such as automotive and aerospace, where components often need to be customized to fit specific design requirements.
6. Challenges
6.1 High Initial Investment
The purchase and installation of a roll - forming tube machine can be a substantial capital investment. The cost of the machine, including all its components such as the uncoiler, leveler, roll - forming stations, welding unit (if applicable), sizing and straightening unit, cut - off unit, and control system, can range from hundreds of thousands to several million dollars, depending on its size, capabilities, and the level of automation. In addition, there are costs associated with infrastructure development, such as a suitable workshop space with proper ventilation, electrical systems to power the machine, and safety measures. Small and medium - sized enterprises may find it difficult to afford such high - cost equipment, which can limit their growth and competitiveness in the market.
6.2 Tooling and Setup Complexity
Changing the product design or the cross - sectional profile of the roll - formed tubes requires changing the rolls in the roll - forming stations. This process, known as tooling, can be time - consuming and costly. The rolls need to be carefully designed, manufactured, and installed, and the machine needs to be re - calibrated. In addition, the setup time for a new production run can be significant, especially for complex tube shapes. This can reduce the overall productivity of the roll - forming tube machine, especially for small - batch production. The complexity of tooling and setup also requires skilled technicians who are familiar with the roll - forming process and the operation of the machine.
6.3 Material Compatibility and Quality Control
Different metals and alloys have different properties, and ensuring that the roll - forming process is compatible with the specific material being used is crucial. Some materials may be more difficult to form than others, and they may require special considerations in terms of roll - design, lubrication, and process parameters. For example, forming tubes from high - strength alloys may require more powerful roll - forming machines and specialized lubricants to prevent cracking or excessive wear on the rolls. Quality control is also a challenge, as any variations in the metal material, such as differences in thickness, hardness, or chemical composition, can affect the roll - forming process and the quality of the final product. Implementing effective quality - control measures, such as regular inspections, in - line monitoring, and statistical process control, is essential but can be resource - intensive.
6.4 Skilled Labor Requirement
Operating and maintaining a roll - forming tube machine requires a high level of technical expertise. Workers need to be trained in setting up the machine, programming the control system, adjusting the roll - gap settings, monitoring and controlling the welding process (if applicable), and troubleshooting any issues that may arise during operation. The shortage of skilled labor in some regions can pose a challenge to the efficient use of these machines. Employers may need to invest in comprehensive training programs or hire experienced technicians, which can add to the overall operational costs.
7. Future Trends
7.1 Integration of Industry 4.0 Technologies
The future of roll - forming tube lies in the integration of Industry 4.0 technologies, such as the Internet of Things (IoT), artificial intelligence (AI), and machine learning (ML). IoT sensors can be installed on the roll - forming tube machine to monitor various parameters, such as temperature, vibration, roll - wear, and material properties, in real - time. This data can be transmitted to a central control system, where AI and ML algorithms can analyze it to predict equipment failures, optimize the roll - forming process, and improve overall efficiency. For example, AI can adjust the roll - gap settings, the speed of the roll - forming process, and the welding parameters based on the real - time condition of the metal sheet and the rolls, reducing the risk of defects and improving the quality of the final product.
7.2 Development of Advanced Materials and Roll - Forming Techniques
As new and more advanced materials are developed, roll - forming techniques will need to be adapted to handle these materials. For example, the use of advanced high - strength steels, lightweight alloys, and composite materials in tube production will require the development of new roll - design concepts and process parameters. In addition, new roll - forming techniques, such as multi - pass roll - forming with variable roll - speeds and hydro - roll - forming (a combination of roll - forming and hydroforming), may be developed to further enhance the capabilities of roll - forming tube. These new techniques can enable the production of tubes with more complex shapes and improved mechanical properties.