Hotline
+86-136 8495 9862
Email:cennia@szmizhi.com
Add::104,Building 27,Third Industrial Zone, Longxi Community,Longgang District,Shenzhen,China.
Coil Forming & Handling Equipment
Surface Treatment Equipment
Solutions
Application
About Us
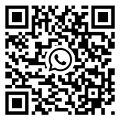
Welcome to MIZHI
For consultation/feedback, please call the service hotline: +86-136 8495 9862 Email:cennia@szmizhi.com
1. Introduction
Shot blast sand, a crucial component in the shot blasting process, plays a fundamental role in various industries for surface preparation. Shot blasting is a widely used technique that involves propelling abrasive materials at high velocities onto a surface to clean, smooth, roughen, or otherwise modify it. Shot blast sand, along with other abrasive media like steel shot and grit, has become an integral part of manufacturing, construction, automotive, and many other sectors. This article delves into the types, properties, applications, and environmental considerations related to shot blast sand.
2. Types of Shot Blast Sand
2.1. Natural Silica Sand
Natural silica sand is one of the most common types of shot blast sand. It is derived from natural deposits of sand, which are mainly composed of silicon dioxide (SiO₂). Silica sand has been used in shot blasting for decades due to its availability and relatively low cost. The sand grains are typically angular to sub angular in shape. This shape provides good cutting and scraping action when propelled at high speeds onto a surface.
The size of silica sand used for shot blasting can vary. Fine grained silica sand, with particle sizes ranging from 0.1 to 0.5 mm, is often used for delicate surface finishing applications. For example, in the restoration of antique metal artifacts or in the preparation of surfaces for high quality paint finishes on small scale components, fine silica sand can be used to gently remove light contaminants and create a smooth surface texture without causing excessive damage. Coarser silica sand, with particle sizes up to 2 3 mm, is more suitable for heavy duty cleaning tasks. In the construction industry, it can be used to remove thick layers of paint, rust, or scale from large concrete or metal surfaces.
2.2. Garnet Sand
Garnet sand is another popular choice for shot blasting. Garnet is a group of silicate minerals that occur naturally in various colors, including red, orange, and brown. Garnet sand is known for its high hardness, with a Mohs hardness rating typically between 6.5 and 7.5. This hardness makes it highly effective in removing tough contaminants from surfaces.
Garnet sand is often preferred for applications where a more aggressive yet controlled abrasive action is required. In the shipbuilding industry, it is used to clean the hulls of ships. The high velocity impact of garnet sand can effectively remove barnacles, marine growth, and old anti fouling coatings from the ship's hull. The angular shape of garnet particles also helps in creating a rough surface texture, which is beneficial for the proper adhesion of new anti fouling coatings. Garnet sand is also used in the surface preparation of concrete floors in industrial settings. It can quickly remove surface imperfections, laitance, and old coatings, preparing the surface for the application of new floor coatings or overlays.
2.3. Aluminum Oxide Sand
Aluminum oxide sand is an artificial abrasive made from bauxite ore. It is processed to produce fine grained aluminum oxide particles. Aluminum oxide sand is extremely hard, with a Mohs hardness of 9, making it one of the hardest abrasive media available. This high hardness allows it to effectively remove very tough materials, such as hardened paint, thick rust, and scale.
In the automotive industry, aluminum oxide sand is used in the stripping of old paint from car bodies. The high speed impact of the aluminum oxide particles can quickly and efficiently remove multiple layers of paint, preparing the surface for repainting. In the manufacturing of industrial machinery, aluminum oxide sand is used to clean and prepare the surfaces of metal parts before assembly. It can remove machining marks, burrs, and contaminants, ensuring a smooth and clean surface for proper fitting and functioning of the parts.
2.4. Olivine Sand
Olivine sand is a type of shot blast sand made from the mineral olivine, which is a magnesium iron silicate. Olivine sand has a relatively high melting point and good thermal stability. It is often used in applications where the surface being blasted may be exposed to high temperatures during subsequent processes.
For example, in the foundry industry, olivine sand can be used to clean the surfaces of cast metal parts. The high temperature resistance of olivine sand ensures that it does not break down or fuse with the metal surface during the shot blasting process, even if the part has just been removed from a high temperature casting operation. Olivine sand is also used in some heat treating applications, where the blasted surface needs to maintain its integrity during subsequent heat treatment processes.
3. Properties of Shot Blast Sand
3.1. Hardness
The hardness of shot blast sand is a critical property that determines its effectiveness in removing contaminants and modifying surfaces. As mentioned earlier, different types of shot blast sand have varying hardness levels. Harder sands, such as aluminum oxide sand, are more suitable for removing tough materials, while softer sands like natural silica sand can be used for more delicate applications.
The hardness of the sand also affects the wear rate of the shot blasting equipment, including the nozzles and the blasting chamber. Harder sands will cause more wear on the equipment over time, but they are also more efficient in performing heavy duty surface preparation tasks. Manufacturers need to balance the choice of sand based on the surface treatment requirements and the cost of equipment maintenance.
3.2. Grain Shape
The shape of the sand grains has a significant impact on the shot blasting process. Angular shaped sand grains, like those of garnet and some types of natural silica sand, provide a more aggressive cutting and scraping action. When they impact the surface, the sharp edges of the angular grains can effectively break down and remove contaminants.
In contrast, rounded sand grains, such as those in some specially processed silica sands, have a more peening like effect. They are more suitable for applications where the goal is to smooth the surface or to induce compressive stresses in the surface layer, rather than to remove large amounts of material. For example, in the peening of metal parts to improve their fatigue resistance, rounded sand grains can be used to gently impact the surface, causing a beneficial change in the surface layer properties without significant material removal.
3.3. Particle Size Distribution
The particle size distribution of shot blast sand is another important property. A well controlled particle size distribution ensures consistent performance in the shot blasting process. Sands with a narrow particle size range will produce a more uniform blasting effect. For example, if a fine grained sand with a tightly controlled particle size is used for surface finishing, it will result in a more consistent surface texture across the treated area.
On the other hand, a wider particle size distribution may be used in some applications to achieve a combination of different effects. Coarser particles can be used for initial material removal, while finer particles can be used for subsequent surface finishing operations. However, a wide particle size distribution requires careful control to ensure that the blasting process remains efficient and does not cause uneven surface treatment.
3.4. Chemical Composition
The chemical composition of shot blast sand can also influence its performance and the applications it is suitable for. For example, natural silica sand, which is mainly composed of SiO₂, may not be suitable for use in environments where silica dust is a health hazard. In such cases, alternative sands like garnet or olivine, which do not produce harmful silica dust, are preferred.
The chemical composition can also affect the interaction between the sand and the surface being blasted. Some sands may react with certain metals or materials, which can be either beneficial or detrimental depending on the application. For instance, in some cases, a mild chemical reaction between the sand and the surface can help in improving the adhesion of subsequent coatings.
4. Applications of Shot Blast Sand
4.1. Manufacturing Industry
In the manufacturing industry, shot blast sand is used in a wide range of applications. In metal fabrication, it is used to clean and prepare the surfaces of metal parts before further processing. For example, before welding metal components, shot blast sand can be used to remove rust, mill scale, and other contaminants from the edges and surfaces to be joined. This ensures a clean and strong weld.
In the production of machinery parts, shot blast sand is used to improve the surface finish and mechanical properties of the parts. By blasting the surfaces with sand, machining marks and burrs can be removed, and the surface can be made smoother. In some cases, the shot blasting process can also induce compressive stresses in the surface layer, which can improve the fatigue resistance of the parts.
4.2. Construction Industry
The construction industry heavily relies on shot blast sand for various surface preparation tasks. In the restoration of old buildings, shot blast sand is used to remove layers of paint, dirt, and grime from brick, stone, and concrete surfaces. This not only restores the original appearance of the building but also prepares the surface for repainting or other finishing treatments.
For new construction projects, shot blast sand is used to clean and roughen the surfaces of concrete floors before applying coatings, adhesives, or overlays. A rough surface created by shot blasting improves the adhesion of these materials, ensuring a long lasting and durable finish. In the case of steel structures in construction, such as bridges and buildings, shot blast sand is used to remove rust and scale from the steel, protecting it from further corrosion and preparing it for the application of protective coatings.
4.3. Automotive Industry
In the automotive industry, shot blast sand is used at several stages of vehicle production. Before painting car body panels, shot blasting with sand is used to remove rust, old paint, and other contaminants from the surface. This ensures proper adhesion of the paint, resulting in a more durable and attractive finish.
Shot blast sand is also used in the manufacturing of engine components. For example, engine blocks and cylinder heads are often blasted with sand to clean the internal and external surfaces. This helps in removing casting residues, machining chips, and other contaminants, ensuring the proper functioning of the engine components.
4.4. Aerospace Industry
The aerospace industry has strict requirements for surface preparation of its components. Shot blast sand is used to clean and prepare the surfaces of aircraft parts, such as landing gear, engine components, and wing structures. The high precision and consistent surface finish achieved by shot blasting with sand are crucial in the aerospace industry.
For example, in the preparation of engine components, shot blast sand can be used to remove any oxidation or contaminants from the surface, ensuring proper fit and function of the parts. The shot blasting process can also be used to create a specific surface texture that enhances the adhesion of coatings, which are used to protect the components from the harsh operating conditions in the aerospace environment, such as high temperatures, moisture, and chemical exposure.
5. Environmental Considerations of Shot Blast Sand
5.1. Dust Generation
One of the major environmental concerns associated with shot blast sand is dust generation. When sand is propelled at high speeds onto a surface, fine particles of dust are produced. In the case of natural silica sand, the dust contains silica particles, which can be a serious health hazard if inhaled. Prolonged exposure to silica dust can lead to respiratory diseases such as silicosis.
To mitigate this issue, modern shot blasting equipment is often equipped with advanced dust collection systems. These systems use methods such as cyclonic separation, bag filtering, and electrostatic precipitation to capture the dust particles before they are released into the atmosphere. In addition, workers in shot blasting areas are required to wear appropriate personal protective equipment, such as respirators, to prevent inhalation of the dust.
5.2. Disposal of Spent Sand
Another environmental consideration is the disposal of spent shot blast sand. After the sand has been used in the shot blasting process, it may be contaminated with the removed materials, such as rust, paint particles, and other contaminants. The disposal of this spent sand needs to comply with environmental regulations.
In some cases, the spent sand can be recycled. For example, if the contaminants are not hazardous, the sand can be processed to remove the contaminants and then reused in the shot blasting process. However, if the spent sand is contaminated with hazardous materials, it needs to be disposed of in a proper hazardous waste disposal facility. This ensures that the environment is not polluted by the disposal of the spent sand.
5.3. Sustainability of Sand Sources
The extraction of natural sands, such as silica sand, for use in shot blasting has implications for the sustainability of sand sources. Over extraction of sand from natural deposits can lead to environmental degradation, including habitat destruction and erosion. To address this issue, there is a growing trend towards using alternative sources of shot blast sand, such as recycled materials or synthetic abrasives.
For example, recycled glass can be processed into an abrasive medium that can be used in shot blasting. This not only reduces the reliance on natural sand sources but also provides a sustainable solution for the disposal of waste glass. Synthetic abrasives, such as aluminum oxide sand, are also a more sustainable option as they are produced from processed minerals rather than relying on natural sand deposits.
6. Selection and Handling of Shot Blast Sand
6.1. Choosing the Right Type of Sand
Selecting the appropriate type of shot blast sand for a specific application is crucial. The choice depends on several factors, including the type of surface to be treated, the nature of the contaminants to be removed, and the desired surface finish. For example, if the surface is made of a soft material and only light cleaning and surface finishing are required, a fine grained, relatively soft sand like natural silica sand may be suitable.
On the other hand, if the surface has thick layers of hardened paint or rust and a more aggressive cleaning action is needed, a harder sand like aluminum oxide or garnet sand should be chosen. The cost of the sand also plays a role in the selection process. Natural silica sand is generally less expensive than synthetic or specialty sands, but it may not be suitable for all applications.
6.2. Storage and Handling
Proper storage and handling of shot blast sand are essential to maintain its quality and performance. Sand should be stored in a dry, covered area to prevent moisture absorption. Moisture can cause the sand grains to clump together, which can affect the flow of the sand through the shot blasting equipment and result in inconsistent blasting performance.
During handling, care should be taken to prevent contamination of the sand. The sand should be transferred using clean equipment, and it should not come into contact with other materials that could affect its abrasive properties. In addition, the sand should be regularly inspected for any signs of degradation, such as excessive wear or contamination, before being used in the shot blasting process.
6.3. Compatibility with Equipment
The shot blast sand must be compatible with the shot blasting equipment. Different types of sand may require different nozzle sizes, blasting pressures, and equipment configurations. For example, a coarser sand may require a larger diameter nozzle to ensure a smooth flow, while a harder sand may require a more robust blasting chamber to withstand the higher impact forces.
Before using a new type of sand in the shot blasting equipment, it is important to consult the equipment manufacturer's guidelines and, if necessary, perform test runs to ensure proper compatibility. This helps to optimize the performance of the shot blasting process and prevent damage to the equipment.
7. Future Trends in Shot Blast Sand Technology
7.1. Development of Sustainable Abrasives
As environmental concerns continue to grow, there will be an increasing focus on the development of sustainable shot blast sands. This includes the further exploration and utilization of recycled materials as abrasive media. For example, recycled ceramics, plastics, and even waste materials from other industries may be processed into effective shot blast sands.
In addition, the development of new synthetic abrasives with improved environmental profiles is expected. These synthetic abrasives may be designed to be more energy efficient to produce, have a longer lifespan, and generate less waste during the shot blasting process. The use of such sustainable abrasives will not only reduce the environmental impact of shot blasting but also contribute to the overall circular economy.
7.2. Advanced Particle Engineering
Future research may lead to advanced particle engineering of shot blast sands. This could involve the development of sand particles with customized shapes, sizes, and surface properties. For example, particles could be engineered to have a specific shape that maximizes their abrasive efficiency while minimizing wear on the shot blasting equipment.
Advanced particle engineering may also involve the development of composite particles, which combine different materials to achieve unique properties. These composite particles could offer enhanced performance in terms of hardness, chemical resistance, and the ability to interact with specific surfaces in a more controlled manner.
7.3. Integration with Smart Shot Blasting Systems
Shot blast sand technology is likely to be integrated with smart shot blasting systems in the future. These systems may use sensors to monitor the condition of the sand during the shot blasting process, such as its particle size distribution, wear rate, and contamination level. Based on this real time data, the system could automatically adjust the blasting parameters, such as the blasting pressure, the flow rate of the sand, or the type of sand being used.
For example, if the sensor detects that the sand is becoming too worn or contaminated, the system could automatically switch to a fresh batch of sand or adjust the blasting pressure to compensate for the reduced abrasive performance. This integration of shot blast sand with smart systems will improve the efficiency and quality of the shot blasting process.
8. Conclusion
Shot blast sand is an essential component in the shot blasting process, with a wide range of applications across multiple industries. The different types of shot blast sand, each with its unique properties, offer flexibility in surface preparation tasks. However, environmental considerations, such as dust generation and sustainable sand sources, need to be carefully addressed. By making informed choices in the selection, handling, and disposal of shot blast sand, and by embracing future trends in technology, industries can continue to benefit from the effective surface treatment capabilities of shot blast sand while minimizing their environmental impact.