Hotline
+86-136 8495 9862
Email:cennia@szmizhi.com
Add::104,Building 27,Third Industrial Zone, Longxi Community,Longgang District,Shenzhen,China.
Coil Forming & Handling Equipment
Surface Treatment Equipment
Solutions
Application
About Us
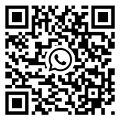
Welcome to MIZHI
For consultation/feedback, please call the service hotline: +86-136 8495 9862 Email:cennia@szmizhi.com
1. Introduction
In the vast and intricate landscape of industrial surface treatment, shot blast grit serves as a fundamental and often under appreciated element. Shot blasting is a process that involves propelling abrasive materials, known as shot blast grit, at high velocities onto the surface of a workpiece. This high energy impact is a game changer for a multitude of industries, from manufacturing and construction to automotive and aerospace. The grit, with its diverse range of materials, shapes, and sizes, plays a pivotal role in determining the quality, efficiency, and cost effectiveness of the shot blasting process. Understanding the nuances of shot blast grit is essential for optimizing surface preparation, enhancing product performance, and ensuring the longevity of industrial components.
2. Types of Shot Blast Grit
2.1 Steel Shot
Steel shot is one of the most commonly used types of shot blast grit. It is typically made from high carbon steel and is heat treated to achieve the desired hardness and toughness. Steel shot comes in a variety of sizes, usually ranging from 0.1mm to 2.5mm in diameter. The spherical shape of steel shot provides a consistent and uniform impact on the workpiece surface.
One of the primary advantages of steel shot is its high density and hardness. This allows it to deliver a powerful impact, making it highly effective in removing heavy duty contaminants such as thick rust, scale, and old paint coatings. In the shipbuilding industry, for example, steel shot is used to clean the hulls of ships. The tough exterior of the ships, which is often covered in layers of marine based corrosion and paint, requires a grit with significant force to remove these contaminants effectively. Steel shot's ability to withstand repeated impacts without breaking down also makes it suitable for high volume, continuous shot blasting operations.
2.2 Cast Iron Grit
Cast iron grit is another popular choice for shot blasting applications. It is made from cast iron and is available in angular or irregular shapes. The angular nature of cast iron grit gives it a cutting like action when it impacts the workpiece surface. This makes it particularly useful for applications where aggressive surface cleaning and material removal are required.
Cast iron grit is often used in the foundry industry to clean metal castings. The rough surface of castings, which may have sand, scale, and other impurities from the casting process, can be effectively cleaned using cast iron grit. The angular particles can penetrate into the crevices and irregularities of the casting surface, removing the contaminants more efficiently than spherical shot. However, cast iron grit is relatively brittle compared to steel shot. This means that it may break down more quickly during the shot blasting process, leading to a higher consumption rate.
2.3 Aluminum Oxide Grit
Aluminum oxide grit is a non metallic abrasive that is widely used in shot blasting, especially for applications where a more delicate touch is required. It is made from aluminum oxide, which can be further classified into different grades based on its purity and hardness. Aluminum oxide grit comes in various shapes, including angular and spherical, depending on the manufacturing process.
The high hardness of aluminum oxide makes it suitable for treating hard materials such as stainless steel, titanium, and high alloy steels. It can effectively remove surface contaminants and create a smooth, clean surface finish. In the aerospace industry, aluminum oxide grit is used to clean and prepare the surfaces of aircraft components. These components often require a high quality surface finish to ensure optimal performance and safety. The non metallic nature of aluminum oxide grit also makes it ideal for applications where there is a risk of contamination from metallic abrasives, such as in the electronics industry.
2.4 Glass Beads
Glass beads are a unique type of shot blast grit. They are made from high quality glass and are spherical in shape. Glass beads are known for their relatively soft nature compared to metal based grits. This makes them suitable for applications where a gentle surface treatment is required.
Glass beads are often used in the automotive industry for surface finishing operations. They can be used to create a smooth, satin like finish on automotive parts, such as engine components and body panels. The spherical shape of glass beads also allows for a more uniform distribution of impact energy, reducing the risk of surface damage. In addition, glass beads are non conductive and non magnetic, making them suitable for applications where these properties are important, such as in the electronics and jewelry industries.
3. Selection Criteria for Shot Blast Grit
3.1 Material of the Workpiece
The material of the workpiece is a crucial factor in selecting the appropriate shot blast grit. Different materials have different hardness levels and surface sensitivities. For example, when treating a soft metal like aluminum, a more delicate abrasive such as glass beads or fine sized aluminum oxide grit may be preferred. Using a hard and aggressive grit like cast iron grit on aluminum could cause surface damage, such as scratching or pitting.
On the other hand, for hard materials like high strength steel, a more robust and hard wearing grit like steel shot or coarse sized aluminum oxide grit is required. These grits can effectively remove contaminants and perform surface hardening operations on the steel. In the case of non metallic materials, such as plastics or ceramics, the choice of grit needs to be carefully considered to avoid damage to the material.
3.2 Desired Surface Finish
The desired surface finish is another key consideration. If a smooth, polished surface is required, spherical shaped grits like glass beads or fine sized steel shot are more suitable. These grits can create a uniform and smooth surface by evenly distributing the impact energy. For example, in the production of decorative metal products, glass beads can be used to achieve a high quality, mirror like finish.
However, if the goal is to create a rough surface for better adhesion of coatings or to perform surface hardening operations, angular shaped grits like cast iron grit or coarse sized aluminum oxide grit are more appropriate. The angular particles can create a micro roughened surface, which is ideal for improving the bonding strength of paints, primers, and other coatings.
3.3 Cost Efficiency
Cost efficiency is an important factor in the selection of shot blast grit. The cost of the grit includes not only the initial purchase price but also the consumption rate and the cost of disposal. For example, steel shot, although more expensive initially, may be more cost effective in the long run for high volume applications due to its durability and recyclability. It can be reused multiple times before it needs to be replaced, reducing the overall cost per unit of surface treatment.
In contrast, cast iron grit, which is relatively inexpensive but brittle, may have a higher consumption rate as it breaks down more quickly during the shot blasting process. This can lead to higher overall costs, especially for long term, continuous operations. The cost of disposal also needs to be considered. Some non metallic grits, such as aluminum oxide, may be more environmentally friendly and easier to dispose of, which can save on disposal costs.
4. Role of Shot Blast Grit in Different Industries
4.1 Automotive Industry
In the automotive industry, shot blast grit is used in multiple stages of production. During the manufacturing of engine components, such as cylinder heads, crankshafts, and camshafts, shot blasting with steel shot or aluminum oxide grit is used to remove casting sand, scale, and other impurities. This not only cleans the surface but also improves the fatigue resistance of the components by inducing compressive stresses.
For automotive body parts, glass beads or fine sized steel shot may be used for surface finishing operations. The smooth surface finish obtained from these grits is important for aesthetic reasons and also for improving the adhesion of paint. A well prepared surface ensures that the paint adheres firmly, reducing the risk of peeling and corrosion.
4.2 Aerospace Industry
The aerospace industry has extremely high quality standards, and shot blast grit plays a critical role in meeting these requirements. Aerospace components, such as turbine blades, landing gear parts, and aircraft structural components, are often treated with shot blasting. Aluminum oxide grit is commonly used due to its high hardness and ability to clean and harden the surface of high strength materials.
Turbine blades, which are exposed to high temperatures, mechanical stress, and corrosive environments, require a surface treatment that can enhance their fatigue resistance and corrosion resistance. Shot blasting with aluminum oxide grit can create a compressive stressed surface layer, which helps to prevent the formation of cracks and extends the lifespan of the blades.
4.3 Construction Industry
In the construction industry, shot blast grit is used for surface preparation of steel structures. Steel beams, columns, and bridges are often shot blasted with steel shot or cast iron grit to remove rust, mill scale, and other contaminants. This is essential for ensuring the integrity of the structures and for providing a good base for the application of protective coatings.
Shot blasting can also be used to clean and prepare the surface of concrete floors and walls. In the case of concrete, aluminum oxide grit or other non metallic abrasives may be used to remove surface contaminants and create a rough surface for better adhesion of coatings or adhesives.
5. Recycling and Environmental Considerations
5.1 Recycling of Shot Blast Grit
Recycling shot blast grit is an important practice in many industries. Steel shot, for example, can be easily recycled. After the shot blasting process, the spent shot is collected, separated from the debris, and then re processed. The recycling process typically involves cleaning the shot to remove any contaminants, followed by heat treatment to restore its hardness and mechanical properties.
Recycling shot blast grit not only reduces the cost of the grit but also has a positive environmental impact. It reduces the demand for new raw materials, which in turn reduces the energy and resources required for manufacturing new grit. In addition, recycling helps to minimize the amount of waste that needs to be disposed of, reducing the environmental burden.
5.2 Environmental Impact of Shot Blast Grit
The environmental impact of shot blast grit depends on several factors, including the type of grit, the shot blasting process, and the disposal methods. Some types of grit, such as cast iron grit, may produce more dust during the shot blasting process. This dust can be harmful to the environment and human health if not properly controlled.
To mitigate the environmental impact, industries are increasingly adopting dust collection systems and using environmentally friendly grits. For example, the use of non metallic grits like aluminum oxide, which are less likely to produce harmful dust, is becoming more common. In addition, proper disposal methods are being implemented to ensure that the spent grit does not contaminate soil, water, or air.
6. Maintenance and Handling of Shot Blast Grit
6.1 Storage and Handling
Proper storage and handling of shot blast grit are essential to maintain its quality and performance. Shot blast grit should be stored in a dry, clean environment to prevent contamination and corrosion. Moisture can cause rusting of metal based grits, such as steel shot and cast iron grit, which can affect their performance.
During handling, care should be taken to prevent the grit from being mixed with other materials. Mixing different types of grits can lead to inconsistent results in the shot blasting process. In addition, the equipment used for handling the grit, such as conveyors and hoppers, should be regularly cleaned to prevent the accumulation of debris and contaminants.
6.2 Quality Control
Quality control of shot blast grit is crucial for ensuring consistent results in the shot blasting process. The grit should be regularly inspected for its size, shape, and hardness. For example, if the steel shot becomes worn or deformed over time, it may not deliver the same impact energy, leading to inconsistent surface treatment.
In addition, the cleanliness of the grit should be monitored. Contaminated grit can cause surface defects on the workpiece. Quality control measures may also include testing the grit's performance on sample workpieces to ensure that it meets the required standards.
7. Future Trends in Shot Blast Grit Technology
7.1 Development of New Grit Materials
The future of shot blast grit is likely to see the development of new and improved materials. Nanocomposite materials, for example, may be developed to combine the advantages of different materials at the nanoscale. These materials could potentially offer higher hardness, better wear resistance, and more precise surface treatment capabilities.
In addition, there may be a focus on developing environmentally friendly grits that are biodegradable or made from recycled materials. This would further reduce the environmental impact of the shot blasting process.
7.2 Integration with Advanced Shot Blasting Technologies
Shot blast grit is likely to be integrated more closely with advanced shot blasting technologies. For example, with the development of automated and intelligent shot blasting systems, the grit may be automatically selected and adjusted based on the material and surface requirements of the workpiece. Sensors could be used to monitor the condition of the grit and the shot blasting process, allowing for real time adjustments to ensure optimal performance.
In conclusion, shot blast grit is a vital component in the industrial surface treatment process. Its diverse types, selection criteria, and applications across various industries make it an essential element for achieving high quality surface finishes, improving product performance, and ensuring the longevity of industrial components. As technology continues to evolve, shot blast grit will play an even more significant role in driving innovation and sustainability in the field of surface treatment.