Hotline
+86-136 8495 9862
Email:cennia@szmizhi.com
Add::104,Building 27,Third Industrial Zone, Longxi Community,Longgang District,Shenzhen,China.
Coil Forming & Handling Equipment
Surface Treatment Equipment
Solutions
Application
About Us
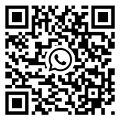
Welcome to MIZHI
For consultation/feedback, please call the service hotline: +86-136 8495 9862 Email:cennia@szmizhi.com
I. Introduction
In the world of surface preparation and finishing, shot blast glass beads have emerged as a popular and effective solution. These small, spherical beads are made of glass and are used in a process called shot blasting to clean, roughen, or decorate various surfaces. In this in-depth exploration, we will take a closer look at shot blast glass beads, their properties, applications, benefits, and the role they play in different industries.
II. History and Evolution of Shot Blast Glass Beads
The use of glass beads for surface treatment can be traced back to ancient times. In early civilizations, glass was used for decorative purposes, and over time, its applications expanded to include surface finishing. The modern process of shot blasting with glass beads began to develop in the early 20th century, as industries sought more efficient and effective ways to prepare surfaces for painting, coating, or other finishing processes.
Today, shot blast glass beads are widely used in a variety of industries, including automotive, aerospace, construction, and manufacturing. They have become an essential tool for achieving high-quality surface finishes and ensuring the durability and performance of products.
III. Properties of Shot Blast Glass Beads
1. Size and Shape: Shot blast glass beads are typically small and spherical in shape, with diameters ranging from a few micrometers to several millimeters. The uniform size and shape of these beads ensure consistent surface treatment and a smooth finish.
2. Hardness: Glass beads are relatively hard, with a Mohs hardness of around 6-7. This hardness allows them to effectively remove contaminants and roughen surfaces without causing excessive damage.
3. Density: The density of shot blast glass beads is lower than that of many other abrasive materials, which makes them easier to handle and less likely to cause damage to delicate surfaces.
4. Chemical Resistance: Glass beads are highly resistant to most chemicals, making them suitable for use in a wide range of applications where exposure to corrosive substances is a concern.
5. Recyclability: Shot blast glass beads can be recycled and reused multiple times, reducing waste and environmental impact.
IV. Applications of Shot Blast Glass Beads
1. Surface Preparation for Painting and Coating: Shot blast glass beads are commonly used to prepare surfaces for painting or coating. The beads remove contaminants, rust, and old coatings, while also creating a rough surface that promotes better adhesion of the new finish.
2. Deburring and Deflashing: In manufacturing processes, glass beads can be used to remove burrs and flash from metal parts, improving the quality and appearance of the finished product.
3. Cleaning and Polishing: Glass beads can be used to clean and polish various surfaces, including metal, plastic, and glass. The gentle abrasion of the beads removes dirt, stains, and oxidation, leaving a smooth and shiny finish.
4. Decorative Finishing: Shot blast glass beads can be used to create decorative finishes on a variety of materials, such as glass, metal, and stone. The beads can be applied in different colors and sizes to create unique patterns and textures.
5. Aerospace and Automotive Industries: In the aerospace and automotive industries, shot blast glass beads are used to prepare surfaces for painting, coating, and bonding. The beads help to ensure the adhesion and durability of these finishes, which are essential for the safety and performance of aircraft and vehicles.
V. Benefits of Using Shot Blast Glass Beads
1. High-Quality Finish: Shot blast glass beads provide a smooth and uniform finish, free from defects and imperfections. This makes them ideal for applications where a high-quality surface finish is required.
2. Minimal Surface Damage: Due to their low density and hardness, glass beads cause minimal surface damage compared to other abrasive materials. This is particularly important for delicate surfaces or parts that require precision finishing.
3. Environmentally Friendly: Glass beads are recyclable and can be reused multiple times, reducing waste and environmental impact. Additionally, the process of shot blasting with glass beads generates less dust and debris than other surface treatment methods, making it a cleaner and more sustainable option.
4. Cost-Effective: Shot blast glass beads are relatively inexpensive compared to other abrasive materials, and their recyclability makes them a cost-effective solution in the long run.
5. Versatility: Glass beads can be used on a wide range of surfaces and materials, making them a versatile tool for various applications. They can be adjusted to different sizes and hardness levels to meet the specific needs of each project.
VI. Choosing the Right Shot Blast Glass Beads
When choosing shot blast glass beads, there are several factors to consider to ensure the best results for your specific application.
1. Surface Material: Consider the type of surface you will be treating. Different materials may require different sizes and hardness levels of glass beads to achieve the desired finish.
2. Finish Requirements: Determine the desired finish, such as a smooth or textured surface. This will help you choose the appropriate size and shape of glass beads.
3. Application Method: Consider the method of application, such as air blasting or wheel blasting. Different application methods may require different types of glass beads.
4. Environmental Considerations: If environmental sustainability is a concern, choose glass beads that are recyclable and generate less dust and debris.
5. Cost: Consider the cost of the glass beads and the overall cost-effectiveness of the surface treatment process.
VII. Storage and Handling of Shot Blast Glass Beads
Proper storage and handling of shot blast glass beads are essential to ensure their quality and performance. Here are some tips for storing and handling glass beads:
1. Store in a Dry Place: Glass beads should be stored in a dry environment to prevent moisture absorption, which can affect their performance.
2. Keep Containers Sealed: Store glass beads in sealed containers to prevent contamination and loss of beads.
3. Handle with Care: When handling glass beads, use proper safety equipment and avoid dropping or spilling the beads, as they can cause injury.
4. Clean Equipment: After using glass beads, clean the shot blasting equipment to remove any remaining beads and prevent clogging.
VIII. Safety Considerations When Using Shot Blast Glass Beads
When using shot blast glass beads, it is important to follow proper safety procedures to protect yourself and others. Here are some safety considerations:
1. Personal Protective Equipment: Wear appropriate personal protective equipment, such as safety glasses, ear protection, and a dust mask, to protect yourself from flying beads and dust.
2. Ventilation: Ensure proper ventilation in the work area to remove dust and fumes generated during the shot blasting process.
3. Equipment Maintenance: Regularly inspect and maintain the shot blasting equipment to ensure its safe operation.
4. Training: Provide proper training to operators on the safe use of shot blasting equipment and glass beads.
IX. Shot Blast Compressor: Powering the Shot Blasting Process
A shot blast compressor is an essential component of the shot blasting process. It provides the compressed air needed to propel the shot blast glass beads or other abrasive materials onto the surface being treated. In this section, we will take a closer look at shot blast compressors, their types, features, and considerations when choosing one for your application.
X. Types of Shot Blast Compressors
1. Reciprocating Compressors: Reciprocating compressors are a common type of shot blast compressor. They use a piston and cylinder mechanism to compress air. Reciprocating compressors are available in different sizes and capacities, making them suitable for a wide range of shot blasting applications.
2. Rotary Screw Compressors: Rotary screw compressors are another popular choice for shot blasting. They use two intermeshing screws to compress air. Rotary screw compressors are known for their high efficiency, reliability, and continuous operation.
3. Portable Compressors: For smaller shot blasting applications or on-site work, portable compressors are a convenient option. These compressors are lightweight and easy to transport, making them ideal for jobs that require mobility.
XI. Features of Shot Blast Compressors
1. Capacity: The capacity of a shot blast compressor is measured in cubic feet per minute (CFM) and determines the amount of compressed air it can deliver. Choose a compressor with a capacity that meets the requirements of your shot blasting equipment and application.
2. Pressure: The pressure output of a compressor is measured in pounds per square inch (PSI) and determines the force with which the abrasive materials are propelled onto the surface. Choose a compressor with the appropriate pressure for your specific application.
3. Reliability: Look for a compressor that is reliable and built to withstand the demands of continuous operation in a shot blasting environment. Consider factors such as durability, quality of components, and ease of maintenance.
4. Energy Efficiency: Energy-efficient compressors can help reduce operating costs and environmental impact. Look for compressors that are designed to minimize energy consumption while still providing the required performance.
5. Noise Level: Shot blast compressors can be noisy, so consider the noise level when choosing one for your application. Look for compressors with noise reduction features or choose a location for the compressor that minimizes noise disturbance.
XII. Choosing the Right Shot Blast Compressor
When choosing a shot blast compressor, consider the following factors:
1. Application Requirements: Determine the specific requirements of your shot blasting application, including the size and type of equipment, the amount of abrasive material being used, and the desired pressure and flow rate.
2. Compressor Capacity: Choose a compressor with a capacity that meets or exceeds the requirements of your application. Consider future expansion or changes in your operations when determining the appropriate capacity.
3. Pressure and Flow Rate: Ensure that the compressor can provide the required pressure and flow rate for your shot blasting equipment. Consult the manufacturer's specifications of your equipment to determine the appropriate pressure and flow rate.
4. Reliability and Durability: Look for a compressor that is reliable and durable, with a reputation for quality and performance. Consider factors such as brand reputation, customer reviews, and warranty.
5. Energy Efficiency: Consider the energy consumption of the compressor and choose one that is energy-efficient to reduce operating costs and environmental impact.
6. Noise Level: If noise is a concern, choose a compressor with low noise levels or consider noise reduction measures such as enclosures or silencers.
7. Maintenance and Service: Consider the ease of maintenance and availability of service and support for the compressor. Look for a compressor that is easy to maintain and has a network of service providers in your area.
XIII. Maintenance and Care of Shot Blast Compressors
Proper maintenance and care of your shot blast compressor are essential to ensure its reliable operation and longevity. Here are some tips for maintaining your compressor:
1. Regular Inspections: Perform regular inspections of your compressor to check for signs of wear and tear, leaks, or other issues. Inspect the filters, hoses, valves, and other components for proper functioning.
2. Filter Maintenance: Clean or replace the air filters regularly to ensure proper air flow and prevent contaminants from entering the compressor. Follow the manufacturer's recommendations for filter maintenance.
3. Lubrication: Lubricate the moving parts of the compressor according to the manufacturer's instructions. Use the appropriate lubricant and ensure proper lubrication levels to reduce friction and wear.
4. Cooling System Maintenance: If your compressor has a cooling system, ensure that it is functioning properly. Clean the cooling fins and check the coolant levels regularly.
5. Storage: When not in use, store the compressor in a dry, clean, and protected area. Cover the compressor to prevent dust and moisture from entering.
6. Professional Maintenance: Consider having your compressor serviced by a professional technician on a regular basis. This can help detect and address potential issues before they become major problems and ensure the optimal performance of your compressor.
Shot blast glass beads and shot blast compressors are essential tools for surface preparation and finishing. By understanding the properties, applications, benefits, and considerations of these products, you can choose the right combination for your specific needs and achieve high-quality results. Whether you are in the automotive, aerospace, construction, or manufacturing industry, shot blast glass beads and compressors can help you improve the quality and durability of your products while reducing costs and environmental impact. With proper storage, handling, and maintenance, these tools can provide years of reliable service and help you stay competitive in your industry.