Hotline
+86-136 8495 9862
Email:cennia@szmizhi.com
Add::104,Building 27,Third Industrial Zone, Longxi Community,Longgang District,Shenzhen,China.
Coil Forming & Handling Equipment
Surface Treatment Equipment
Solutions
Application
About Us
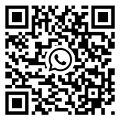
Welcome to MIZHI
For consultation/feedback, please call the service hotline: +86-136 8495 9862 Email:cennia@szmizhi.com
1. Introduction
In the industrial manufacturing and metalworking sectors, achieving a high quality surface finish on components is of utmost importance. Shot blast cabinets have emerged as a fundamental and highly effective solution for a wide range of surface treatment needs. These cabinets provide a controlled environment where high velocity abrasive media, in the form of shots, are propelled onto the surfaces of workpieces. This process serves multiple purposes, including cleaning, deburring, descaling, and enhancing the surface properties of materials. From small scale workshops to large scale industrial plants, shot blast cabinets are utilized across various industries such as automotive, aerospace, construction, and artisanal metalwork. This in depth analysis will cover all aspects of shot blast cabinets, including their components, working principles, applications, advantages, challenges, and future trends.
2. Components of Shot Blast Cabinets
2.1 Cabinet Enclosure
The cabinet enclosure is the outer structure that houses the entire shot blasting operation. It is typically made of thick gauge steel to withstand the impact of the high velocity shots and to ensure the safety of the operators and the surrounding environment. The interior of the cabinet is often lined with wear resistant materials such as rubber or manganese steel. Rubber linings are popular due to their ability to absorb the impact of the shots, reducing noise and minimizing damage to the cabinet walls. Manganese steel linings, on the other hand, offer exceptional durability and are suitable for heavy duty applications where high intensity shot blasting is required.
The cabinet is designed with access doors or hatches that allow for easy loading and unloading of workpieces. These doors are equipped with safety interlocks to prevent the shot blasting process from starting when the doors are open. In some advanced models, the doors may be automated, either pneumatically or electrically, to improve the efficiency of the operation. The size of the cabinet can vary significantly, from small benchtop models with a volume of a few cubic feet, suitable for small scale hobbyist or jewelry making applications, to large industrial sized cabinets that can accommodate large scale components such as aircraft engine parts or construction machinery components.
2.2 Blast Wheel Assembly
The blast wheel assembly is the heart of the shot blast cabinet. It is responsible for accelerating the abrasive shots to high velocities. The blast wheel consists of a rotating disk with carefully designed vanes. The shots are fed into the center of the rotating disk and are then flung outwards by centrifugal force. The speed of the blast wheel can be adjusted, usually within a range of 1000 3000 revolutions per minute, depending on the model and the application. Higher speeds are used for heavy duty cleaning and surface hardening, while lower speeds are suitable for more delicate surface finishing tasks.
The vanes on the blast wheel are made of wear resistant materials such as high chromium cast iron. These vanes are constantly in contact with the high velocity shots, and their durability is crucial for the consistent operation of the shot blasting process. Over time, the vanes may wear down and need to be replaced. Some modern blast wheels are designed with quick change vane systems, allowing for faster maintenance and reduced downtime. The blast wheel is powered by an electric motor, and the motor's power rating can vary from a few horsepower for small scale cabinets to tens of horsepower for large industrial models.
2.3 Abrasive Feeding System
The abrasive feeding system is responsible for supplying the shots to the blast wheel. It typically includes a hopper that stores the abrasive shots. The hopper is designed to hold a sufficient quantity of shots to ensure continuous operation of the shot blasting process. A metering device, such as a rotary valve or a vibrating feeder, controls the flow rate of the shots from the hopper to the blast wheel. Precise control of the abrasive feeding rate is essential. If the feeding rate is too high, it can overload the blast wheel and cause inefficiencies, such as inconsistent shot distribution. If the rate is too low, it can result in incomplete surface treatment.
The abrasive feeding system may also include a recycling mechanism. In many shot blast cabinets, the used shots are collected at the bottom of the cabinet and are recycled back into the hopper for reuse. This recycling process not only reduces the cost of the abrasive media but also minimizes waste. The recycling system may use a combination of augers, conveyors, and separators to clean and sort the used shots before returning them to the hopper.
2.4 Dust Collection System
During the shot blasting process, a significant amount of dust is generated. This dust consists of abrasive particles, debris from the surface being treated, and in some cases, fine metal particles. The dust collection system is crucial for maintaining a clean and safe working environment. It typically includes a series of ducts, filters, and a powerful fan. The fan creates a suction force that draws the dust laden air from the cabinet into the ducts.
The filters are designed to trap the dust particles, allowing clean air to be released back into the atmosphere. There are different types of filters used in dust collection systems, such as cartridge filters and bag filters. Cartridge filters are known for their high efficiency dust removal capabilities and are often used in industrial settings where strict environmental regulations need to be met. Bag filters, on the other hand, are more cost effective and are suitable for less demanding applications. The dust collection system may also include a dust disposal mechanism, such as a dust bin or a connection to a central dust collection system in a large industrial plant.
2.5 Workpiece Handling System
The workpiece handling system is responsible for moving the components to be shot blasted in and out of the cabinet. In small scale shot blast cabinets, this may be a simple manual operation, where the operator uses a hook or a tray to place and remove the workpieces. In larger industrial scale cabinets, more sophisticated workpiece handling systems are used. These can include conveyor belts, overhead cranes, or robotic arms.
Conveyor belts are commonly used for continuous production processes, where workpieces are moved through the cabinet in a sequential manner. Overhead cranes are useful for handling large and heavy components, allowing for easy loading and unloading. Robotic arms offer high precision handling and can be programmed to perform specific tasks, such as rotating the workpiece to ensure all surfaces are evenly treated. The workpiece handling system may also include fixtures or holders to keep the components in place during the shot blasting process, especially for complex shaped parts.
2.6 Control Panel
The control panel is the interface between the operator and the shot blast cabinet. It allows the operator to set various parameters, such as the blast wheel speed, the abrasive feeding rate, and the duration of the shot blasting process. In modern shot blast cabinets, the control panel may be a digital interface with touch screen capabilities. This makes it easier for the operator to input and adjust the parameters.
The control panel also provides information about the machine's status, such as the remaining quantity of abrasive in the hopper, the temperature of the dust collection system, and any error messages. Some advanced control panels may also offer features such as preset programs for different types of surface treatment tasks. For example, a pre set program for cleaning automotive engine parts may have specific settings for blast wheel speed, abrasive feeding rate, and shot blasting time. The control panel can also be integrated into a larger plant wide control system, allowing for remote monitoring and control of the shot blast cabinet.
3. Working Principle
The operation of a shot blast cabinet is based on the principle of high velocity abrasive impact.
1. Abrasive Feeding: The abrasive shots are stored in the hopper of the abrasive feeding system. The metering device regulates the flow of shots from the hopper to the center of the blast wheel assembly. The precise control of the shot feeding rate ensures a consistent supply of shots to the blast wheel.
2. Acceleration in the Blast Wheel: Once the shots enter the blast wheel, the rotating disk and its vanes accelerate them to high velocities using centrifugal force. The speed of the blast wheel can be adjusted according to the requirements of the surface treatment process. For example, when removing thick rust from a large steel plate, a higher blast wheel speed may be required to provide sufficient impact energy.
3. Shot Blasting Process in the Cabinet: The high velocity shots are then directed towards the workpiece inside the cabinet. The impact of the shots on the surface of the workpiece removes contaminants such as rust, paint, scale, and burrs. The shots also impart compressive stresses on the surface, which can improve the fatigue resistance and durability of the material. The layout of the blast wheel and the interior of the cabinet are designed to ensure that the shots cover the entire surface of the workpiece as uniformly as possible.
4. Dust Collection: As the shots impact the workpiece, dust is generated. The dust collection system, powered by a fan, creates a negative pressure inside the cabinet. This draws the dust laden air into the ducts, where the dust particles are filtered out, and clean air is released back into the environment. The efficient operation of the dust collection system is crucial for maintaining a clean working environment and for meeting environmental regulations.
5. Workpiece Handling: After the shot blasting process is complete, the workpiece handling system removes the treated workpiece from the cabinet. If there are multiple workpieces to be processed, the handling system ensures the efficient loading and unloading of components, maximizing the productivity of the shot blast cabinet.
4. Applications
4.1 Automotive Industry
In the automotive industry, shot blast cabinets are used for a variety of applications. Engine components, such as cylinder heads, engine blocks, and crankshafts, often need to be cleaned and surface treated. Shot blasting can effectively remove casting sand, rust, and machining burrs from these components. The compressive stresses imparted by shot blasting can also improve the fatigue resistance of the engine parts, enhancing their durability.
Automotive body parts, such as doors, hoods, and fenders, are also treated with shot blasting before painting. This helps in achieving a better adhesion of the paint, resulting in a more durable and aesthetically pleasing finish. In the restoration of classic cars, shot blasting is a preferred method for removing old paint and rust without causing damage to the underlying metal, preserving the historical value of the vehicle.
4.2 Aerospace Industry
The aerospace industry has strict quality and safety requirements, and shot blast cabinets play a crucial role in meeting these standards. Aircraft components, such as turbine blades, engine casings, and structural parts, are made of high strength materials that require precise surface treatment. Shot blasting can remove surface imperfections, such as oxidation layers and machining marks, improving the aerodynamic performance and fatigue resistance of the components.
Turbine blades, which are subjected to extreme temperatures and mechanical stresses, benefit from shot blasting as it can enhance their resistance to these harsh conditions. The ability of shot blasting to provide a uniform surface finish is crucial in the aerospace industry, where even the slightest surface irregularity can affect the performance and safety of the aircraft.
4.3 Construction Industry
In the construction industry, shot blast cabinets are used for cleaning and preparing steel structures. Bridges, buildings, and industrial facilities often have steel components that need to be free of rust, scale, and other contaminants before painting or coating. Shot blasting can effectively remove these impurities, ensuring better adhesion of the protective coatings.
This helps in prolonging the lifespan of the structures and preventing corrosion. In the production of pre fabricated concrete elements, shot blasting can be used to clean and texture the surfaces, improving the bond between the concrete and other materials, such as steel reinforcement bars.
4.4 Artisanal and Small Scale Metalwork
In artisanal metalwork and small scale workshops, shot blast cabinets are used for a variety of creative and functional purposes. Jewelry makers may use small scale shot blast cabinets to create unique surface finishes on metal jewelry pieces. The controlled shot blasting process can add a textured or satin like finish to the jewelry, enhancing its aesthetic appeal.
Small scale metal fabricators may use shot blasting to clean and finish custom made metal parts, such as decorative ironwork or small scale machinery components. The ability to achieve a high quality surface finish in a small scale, cost effective manner makes shot blast cabinets a valuable tool in these settings.
5. Advantages
5.1 High Precision Surface Treatment
Shot blast cabinets offer high precision surface treatment. The controlled environment of the cabinet allows for precise control of the shot blasting process, ensuring consistent results. The ability to adjust parameters such as blast wheel speed, abrasive feeding rate, and shot blasting time enables the operator to customize the surface treatment process according to the specific requirements of the workpiece. This precision is crucial for applications where surface quality is of utmost importance, such as in the aerospace and automotive industries.
5.2 Versatility
These cabinets are highly versatile and can be used on a wide range of materials, including steel, aluminum, cast iron, and even some non metallic materials. They can perform various surface treatment tasks, such as cleaning, descaling, deburring, and surface hardening. The ability to use different types of abrasive media, such as steel shot, aluminum oxide, or glass beads, further expands the versatility of shot blast cabinets. For example, glass beads can be used for a more delicate surface finish on soft metals or for removing paint from sensitive components.
5.3 Cost Effectiveness in the Long Run
Although the initial investment in a shot blast cabinet can be significant, it is cost effective in the long run. The ability to recycle the abrasive media reduces the ongoing cost of the surface treatment process. The high efficiency of the shot blasting process also reduces the labor cost associated with manual surface treatment methods. Additionally, the improved surface quality and durability of the treated workpieces can lead to cost savings in terms of reduced maintenance and replacement costs over time.
5.4 Safety and Environmentally Friendly Operation
Shot blast cabinets provide a safe working environment as the cabinet enclosure contains the high velocity shots, protecting the operator from potential injuries. The dust collection system helps in maintaining a clean working environment and reduces the environmental impact of the shot blasting process. By trapping the dust particles, the system prevents them from being released into the atmosphere, which is beneficial for both the operator's health and the environment.
6. Challenges
6.1 High Initial Investment
The purchase and installation of a shot blast cabinet can be a substantial capital investment. The cost of the cabinet, including all its components such as the blast wheel assembly, abrasive feeding system, dust collection system, and workpiece handling system, can range from a few thousand dollars for a small benchtop model to hundreds of thousands of dollars for a large industrial scale cabinet. In addition, there are costs associated with infrastructure development, such as a suitable workspace with proper ventilation, electrical systems to power the machine, and safety measures. Small and medium sized enterprises may find it difficult to afford such high cost equipment, which can limit their growth and competitiveness in the market.
6.2 Maintenance Requirements
Shot blast cabinets require regular maintenance to ensure their optimal performance. The blast wheel vanes, which are constantly in contact with the high velocity shots, need to be replaced periodically due to wear and tear. The abrasive feeding system may also experience clogging or other mechanical issues that require maintenance. The dust collection system filters need to be cleaned or replaced regularly to maintain their efficiency. Maintenance can be time consuming and costly, and any downtime due to maintenance can affect the production schedule.
6.3 Limited Workpiece Size and Shape Compatibility
The size and shape of the workpiece can pose challenges in shot blast cabinets. Larger workpieces may not fit inside the cabinet, or it may be difficult to ensure uniform shot blasting coverage. Complex shaped workpieces may also require special fixtures or multiple re positionings to ensure all surfaces are treated. In some cases, the design of the cabinet may need to be customized to accommodate specific workpiece sizes and shapes, which can add to the cost and complexity of the operation.
6.4 Operator Training
Operating a shot blast cabinet effectively requires proper training. The operator needs to understand how to set the correct parameters, such as the blast wheel speed, the abrasive feeding rate, and the shot blasting time. Incorrect settings can lead to under treatment or over treatment of the workpieces, resulting in poor product quality. The operator also needs to be aware of safety procedures, such as wearing appropriate personal protective equipment and following proper loading and unloading procedures. Lack of proper training can lead to accidents and reduced productivity.
7. Future Trends
7.1 Integration of Automation and Smart Technologies
The future of shot blast cabinets lies in the integration of automation and smart technologies. Automated workpiece handling systems, such as robotic arms and conveyor belts, can be integrated with the shot blast cabinet to improve the efficiency of the production process. Smart sensors can be installed on the machine to monitor various parameters, such as the wear of the blast wheel vanes, the amount of abrasive in the hopper, and the performance of the dust collection system. This data can be analyzed using artificial intelligence and machine learning algorithms to predict maintenance needs, optimize the shot blasting process, and improve overall efficiency.
7.2 Development of Environmentally Friendly Abrasives and Processes
As environmental concerns become more prominent, there will be a growing focus on developing environmentally friendly abrasives and shot blasting processes. New types of biodegradable or recyclable abrasives may be developed, reducing the environmental impact of the shot blasting process. The dust collection and waste management systems of the shot blast cabinet will also be improved to meet stricter environmental regulations. For example, more efficient dust collection technologies may be developed to reduce the amount of dust emissions, and better recycling methods for used abrasive media may be implemented.
7.3 Customization and Modularity
In response to the increasing demand for specialized products in various industries, shot blast cabinets will likely become more customizable and modular. Manufacturers will be able to offer modular designs that can be easily configured or expanded to meet the specific requirements of different applications. This may involve the development of interchangeable blast wheel assemblies, abrasive feeding systems, and workpiece handling mechanisms. Custom built shot blast cabinets can be designed to accommodate unique workpiece sizes, shapes, and surface treatment requirements, providing a more tailored solution for different industries.
In conclusion, shot blast cabinets are an essential tool in the industrial surface treatment landscape. Their components, working principle, wide ranging applications, numerous advantages, and the challenges they face all contribute to their significance in modern manufacturing. With the advent of new technologies and the evolving demands of various industries, shot blast cabinets are set to undergo further advancements, continuing to play a pivotal role in the production of high quality components.