Hotline
+86-136 8495 9862
Email:cennia@szmizhi.com
Add::104,Building 27,Third Industrial Zone, Longxi Community,Longgang District,Shenzhen,China.
Coil Forming & Handling Equipment
Surface Treatment Equipment
Solutions
Application
About Us
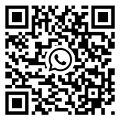
Welcome to MIZHI
For consultation/feedback, please call the service hotline: +86-136 8495 9862 Email:cennia@szmizhi.com
1. Introduction
In the construction industry, the roofing sheet machine holds a position of utmost importance. It is the key equipment that enables the transformation of raw metal or other sheet like materials into the final roofing products that protect buildings from the elements. The development of roofing sheet machines has been a game changer, revolutionizing the way roofs are constructed. These machines have evolved from simple, manually operated devices to highly automated and sophisticated systems, capable of producing a wide variety of roofing sheet profiles with high precision and efficiency. Whether it's for residential, commercial, or industrial buildings, the quality and performance of the roofing sheets produced by these machines directly impact the durability, energy efficiency, and aesthetic appeal of the structures.
2. Working Principle
2.1 Material Feeding
The operation of a roofing sheet machine commences with the material feeding stage. Typically, a large coil of metal sheet, such as galvanized steel, aluminum, or color coated steel, is loaded onto a decoiling unit. This unit is designed to unwind the coil smoothly and feed the sheet into the subsequent processing sections. The decoiling process is carefully controlled to ensure a consistent and even feed of the material. For example, in high end roofing sheet machines, advanced tension control systems are used to prevent the sheet from stretching or wrinkling during decoiling. These systems monitor the tension in the sheet and adjust the decoiling speed accordingly, maintaining optimal conditions for the forming process.
2.2 Forming Process
Once the sheet is fed into the machine, it enters the forming section. This is the heart of the roofing sheet machine, where the flat sheet is transformed into the desired roofing profile. The forming section consists of a series of roll forming stations. Each station has a set of rolls, and as the sheet passes through these rolls, it is gradually bent and shaped. The rolls are designed with specific curvatures and angles that correspond to the final profile of the roofing sheet. For instance, in the production of corrugated roofing sheets, the rolls are configured to create the characteristic wave like pattern. The number of roll forming stations can vary depending on the complexity of the profile. Simple profiles may require only a few stations, while more intricate designs, such as those with multiple bends and embossed features, may need a larger number of stations.
2.3 Cutting and Finishing
After the sheet is formed into the roofing profile, it needs to be cut into the required lengths. The cutting process is usually carried out using a high precision cutting device, such as a hydraulic or pneumatic guillotine cutter. The cutting mechanism is synchronized with the speed of the forming process to ensure that the sheets are cut accurately. In some advanced roofing sheet machines, computer controlled cutting systems are used, which can be programmed to cut the sheets into different lengths according to the specific requirements of the construction project.
Once cut, the roofing sheets may undergo additional finishing operations. This can include edge trimming to remove any rough edges, and in some cases, the application of coatings or sealants. For example, a protective coating may be applied to the roofing sheets to enhance their corrosion resistance and weather proofing capabilities. Some machines are also equipped to perform embossing or stamping operations, which can add decorative elements or brand markings to the sheets.
3. Types of Roofing Sheet Machines
3.1 Manual Roofing Sheet Machines
Manual roofing sheet machines are the most basic type of these machines. They are relatively simple in design and operation, and are often suitable for small scale roofing projects or for use in areas with limited resources. In a manual machine, the operator is responsible for most of the processes, such as feeding the material, controlling the forming process, and cutting the sheets. These machines typically have a lower production capacity compared to their automated counterparts. However, they are more affordable and can be a viable option for small scale roofing contractors or for DIY roofing projects. For example, a small scale roofing business in a rural area may use a manual roofing sheet machine to produce roofing sheets for local residential buildings.
3.2 Semi Automatic Roofing Sheet Machines
Semi automatic roofing sheet machines offer a step up in terms of automation. In these machines, some of the processes are automated, while others still require manual intervention. For example, the forming process may be automated, with the rolls being driven by electric motors, but the feeding of the material and the cutting of the sheets may still need to be done manually. Semi automatic machines are a good option for medium sized roofing contractors. They offer a balance between cost and productivity, allowing contractors to produce a larger volume of roofing sheets compared to manual machines, while still being relatively affordable. These machines are also easier to operate and maintain compared to fully automatic machines, making them suitable for businesses with limited technical expertise.
3.3 Fully Automatic Roofing Sheet Machines
Fully automatic roofing sheet machines are the pinnacle of roofing sheet manufacturing technology. These machines are equipped with advanced computer controlled systems that automate all aspects of the production process, from material feeding to cutting and finishing. The material is automatically fed from the decoiling unit into the forming section, and the forming and cutting processes are precisely controlled by the machine's control system. Fully automatic machines are capable of high speed production and can achieve a high degree of accuracy in the production of roofing sheets. They are ideal for large scale roofing projects, such as those in commercial and industrial construction. For example, a large scale industrial roofing project may require the production of a large number of roofing sheets in a short period. A fully automatic roofing sheet machine can meet this demand by producing sheets at a high rate while maintaining consistent quality.
4. Applications in the Construction Industry
4.1 Residential Roofing
In residential construction, roofing sheet machines play a crucial role in providing durable and aesthetically pleasing roofing solutions. Galvanized steel or color coated steel roofing sheets produced by these machines are popular choices for residential roofs. They offer excellent protection against rain, snow, and sunlight, and can last for many years with proper maintenance. The variety of profiles available, such as corrugated, trapezoidal, and standing seam, allows homeowners and architects to choose a roofing style that complements the overall design of the house. For example, a modern style house may feature standing seam roofing sheets, which give a sleek and contemporary look, while a traditional style house may be better suited with corrugated roofing sheets.
4.2 Commercial Roofing
Commercial buildings, such as offices, warehouses, and retail stores, also rely heavily on roofing sheet machines. These buildings often require large scale roofing solutions, and the high production capacity of roofing sheet machines makes them ideal for such projects. The use of high quality roofing sheets produced by these machines can improve the energy efficiency of commercial buildings. For example, some roofing sheets are designed with insulation properties, which can help to reduce the heating and cooling costs of the building. In addition, the durability of the roofing sheets is important for commercial buildings, as any roof leaks or damage can disrupt business operations and cause significant losses.
4.3 Industrial Roofing
Industrial buildings, such as factories and manufacturing plants, have unique roofing requirements. They often need roofing sheets that can withstand harsh environmental conditions, such as heavy industrial pollutants, extreme weather, and high temperature variations. Roofing sheet machines can produce sheets made from materials like stainless steel or aluminum zinc alloy, which offer excellent corrosion resistance and durability. These sheets can also be designed to meet the specific structural requirements of industrial buildings, such as the ability to support heavy equipment or to withstand high wind loads. For example, in a chemical factory, the roofing sheets need to be resistant to chemical corrosion, and the roofing sheet machine can produce sheets with appropriate coatings and materials to meet this requirement.
5. Advantages of Roofing Sheet Machines
4.1 High Quality and Consistent Products
Roofing sheet machines are capable of producing high quality roofing sheets with consistent dimensions and profiles. The precise roll forming and cutting processes ensure that each sheet meets the required standards. This consistency is important for the proper installation of the roofing sheets, as it ensures a tight fit and a uniform appearance. For example, in a large scale roofing project, if the roofing sheets have inconsistent dimensions, it can lead to difficulties in installation, such as gaps between the sheets, which can compromise the waterproofing and insulation properties of the roof.
4.2 Cost Efficiency
In the long run, using a roofing sheet machine can be cost efficient. While the initial investment in the machine can be significant, especially for fully automatic models, the cost per unit of roofing sheet produced is relatively low for high volume production. By producing roofing sheets in house, roofing contractors can eliminate the need to purchase pre fabricated sheets from external suppliers, which can save on transportation costs and the supplier's profit margin. In addition, the high speed production capabilities of roofing sheet machines can increase productivity, allowing contractors to complete projects more quickly and potentially take on more jobs.
4.3 Design Flexibility
Roofing sheet machines offer a high degree of design flexibility. They can be used to produce a wide variety of roofing sheet profiles, and the machine settings can be adjusted to create different sheet widths, lengths, and thicknesses. This allows roofing contractors and architects to choose the most suitable roofing solution for each project. For example, in a custom built residential project, the architect may want a unique roofing profile that is not commonly available in the market. A roofing sheet machine can be programmed to produce the desired profile, providing a customized solution for the project.
4.4 Energy Efficiency
Modern roofing sheet machines are designed to be energy efficient. They use advanced technologies, such as servo motor drives and energy saving control systems, to reduce energy consumption during the production process. This not only helps to lower the operating costs of the machine but also has a positive environmental impact. In addition, the roofing sheets produced by these machines can also contribute to the energy efficiency of buildings. For example, some roofing sheets are designed with reflective coatings that can reduce the amount of heat absorbed by the building, thus reducing the need for air conditioning.
6. Challenges and Solutions in Using Roofing Sheet Machines
6.1 Material Compatibility
One of the challenges in using roofing sheet machines is ensuring material compatibility. Different materials have different mechanical properties, such as hardness, ductility, and yield strength. Using the wrong material or improper machine settings for a particular material can lead to problems during the forming process, such as cracking, wrinkling, or uneven shaping. To address this challenge, it is important to carefully select the material based on the requirements of the roofing project and to adjust the machine settings accordingly. Some roofing sheet machines are equipped with sensors that can detect the properties of the incoming material and automatically adjust the forming parameters to ensure a smooth forming process.
6.2 Maintenance and Repairs
Roofing sheet machines, like any other industrial equipment, require regular maintenance and occasional repairs. The moving parts, such as the rolls, motors, and cutting blades, are subject to wear and tear over time. Neglecting maintenance can lead to reduced machine performance, increased downtime, and lower quality products. To solve this problem, a regular maintenance schedule should be established. This includes lubricating the moving parts, checking for loose connections, and replacing worn out components. In addition, having a reliable source of spare parts and access to technical support from the machine manufacturer can help to minimize downtime in case of repairs.
6.3 Operator Training
Operating a roofing sheet machine, especially a fully automatic one, requires a certain level of technical knowledge and skills. Untrained operators may make mistakes during the operation, such as incorrect machine settings, improper material feeding, or mishandling of the cutting process. This can lead to product defects, machine damage, and safety hazards. To overcome this challenge, comprehensive operator training programs should be provided. These programs should cover all aspects of machine operation, including startup, shutdown, parameter adjustment, and troubleshooting. In addition, operators should be trained on safety procedures to prevent accidents.
7. Future Trends in Roofing Sheet Machine Technology
7.1 Advanced Automation and Smart Manufacturing
The future of roofing sheet machines lies in advanced automation and smart manufacturing. These machines will be equipped with more advanced computer controlled systems, including artificial intelligence (AI) and machine learning (ML) algorithms. AI powered sensors will be able to monitor the production process in real time, detect any anomalies, and automatically adjust the machine settings to ensure optimal performance. For example, if the sensor detects a change in the material properties, the machine can automatically adjust the forming pressure and speed to compensate for the change. Smart manufacturing also enables remote monitoring and control of the machine, allowing operators to manage the production process from a distance.
7.2 Sustainable and Environmentally Friendly Features
As environmental concerns become more prominent, roofing sheet machines will incorporate more sustainable and environmentally friendly features. This may include the use of recycled materials for roofing sheet production, the development of energy efficient machine designs, and the reduction of waste during the production process. For example, some roofing sheet machines may be designed to use a higher percentage of recycled metal in the production of roofing sheets. In addition, the machine may be equipped with waste collection systems that can recycle or properly dispose of any scrap material generated during the production process.
7.3 Integration with Building Information Modeling (BIM)
Roofing sheet machines are likely to be integrated with Building Information Modeling (BIM) technology in the future. BIM is a digital representation of the physical and functional characteristics of a building. By integrating roofing sheet machines with BIM, the roofing design can be directly transferred from the BIM model to the machine's control system. This ensures that the roofing sheets are produced exactly according to the design specifications, reducing the risk of errors and improving the overall efficiency of the construction process. In addition, BIM integration can also help in the coordination of the roofing installation with other building components, such as the structural framework and the insulation system.
In conclusion, the roofing sheet machine is an essential piece of equipment in the construction industry. Its ability to produce high quality, cost effective, and versatile roofing sheets makes it a cornerstone of modern roofing construction. While there are challenges associated with its use, ongoing technological advancements are addressing these issues and opening up new possibilities for the future. As the construction industry continues to evolve, the roofing sheet machine will play an increasingly important role in providing innovative and sustainable roofing solutions.
Steel Roofing Machine: Transforming the Landscape of Roof Construction
1. Introduction
In the dynamic realm of construction, the steel roofing machine stands as a technological marvel that has revolutionized the way roofs are fabricated and installed. Steel has emerged as a favored material for roofing due to its remarkable strength, durability, and cost effectiveness. The steel roofing machine serves as the catalyst that transforms raw steel coils into precisely shaped roofing sheets, tailored to meet the diverse needs of residential, commercial, and industrial buildings. This equipment has not only enhanced the efficiency of roof construction but has also contributed to the overall quality and longevity of roofing systems. From withstanding extreme weather conditions to providing energy efficient solutions, steel roofing machines play a pivotal role in modern construction practices.
2. Working Principle
2.1 Material Feeding and Decoiling
The operation of a steel roofing machine commences with the material feeding stage. A large coil of steel, typically galvanized or color coated steel, is loaded onto a decoiling unit. This unit is designed to unwind the coil smoothly and feed the steel strip into the subsequent processing sections. The decoiling process is carefully regulated to ensure a consistent and even feed of the material. Advanced tension control systems are often integrated into the decoiling unit. These systems monitor the tension in the steel strip as it is unwound. For instance, if the tension is too high, the steel strip may stretch or break, while too low a tension can lead to wrinkling or uneven feeding. By maintaining optimal tension, the decoiling unit ensures that the steel strip enters the forming section in the best possible condition.
2.2 Forming Process
Once the steel strip is fed into the forming section, the real transformation begins. The forming section consists of a series of roll forming stations. Each station has a set of rolls, and as the steel strip passes through these rolls, it is gradually bent and shaped into the desired roofing profile. The rolls are precisely designed with specific curvatures and angles that correspond to the final shape of the roofing sheet. For example, in the production of trapezoidal shaped steel roofing sheets, the rolls are configured to create the characteristic upward sloping sides and flat tops. The number of roll forming stations can vary depending on the complexity of the profile. More intricate profiles, such as those with multiple bends and embossed features, may require a larger number of stations to achieve the desired shape accurately.
2.3 Cutting and Finishing
After the steel strip is formed into the roofing profile, it needs to be cut into the required lengths. The cutting process is usually carried out using a high precision cutting device, such as a hydraulic or pneumatic guillotine cutter. The cutting mechanism is synchronized with the speed of the forming process. This synchronization ensures that the sheets are cut accurately, with consistent lengths. In some advanced steel roofing machines, computer controlled cutting systems are employed. These systems can be programmed to cut the sheets into different lengths according to the specific requirements of the construction project.
Once cut, the steel roofing sheets may undergo additional finishing operations. This can include edge trimming to remove any rough edges, which could otherwise pose a safety hazard during installation. In some cases, a protective coating may be applied to enhance the corrosion resistance of the steel. For example, a layer of zinc aluminum alloy coating can be applied to the steel sheets, providing long term protection against rust and other forms of corrosion. Some machines are also equipped to perform embossing or stamping operations, which can add decorative elements or brand markings to the sheets.
3. Types of Steel Roofing Machines
3.1 Manual Steel Roofing Machines
Manual steel roofing machines are the most basic type. They are relatively simple in design and operation, making them suitable for small scale roofing projects or for use in areas with limited resources. In a manual machine, the operator is responsible for most of the processes. This includes feeding the steel strip into the machine, controlling the forming process by manually adjusting the roll positions (in some cases), and operating the cutting mechanism. Manual machines typically have a lower production capacity compared to their automated counterparts. However, they are more affordable and can be a viable option for small scale roofing contractors or for DIY roofing projects. For example, a homeowner in a rural area who wants to build a small shed may use a manual steel roofing machine to produce the roofing sheets.
3.2 Semi Automatic Steel Roofing Machines
Semi automatic steel roofing machines offer a step up in terms of automation. In these machines, some of the processes are automated, while others still require manual intervention. For example, the forming process may be automated, with the rolls being driven by electric motors. However, the feeding of the steel strip and the cutting of the sheets may still need to be done manually. Semi automatic machines are a good option for medium sized roofing contractors. They offer a balance between cost and productivity. They can produce a larger volume of roofing sheets compared to manual machines, while still being relatively affordable. These machines are also easier to operate and maintain compared to fully automatic machines, making them suitable for businesses with limited technical expertise.
3.3 Fully Automatic Steel Roofing Machines
Fully automatic steel roofing machines are the pinnacle of roofing machine technology. These machines are equipped with advanced computer controlled systems that automate all aspects of the production process, from material feeding to cutting and finishing. The material is automatically fed from the decoiling unit into the forming section, and the forming and cutting processes are precisely controlled by the machine's control system. Fully automatic machines are capable of high speed production and can achieve a high degree of accuracy in the production of roofing sheets. They are ideal for large scale roofing projects, such as those in commercial and industrial construction. For example, in the construction of a large industrial warehouse, a fully automatic steel roofing machine can produce a large number of roofing sheets in a short period, ensuring the project stays on schedule.
4. Applications in the Construction Industry
4.1 Residential Roofing
In residential construction, steel roofing machines have become increasingly popular. Steel roofing sheets produced by these machines offer several advantages. They are highly durable, capable of withstanding harsh weather conditions such as heavy rain, strong winds, and snow. The variety of profiles available, such as standing seam, corrugated, and trapezoidal, allows homeowners to choose a roofing style that complements the overall design of their houses. For example, a modern style house may feature standing seam steel roofing, which gives a sleek and contemporary look. Steel roofing is also energy efficient. Some steel roofing sheets are designed with reflective coatings that can reduce the amount of heat absorbed by the house, thus reducing the need for air conditioning and lowering energy bills.
4.2 Commercial Roofing
Commercial buildings, such as offices, warehouses, and retail stores, rely heavily on steel roofing machines. These buildings often require large scale roofing solutions, and the high production capacity of steel roofing machines makes them ideal for such projects. The durability of steel roofing sheets is crucial for commercial buildings, as any roof leaks or damage can disrupt business operations and cause significant losses. In addition, the energy efficiency of steel roofing can contribute to reducing the overall operating costs of the building. For example, a large warehouse can benefit from the use of energy efficient steel roofing sheets, which can help to lower the heating and cooling costs.
4.3 Industrial Roofing
Industrial buildings, such as factories and manufacturing plants, have unique roofing requirements. They often need roofing sheets that can withstand harsh environmental conditions, such as heavy industrial pollutants, extreme weather, and high temperature variations. Steel roofing machines can produce sheets made from materials like stainless steel or high strength galvanized steel, which offer excellent corrosion resistance and durability. These sheets can also be designed to meet the specific structural requirements of industrial buildings, such as the ability to support heavy equipment or to withstand high wind loads. For example, in a chemical factory, the roofing sheets need to be resistant to chemical corrosion, and the steel roofing machine can produce sheets with appropriate coatings and materials to meet this requirement.
5. Advantages of Steel Roofing Machines
5.1 High Quality and Consistent Products
Steel roofing machines are capable of producing high quality roofing sheets with consistent dimensions and profiles. The precise roll forming and cutting processes ensure that each sheet meets the required standards. This consistency is essential for the proper installation of the roofing sheets. In a large scale roofing project, if the roofing sheets have inconsistent dimensions, it can lead to difficulties in installation, such as gaps between the sheets, which can compromise the waterproofing and insulation properties of the roof. High quality steel roofing sheets produced by these machines also have a longer lifespan, reducing the need for frequent roof replacements.
5.2 Cost Efficiency
In the long run, using a steel roofing machine can be cost efficient. While the initial investment in the machine can be significant, especially for fully automatic models, the cost per unit of roofing sheet produced is relatively low for high volume production. By producing roofing sheets in house, roofing contractors can eliminate the need to purchase pre fabricated sheets from external suppliers, which can save on transportation costs and the supplier's profit margin. In addition, the high speed production capabilities of steel roofing machines can increase productivity, allowing contractors to complete projects more quickly and potentially take on more jobs.
5.3 Design Flexibility
Steel roofing machines offer a high degree of design flexibility. They can be used to produce a wide variety of roofing sheet profiles, and the machine settings can be adjusted to create different sheet widths, lengths, and thicknesses. This allows roofing contractors and architects to choose the most suitable roofing solution for each project. For example, in a custom built residential project, the architect may want a unique roofing profile that is not commonly available in the market. A steel roofing machine can be programmed to produce the desired profile, providing a customized solution for the project.
5.4 Energy Efficiency
Modern steel roofing machines are designed to be energy efficient. They use advanced technologies, such as servo motor drives and energy saving control systems, to reduce energy consumption during the production process. The roofing sheets produced by these machines can also contribute to the energy efficiency of buildings. Some steel roofing sheets are designed with reflective coatings that can reduce the amount of heat absorbed by the building, thus reducing the need for air conditioning. This not only helps to lower the operating costs of the building but also has a positive environmental impact.
6. Challenges and Solutions in Using Steel Roofing Machines
6.1 Material Compatibility
One of the challenges in using steel roofing machines is ensuring material compatibility. Different types of steel have different mechanical properties, such as hardness, ductility, and yield strength. Using the wrong type of steel or improper machine settings for a particular steel can lead to problems during the forming process, such as cracking, wrinkling, or uneven shaping. To address this challenge, it is crucial to carefully select the steel material based on the requirements of the roofing project and to adjust the machine settings accordingly. Some advanced steel roofing machines are equipped with sensors that can detect the properties of the incoming steel and automatically adjust the forming parameters to ensure a smooth forming process.
6.2 Maintenance and Repairs
Steel roofing machines, like any other industrial equipment, require regular maintenance and occasional repairs. The moving parts, such as the rolls, motors, and cutting blades, are subject to wear and tear over time. Neglecting maintenance can lead to reduced machine performance, increased downtime, and lower quality products. To solve this problem, a regular maintenance schedule should be established. This includes lubricating the moving parts, checking for loose connections, and replacing worn out components. In addition, having a reliable source of spare parts and access to technical support from the machine manufacturer can help to minimize downtime in case of repairs.
6.3 Operator Training
Operating a steel roofing machine, especially a fully automatic one, requires a certain level of technical knowledge and skills. Untrained operators may make mistakes during the operation, such as incorrect machine settings, improper material feeding, or mishandling of the cutting process. This can lead to product defects, machine damage, and safety hazards. To overcome this challenge, comprehensive operator training programs should be provided. These programs should cover all aspects of machine operation, including startup, shutdown, parameter adjustment, and troubleshooting. In addition, operators should be trained on safety procedures to prevent accidents.
7. Future Trends in Steel Roofing Machine Technology
7.1 Advanced Automation and Smart Manufacturing
The future of steel roofing machines lies in advanced automation and smart manufacturing. These machines will be equipped with more advanced computer controlled systems, including artificial intelligence (AI) and machine learning (ML) algorithms. AI powered sensors will be able to monitor the production process in real time, detect any anomalies, and automatically adjust the machine settings to ensure optimal performance. For example, if the sensor detects a change in the thickness of the incoming steel coil, the machine can automatically adjust the forming pressure and speed to compensate for the change. Smart manufacturing also enables remote monitoring and control of the machine, allowing operators to manage the production process from a distance.
7.2 Sustainable and Environmentally Friendly Features
As environmental concerns become more prominent, steel roofing machines will incorporate more sustainable and environmentally friendly features. This may include the use of recycled steel in the production of roofing sheets, the development of energy efficient machine designs, and the reduction of waste during the production process. For example, some steel roofing machines may be designed to use a higher percentage of recycled steel in the production of roofing sheets. In addition, the machine may be equipped with waste collection systems that can recycle or properly dispose of any scrap material generated during the production process.
7.3 Integration with Building Information Modeling (BIM)
Steel roofing machines are likely to be integrated with Building Information Modeling (BIM) technology in the future. BIM is a digital representation of the physical and functional characteristics of a building. By integrating steel roofing machines with BIM, the roofing design can be directly transferred from the BIM model to the machine's control system. This ensures that the roofing sheets are produced exactly according to the design specifications, reducing the risk of errors and improving the overall efficiency of the construction process. In addition, BIM integration can also help in the coordination of the roofing installation with other building components, such as the structural framework and the insulation system.
In conclusion, the steel roofing machine is an indispensable tool in the construction industry. Its ability to produce high quality, cost effective, and versatile steel roofing sheets has transformed the way roofs are constructed. While there are challenges associated with its use, ongoing technological advancements are addressing these issues and opening up new possibilities for the future. As the construction industry continues to evolve, the steel roofing machine will play an increasingly important role in providing innovative and sustainable roofing solutions.