Hotline
+86-136 8495 9862
Email:cennia@szmizhi.com
Add::104,Building 27,Third Industrial Zone, Longxi Community,Longgang District,Shenzhen,China.
Coil Forming & Handling Equipment
Surface Treatment Equipment
Solutions
Application
About Us
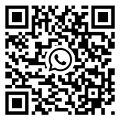
Welcome to MIZHI
For consultation/feedback, please call the service hotline: +86-136 8495 9862 Email:cennia@szmizhi.com
In the world of industrial surface preparation, shot blasters play a crucial role in achieving high-quality finishes and removing contaminants from various surfaces. Whether it's for cleaning metal parts, preparing surfaces for painting, or restoring old structures, a reliable shot blaster can make a significant difference. In this comprehensive article, we will explore the features, benefits, types, and applications of shot blasters for sale, as well as provide tips on choosing the right one for your specific needs.
I. Introduction
Shot blasting is a process that uses abrasive materials, such as steel shot or grit, to clean, roughen, or remove coatings from surfaces. Shot blasters are machines designed to propel these abrasives at high velocities onto the surface being treated, creating a mechanical impact that effectively cleans and prepares the surface. With the increasing demand for efficient surface preparation methods, shot blasters have become an essential tool in many industries.
II. Features of Shot Blasters for Sale
1. High-Efficiency Cleaning
Shot blasters are known for their ability to quickly and effectively clean surfaces. The high-velocity impact of the abrasive materials removes rust, scale, dirt, and old coatings, leaving a clean and smooth surface ready for further processing. This efficiency makes shot blasters ideal for large-scale industrial applications where time is of the essence.
2. Versatility
Shot blasters can be used on a wide variety of surfaces, including metal, concrete, wood, and composites. They can handle different types of contaminants and coatings, making them suitable for a diverse range of industries such as automotive, aerospace, construction, and manufacturing. Additionally, shot blasters can be adjusted to different settings to achieve different levels of surface roughness, depending on the specific requirements of the application.
3. Durability and Reliability
Shot blasters are built to withstand the rigors of industrial use. They are made from high-quality materials and are designed to operate continuously for long periods without breakdowns. This durability and reliability ensure that businesses can rely on shot blasters to maintain a consistent level of productivity and quality.
4. User-Friendly Operation
Modern shot blasters are designed with user convenience in mind. They often feature intuitive controls, easy-to-adjust settings, and safety features that make them easy to operate even for inexperienced users. Some shot blasters also come with automated functions, such as programmable blasting cycles and self-cleaning systems, which further enhance their ease of use.
5. Environmental Friendliness
Many shot blasters for sale today are designed to be environmentally friendly. They are equipped with dust collection systems that capture and filter the abrasive dust generated during the blasting process, reducing air pollution and protecting the health of operators. Additionally, some shot blasters use recycled abrasive materials, minimizing waste and reducing the environmental impact of the surface preparation process.
III. Benefits of Owning a Shot Blaster for Sale
1. Cost Savings
Investing in a shot blaster can lead to significant cost savings in the long run. By performing surface preparation in-house, businesses can avoid outsourcing costs and have more control over the quality and timing of the process. Additionally, shot blasters are highly efficient, reducing the time and labor required for surface preparation, which can result in lower overall production costs.
2. Improved Quality
Shot blasters provide a superior level of surface preparation compared to traditional methods such as sanding or grinding. The high-velocity impact of the abrasive materials creates a uniform and consistent surface finish, enhancing the adhesion of paints, coatings, and other finishes. This results in improved product quality and durability, reducing the likelihood of defects and rework.
3. Increased Productivity
With their high efficiency and versatility, shot blasters can significantly increase productivity. They can handle large volumes of work quickly, allowing businesses to complete projects faster and meet tight deadlines. Additionally, shot blasters can be integrated into production lines, streamlining the surface preparation process and reducing downtime.
4. Flexibility
Owning a shot blaster gives businesses the flexibility to handle a wide range of surface preparation tasks. They can be used for different types of projects, from small-scale repairs to large industrial applications. This flexibility allows businesses to adapt to changing market demands and take on new projects without having to rely on external contractors.
5. Enhanced Safety
Shot blasters are designed with safety in mind. They are equipped with safety features such as guards, emergency stop buttons, and dust collection systems to protect operators from potential hazards. Additionally, by using a shot blaster, businesses can reduce the need for manual labor, minimizing the risk of injuries associated with traditional surface preparation methods.
IV. Types of Shot Blasters for Sale
1. Wheel Blasters
Wheel blasters use a spinning wheel to propel the abrasive materials onto the surface being treated. They are available in different sizes and configurations, ranging from small portable units to large industrial models. Wheel blasters are known for their high productivity and are suitable for applications where large volumes of work need to be completed quickly.
2. Air Blasters
Air blasters use compressed air to propel the abrasive materials. They are lightweight and portable, making them ideal for use in confined spaces or on-site jobs. Air blasters are also relatively inexpensive compared to other types of shot blasters, making them a popular choice for small businesses and hobbyists.
3. Centrifugal Blasters
Centrifugal blasters use a centrifugal force to accelerate the abrasive materials. They are highly efficient and can handle a wide variety of abrasive materials, making them suitable for different types of surfaces and applications. Centrifugal blasters are often used in the automotive and aerospace industries for surface preparation of complex parts.
4. Tumblast Blasters
Tumblast blasters are designed to process large quantities of small parts. They work by tumbling the parts in a chamber along with the abrasive materials, ensuring that all surfaces are evenly blasted. Tumblast blasters are commonly used in the foundry industry for cleaning castings.
V. Applications of Shot Blasters for Sale
1. Automotive Industry
In the automotive industry, shot blasters are used for cleaning and preparing metal parts such as engine blocks, transmission cases, and suspension components. They remove rust, scale, and old coatings, providing a clean surface for painting or other finishing processes. Shot blasters are also used for restoring old classic cars and refurbishing damaged body panels.
2. Aerospace Industry
The aerospace industry requires high-quality surface preparation for aircraft components. Shot blasters are used to remove contaminants, improve surface roughness, and enhance adhesion of coatings on parts such as turbine blades, landing gears, and fuselage sections. The precision and efficiency of shot blasters make them essential tools in the aerospace manufacturing process.
3. Construction Industry
In the construction industry, shot blasters are used for cleaning and preparing concrete surfaces before painting or applying coatings. They remove dirt, grease, and old coatings, creating a rough surface that promotes better adhesion of the new finish. Shot blasters are also used for restoring old buildings and removing graffiti from walls.
4. Manufacturing Industry
Shot blasters are widely used in the manufacturing industry for surface preparation of various metal parts. They are used to deburr, clean, and roughen surfaces, improving the quality and appearance of the finished products. Shot blasters can handle different shapes and sizes of parts, making them suitable for a wide range of manufacturing processes.
5. Foundry Industry
In the foundry industry, shot blasters are used for cleaning castings after they are removed from the molds. They remove sand, scale, and other contaminants, leaving a smooth surface ready for further processing. Shot blasters are also used for fettling, which involves removing excess material and smoothing the edges of castings.
VI. Factors to Consider When Buying a Shot Blaster for Sale
1. Surface Requirements
Consider the type of surface you will be treating and the specific requirements for surface roughness and cleanliness. Different shot blasters are designed for different applications, so it's important to choose one that is suitable for your specific needs. For example, if you are working with delicate materials or require a very smooth finish, you may need a shot blaster with adjustable settings and a gentle abrasive.
2. Production Volume
Determine the volume of work you need to process and choose a shot blaster that can handle your production requirements. If you have a large volume of work, you may need a larger, more powerful machine with a high throughput. On the other hand, if you have only occasional small jobs, a smaller, portable shot blaster may be more suitable.
3. Budget
Set a budget for your shot blaster purchase and consider the cost of the machine, as well as any additional expenses such as abrasive materials, maintenance, and operating costs. While it's important to find a machine that fits your budget, don't sacrifice quality and performance for a lower price. Consider the long-term cost savings and benefits of investing in a reliable and efficient shot blaster.
4. Brand and Reputation
Research different brands and manufacturers of shot blasters and choose one with a good reputation for quality and reliability. Look for reviews and testimonials from other users to get an idea of the performance and durability of the machine. A reputable brand will often provide better customer support and warranty options.
5. Safety Features
Ensure that the shot blaster you choose has adequate safety features to protect operators from potential hazards. Look for features such as guards, emergency stop buttons, and dust collection systems. Additionally, make sure that the machine is easy to operate and maintain, reducing the risk of accidents and injuries.
VII. Maintenance and Care of Shot Blasters for Sale
1. Regular Cleaning
After each use, clean the shot blaster thoroughly to remove any abrasive materials, dust, and debris. This will prevent clogging and ensure optimal performance. Use a brush or compressed air to clean the machine's internal components and the blasting chamber.
2. Inspect and Replace Parts
Regularly inspect the shot blaster for any signs of wear or damage. Check the abrasive wheels, nozzles, hoses, and filters, and replace any worn or damaged parts promptly. This will prevent breakdowns and ensure consistent performance.
3. Lubrication
Lubricate the moving parts of the shot blaster regularly to reduce friction and wear. Follow the manufacturer's instructions for the proper lubrication points and types of lubricants to use.
4. Store Properly
When not in use, store the shot blaster in a dry, clean place. Protect it from moisture, dust, and extreme temperatures. Cover the machine with a protective cover or store it in a cabinet to prevent damage.
5. Training and Safety
Provide proper training to operators on how to use and maintain the shot blaster safely. Ensure that they are familiar with the machine's controls, safety features, and operating procedures. Follow all safety guidelines and wear appropriate personal protective equipment when operating the shot blaster.
VIII. Conclusion
Shot blasters for sale offer a powerful and efficient solution for surface preparation in various industries. With their high-efficiency cleaning, versatility, durability, and user-friendly operation, shot blasters can enhance productivity, improve quality, and reduce costs. When choosing a shot blaster, consider your surface requirements, production volume, budget, brand reputation, and safety features. Proper maintenance and care will ensure the longevity and optimal performance of your shot blaster. Whether you are in the automotive, aerospace, construction, manufacturing, or foundry industry, a shot blaster can be a valuable investment for your business.