Hotline
+86-136 8495 9862
Email:cennia@szmizhi.com
Add::104,Building 27,Third Industrial Zone, Longxi Community,Longgang District,Shenzhen,China.
Coil Forming & Handling Equipment
Surface Treatment Equipment
Solutions
Application
About Us
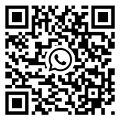
Welcome to MIZHI
For consultation/feedback, please call the service hotline: +86-136 8495 9862 Email:cennia@szmizhi.com
I. Introduction
The rotary shear cut to length line represents a significant advancement in the metal processing industry. It is a specialized production system designed to transform continuous metal coils into precisely cut sheets or strips of predetermined lengths with remarkable speed and accuracy. This technology has found extensive applications across diverse sectors, including automotive, construction, appliance manufacturing, and metal fabrication, playing a crucial role in meeting the growing demands for high-quality metal components.
II. Key Components and Their Functions
1. Uncoiling Unit
The process commences with the uncoiling unit, which serves as the starting point for the metal coil. It is equipped with a robust mandrel or expansion shaft capable of securely holding coils of varying sizes and weights. The uncoiling mechanism is designed to unwind the metal strip smoothly, and its speed can be precisely controlled using advanced variable speed drives. This control is essential to synchronize with the downstream operations. For example, in a busy steel service center processing coils for multiple customers, the uncoiling speed needs to be adjusted according to the specific requirements of each job to ensure a continuous and efficient flow of material.
Tension control is a vital aspect of the uncoiling unit. It employs load cells and feedback control systems to maintain a constant tension on the unwinding metal. This prevents issues such as strip wrinkling, which can occur if the tension is too low, or strip breakage, which might happen if the tension is too high. In the production of thin-gauge metal sheets for electronics applications, where even minor deformations can render the product unusable, precise tension control is of utmost importance.
2. Leveling Unit
Once the metal strip is uncoiled, it enters the leveling unit. Metal coils often develop internal stresses during manufacturing, storage, or transportation, leading to warping or curling. The leveling unit utilizes a series of precisely calibrated rollers, strategically arranged to apply opposing forces that flatten the metal. This process eliminates residual stresses and ensures a flat, planar surface. In the aerospace industry, where tight tolerances are required for components such as aircraft wings and fuselage panels, the leveling process is critical to achieving the necessary precision.
3. Rotary Shear Cutting Unit
The rotary shear cutting unit is the heart of the line. It consists of a circular blade that rotates at high speed, slicing through the metal strip with remarkable precision. The blade is typically made of high-quality, hardened steel to withstand the continuous cutting action. The cutting process is highly efficient, allowing for rapid production of cut sheets. Different blade geometries and configurations can be employed depending on the material thickness and the desired cut quality. For thicker metal sheets, a larger diameter blade with more robust cutting edges may be used, while for thinner materials, a finer blade with a higher rotational speed can achieve the best results.
The cutting unit is synchronized with the other components through advanced control systems. It can receive signals from sensors monitoring the metal strip's position and speed, ensuring accurate cut lengths. This synchronization also minimizes waste generation by precisely cutting the metal according to the programmed specifications. In the construction industry, where large quantities of metal studs and roofing sheets are produced, the ability to cut accurately and minimize waste is crucial for cost-effective production.
4. Stacking and Packaging Unit
After the metal sheets are cut to the desired lengths, they are transferred to the stacking and packaging unit. Automated stacking mechanisms arrange the sheets in an orderly manner, either horizontally or vertically, depending on the storage and transportation requirements. The stacks can then be bundled together using straps or shrink-wrapped to protect the sheets during transit and storage. In a manufacturing facility producing metal components for appliances, the stacking and packaging unit ensures that the cut sheets are ready for further processing or shipment in a convenient and organized fashion.
III. Operation and Workflow
1. Setup Phase
Before initiating production, operators must carefully load the metal coil onto the uncoiling unit. This involves proper alignment of the coil and ensuring it is firmly seated on the mandrel. The leveling, cutting, and stacking parameters are then set based on the job requirements. For instance, if manufacturing sheets for a specific automotive part, the thickness, width, length, and any surface finish specifications are entered into the control system. The cutting unit's blade speed and rotational direction, as well as the tension control settings, are adjusted accordingly.
2. Continuous Production
Once the setup is complete, the rotary shear cut to length line begins operation. The metal coil unwinds at a controlled rate, passes through the leveling unit to be flattened, and then reaches the cutting unit. Here, the rotary shear blade cuts the metal into precise lengths as per the programmed instructions. The cut sheets are immediately transferred to the stacking and packaging unit, where they are organized and prepared for further use or shipment. Throughout this process, sensors and feedback loops continuously monitor the quality of the metal strip, the cutting accuracy, and the stack height. Any deviations from the set parameters are detected and corrected in real-time, ensuring optimal performance.
3. Quality Control
Quality control is an integral part of the line's operation. Visual inspection systems, equipped with high-resolution cameras and image processing software, scan the metal sheets for surface defects such as scratches, dents, or discoloration. Dimensional measurement tools, like laser gauges and precision calipers, check the cut lengths, widths, and thicknesses against the preset tolerances. In case of any non-compliance, the production line can be paused automatically, and an alarm raised to alert the operators. This ensures that only high-quality, accurately cut metal sheets are released for downstream applications.
IV. Advantages of Rotary Shear Cut to Length Lines
1. High Precision
The rotary shear cutting technology offers outstanding precision. The rotating blade can make extremely clean and accurate cuts, ensuring that the cut lengths and dimensions of the metal sheets are within tight tolerances. This is crucial in industries where component fit and function depend on precise metal dimensions, such as the electronics and aerospace sectors. For example, in the production of microelectronic substrates, any deviation from the exact size could lead to malfunctioning of the final product.
2. High Speed
These lines are capable of operating at high speeds, enabling rapid production of cut sheets. The efficient rotary shear cutting process, combined with the synchronized operation of the other components, allows for a significant throughput of metal. In a large-scale manufacturing facility, a rotary shear cut to length line can process a substantial amount of metal coil per hour, meeting tight production schedules. This speed advantage is especially beneficial in industries with high demand for metal components, like automotive and construction.
3. Versatility
Rotary shear cut to length lines can handle a wide range of metal materials, including steel, aluminum, and copper. They can also accommodate different material thicknesses, from thin sheets used in electronics to thicker plates required in heavy machinery manufacturing. This versatility makes them suitable for diverse manufacturing applications, providing manufacturers with the flexibility to produce various metal products without the need for multiple specialized lines.
4. Cost-Effectiveness
The combination of high precision, high speed, and versatility leads to cost savings. The ability to produce accurately cut sheets with minimal waste reduces material costs. Faster production rates mean lower labor costs per unit, as fewer operators are needed to oversee the process. Additionally, the reliable operation of the line and reduced need for rework due to high quality contribute to overall cost efficiency. In the long run, investing in a rotary shear cut to length line can be a profitable choice for manufacturers.
V. Applications in Different Industries
1. Automotive
In the automotive industry, rotary shear cut to length lines are essential for producing metal components such as body panels, chassis parts, and engine covers. The high precision ensures a proper fit of these components during assembly, while the high speed enables the production of large quantities to meet the demands of vehicle manufacturing. For instance, in the production of a new car model, thousands of identically sized and shaped metal sheets are required, and these lines can supply them efficiently.
2. Electronics
For the electronics industry, the precision and speed of these lines are invaluable. They are used to cut thin metal sheets for circuit boards, casings, and connectors. The micro-sized components demand extremely tight tolerances, and the rotary shear cut to length line can deliver. In the manufacture of smartphones, tablets, and other portable devices, the quality of the cut metal parts can directly affect the device's performance and durability.
3. Construction
In construction, rotary shear cut to length lines are widely used to process metal building materials. They can quickly produce the required lengths of metal studs, roofing sheets, and siding panels. This not only speeds up construction projects but also ensures the quality and consistency of the metal components used. For a large commercial building project, the line can provide the necessary metal materials in a timely manner, reducing construction delays.
4. Metal Fabrication
In the metal fabrication industry, these lines are the backbone of production. They are used to cut metal sheets and strips for a wide variety of custom projects, from industrial machinery parts to decorative metalwork. The versatility of the rotary shear cut to length line allows fabricators to take on diverse jobs and meet the unique requirements of each customer.
VI. Maintenance and Safety Considerations
1. Maintenance
Regular maintenance is crucial to keep the rotary shear cut to length line in optimal working condition. The rollers in the uncoiling, leveling, and transport units need to be lubricated and inspected for wear. The rotary shear blade must be sharpened or replaced regularly to maintain its cutting efficiency. The control systems and sensors also require calibration to ensure accurate operation. Manufacturers typically provide detailed maintenance schedules and procedures, which operators should follow strictly.
2. Safety
Given the presence of high-speed rotating blades and other moving parts, safety is a top priority. Safety guards are installed around the uncoiling, leveling, and cutting units to prevent operators from coming into contact with dangerous elements. Emergency stop buttons are strategically placed throughout the line, allowing for immediate shutdown in case of an accident or malfunction. Additionally, operators are trained in proper safety procedures and must wear appropriate personal protective equipment such as safety glasses, gloves, and hard hats. Safety interlocks prevent unauthorized access to the operating area while the line is running.
VII. Future Trends and Developments
As technology continues to advance, rotary shear cut to length lines are expected to evolve. New materials and coatings for the rotary shear blade may enhance its durability and cutting performance. The control systems will likely become more intelligent, with predictive maintenance capabilities and enhanced synchronization with other manufacturing processes. Integration with robotics and automated warehousing could further streamline production and improve overall efficiency. Moreover, as industries demand even tighter tolerances and faster production speeds, these lines will continue to adapt to meet the challenges, remaining a vital part of the global manufacturing landscape.
VIII. Conclusion
The rotary shear cut to length line is a remarkable innovation in the metal processing industry. Its combination of precision, speed, versatility, and cost-effectiveness has made it indispensable in numerous industries. By enabling the efficient production of high-quality metal sheets and strips, it has contributed to the growth and success of manufacturing enterprises. As we look to the future, further advancements in this technology will surely open up new opportunities and drive continued progress in metal processing and manufacturing as a whole.