Hotline
+86-136 8495 9862
Email:cennia@szmizhi.com
Add::104,Building 27,Third Industrial Zone, Longxi Community,Longgang District,Shenzhen,China.
Coil Forming & Handling Equipment
Surface Treatment Equipment
Solutions
Application
About Us
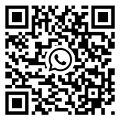
Welcome to MIZHI
For consultation/feedback, please call the service hotline: +86-136 8495 9862 Email:cennia@szmizhi.com
The roof sheet roll forming machine is an essential piece of equipment in the construction and manufacturing industries. It is designed to transform flat metal coils, typically made of steel, aluminum, or other alloys, into precisely shaped roof sheets. These roof sheets are widely used in residential, commercial, and industrial buildings due to their durability, cost - effectiveness, and ease of installation. This article will delve into various aspects of roof sheet roll forming machines, including their working principle, types, applications, advantages, and key considerations when choosing a machine.
Working Principle of Roof Sheet Roll Forming Machines
1. Material Feeding
The process begins with the feeding of a flat metal coil into the roll forming machine. The coil is mounted on a pay - off reel, which is designed to unwind the metal strip at a controlled rate. Advanced machines are equipped with automatic coil loading systems that can handle coils of different weights and diameters. These systems ensure smooth and continuous feeding of the material, minimizing any disruptions in the production process.
For example, in a high - volume production facility, a hydraulic - powered pay - off reel can be adjusted to precisely control the tension of the metal strip as it is fed into the machine. This is crucial as improper tension can lead to defects in the formed roof sheets, such as wrinkles or uneven bends.
2. Roll Forming Process
Once the metal strip is fed into the machine, it passes through a series of forming rollers. These rollers are carefully designed and arranged in a specific sequence to gradually shape the flat metal into the desired roof sheet profile. Each set of rollers imparts a small incremental deformation to the metal, working in harmony to create the final shape.
The number of forming stations in a roof sheet roll forming machine can vary depending on the complexity of the profile. A simple corrugated roof sheet may require only 6 - 8 forming stations, while a more intricate standing - seam roof sheet could need 12 - 15 stations. The rollers are typically made of high - quality steel or alloy materials to withstand the high pressures and frictional forces during the forming process.
In addition, the rollers can be customized with different profiles to produce various types of roof sheets, such as trapezoidal, sinusoidal, or ribbed profiles. Computer - aided design (CAD) and computer - aided manufacturing (CAM) technologies are often used to ensure the precise machining of the rollers, resulting in consistent and accurate roof sheet profiles.
3. Cutting and Finishing
After the metal strip has been formed into the desired roof sheet profile, it needs to be cut to the required length. Roof sheet roll forming machines are equipped with cutting mechanisms, which can be either mechanical (such as a flying shear) or hydraulic. A flying shear is a common choice as it can cut the moving formed sheet without stopping the production line, thereby increasing production efficiency.
Once cut, the roof sheets may undergo additional finishing operations, such as edge trimming, hole punching (for fastening purposes), or surface coating. Some machines are integrated with in - line coating systems that can apply protective coatings, such as zinc - based or polymer - based coatings, to enhance the corrosion resistance and aesthetic appeal of the roof sheets.
Types of Roof Sheet Roll Forming Machines
1. Manual Roof Sheet Roll Forming Machines
Manual roof sheet roll forming machines are the simplest and most basic type. They are operated by hand, typically using a crank or a lever to rotate the forming rollers. These machines are relatively inexpensive and are suitable for small - scale production or for use in areas where electricity may not be readily available.
For instance, in a rural construction project or a small - scale metalworking workshop, a manual roof sheet roll forming machine can be used to produce a limited number of roof sheets. However, their production speed is slow, and the operator needs to have a certain level of skill to ensure consistent quality.
2. Semi - Automatic Roof Sheet Roll Forming Machines
Semi - automatic roof sheet roll forming machines incorporate some level of automation. They usually have an electric motor to drive the forming rollers, which significantly increases the production speed compared to manual machines. However, the feeding of the metal coil and the cutting of the formed sheets may still require some manual intervention.
These machines are often used by medium - sized construction companies or fabricators that need to produce a moderate volume of roof sheets. They offer a balance between cost and production efficiency, and can be easily operated with minimal training.
3. Fully Automatic Roof Sheet Roll Forming Machines
Fully automatic roof sheet roll forming machines are highly advanced and offer the highest level of production efficiency. They are equipped with automated coil loading, feeding, forming, cutting, and stacking systems. These machines can be programmed to produce roof sheets of different lengths and profiles with a high degree of accuracy.
In large - scale manufacturing plants, fully automatic roof sheet roll forming machines can operate continuously, producing hundreds of roof sheets per hour. They are often integrated with computer - controlled systems that monitor and adjust the production process in real - time to ensure consistent quality. Some of these machines also have the ability to detect and correct any defects in the formed sheets automatically.
Applications of Roof Sheet Roll Forming Machines
1. Residential Buildings
Roof sheet roll forming machines play a crucial role in the construction of residential buildings. The formed roof sheets are used for various types of residential roofing systems, such as pitched roofs and flat roofs. Corrugated or trapezoidal roof sheets are popular choices for residential applications due to their aesthetic appeal and good water - shedding properties.
In addition, the use of pre - formed roof sheets made by roll forming machines reduces the installation time and cost compared to traditional roofing methods. For example, in a suburban housing development, roof sheets produced by a roll forming machine can be quickly installed, allowing for faster completion of the construction project.
2. Commercial Buildings
Commercial buildings, such as warehouses, factories, and retail stores, also rely heavily on roof sheet roll forming machines. These buildings often require large - scale roofing solutions, and roll - formed roof sheets can be produced in long lengths to cover large areas efficiently. Standing - seam roof sheets, which are known for their high - end appearance and excellent weather - tightness, are commonly used in commercial buildings.
The durability of roll - formed roof sheets makes them suitable for commercial applications where long - term performance is essential. For instance, in a large - scale distribution center, the roof sheets need to withstand heavy snow loads, strong winds, and exposure to various weather conditions over an extended period.
3. Industrial Buildings
Industrial buildings, including power plants, refineries, and manufacturing facilities, have specific roofing requirements. Roof sheet roll forming machines can produce specialized roof sheets that are resistant to corrosion, high temperatures, and chemical exposure. For example, in a chemical plant, roof sheets made of stainless steel or aluminum alloy can be produced using a roll forming machine to ensure protection against corrosive chemicals in the environment.
These industrial - grade roof sheets are also designed to provide high - strength and structural integrity to support the weight of equipment and to withstand the harsh operating conditions within industrial facilities.
Advantages of Using Roof Sheet Roll Forming Machines
1. High - Quality and Consistent Products
Roof sheet roll forming machines are capable of producing roof sheets with a high degree of precision and consistency. The use of well - designed rollers and automated control systems ensures that each roof sheet has the same shape, dimensions, and quality. This results in a more professional - looking and reliable roofing installation.
For example, in a large - scale roofing project, the consistent quality of the roof sheets produced by a roll forming machine ensures that the roof has a uniform appearance and performs well in terms of water - proofing and structural integrity.
2. Cost - Effectiveness
In the long run, using a roof sheet roll forming machine can be highly cost - effective. The ability to produce roof sheets in - house reduces the need to purchase pre - fabricated sheets from external suppliers, which can often be more expensive. Additionally, the high production speed of modern roll forming machines allows for economies of scale, further reducing the cost per unit.
For a construction company that undertakes multiple roofing projects, investing in a roll forming machine can lead to significant savings over time. The machine can also be used to produce customized roof sheets, eliminating the need to pay for expensive custom - made products from third - party manufacturers.
3. Versatility
Roof sheet roll forming machines are highly versatile. They can be used to produce a wide variety of roof sheet profiles, materials, and sizes. By simply changing the rollers and adjusting the machine settings, different types of roof sheets can be manufactured. This versatility makes roll forming machines suitable for a diverse range of construction projects, from small residential jobs to large - scale industrial developments.
For example, a fabricator can use the same roll forming machine to produce both corrugated roof sheets for a low - cost housing project and standing - seam roof sheets for a high - end commercial building, depending on the client's requirements.
Key Considerations When Choosing a Roof Sheet Roll Forming Machine
1. Production Capacity
Consider the volume of roof sheets you need to produce. If you are a large - scale manufacturer or a construction company with high - volume projects, you will require a roll forming machine with a high production capacity. Look for machines with fast operating speeds and the ability to handle large - diameter metal coils.
On the other hand, if you are a small - scale operator or work on projects with limited scope, a machine with a lower production capacity may be more suitable and cost - effective.
2. Profile Complexity
Evaluate the complexity of the roof sheet profiles you intend to produce. Some roll forming machines are better suited for simple profiles, while others are designed to handle more intricate shapes. If you plan to produce standing - seam or other complex profiles, ensure that the machine you choose has the appropriate number of forming stations and the ability to achieve the required precision.
3. Material Compatibility
Different roll forming machines are designed to work with specific types of materials. Make sure the machine you select can handle the metal alloys or materials you plan to use, such as steel, aluminum, or copper. Some machines may require additional modifications or specialized rollers to work with certain materials.
4. After - Sales Service and Support
Choose a supplier that offers good after - sales service and support. This includes the availability of spare parts, technical assistance for machine operation and maintenance, and training for your staff. A reliable supplier will be able to quickly respond to any issues that may arise with the roll forming machine, minimizing downtime and ensuring continuous production.
Conclusion
Roof sheet roll forming machines are an integral part of the construction and manufacturing industries. Their ability to produce high - quality, cost - effective, and versatile roof sheets makes them indispensable for a wide range of projects. By understanding their working principle, types, applications, advantages, and key considerations when choosing a machine, businesses can make informed decisions and invest in the right equipment to meet their production needs. As technology continues to advance, we can expect further improvements in the efficiency, precision, and versatility of roof sheet roll forming machines, driving innovation in the roofing industry.