Hotline
+86-136 8495 9862
Email:cennia@szmizhi.com
Add::104,Building 27,Third Industrial Zone, Longxi Community,Longgang District,Shenzhen,China.
Coil Forming & Handling Equipment
Surface Treatment Equipment
Solutions
Application
About Us
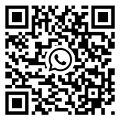
Welcome to MIZHI
For consultation/feedback, please call the service hotline: +86-136 8495 9862 Email:cennia@szmizhi.com
1. Introduction
In the intricate world of industrial manufacturing and metalworking, surface treatment is a fundamental process that significantly impacts the quality, durability, and performance of products. The shot blast unit stands as a cornerstone technology in this domain, offering a highly effective method for cleaning, strengthening, and finishing the surfaces of a diverse range of materials. Whether it's removing rust from steel components, enhancing the fatigue resistance of aerospace parts, or creating a smooth finish on decorative metalwork, shot blast units play a crucial role. This comprehensive exploration will delve into every aspect of shot blast units, including their components, working principles, applications, advantages, challenges, and future trends.
2. Components of a Shot Blast Unit
2.1 Blast Wheel Assembly
The blast wheel assembly is the heart of the shot blast unit. It is responsible for imparting high velocities to the abrasive shots, which are the key agents in the surface treatment process. The blast wheel consists of a rapidly rotating disk, typically driven by a powerful electric motor. Mounted on the disk are a series of precisely engineered vanes. These vanes are designed to receive the abrasive shots at the center of the disk and then, through centrifugal force, accelerate them to speeds that can range from several hundred to over a thousand feet per second.
The speed of the blast wheel is a critical parameter. It can be adjusted based on the specific requirements of the surface treatment task. For example, when dealing with heavy duty cleaning of large scale industrial components, a higher blast wheel speed may be necessary to provide the necessary impact energy to remove thick layers of rust, scale, or old paint. On the other hand, for more delicate surface finishing operations, such as on precision machined parts or high value decorative items, a lower blast wheel speed is used to avoid over treatment and potential damage to the workpiece.
The vanes on the blast wheel are made of materials with excellent wear resistance properties. High chromium cast iron is a common choice due to its ability to withstand the continuous impact of the high velocity shots. Over time, the vanes will experience wear and tear, and they need to be periodically inspected and replaced. Some advanced blast wheel designs incorporate quick change mechanisms for the vanes, reducing the downtime associated with maintenance.
2.2 Abrasive Feeding System
The abrasive feeding system is tasked with supplying the abrasive shots to the blast wheel in a controlled and consistent manner. It typically starts with a hopper, which serves as a storage reservoir for the abrasive media. The hopper is designed to hold a sufficient quantity of shots to ensure continuous operation of the shot blast unit for an extended period without the need for frequent refilling.
A metering device is a crucial part of the abrasive feeding system. This device, which can be a rotary valve, a vibrating feeder, or a screw conveyor, regulates the flow rate of the shots from the hopper to the blast wheel. Precise control of the abrasive feeding rate is essential. If the rate is too high, the blast wheel may become over loaded, leading to inconsistent shot distribution and reduced efficiency. Conversely, if the feeding rate is too low, the surface treatment process may be incomplete or take longer than necessary.
In many shot blast units, a recycling mechanism is integrated into the abrasive feeding system. After the shots have impacted the workpiece, they fall to the bottom of the unit. Here, they are collected and passed through a series of separation and cleaning processes. The cleaned and sorted shots are then returned to the hopper for reuse. This recycling process not only reduces the cost of the abrasive media but also minimizes waste, making the shot blasting operation more sustainable.
2.3 Blast Chamber
The blast chamber is the enclosed space where the actual shot blasting process takes place. It is designed to contain the high velocity shots and protect the surrounding environment, including operators and other equipment, from the potentially dangerous effects of the shot blasting operation. The blast chamber is typically constructed from thick gauge steel to withstand the impact of the shots.
The interior of the blast chamber is often lined with wear resistant materials. Rubber linings are popular as they can absorb the impact of the shots, reducing noise and protecting the chamber walls from damage. Manganese steel linings are also used, especially in applications where extreme durability is required. These linings need to be periodically inspected for signs of wear and replaced when necessary to ensure the continued safe and efficient operation of the shot blast unit.
The blast chamber is equipped with access points, such as doors or hatches, to allow for the loading and unloading of workpieces. These access points are fitted with safety interlocks to prevent the shot blasting process from starting when the doors are open. In some cases, the blast chamber may be designed with a conveyor system or a robotic arm to automate the handling of workpieces, improving the efficiency of the operation.
2.4 Dust Collection System
During the shot blasting process, a significant amount of dust is generated. This dust is a mixture of abrasive particles, debris from the surface of the workpiece (such as rust, paint flakes, and metal shavings), and in some cases, fine metal particles that are dislodged from the workpiece during the shot blasting operation. The dust collection system is crucial for maintaining a clean and safe working environment.
The dust collection system typically consists of a powerful fan, a series of ducts, and one or more filters. The fan creates a suction force that draws the dust laden air from the blast chamber into the ducts. The ducts direct the air towards the filters, which are designed to trap the dust particles. Cartridge filters and bag filters are commonly used in shot blast units. Cartridge filters offer high efficiency dust removal capabilities and are suitable for applications where strict environmental regulations need to be met. Bag filters, on the other hand, are more cost effective and are often used in less demanding industrial settings.
The collected dust is either stored in a dust bin for periodic disposal or, in some cases, connected to a central dust collection system in a large industrial plant. Regular maintenance of the dust collection system, including filter cleaning and replacement, is essential to ensure its continued effectiveness.
2.5 Workpiece Handling System
The workpiece handling system is responsible for moving the components to be shot blasted in and out of the blast chamber. In small scale shot blast units, this may be a simple manual operation, where an operator uses a hook, a tray, or a small trolley to load and unload the workpieces. However, in large scale industrial applications, more sophisticated workpiece handling systems are employed.
Conveyor based systems are commonly used in high volume production environments. These can be roller conveyors, belt conveyors, or chain conveyors, depending on the size and weight of the workpieces. The conveyors can be designed to move the workpieces through the blast chamber in a continuous or intermittent manner. Overhead cranes are another option for handling large and heavy components. They provide the flexibility to lift and position the workpieces precisely inside the blast chamber.
In modern shot blast units, robotic arms are increasingly being used for workpiece handling. Robotic arms offer high precision movement and can be programmed to perform complex tasks, such as rotating the workpiece to ensure all surfaces are evenly shot blasted. They can also be integrated with other automation systems in the manufacturing plant, further enhancing the overall efficiency of the production process.
2.6 Control Panel
The control panel is the interface between the operator and the shot blast unit. It allows the operator to set and adjust various parameters that govern the shot blasting process. These parameters include the blast wheel speed, the abrasive feeding rate, the duration of the shot blasting cycle, and in some cases, the movement speed of the workpiece handling system.
In older shot blast units, the control panel may consist of a series of knobs, switches, and gauges. However, in modern units, digital interfaces with touch screen capabilities are becoming more prevalent. These digital control panels offer a more user friendly experience, allowing for easy input and adjustment of parameters. They also provide real time feedback on the status of the shot blast unit, such as the remaining quantity of abrasive in the hopper, the temperature of the dust collection system, and any error messages.
The control panel can be integrated with other control systems in the industrial plant, enabling remote monitoring and control of the shot blast unit. This is particularly useful in large scale manufacturing facilities where multiple shot blast units are in operation, and plant managers need to monitor and manage the production process from a central location.
3. Working Principle
The operation of a shot blast unit is based on the principle of high velocity abrasive impact.
1. Abrasive Feeding: Abrasive shots are stored in the hopper of the abrasive feeding system. The metering device regulates the flow of shots from the hopper to the center of the blast wheel assembly. This ensures a consistent supply of shots to the blast wheel at the desired rate.
2. Acceleration in the Blast Wheel: Once the shots enter the blast wheel, the rotating disk and its vanes accelerate them to high velocities using centrifugal force. The speed of the blast wheel can be adjusted according to the specific requirements of the surface treatment task. For example, for heavy duty cleaning, a higher blast wheel speed will result in more forceful impacts on the workpiece.
3. Shot Blasting Process in the Chamber: The high velocity shots are then directed towards the workpiece inside the blast chamber. The impact of the shots on the surface of the workpiece removes contaminants such as rust, paint, scale, and burrs. The shots also impart compressive stresses on the surface, which can improve the fatigue resistance and durability of the material. The layout of the blast wheel and the interior of the blast chamber are designed to ensure that the shots cover the entire surface of the workpiece as uniformly as possible.
4. Dust Collection: As the shots impact the workpiece, dust is generated. The dust collection system, powered by a fan, creates a negative pressure inside the blast chamber. This draws the dust laden air into the ducts, where the dust particles are filtered out, and clean air is released back into the environment.
5. Workpiece Handling: After the shot blasting process is complete, the workpiece handling system removes the treated workpiece from the blast chamber. If there are multiple workpieces to be processed, the handling system ensures the efficient loading and unloading of components, maximizing the productivity of the shot blast unit.
4. Applications
4.1 Automotive Industry
In the automotive industry, shot blast units are used in multiple stages of the manufacturing process. Engine components, such as cylinder heads, engine blocks, and crankshafts, often require thorough cleaning and surface treatment. Shot blasting can effectively remove casting sand, rust, and machining burrs from these components. The compressive stresses imparted by shot blasting improve the fatigue resistance of the engine parts, ensuring their long term durability under the high stress conditions of engine operation.
Automotive body parts, such as doors, hoods, and fenders, are shot blasted before painting. This helps to create a clean and rough textured surface that promotes better adhesion of the paint. A well shot blasted surface can enhance the durability of the paint finish, protecting the body parts from corrosion and improving the overall appearance of the vehicle. In the restoration of classic cars, shot blasting is a valuable technique for removing old paint and rust without causing damage to the original metal structure, preserving the historical value of the vehicle.
4.2 Aerospace Industry
The aerospace industry has stringent quality and safety requirements, and shot blast units play a crucial role in meeting these standards. Aircraft components, such as turbine blades, engine casings, and structural parts, are made of high strength materials that require precise surface treatment. Shot blasting can remove surface imperfections, such as oxidation layers and machining marks, improving the aerodynamic performance and fatigue resistance of the components.
Turbine blades, which operate under extreme temperatures and mechanical stresses, benefit greatly from shot blasting. The process can enhance their resistance to these harsh conditions, ensuring the reliable operation of the aircraft engine. The uniform surface finish achieved through shot blasting is essential in the aerospace industry, as even the slightest surface irregularity can have a significant impact on the performance and safety of the aircraft.
4.3 Construction Industry
In the construction industry, shot blast units are used for cleaning and preparing steel structures. Bridges, buildings, and industrial facilities often have steel components that need to be free of rust, scale, and other contaminants before painting or coating. Shot blasting can effectively remove these impurities, ensuring better adhesion of the protective coatings. This helps to prolong the lifespan of the structures, reducing the need for frequent maintenance and replacement due to corrosion.
In the production of pre fabricated concrete elements, shot blasting can be used to clean and texture the surfaces. This improves the bond between the concrete and other materials, such as steel reinforcement bars, enhancing the structural integrity of the concrete elements.
4.4 Metal Fabrication and Artisanal Metalwork
In metal fabrication workshops, shot blast units are used to clean and finish a wide range of metal products. From small scale metal parts to large scale fabricated structures, shot blasting can improve the surface quality and mechanical properties of the components. For example, in the production of metal furniture, shot blasting can remove any surface defects and create a smooth finish, enhancing the aesthetic appeal of the furniture.
In artisanal metalwork, shot blasting is used to create unique surface textures and finishes. Jewelry makers may use shot blasting to add a satin like or textured finish to metal jewelry pieces, enhancing their visual appeal. Small scale metal artists can also use shot blasting to achieve interesting surface effects on their custom made metal sculptures and decorative items.
5. Advantages
5.1 High Precision Surface Treatment
Shot blast units offer high precision surface treatment. The ability to control parameters such as blast wheel speed, abrasive feeding rate, and shot blasting time allows for customized surface treatment processes. This precision is crucial for applications where surface quality is of utmost importance, such as in the aerospace and automotive industries. The uniform distribution of the abrasive shots ensures consistent surface treatment across the entire workpiece, resulting in high quality finishes.
5.2 Versatility
These units are highly versatile and can be used on a wide variety of materials, including steel, aluminum, cast iron, and non metallic materials such as composites. They can perform multiple surface treatment tasks, such as cleaning, descaling, deburring, and surface hardening. The option to use different types of abrasive media, such as steel shot, aluminum oxide, or glass beads, further expands the versatility of shot blast units. For example, glass beads are often used for a more delicate surface finish on soft metals or for removing paint from sensitive components.
5.3 Cost Effectiveness in the Long Run
Although the initial investment in a shot blast unit can be significant, it is cost effective in the long run. The ability to recycle the abrasive media reduces the ongoing cost of the surface treatment process. The high efficiency of the shot blasting process also reduces the labor cost associated with manual surface treatment methods. Additionally, the improved surface quality and durability of the treated workpieces can lead to cost savings in terms of reduced maintenance and replacement costs over time.
5.4 Safety and Environmentally Friendly Operation
Shot blast units are designed with safety in mind. The blast chamber encloses the high velocity shots, protecting the operator from potential injuries. The dust collection system helps to maintain a clean working environment by trapping and removing the dust generated during the shot blasting process. This not only improves the safety and health of the operators but also reduces the environmental impact of the operation, making it compliant with environmental regulations.
6. Challenges
6.1 High Initial Investment
The purchase and installation of a shot blast unit can be a substantial capital investment. The cost of the unit, including all its components such as the blast wheel assembly, abrasive feeding system, dust collection system, and workpiece handling system, can range from a few thousand dollars for a small, basic unit to hundreds of thousands of dollars for a large, industrial scale unit with advanced features. In addition, there are costs associated with infrastructure development, such as a suitable workspace with proper ventilation, electrical systems to power the unit, and safety measures. Small and medium sized enterprises may find it difficult to afford such high cost equipment, which can limit their growth and competitiveness in the market.
6.2 Maintenance Requirements
Shot blast units require regular maintenance to ensure their optimal performance. The blast wheel vanes, which are constantly in contact with the high velocity shots, need to be replaced periodically due to wear and tear. The abrasive feeding system may experience clogging or other mechanical issues that require maintenance. The dust collection system filters need to be cleaned or replaced regularly to maintain their efficiency. Maintenance can be time consuming and costly, and any downtime due to maintenance can disrupt the production schedule.
6.3 Limited Workpiece Size and Shape Compatibility
The size and shape of the workpiece can pose challenges in shot blast units. Larger workpieces may not fit inside the blast chamber, or it may be difficult to ensure uniform shot blasting coverage. Complex shaped workpieces may require special fixtures or multiple re positionings to ensure all surfaces are treated. In some cases, the design of the shot blast unit may need to be customized to accommodate specific workpiece sizes and shapes, which can add to the cost and complexity of the operation.
6.4 Operator Training
Operating a shot blast unit effectively requires proper training. The operator needs to understand how to set the correct parameters, such as the blast wheel speed, the abrasive feeding rate, and the shot blasting time. Incorrect settings can lead to under treatment or over treatment of the workpieces, resulting in poor product quality. The operator also needs to be aware of safety procedures, such as wearing appropriate personal protective equipment and following proper loading and unloading procedures. Lack of proper training can lead to accidents and reduced productivity.
7. Future Trends
7.1 Integration of Automation and Smart Technologies
The future of shot blast units lies in the integration of automation and smart technologies. Automated workpiece handling systems, such as robotic arms and conveyor belts, will become more prevalent, improving the efficiency and precision of the shot blasting process. Smart sensors will be installed on the unit to monitor various parameters in real time, such as the wear of the blast wheel vanes, the amount of abrasive in the hopper, and the performance of the dust collection system. This data will be analyzed using artificial intelligence and machine learning algorithms to predict maintenance needs, optimize the shot blasting process, and improve overall efficiency.
7.2 Development of Environmentally Friendly Abrasives and Processes
As environmental concerns continue to grow, there will be a greater focus on developing environmentally friendly abrasives and shot blasting processes. New types of biodegradable or recyclable abrasives will be developed, reducing the environmental impact of the shot blasting operation. The dust collection and waste management systems of the shot blast unit will be further improved to meet stricter environmental regulations.