Hotline
+86-136 8495 9862
Email:cennia@szmizhi.com
Add::104,Building 27,Third Industrial Zone, Longxi Community,Longgang District,Shenzhen,China.
Coil Forming & Handling Equipment
Surface Treatment Equipment
Solutions
Application
About Us
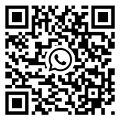
Welcome to MIZHI
For consultation/feedback, please call the service hotline: +86-136 8495 9862 Email:cennia@szmizhi.com
I. Introduction
The SS (stainless steel) coil slitting machine is a specialized piece of equipment in the metal processing industry. Stainless steel is known for its excellent corrosion resistance, strength, and aesthetic appeal, making it a highly sought - after material in numerous applications. The SS coil slitting machine plays a crucial role in transforming large coils of stainless steel into narrower strips, which can then be further processed or used directly in various end - use products.
II. Design and Components of an SS Coil Slitting Machine
A. Uncoiling Unit
1. Mandrel and Expansion Mechanism
The uncoiling unit is the starting point of the SS coil slitting machine. The mandrel is designed to hold the stainless - steel coil. It has an expansion mechanism, which is typically hydraulic or mechanical. The expansion mechanism is crucial as it ensures a firm grip on the coil. Since stainless - steel coils can come in different inner diameters, the ability of the mandrel to expand and contract accordingly is vital. For example, in a high - production environment where different suppliers' coils are used, the mandrel must be able to adapt. A hydraulic expansion system offers more precise control, allowing for a snug fit around the coil's inner diameter, which is essential for preventing the coil from slipping during the uncoiling process.
2. Brake and Tension Control
To regulate the uncoiling speed of the stainless - steel coil, a brake system is incorporated. This is necessary because if the coil unwinds too quickly, it can lead to issues such as material wrinkling or improper feeding into the slitting section. Tension control is also a key aspect of the uncoiling unit. Maintaining the correct tension is important for the quality of the slitting process. If the tension is too high, it can cause the stainless - steel coil to deform or even break, while too low tension may result in a lack of stability during feeding. Advanced uncoiling units use sensors and feedback systems to continuously monitor and adjust the brake and tension settings.
B. Slitting Section
1. Slitting Blades
The slitting section is the heart of the SS coil slitting machine. It contains the slitting blades, which are responsible for cutting the wide stainless - steel coil into narrower widths. These blades are made of high - quality materials, often carbide or specialized tool steel. Carbide blades are preferred for slitting stainless steel due to their high hardness and wear resistance. The blades are mounted on shafts, and the number of blades can be adjusted according to the desired width of the slit coils. For instance, if a manufacturer needs to produce multiple widths of stainless - steel strips from a single coil, they can configure the number and spacing of the slitting blades accordingly.
2. Blade Gap Adjustment
Precise adjustment of the blade gap is crucial for achieving accurate slitting of stainless steel. The gap between the blades needs to be set based on the thickness of the coil. If the gap is too wide, the slitting quality will be compromised, resulting in rough edges and potential burrs. On the other hand, if the gap is too narrow, the blades may collide, leading to premature wear and damage. Modern SS coil slitting machines often feature automated blade gap adjustment systems. These systems can be calibrated according to the input of the coil thickness, ensuring consistent and high - quality slitting.
3. Blade Drive System
The slitting blades are driven by a drive system, usually an electric motor. The drive system must be powerful enough to cut through the stainless - steel coil. Since stainless steel is relatively hard compared to some other metals, a high - torque motor is often required. The speed of the blade rotation can also be adjusted. This adjustment is important as it can be optimized based on factors such as the thickness of the coil and the desired slitting speed. For example, when slitting thicker stainless - steel coils, a slower blade rotation speed may be necessary to ensure a clean cut.
C. Edge Trimming Unit
1. Trimming Blades
The edge trimming unit is responsible for removing any irregular or damaged edges from the slit stainless - steel coils. The trimming blades are similar in nature to the slitting blades but are specifically designed for edge trimming. They are often adjustable in terms of their cutting depth. This adjustability allows for precise removal of the edges, ensuring a clean and smooth finish. In the case of stainless - steel coils, a high - quality edge trim is important as it can affect the appearance and functionality of the final product.
2. Alignment and Positioning
Accurate alignment and positioning of the trimming blades are critical for effective edge trimming. The unit uses sensors and servo - motor - based control systems to detect the position of the coil edges and adjust the trimming blades accordingly. This ensures that the edges are trimmed evenly and precisely, which is especially important for stainless - steel products where aesthetics and dimensional accuracy are often highly valued.
D. Recoiling Unit
1. Mandrel and Tension Control
The recoiling unit is where the slit and edge - trimmed stainless - steel coils are rewound into new coils. The mandrel in the recoiling unit is similar to that in the uncoiling unit but may have different tension control mechanisms. Tension control during recoiling is essential to ensure that the new coils are wound tightly and evenly. For stainless - steel coils, proper tension control is crucial as it can prevent issues such as coil loosening during handling or storage. If the tension is not correct, the coil may unwind or become deformed, which can be problematic for subsequent processing or use.
2. Wrapping and Packaging
Some recoiling units also include features for wrapping and packaging the new coils. This is important for protecting the stainless - steel coils from damage during storage and transportation. The wrapping can be done using materials such as plastic or paper. Automated wrapping systems are becoming more common, which can apply the wrapping material evenly around the coil, providing better protection and a more professional appearance.
III. Functioning of an SS Coil Slitting Machine
A. Uncoiling and Initial Feed
The process begins with the placement of the stainless - steel coil on the uncoiling unit's mandrel. The expansion mechanism secures the coil in place, and the brake and tension control systems are set. The coil then starts to unwind, and the material is fed through a series of rollers towards the slitting section. These rollers play an important role in guiding the material and maintaining the proper tension. The speed of the uncoiling and feeding is carefully controlled to ensure a smooth and continuous flow of the stainless - steel coil.
B. Slitting Process
As the stainless - steel coil enters the slitting section, the slitting blades start to cut the wide coil into narrower widths. The blades rotate at a high speed, and the coil is continuously fed through them. The cutting force exerted by the blades is determined by factors such as the blade sharpness, the speed of rotation, and the thickness of the coil. During the slitting process, the edge trimming unit may also be activated simultaneously to remove any unwanted edges from the newly slit coils. The heat generated during the slitting of stainless steel needs to be managed, especially in high - speed slitting operations. Some machines are equipped with cooling systems to dissipate the heat and prevent any negative effects on the blade life or the quality of the slit coils.
C. Edge Trimming
After the slitting, the coil passes through the edge trimming unit. The trimming blades are activated to remove the edges as per the set parameters. The trimmed edges are collected and disposed of separately. The edge trimming process helps to improve the quality of the slit coils, making them suitable for applications where precise edge quality is required. For stainless - steel products, such as those used in the food industry or high - end architectural applications, a smooth and clean edge is essential.
D. Recoiling
The slit and edge - trimmed stainless - steel coils then enter the recoiling unit. Here, they are rewound onto new mandrels. The tension control system ensures that the recoiling is done with the appropriate amount of tension. Once the recoiling is complete, the new coils are either wrapped for protection or sent directly for further processing or storage.
IV. Applications of SS Coil Slitting Machines
A. Construction Industry
1. Architectural Facades
In the construction industry, SS coil slitting machines are used to produce stainless - steel strips for architectural facades. The ability to slit stainless - steel coils into precise widths allows for the creation of custom - designed facades with a high - end aesthetic. These facades are not only durable but also resistant to corrosion, making them suitable for both indoor and outdoor applications. For example, in modern high - rise buildings, slit stainless - steel strips are used to create unique patterns and textures on the building's exterior.
2. Interior Decoration
Stainless - steel strips produced by SS coil slitting machines are also used for interior decoration. They can be used for applications such as wall cladding, elevator interiors, and decorative trim. The smooth and clean edges of the slit stainless - steel strips contribute to a luxurious and modern look. Additionally, the corrosion resistance of stainless steel makes it a practical choice for interior applications where it may be exposed to moisture or other environmental factors.
B. Food Processing Industry
1. Equipment Manufacturing
In the food processing industry, stainless steel is widely used due to its hygienic properties. SS coil slitting machines are used to produce components for food processing equipment, such as conveyor belts, storage tanks, and processing chambers. The precise slitting of stainless - steel coils ensures that these components meet the strict hygiene and safety requirements of the food industry. The clean edges and accurate dimensions of the slit stainless - steel parts are crucial for preventing the accumulation of food particles and for easy cleaning.
2. Packaging
Stainless - steel strips are also used in food packaging applications. For example, they can be used to make closures or reinforcing elements for food containers. The slitting of stainless - steel coils into the appropriate widths allows for the production of packaging components that are both strong and resistant to corrosion, protecting the food inside.
C. Automotive Industry
1. Exterior Trim
In the automotive industry, SS coil slitting machines are used to produce stainless - steel strips for exterior trim. These strips are used for applications such as window surrounds, grille inserts, and side moldings. The high - quality finish of the slit stainless - steel strips enhances the appearance of the vehicle. Additionally, the corrosion resistance of stainless steel ensures that the exterior trim remains in good condition over time, even in harsh environmental conditions.
2. Interior Components
Stainless - steel is also used for some interior automotive components, such as seat frames and dashboard accents. SS coil slitting machines are used to produce the necessary stainless - steel parts with the correct dimensions. The ability to slit stainless - steel coils accurately is important for ensuring a proper fit and finish of these interior components.
V. Factors Affecting the Performance of an SS Coil Slitting Machine
A. Stainless - Steel Properties
1. Thickness
The thickness of the stainless - steel coil has a significant impact on the performance of the SS coil slitting machine. Thicker coils require more powerful slitting blades and drive systems, as well as more precise tension control. For example, a 3 - mm - thick stainless - steel coil will demand a higher - torque drive for the slitting blades compared to a 1 - mm - thick coil. Additionally, thicker coils may require slower slitting speeds to ensure a clean cut.
2. Grade and Composition
The grade and composition of the stainless steel also play a role. Different grades of stainless steel have different levels of hardness, ductility, and corrosion resistance. For instance, austenitic stainless steels are generally more ductile than martensitic stainless steels. This difference in properties can affect the slitting process. A more ductile stainless steel may require different blade settings or cutting speeds to achieve the best slitting quality.
B. Machine - related Factors
1. Blade Quality
The quality of the slitting and trimming blades is crucial for the performance of the SS coil slitting machine. High - quality blades made of appropriate materials (e.g., carbide for hard stainless steels) will result in better slitting and edge trimming quality. Dull or damaged blades will lead to rough cuts, burrs, and increased wear on other machine components. Regular blade maintenance and replacement are necessary to ensure optimal performance.
2. Machine Calibration
Proper calibration of the entire SS coil slitting machine is essential. This includes calibrating the uncoiling and recoiling systems for correct tension control, the slitting section for accurate blade gap adjustment and blade rotation speed, and the edge trimming unit for proper alignment. Incorrect calibration can result in poor - quality products and reduced machine efficiency.
VI. Advantages of Using an SS Coil Slitting Machine
A. Precision
One of the main advantages of using an SS coil slitting machine is the high precision it offers. The ability to slit stainless - steel coils into very accurate widths and produce clean edges is essential for many applications. For example, in the manufacturing of precision parts for the food processing or automotive industries, precise slitting ensures that the parts fit together correctly and meet the required specifications.
B. Efficiency
These machines can significantly improve the efficiency of stainless - steel processing. They can slit large coils into smaller widths at a relatively high speed, depending on the machine's capabilities and the characteristics of the stainless - steel coil. This allows for large - volume production in a shorter amount of time. Additionally, the automated nature of many SS coil slitting machines reduces the need for manual labor, further increasing efficiency.
C. Customization
SS coil slitting machines enable customization of stainless - steel products. Manufacturers can slit coils into specific widths according to the requirements of different customers or applications. This is particularly important in industries such as construction and automotive, where customized products are often in high demand. For instance, in the construction of a unique building facade, the ability to produce stainless - steel strips of different widths is crucial for achieving the desired design.
VII. Challenges and Future Developments
A. Challenges
1. Blade Wear
One of the main challenges in SS coil slitting machines is blade wear. Since stainless steel is a relatively hard material, the slitting and trimming blades are subject to significant wear during the cutting process. Regular blade replacement is required, which can be costly and time - consuming. The wear rate also depends on factors such as the thickness and grade of the stainless - steel coil, as well as the cutting speed and blade quality.
2. Maintenance and Downtime
The complex nature of SS coil slitting machines means that they require regular maintenance. Components such as the uncoiling and recoiling systems, slitting blades, and edge trimming units need to be maintained to ensure optimal performance. Downtime for maintenance can be a significant issue, especially in high - volume production environments. Finding ways to reduce maintenance time and increase the reliability of the machine is a continuous challenge.
B. Future Developments
1. Automation and Industry 4.0 Integration
The future of SS coil slitting machines is likely to see increased automation and integration with Industry 4.0 concepts. Machines will be more connected, allowing for remote monitoring and control. Automated blade replacement systems and predictive maintenance based on real - time data analysis will be developed. For example, sensors can be installed to monitor blade wear, tension levels, and other key parameters, and the system can predict when maintenance is required and schedule it accordingly.
2. Improved Slitting Technologies
There will be continuous improvement in slitting technologies. New blade materials and designs may be developed to reduce blade wear and improve slitting quality. For example, advanced coatings on slitting blades may be introduced to increase their hardness and wear resistance. Additionally, new slitting methods that are more energy - efficient and produce less waste may emerge.
In conclusion, the SS coil slitting machine is a vital piece of equipment in the processing of stainless - steel coils. It offers numerous advantages in terms of precision, efficiency, and customization, but also faces challenges such as blade wear and maintenance requirements. With future developments in automation and slitting technologies, these machines are expected to become more efficient and reliable, further enhancing their importance in various industries.