Hotline
+86-136 8495 9862
Email:cennia@szmizhi.com
Add::104,Building 27,Third Industrial Zone, Longxi Community,Longgang District,Shenzhen,China.
Coil Forming & Handling Equipment
Surface Treatment Equipment
Solutions
Application
About Us
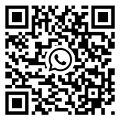
Welcome to MIZHI
For consultation/feedback, please call the service hotline: +86-136 8495 9862 Email:cennia@szmizhi.com
In the realm of metal fabrication and manufacturing, the sheet metal cut to length machine stands as a crucial tool for achieving precision and efficiency. This advanced piece of equipment is designed to cut sheet metal into specific lengths with accuracy and speed, meeting the diverse needs of various industries.
I. Introduction to Sheet Metal Cut to Length Machine
The sheet metal cut to length machine is a specialized piece of machinery that is used to cut large sheets of metal into smaller, more manageable lengths. It is commonly found in industries such as automotive, aerospace, construction, and appliance manufacturing, where precise cuts are essential for the production of components and parts.
These machines typically consist of several key components, including an uncoiler, a straightener, a shear unit, and a stacker. The uncoiler unwinds the sheet metal coil, while the straightener ensures that the metal is flat and free from any distortions. The shear unit then cuts the metal to the desired length, and the stacker neatly stacks the cut pieces for easy handling and transportation.
Sheet metal cut to length machines can handle a wide range of metal materials, including steel, aluminum, copper, and stainless steel. They are also capable of processing sheets of different thicknesses and widths, making them highly versatile and suitable for a variety of applications.
II. Working Principle of Sheet Metal Cut to Length Machine
The operation of a sheet metal cut to length machine is based on a precise and coordinated process. As the sheet metal coil is unwound by the uncoiler, it passes through the straightener, which uses a series of rollers to flatten and align the metal. The straightened sheet then enters the shear unit, where a pair of blades or a rotary shear cuts the metal to the specified length.
The cutting process is controlled by a programmable logic controller (PLC), which ensures accurate and consistent cuts. The PLC can be programmed to adjust the cutting length, speed, and other parameters according to the specific requirements of the job.
Once the sheet metal is cut, it is conveyed to the stacker, where it is neatly stacked in a predetermined manner. The stacker can be adjusted to accommodate different sheet sizes and stack heights, ensuring efficient storage and transportation of the cut pieces.
III. Advantages of Sheet Metal Cut to Length Machine
1. Precision Cutting: Sheet metal cut to length machines are designed to provide accurate and consistent cuts, ensuring that the finished products meet the strictest quality standards. The use of advanced cutting technology and precision controls allows for minimal tolerance deviations, resulting in high-quality cuts.
2. High Production Capacity: These machines are capable of processing large volumes of sheet metal quickly and efficiently, significantly increasing production capacity. With their high-speed cutting capabilities and automated processes, they can keep up with the demands of large-scale manufacturing operations.
3. Versatility: Sheet metal cut to length machines can handle a wide range of metal materials, thicknesses, and widths, making them highly versatile and suitable for various applications. They can be easily adjusted to meet different production requirements, providing flexibility to manufacturers.
4. Cost-Effective: By reducing waste and minimizing the need for additional processing steps, sheet metal cut to length machines can help to lower production costs. They also offer a more efficient use of raw materials, as they can cut the sheet metal to the exact lengths needed for a particular job.
5. Automated Operation: Many sheet metal cut to length machines are equipped with advanced automation features, such as PLCs and human-machine interfaces (HMIs). These features allow for easy operation and control, reducing the need for manual labor and minimizing the risk of errors.
IV. Applications of Sheet Metal Cut to Length Machine
1. Automotive Industry: In the automotive industry, sheet metal cut to length machines are used to cut sheet metal for body panels, chassis components, and other parts. The precision and high production capacity of these machines are essential for meeting the demanding requirements of the automotive industry.
2. Aerospace Industry: The aerospace industry also relies on sheet metal cut to length machines for the production of aircraft components. The accuracy and quality of the cuts are crucial for ensuring the safety and performance of aircraft.
3. Construction Industry: Sheet metal cut to length machines are used in the construction industry for cutting metal sheets for roofing, siding, and other applications. The versatility and cost-effectiveness of these machines make them a popular choice for construction projects.
4. Appliance Manufacturing: In appliance manufacturing, sheet metal cut to length machines are used to cut sheet metal for the production of refrigerators, washing machines, and other appliances. The precision and high production capacity of these machines are essential for meeting the demand for these products.
5. Metal Fabrication: Metal fabricators use sheet metal cut to length machines to cut sheet metal for a variety of applications, including structural components, enclosures, and decorative elements. The versatility and efficiency of these machines make them an essential tool for metal fabricators.
V. Maintenance and Care of Sheet Metal Cut to Length Machine
To ensure the optimal performance and longevity of a sheet metal cut to length machine, regular maintenance and care are essential. Some of the key maintenance tasks include:
1. Lubrication: Regularly lubricate the moving parts of the machine, such as the rollers, bearings, and shear blades. This helps to reduce friction and wear, ensuring smooth operation.
2. Blade Sharpening: The shear blades need to be sharpened regularly to maintain their cutting efficiency. Depending on the usage, the blades may need to be sharpened every few weeks or months.
3. Inspection: Inspect the machine regularly for signs of wear, damage, or malfunction. Check the alignment of the rollers, the condition of the shear blades, and the operation of the uncoiler, straightener, and stacker.
4. Cleaning: Keep the machine clean by removing dust, debris, and metal shavings. This helps to prevent clogging and damage to the components.
5. Training: Provide proper training to the operators to ensure they understand the operation and maintenance requirements of the machine. This helps to reduce the risk of accidents and ensure the machine is used correctly.
VI. Future Trends in Sheet Metal Cut to Length Machine Technology
As technology continues to advance, we can expect to see several trends in the development of sheet metal cut to length machine technology. Some of these trends include:
1. Increased Automation: With the growing demand for high productivity and consistent quality, we can expect to see more advanced automation features being integrated into sheet metal cut to length machines. This may include the use of artificial intelligence and machine learning algorithms to optimize the cutting process and improve efficiency.
2. Enhanced Precision: As industries demand even higher precision in metal processing, we can expect to see improvements in the cutting accuracy of sheet metal cut to length machines. This may involve the use of more advanced sensors and control systems to ensure precise cuts with minimal tolerance deviations.
3. Versatility and Flexibility: Manufacturers will continue to seek equipment that is more versatile and flexible, able to handle a wide range of metal materials, thicknesses, and widths. This may lead to the development of modular sheet metal cut to length machines that can be easily customized and reconfigured to meet different production requirements.
4. Energy Efficiency: With the increasing focus on sustainability and energy conservation, we can expect to see the development of more energy-efficient sheet metal cut to length machines. This may involve the use of advanced drive systems and power management technologies to reduce energy consumption.
In conclusion, the sheet metal cut to length machine is a vital tool for metal fabrication and manufacturing. With its precision cutting capabilities, high production capacity, and versatility, it offers significant advantages over traditional cutting methods. As technology continues to advance, we can expect to see further improvements in this technology, making it even more valuable in the metal processing industry.