Hotline
+86-136 8495 9862
Email:cennia@szmizhi.com
Add::104,Building 27,Third Industrial Zone, Longxi Community,Longgang District,Shenzhen,China.
Coil Forming & Handling Equipment
Surface Treatment Equipment
Solutions
Application
About Us
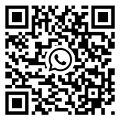
Welcome to MIZHI
For consultation/feedback, please call the service hotline: +86-136 8495 9862 Email:cennia@szmizhi.com
In the world of industrial manufacturing and surface treatment, shot blaster shot plays a crucial role in achieving high-quality finishes and enhancing the durability of various materials. This abrasive medium is widely used in processes such as cleaning, descaling, deburring, and surface hardening. In this in-depth exploration, we will take a closer look at shot blaster shot, its types, applications, advantages, and the impact it has on different industries.
I. Introduction
Shot blasting is a surface treatment process that uses abrasive particles, known as shot blaster shot, to clean and roughen surfaces. The shot is propelled at high velocities onto the workpiece, removing contaminants, rust, scale, and old coatings. This process not only prepares the surface for further processing such as painting, coating, or welding but also improves the adhesion and durability of the applied finishes.
II. Types of Shot Blaster Shot
1. Steel Shot
Steel shot is one of the most commonly used types of shot blaster shot. It is made from high-carbon steel and is available in various sizes and hardness levels. Steel shot is known for its excellent cleaning and peening capabilities, making it suitable for a wide range of applications. It can be used on steel, cast iron, and other ferrous metals to remove rust, scale, and old paint, as well as to improve the surface hardness and fatigue resistance.
2. Stainless Steel Shot
Stainless steel shot is another popular choice for shot blasting. It is made from stainless steel alloys and is resistant to corrosion and oxidation. This makes it ideal for use on stainless steel and other non-ferrous metals, as well as in applications where corrosion resistance is a concern. Stainless steel shot is also available in different sizes and hardness levels, allowing for customization based on the specific requirements of the application.
3. Cast Steel Shot
Cast steel shot is produced by casting molten steel into spherical shapes. It has a rough surface texture, which provides excellent cleaning and peening effects. Cast steel shot is often used in heavy-duty applications where a more aggressive abrasive is needed. It is suitable for removing thick layers of rust, scale, and paint, as well as for surface hardening of large metal components.
4. Aluminum Shot
Aluminum shot is a lightweight abrasive that is commonly used on soft metals such as aluminum, brass, and copper. It is less aggressive than steel shot and is suitable for applications where a gentle cleaning and polishing effect is desired. Aluminum shot is also resistant to corrosion and can be used in environments where moisture and chemicals are present.
5. Glass Bead Shot
Glass bead shot is a non-metallic abrasive that is made from crushed glass. It has a smooth surface texture and is often used for cosmetic finishing and light cleaning applications. Glass bead shot is suitable for use on delicate materials such as plastics, composites, and painted surfaces, as it does not cause damage or distortion. It can also be used to create a matte or satin finish on metal surfaces.
III. Applications of Shot Blaster Shot
1. Automotive Industry
In the automotive industry, shot blaster shot is used for cleaning and preparing metal components such as engine blocks, transmission cases, and suspension parts. It removes rust, scale, and old coatings, ensuring proper adhesion of new paints and coatings. Shot blasting also improves the surface finish of the components, enhancing their aesthetic appeal and durability.
2. Aerospace Industry
The aerospace industry relies on shot blaster shot for surface preparation of aircraft components such as turbine blades, landing gears, and structural parts. The process removes contaminants and surface imperfections, ensuring the integrity and reliability of the components. Shot blasting also helps to improve the fatigue resistance and corrosion resistance of the materials, increasing the lifespan of the aircraft.
3. Construction Industry
In the construction industry, shot blaster shot is used for cleaning and preparing steel structures such as bridges, buildings, and storage tanks. It removes rust, scale, and old coatings, providing a clean and rough surface for the application of new protective coatings. Shot blasting also helps to improve the adhesion of the coatings, enhancing the corrosion resistance and durability of the structures.
4. Shipbuilding Industry
The shipbuilding industry uses shot blaster shot for surface preparation of ship hulls, decks, and other metal components. It removes rust, scale, and marine growth, ensuring a clean and smooth surface for painting and coating. Shot blasting also helps to improve the adhesion of the coatings, protecting the ship from corrosion and wear.
5. Foundry Industry
In the foundry industry, shot blaster shot is used for cleaning and finishing castings. It removes sand, scale, and other contaminants from the surface of the castings, improving their appearance and quality. Shot blasting also helps to remove internal stresses and improve the mechanical properties of the castings.
IV. Advantages of Shot Blaster Shot
1. Efficient Surface Cleaning
Shot blaster shot is highly effective in removing contaminants, rust, scale, and old coatings from various surfaces. The high-velocity impact of the shot breaks down and dislodges the unwanted materials, leaving a clean and smooth surface. This process is much faster and more efficient than traditional cleaning methods such as sanding, grinding, or chemical stripping.
2. Improved Surface Finish
Shot blasting not only cleans the surface but also roughens it, creating a profile that enhances the adhesion of paints, coatings, and other finishes. The rough surface provides a mechanical key for the applied materials, ensuring better bonding and durability. Additionally, shot blasting can be used to create specific surface finishes such as matte, satin, or textured finishes, depending on the type of shot and the blasting parameters.
3. Surface Hardening
The impact of the shot blaster shot can cause plastic deformation and work hardening of the surface layer of the workpiece. This increases the surface hardness and fatigue resistance of the material, improving its durability and performance. Surface hardening is particularly beneficial for applications where the workpiece is subjected to wear, abrasion, or impact.
4. Versatility
Shot blaster shot can be used on a wide range of materials, including steel, cast iron, stainless steel, aluminum, copper, and plastics. It can also be used for different applications, such as cleaning, descaling, deburring, surface hardening, and cosmetic finishing. The versatility of shot blasting makes it a valuable tool in various industries.
5. Environmentally Friendly
Compared to traditional surface treatment methods, shot blasting is relatively environmentally friendly. It does not produce harmful fumes or chemicals, and the spent shot can be recycled and reused. Additionally, shot blasting is a dry process, which reduces the amount of water and waste generated compared to wet processes such as chemical stripping or hydroblasting.
V. Factors to Consider When Choosing Shot Blaster Shot
1. Material to be Treated
The type of material being treated is an important factor to consider when choosing shot blaster shot. Different materials have different hardnesses, compositions, and surface characteristics, which require specific types of shot for optimal results. For example, steel shot may be suitable for treating steel surfaces, while aluminum shot may be better for softer metals such as aluminum or brass.
2. Surface Finish Requirements
The desired surface finish is another important consideration. Different types of shot blaster shot can create different surface finishes, ranging from smooth and polished to rough and textured. Consider the aesthetic and functional requirements of the application to determine the appropriate shot type and blasting parameters.
3. Application Requirements
The specific application requirements, such as cleaning, descaling, deburring, or surface hardening, will also influence the choice of shot blaster shot. Some applications may require a more aggressive abrasive for heavy-duty cleaning, while others may need a gentler shot for cosmetic finishing. Additionally, consider the size and shape of the workpiece, as well as the accessibility of the surface to be treated.
4. Cost Considerations
The cost of shot blaster shot is an important factor to consider, especially for large-scale applications. Different types of shot have different prices, and the cost may also vary depending on the size, hardness, and quality of the shot. Consider the cost-effectiveness of the shot in relation to the desired results and the volume of work to be done.
5. Safety and Environmental Factors
Safety and environmental considerations should also be taken into account when choosing shot blaster shot. Some types of shot may produce dust or noise during the blasting process, which can pose a health hazard to operators. Additionally, consider the environmental impact of the shot, such as its recyclability and disposal methods.
VI. Maintenance and Storage of Shot Blaster Shot
1. Maintenance
To ensure the effectiveness and longevity of shot blaster shot, proper maintenance is essential. After each use, the shot should be screened and cleaned to remove any contaminants or broken pieces. Damaged or worn shot should be replaced to maintain the quality of the blasting process. Additionally, the blasting equipment should be regularly inspected and maintained to ensure proper operation and safety.
2. Storage
Shot blaster shot should be stored in a dry and clean environment to prevent moisture and contaminants from affecting its quality. It should be stored in sealed containers or bins to prevent dust and debris from entering. Avoid stacking the shot too high to prevent crushing and deformation. Additionally, the storage area should be well-ventilated to prevent the buildup of dust and fumes.
VII. Future Trends in Shot Blaster Shot Technology
1. Automation and Robotics
The use of automation and robotics in shot blasting is expected to increase in the future. Automated shot blasting systems can improve productivity, reduce labor costs, and ensure consistent quality. Robotic shot blasters can be programmed to perform complex blasting patterns and can adapt to different workpiece geometries, providing greater flexibility and efficiency.
2. Advanced Materials
The development of new and advanced materials for shot blaster shot is also expected. These materials may offer improved performance, durability, and environmental friendliness. For example, composite shots made from ceramic and metal materials may provide better cleaning and peening effects while being lighter and more durable than traditional steel shots.
3. Environmental Sustainability
As environmental concerns continue to grow, there will be a greater focus on developing environmentally sustainable shot blasting solutions. This may include the use of recycled or biodegradable shot materials, as well as the development of energy-efficient blasting equipment. Additionally, there will be a greater emphasis on reducing dust and noise emissions during the blasting process.
4. Digitalization and Monitoring
The use of digital technologies such as sensors, data analytics, and the Internet of Things (IoT) is expected to transform the shot blasting process. These technologies can be used to monitor and optimize the blasting parameters in real-time, ensuring consistent quality and reducing waste. Additionally, digitalization can enable remote monitoring and control of the blasting process, improving productivity and safety.
VIII. Conclusion
Shot blaster shot is a powerful tool for surface preparation in various industries. Its ability to clean, roughen, and harden surfaces makes it an essential part of many manufacturing and maintenance processes. With a wide range of shot types available and the ability to customize the blasting parameters, shot blasting can be tailored to meet the specific requirements of different applications. As technology continues to advance, we can expect to see further improvements in shot blaster shot technology, making it even more efficient, versatile, and environmentally friendly. Whether it's for automotive, aerospace, construction, shipbuilding, or foundry applications, shot blaster shot is sure to play a crucial role in achieving high-quality finishes and enhancing the durability of materials.