Hotline
+86-136 8495 9862
Email:cennia@szmizhi.com
Add::104,Building 27,Third Industrial Zone, Longxi Community,Longgang District,Shenzhen,China.
Coil Forming & Handling Equipment
Surface Treatment Equipment
Solutions
Application
About Us
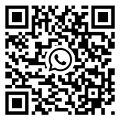
Welcome to MIZHI
For consultation/feedback, please call the service hotline: +86-136 8495 9862 Email:cennia@szmizhi.com
1. Introduction
Shot blast nozzles are fundamental components in the shot blasting process, a technique widely used across numerous industries for surface preparation. Surface preparation is crucial as it removes contaminants, rust, paint, and other unwanted materials from surfaces, creating an ideal substrate for subsequent processes such as painting, coating, or bonding. The shot blast nozzle plays a pivotal role in determining the effectiveness, precision, and efficiency of the entire shot blasting operation. It is the point through which abrasive media, such as steel shot, grit, or glass beads, are propelled at high velocities towards the target surface.
2. Working Principle of Shot Blast Nozzles
2.1. Abrasive Media Propulsion
The core function of a shot blast nozzle is to direct and accelerate the abrasive media towards the surface to be treated. In most shot blasting systems, the abrasive media is fed into a blasting chamber or hose. The nozzle is connected to this system, and as the media enters the nozzle, it is subjected to a force that propels it forward.
In air operated shot blast nozzles, compressed air is the driving force. The compressed air enters the nozzle at a high pressure, typically ranging from 60 120 pounds per square inch (psi). As the air flows through the nozzle, it entrains the abrasive media. The design of the nozzle is such that it creates a Venturi like effect. The constricted section of the nozzle accelerates the air media mixture, increasing its velocity. By the time the mixture exits the nozzle, the abrasive media is traveling at high speeds, often between 100 200 feet per second. This high velocity impact of the media on the surface effectively removes contaminants and modifies the surface texture.
In centrifugal shot blast nozzles, the mechanism is different. Here, a high speed impeller is used to accelerate the abrasive media. The media is fed into the impeller, which rotates at high speeds, typically 10,000 30,000 revolutions per minute. As the impeller spins, the media is flung outwards due to centrifugal force. The nozzle is designed to direct this high velocity media stream towards the target surface. The shape and orientation of the nozzle in a centrifugal system are carefully engineered to ensure that the media is focused and directed precisely where it is needed.
2.2. Nozzle Design and its Impact on Performance
The design of the shot blast nozzle is a critical factor in determining its performance. The internal geometry of the nozzle, such as the diameter of the inlet, the length of the nozzle, and the shape of the outlet, all influence how the abrasive media is accelerated and directed.
A nozzle with a smaller inlet diameter relative to its length will create a more concentrated and high velocity stream of abrasive media. This type of nozzle is suitable for applications where a high impact, focused blast is required, such as removing thick layers of rust or paint from a small area. For example, in the restoration of historical artifacts, a small diameter, long length nozzle can be used to precisely target and clean delicate areas without causing damage to the surrounding parts.
On the other hand, a nozzle with a larger inlet diameter and a shorter length may be used when a wider coverage area is needed. This design allows for a greater volume of abrasive media to be propelled, but at a slightly lower velocity. It is often used in applications like surface preparation of large scale industrial floors or the exterior of buildings, where the goal is to cover a large area quickly while still achieving an effective cleaning and surface roughening.
The shape of the nozzle outlet also matters. A round shaped outlet will produce a circular pattern of abrasive media impact on the surface. However, for some applications, a rectangular or slit shaped outlet may be more suitable. For instance, in the preparation of long, narrow surfaces like metal strips or pipes, a rectangular nozzle can be used to direct the abrasive media in a linear pattern, maximizing the efficiency of the process.
3. Types of Shot Blast Nozzles
3.1. Air Operated Nozzles
3.1.1. Straight Nozzles
Straight air operated nozzles are the most basic type. They have a simple, straight through design where the abrasive media and compressed air mixture travels in a straight line from the inlet to the outlet. These nozzles are widely used in general purpose shot blasting applications. For example, in a small scale metal fabrication shop, straight nozzles can be used to clean and prepare the surfaces of metal parts before welding or painting. They are relatively inexpensive and easy to install and maintain. However, their performance may be limited in terms of the ability to reach difficult to access areas.
3.1.2. Curved Nozzles
Curved air operated nozzles are designed to direct the abrasive media around corners or into confined spaces. The curvature of the nozzle allows for a more flexible blasting operation. In the automotive industry, curved nozzles are often used to clean the internal components of engines or the recessed areas of car body panels. The ability to reach into tight spaces makes them invaluable in applications where straight nozzles would be ineffective. The degree of curvature can vary depending on the specific application requirements, with some nozzles having a gentle curve for slightly angled access and others having a more pronounced curve for reaching deep into complex geometries.
3.1.3. Adjustable Nozzles
Adjustable air operated nozzles offer the flexibility to change the direction and intensity of the abrasive media flow. These nozzles typically have a mechanism that allows the operator to adjust the angle of the nozzle outlet or the size of the orifice through which the media exits. This makes them suitable for applications where the surface to be treated has irregular shapes or where different levels of blasting intensity are required in different areas. For example, in the restoration of statues or sculptures, an adjustable nozzle can be used to vary the blasting force depending on whether the area being treated is a flat surface or a more detailed, delicate area.
3.2. Centrifugal Nozzles
3.2.1. Fixed Angle Centrifugal Nozzles
Fixed angle centrifugal nozzles are designed to direct the abrasive media at a specific, unchanging angle. They are commonly used in large scale industrial applications where a consistent and focused blast pattern is required. In a steel making plant, fixed angle centrifugal nozzles can be used to clean the surfaces of large steel plates or to prepare the molds for casting. The fixed angle design ensures that the abrasive media is always directed in the same way, allowing for efficient and uniform surface treatment. These nozzles are often part of automated shot blasting systems, where the consistency of the blasting process is crucial for high volume production.
3.2.2. Variable Angle Centrifugal Nozzles
Variable angle centrifugal nozzles, as the name implies, can be adjusted to direct the abrasive media at different angles. This type of nozzle is more versatile than the fixed angle version. In the aerospace industry, where components often have complex shapes, variable angle centrifugal nozzles can be used to precisely target different areas of the parts. For example, when preparing the surfaces of aircraft turbine blades, the nozzle can be adjusted to direct the abrasive media at different angles to clean and roughen the various surfaces of the blade, ensuring proper adhesion of protective coatings.
4. Materials Used in Shot Blast Nozzles
4.1. Tungsten Carbide
Tungsten carbide is a popular material for shot blast nozzles due to its exceptional hardness and wear resistance. The high velocity impact of the abrasive media can cause significant wear on the nozzle over time, but tungsten carbide can withstand this abuse much better than many other materials. In applications where the abrasive media is particularly harsh, such as when using steel grit, tungsten carbide nozzles are the preferred choice. They can last significantly longer than nozzles made of other materials, reducing the frequency of nozzle replacements and minimizing downtime in production processes. However, tungsten carbide nozzles are relatively expensive, which may limit their use in some cost sensitive applications.
4.2. Boron Carbide
Boron carbide is another hard wearing material used in shot blast nozzles. It has a high hardness rating and excellent resistance to abrasion. Boron carbide nozzles are often used in applications where a combination of high wear resistance and lightweight is desired. In the electronics industry, for example, where precision and reduced weight of equipment are important, boron carbide nozzles can be used in small scale shot blasting operations. They can effectively clean and prepare the surfaces of electronic components without adding excessive weight to the equipment.
4.3. Ceramic
Ceramic materials, such as alumina ceramic, are also commonly used in shot blast nozzles. Ceramic nozzles offer good wear resistance and are relatively inexpensive compared to tungsten carbide or boron carbide nozzles. They are suitable for applications where the abrasive media is not extremely harsh, such as when using glass beads for surface finishing. Ceramic nozzles are also resistant to corrosion, making them a good choice for applications where the blasting environment may be corrosive, such as in the marine industry. However, they are more brittle than some of the other materials, so they may be more prone to cracking if subjected to sudden impacts or temperature changes.
4.4. Steel
Steel nozzles are the most basic and cost effective option. They are suitable for applications where the abrasive media is relatively soft and the blasting requirements are not too demanding. For example, in a hobbyist level metalworking shop, steel nozzles can be used when using soft abrasive media like walnut shells for gentle surface cleaning. Steel nozzles are easy to manufacture and are widely available. However, they have a relatively short lifespan compared to nozzles made of more wear resistant materials and are more likely to deform or wear out quickly when exposed to harsh abrasive media.
5. Applications of Shot Blast Nozzles
5.1. Automotive Industry
In the automotive industry, shot blast nozzles are used in several crucial applications. Before painting car body panels, shot blasting is used to remove rust, old paint, and contaminants from the surface. Curved and adjustable air operated nozzles are often used to reach the recessed areas and corners of the body panels. This ensures that the entire surface is clean and properly prepared for painting, which improves the adhesion of the paint and extends the lifespan of the finish.
In the manufacturing of engine components, such as cylinder heads and crankshafts, shot blast nozzles are used to clean the surfaces and improve their fatigue resistance. Centrifugal nozzles, with their high velocity and focused blast, can effectively remove machining marks and contaminants from these critical components. The use of tungsten carbide nozzles in this application is common due to the harsh nature of the abrasive media required to clean the hard metal engine parts.
5.2. Construction Industry
The construction industry makes extensive use of shot blast nozzles for surface preparation. In the restoration of old buildings, straight and curved air operated nozzles are used to remove layers of paint, dirt, and grime from brick, stone, and concrete surfaces. This not only restores the appearance of the building but also prepares the surface for repainting or other finishing treatments.
For new construction projects, shot blast nozzles are used to clean and roughen the surfaces of concrete floors before applying coatings or adhesives. Adjustable nozzles can be used to vary the blasting intensity depending on the condition of the concrete surface. In the case of steel structures in construction, such as bridges and buildings, shot blast nozzles are used to remove rust and scale from the steel, ensuring proper adhesion of protective coatings and preventing corrosion.
5.3. Aerospace Industry
In the aerospace industry, shot blast nozzles play a vital role in surface preparation. The surfaces of aircraft components need to be meticulously cleaned and prepared to ensure the safety and performance of the aircraft. Variable angle centrifugal nozzles are used to clean and treat the complex shaped components such as turbine blades, wing spars, and landing gear parts. The ability to precisely control the angle and intensity of the blast is crucial in this industry, as any surface irregularities or contaminants can have serious consequences for the operation of the aircraft.
Shot blast nozzles are also used to create a specific surface texture on aerospace components. This surface texture can enhance the adhesion of coatings, which are used to protect the components from the harsh operating environment of the aircraft, including high temperatures, moisture, and chemical exposure.
5.4. Manufacturing Industry
In the manufacturing industry, shot blast nozzles are used in a wide range of applications. In the production of machinery parts, such as gears, shafts, and bearings, shot blasting is used to remove burrs, scale, and contaminants. The use of appropriate nozzles, such as straight air operated nozzles for general cleaning and centrifugal nozzles for high volume production, ensures that the parts are clean and ready for further processing or assembly.
In the production of consumer products, such as appliances and furniture, shot blast nozzles are used to prepare the metal surfaces for painting or coating. This improves the appearance and durability of the products. The choice of nozzle material, such as ceramic for less abrasive media applications, is important to balance cost and performance in the manufacturing process.
6. Selection Criteria for Shot Blast Nozzles
6.1. Abrasive Media Type
The type of abrasive media used in the shot blasting process is a crucial factor in selecting the right nozzle. If the abrasive media is very hard and aggressive, such as steel grit, a nozzle made of a highly wear resistant material like tungsten carbide is required. On the other hand, if the abrasive media is relatively soft, like glass beads or walnut shells, a less expensive material such as ceramic or even steel may be sufficient. The size of the abrasive media particles also matters. Larger particles may require a nozzle with a larger orifice to ensure a smooth flow, while smaller particles can be used with nozzles having smaller openings.
6.2. Surface Treatment Requirements
The specific surface treatment requirements of the application will determine the type of nozzle needed. If the goal is to remove thick layers of rust or paint, a high impact nozzle, such as a straight air operated nozzle with a small orifice for concentrated blast or a high power centrifugal nozzle, is suitable. For delicate surface finishing, where a gentle but effective cleaning is required, a nozzle with a larger orifice and a lower velocity blast, like an adjustable air operated nozzle with a wider outlet, may be more appropriate.
If the surface has complex shapes or hard to reach areas, curved or adjustable nozzles are the way to go. In applications where a uniform surface texture is desired, fixed angle centrifugal nozzles can be used to ensure consistent blasting across the surface.
6.3. Cost Considerations
Cost is always a factor in any industrial decision making process. Tungsten carbide nozzles, while highly effective and durable, are expensive. If the application is not extremely demanding in terms of wear resistance and the budget is tight, a more cost effective option like a ceramic or steel nozzle may be considered. However, it's important to balance the initial cost of the nozzle with its lifespan and the overall cost of the shot blasting operation. A cheaper nozzle that needs to be replaced frequently may end up costing more in the long run due to increased downtime and replacement costs.
6.4. Compatibility with Shot Blasting Equipment
The nozzle must be compatible with the existing shot blasting equipment. This includes factors such as the type of blasting system (air operated or centrifugal), the pressure of the compressed air (in air operated systems), and the power of the impeller (in centrifugal systems). The connection between the nozzle and the blasting equipment also needs to be properly matched to ensure a secure and efficient flow of the abrasive media. If the nozzle is not compatible with the equipment, it can lead to reduced performance, leaks, or even damage to the equipment.
7. Maintenance and Replacement of Shot Blast Nozzles
7.1. Wear and Tear Monitoring
Regular monitoring of the shot blast nozzles for wear and tear is essential. The high velocity impact of the abrasive media can cause the nozzle to wear out over time. Visual inspection is a basic but effective way to check for wear. Signs of wear include a change in the shape of the nozzle outlet, such as elongation or rounding of the edges, and a reduction in the diameter of the orifice. In some cases, the nozzle may also show signs of pitting or erosion on the inner walls.
For more precise monitoring, non destructive testing methods can be used. Ultrasonic testing, for example, can be used to measure the thickness of the nozzle walls. As the nozzle wears, the wall thickness decreases, and ultrasonic testing can detect these changes accurately. This allows for timely replacement of the nozzle before it fails completely and causes disruptions to the shot blasting process.
7.2. Cleaning and Maintenance
Cleaning the shot blast nozzles is an important part of maintenance. After each use, the nozzle should be cleaned to remove any residual abrasive media and debris. This can be done using compressed air or a suitable cleaning solvent. In some cases, the nozzle may need to be disassembled for more thorough cleaning, especially if there are blockages in the internal passages.
Lubrication of any moving parts in the nozzle, such as in adjustable nozzles, is also necessary. Proper lubrication ensures smooth operation and reduces the risk of mechanical failures. However, it's important to use lubricants that are compatible with the abrasive media and the working environment of the nozzle.
7.3. Replacement Timing
Determining the right time to replace a shot blast nozzle is crucial. As mentioned earlier, monitoring for wear and tear is the key. If the nozzle shows significant signs of wear, such as a large reduction in the thickness of the walls or a substantial change in the shape of the outlet, it should be replaced. In general, nozzles made of more wear resistant materials like tungsten carbide will have a longer lifespan compared to those made of steel or ceramic.
The frequency of replacement also depends on the intensity of use. In high volume, continuous shot blasting operations, nozzles may need to be replaced more frequently than in intermittent or low volume applications. Manufacturers often provide guidelines on the expected lifespan of their nozzles under different operating conditions, which can be used as a reference for replacement timing.
8. Future Trends in Shot Blast Nozzle Technology
8.1. Advanced Material Development
The future of shot blast nozzles is likely to see the development of new and improved materials. Researchers are constantly exploring materials that offer even better wear resistance, higher strength, and improved performance in harsh environments. For example, the development of new composite materials that combine the best properties of different materials, such as the hardness of tungsten carbide and the