Hotline
+86-136 8495 9862
Email:cennia@szmizhi.com
Add::104,Building 27,Third Industrial Zone, Longxi Community,Longgang District,Shenzhen,China.
Coil Forming & Handling Equipment
Surface Treatment Equipment
Solutions
Application
About Us
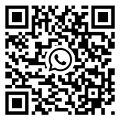
Welcome to MIZHI
For consultation/feedback, please call the service hotline: +86-136 8495 9862 Email:cennia@szmizhi.com
1. Introduction
In the realm of construction, the roof is not only a fundamental structural element but also a crucial component that safeguards the interior of a building from the elements. Roof panel machines have emerged as essential tools in the production of high quality roof panels, which are widely used in residential, commercial, and industrial buildings. These machines play a pivotal role in transforming raw metal materials into precisely shaped, durable, and aesthetically pleasing roof panels. This comprehensive exploration will cover every aspect of roof panel machines, including their components, working principles, applications, advantages, challenges, and future trends.
2. Components of a Roof Panel Machine
2.1 Uncoiler
The uncoiler serves as the starting point of the roof panel production process. It is designed to hold and unwind large rolls of metal sheets, which are the primary raw materials for manufacturing roof panels. These metal sheets can be made of various materials such as galvanized steel, aluminum, or copper, each with its own set of properties and applications. For instance, galvanized steel is popular due to its high strength and corrosion resistance, making it suitable for a wide range of roofing applications. Uncoilers are typically equipped with expandable mandrels, which can be adjusted to fit different inner diameters of the metal coils. This adaptability allows the machine to handle coils of varying sizes, from small scale residential roofing projects to large scale industrial ones.
The uncoiler is also equipped with a tension control system. Maintaining the right tension during the unwinding process is crucial. If the tension is too low, the metal sheet may sag, leading to misalignment during the subsequent panel forming process. Conversely, excessive tension can cause the sheet to stretch or even tear, especially when dealing with thin gauge materials. In a large scale manufacturing facility that produces roof panels for multiple construction sites, a well functioning uncoiler ensures a smooth and continuous supply of metal sheets for the roof panel machine.
2.2 Leveler
After the metal sheet is unwound, it often has some curvature and unevenness due to the coiling process. The leveler is responsible for straightening the sheet to provide a flat and uniform base for the panel forming process. It consists of multiple rolls, usually made of hardened steel to withstand the forces exerted during leveling. The number of rolls can vary depending on the thickness and material of the metal. For thinner aluminum sheets used in some residential roofing applications, a 7 roll leveler might be sufficient. However, for thicker steel sheets used in industrial buildings, a 21 roll leveler could be required.
The leveler works by applying a combination of bending and stretching forces to the sheet. As the metal sheet passes through the rolls, the rolls gradually eliminate any waves, curls, or bowing. Some advanced levelers have adjustable roll gap settings. This feature allows operators to fine tune the leveling process according to the specific characteristics of the metal sheet, such as its hardness and thickness. Precise leveling is essential as it ensures that the metal sheet is in the optimal condition for accurate panel formation.
2.3 Roll Forming Stations
The roll forming stations are the core of the roof panel machine. These stations are a series of paired rolls, each with a specific profile. As the metal sheet progresses through these stations, the rolls gradually shape it into the desired roof panel profile. The number of roll forming stations can range from 5 6 for simple panel profiles to 20 or more for complex designs. For example, a basic trapezoidal roof panel may require fewer stations, while a standing seam roof panel, which has a more intricate design with interlocking seams, needs more stations for proper formation.
The rolls in the roll forming stations are made of high quality alloy steel, hardened and polished to ensure smooth and accurate shaping. They are designed to withstand the significant forces required to deform the metal into the roofing panel profile. The profile of each roll is carefully engineered to create the specific shape, such as the corrugations, ribs, or seams, that are characteristic of the roof panel.
2.4 Cut off Unit
Once the metal sheet has been roll formed into the roof panel profile, it needs to be cut into individual lengths. The cut off unit is responsible for this task. There are two main types of cut off methods: mechanical shearing and flying cut off. Mechanical shearing uses sharp blades to cut the roll formed metal. This method is suitable for most standard applications and can handle a wide range of metal thicknesses. It is often used in small to medium scale production, where the speed of cutting is not the primary concern.
Flying cut off, on the other hand, is used when high speed production is required. In a flying cut off system, the cutting tool moves in synchronization with the moving roll formed metal, allowing for continuous cutting without stopping the production line. This is especially useful in large scale manufacturing plants that produce roof panels in high volumes. The cut off unit is precisely calibrated to ensure that the cut lengths are accurate, meeting the specific requirements of the construction project.
2.5 Control System
The control system of a roof panel machine is like the brain of the entire operation. It coordinates the functions of all the components, ensuring smooth and efficient production. The control system can be based on programmable logic controllers (PLCs) or more advanced computer numerical control (CNC) systems. These systems allow operators to set various parameters, such as the speed of the roll forming process, the tension levels for unwinding, the roll gap settings in the leveler and roll forming stations, and the length of the cut off panels.
The control system also provides real time monitoring of the production process. It can detect any abnormal conditions, such as over tension, misalignment of the rolls, or cutting tool wear, and take immediate corrective actions. Some modern control systems are also equipped with remote monitoring capabilities, allowing plant managers to monitor the operation of the roof panel machine from a central control room or even remotely via the internet. This enables quick response to any issues, minimizing production downtime.
3. Working Principle
The operation of a roof panel machine is a highly coordinated and sequential process.
1. Unwinding: The metal coil is loaded onto the uncoiler. The mandrel of the uncoiler is expanded to grip the inner core of the coil firmly. The control system then activates the uncoiler motor, which starts to unwind the metal sheet at a controlled speed. The tension control system continuously monitors and adjusts the tension of the sheet to ensure a smooth unwinding operation.
2. Leveling: As the unwound metal sheet enters the leveler, it passes through the series of rolls. The rolls apply a combination of bending and stretching forces to the sheet, gradually straightening it. The operator can adjust the roll gap settings based on the thickness and material of the sheet to achieve the best leveling results. The leveling process is crucial as it ensures that the sheet is flat and uniform before entering the roll forming stations, which is essential for accurate panel formation.
3. Roll Forming: After the sheet is leveled, it enters the roll forming stations. The paired rolls in each station gradually shape the metal sheet into the desired roof panel profile. The sheet progresses through the stations, with each set of rolls making incremental changes to the shape. The process is continuous, and the speed of the roll forming can be adjusted according to the complexity of the profile and the thickness of the metal.
4. Cut off: Once the roll formed metal reaches the cut off unit, it is cut into the desired lengths. The cut off method, whether mechanical shearing or flying cut off, is determined by the production requirements. The control system ensures that the cutting is precise and synchronized with the roll forming process.
4. Applications
4.1 Residential Construction
In residential construction, roof panel machines are used to produce a variety of roof panel types. Standing seam metal roof panels are a popular choice for homeowners due to their sleek appearance, excellent water resistance, and durability. The roof panel machine can precisely form the interlocking seams that are characteristic of standing seam roofs. These seams not only provide a watertight seal but also add to the aesthetic appeal of the roof.
Corrugated metal roof panels are also widely used in residential projects, especially in more rustic or budget conscious settings. The machine can produce corrugated panels with the right pitch and wave height to provide a cost effective and durable roofing solution. In addition, some roof panel machines can produce insulated roof panels, which are becoming increasingly popular in residential construction due to their energy efficiency benefits. These panels can help reduce heating and cooling costs by providing better thermal insulation.
4.2 Commercial Construction
Commercial buildings, such as office buildings, warehouses, and retail stores, often require large scale roofing solutions. Roof panel machines can produce long length panels, which are ideal for covering large roof areas. The high strength and durability of the panels produced by these machines make them suitable for commercial applications, where the roof needs to withstand heavy snow loads, strong winds, and other environmental factors.
For example, in the construction of a large scale warehouse, the use of a roof panel machine can significantly speed up the roofing process. The machine can produce panels that are custom sized to fit the specific dimensions of the warehouse roof, reducing the need for on site cutting and fitting. In addition, the smooth and uniform finish of the panels produced by the machine enhances the overall appearance of the commercial building.
4.3 Industrial Construction
Industrial buildings, such as factories and manufacturing plants, have unique roofing requirements. Roof panel machines can produce panels that are designed to handle the specific needs of industrial environments. For example, in a factory where there may be chemical emissions or high humidity levels, corrosion resistant metal roof panels, such as those made of aluminum or galvanized steel with special coatings, can be produced.
The machines can also create panels with special features, such as built in ventilation systems or skylight openings. These features are essential for industrial buildings, where proper ventilation and natural light are crucial for the health and productivity of the workers. The durability of the roof panels in industrial settings is crucial, as any roof damage can lead to costly production disruptions.
4.4 Agricultural Buildings
In the agricultural sector, roof panel machines are used to produce roofing for barns, sheds, and other agricultural structures. Metal roof panels are popular in agricultural buildings because they are low maintenance, durable, and can withstand the harsh outdoor conditions. The machines can produce panels that are suitable for different agricultural applications.
For example, in a dairy barn, the roofing may need to be designed to allow for proper ventilation to keep the animals comfortable. Roof panel machines can create panels with ventilation features, such as ridge vents or louvers. In addition, the panels can be produced in colors and finishes that blend in with the rural environment, enhancing the overall aesthetic of the agricultural property.
5. Advantages
5.1 High Precision Manufacturing
Roof panel machines are capable of producing roof panels with high precision. The roll forming process can achieve tight tolerances, ensuring that the panels fit together perfectly during installation. This precision is crucial for the water tightness and overall integrity of the roof. In the case of standing seam metal roofs, the precise formation of the seams ensures that there are no leaks, even in extreme weather conditions. The smooth and consistent profiles produced by the machines also contribute to the aesthetic appeal of the roof.
5.2 High Volume Production
These machines are designed for high volume production. Once set up, they can produce a large number of roof panels in a short period. This is beneficial for large scale construction projects, where a significant amount of roofing material is required. In a large scale commercial or industrial construction project, a roof panel machine can produce hundreds or even thousands of linear feet of roof panels per day, meeting the tight construction schedules. The continuous production process also reduces the cost per unit, making roof panels more cost effective in large quantities.
5.3 Material Versatility
Roof panel machines can work with a variety of metal materials. Steel, aluminum, and copper are commonly used, each with its own advantages. Steel is strong and cost effective, making it suitable for large scale industrial and commercial applications. Aluminum is lightweight and corrosion resistant, making it a popular choice for residential and coastal area buildings. Copper has a unique aesthetic appeal and excellent durability, often used in high end residential and historical building restorations. The ability to work with different materials allows construction companies to offer a wide range of roofing options to their clients.
5.4 Cost Efficiency in the Long Run
Although the initial investment in a roof panel machine can be significant, it offers long term cost efficiency. Metal roof panels have a long lifespan, often lasting 30 50 years or more with proper maintenance. This reduces the need for frequent roof replacements, saving on labor and material costs over time. In addition, the energy efficiency of some metal roof panels, especially those with insulation features, can lead to lower heating and cooling costs, further contributing to the long term cost savings. The high volume production capabilities of the machines also reduce the per unit production cost, making metal roof panels a cost effective choice for large scale projects.
6. Challenges
6.1 High Initial Investment
The purchase and installation of a roof panel machine represent a substantial capital investment. The cost of the machine, including the uncoiler, leveler, roll forming stations, cut off unit, and control system, can range from hundreds of thousands to several million dollars, depending on its size, capabilities, and the level of automation. In addition, there are costs associated with infrastructure development, such as a suitable workshop space with proper ventilation, electrical systems to power the machine, and safety measures. Small and medium sized construction companies may find it difficult to afford such high cost equipment, which can limit their ability to offer metal roof panel production services and compete in the market.
6.2 Maintenance and Calibration
To ensure the continued high precision and efficient operation of the roof panel machine, regular maintenance and calibration are essential. The roll forming stations, in particular, require maintenance due to the wear and tear caused by the constant shaping of the metal. The rolls need to be periodically inspected, and if necessary, replaced or re polished. The cutting blades in the cut off unit also need to be sharpened or replaced regularly. Calibration of the measuring and control systems is crucial to ensure accurate panel formation and cutting lengths. Any deviation in calibration can lead to inaccurate roof panels, resulting in installation problems and potential leaks. Maintenance and calibration require skilled technicians and can be time consuming and costly.
6.3 Skilled Labor Requirement
Operating a roof panel machine effectively requires a high level of technical expertise. Workers need to be trained in setting up the machine, programming the control system, adjusting the roll gap settings, and troubleshooting any issues that may arise during operation. The shortage of skilled labor in some regions can pose a challenge to the efficient use of these machines. Employers may need to invest in comprehensive training programs or hire experienced technicians, which can add to the overall operational costs. In addition, the complexity of the machine means that new operators may take some time to become proficient, further affecting productivity.
6.4 Competition from Other Roofing Materials
Despite the many advantages of metal roof panels, they face competition from other roofing materials such as asphalt shingles, tile, and synthetic roofing materials. Asphalt shingles are a popular choice for residential roofing due to their lower initial cost and ease of installation. Tile roofs are often preferred for their aesthetic appeal in certain architectural styles. Synthetic roofing materials, such as rubber based or plastic based products, are also emerging as alternatives. Metal roof panel manufacturers and construction companies need to continuously promote the long term benefits of metal roofing, such as its durability and energy efficiency, to overcome this competition.
7. Future Trends
7.1 Integration of Smart Technologies
The future of roof panel machines lies in the integration of smart technologies. Internet of Things (IoT) sensors can be installed on the machine to monitor various parameters, such as temperature, vibration, and roll wear, in real time. This data can be used to predict maintenance needs and optimize the production process. For example, if the sensors detect excessive roll wear, the machine can be adjusted or the rolls can be replaced before it affects the quality of the roof panels. Artificial intelligence (AI) and machine learning (ML) algorithms can also be applied to analyze the production data and make real time adjustments to the machine settings, improving efficiency and reducing waste.
7.2 Development of Sustainable and Energy Efficient Solutions
As environmental concerns become more prominent, there will be a growing focus on developing sustainable and energy efficient roof panel solutions. This may involve the use of recycled metal materials in the production of roof panels. In addition, roof panel machines may be designed to produce panels with better insulation properties, further enhancing the energy efficiency of buildings. For example, new roll forming techniques may be developed to create roof panels with integrated insulation layers. The use of energy efficient motors and control systems in the roof panel machines themselves will also contribute to reducing the overall energy consumption of the production process.
7.3 Customization and Aesthetic Innovation
In response to the increasing demand for unique and personalized building designs, roof panel machines will likely become more customizable. Manufacturers will be able to produce roof panels with more complex shapes and designs, allowing for greater aesthetic innovation. This may involve the development of new roll forming tools and techniques to create custom designed roof panels. In addition, the use of advanced coating technologies will enable the production of roof panels with a wider range of colors and finishes, further enhancing the visual appeal of buildings.
In conclusion, the roof panel machine is an indispensable tool in the construction industry. Its components, working principle, wide ranging applications, numerous advantages, and the challenges it faces all contribute to its significance in modern building construction. With the advent of new technologies and the evolving demands of the construction market, the roof panel machine is set to undergo further advancements, continuing to play a crucial role in providing high quality roofing solutions for a variety of building types.