Hotline
+86-136 8495 9862
Email:cennia@szmizhi.com
Add::104,Building 27,Third Industrial Zone, Longxi Community,Longgang District,Shenzhen,China.
Coil Forming & Handling Equipment
Surface Treatment Equipment
Solutions
Application
About Us
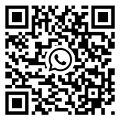
Welcome to MIZHI
For consultation/feedback, please call the service hotline: +86-136 8495 9862 Email:cennia@szmizhi.com
1. Introduction
In the intricate landscape of modern manufacturing and materials engineering, the quality and durability of components are of utmost importance. Shot peening equipment has emerged as a critical technology in enhancing the performance and lifespan of various mechanical parts. This specialized equipment is designed to bombard the surface of a workpiece with a stream of small, spherical particles, known as shot. The high - velocity impact of the shot on the surface induces compressive stresses, which significantly improve the fatigue resistance, stress corrosion cracking resistance, and overall mechanical properties of the material. From aerospace components that endure extreme mechanical and environmental conditions to automotive parts that require long - term reliability, shot peening equipment has found its application in a wide range of industries, playing a pivotal role in ensuring the safety and efficiency of countless products.
2. Working Principle
2.1 The Impact of Shot
At the core of shot peening equipment is the principle of mechanical impact. The shot, typically made of materials such as steel, glass, or ceramic, is propelled at high velocities towards the surface of the workpiece. The velocity of the shot can range from tens to hundreds of meters per second, depending on the type of equipment and the application requirements. When the shot strikes the surface, it creates a small indentation. This indentation causes plastic deformation in the surface layer of the workpiece. As multiple shots impact the surface, a complex network of overlapping indentations is formed.
The plastic deformation beneath the surface leads to the generation of compressive stresses. These compressive stresses act as a protective layer, counteracting the tensile stresses that can cause fatigue cracks to initiate and propagate. For example, in a turbine blade of a jet engine, which is constantly subjected to high - stress cyclic loading during operation, the compressive stresses induced by shot peening can prevent the formation of cracks that could ultimately lead to catastrophic failure.
2.2 Shot Propulsion Methods
There are two main methods of shot propulsion in shot peening equipment: centrifugal wheel and air - blast. In centrifugal - wheel - based shot peening machines, the shot is fed into the center of a high - speed rotating wheel. As the wheel spins, the shot is flung outwards along the vanes of the wheel, achieving high velocities. The speed of the wheel and the design of the vanes can be adjusted to control the velocity and distribution of the shot. This method is highly efficient for large - scale production and is often used in industries with high - volume component processing, such as the automotive industry.
Air - blast shot peening, on the other hand, uses compressed air to accelerate the shot. The shot is mixed with compressed air in a nozzle, and the high - pressure air stream propels the shot towards the workpiece. Air - blast systems offer more precise control over the shot peening process, as the pressure of the air and the flow rate of the shot can be easily adjusted. This makes air - blast shot peening suitable for applications where a high degree of accuracy is required, such as in the aerospace industry, where components often have complex geometries and tight tolerances.
2.3 Shot Selection and Recycling
The choice of shot material is crucial for the effectiveness of the shot peening process. Steel shot is commonly used for general - purpose applications due to its high hardness and durability. It can be heat - treated to achieve different levels of hardness, making it suitable for a wide range of materials and applications. Glass shot, on the other hand, is often used when a more gentle peening action is required, such as for soft metals or components with thin walls. Ceramic shot is known for its high hardness and wear resistance, making it ideal for applications where extreme durability is needed.
Shot recycling is an important aspect of shot peening equipment operation. After the shot has impacted the workpiece, it is collected and recycled. Most shot peening machines are equipped with a shot - recovery system, which separates the spent shot from the debris and dust generated during the peening process. The recycled shot is then re - used, reducing the cost of the shot peening process and minimizing waste. However, over time, the shot may become worn or contaminated, and it may need to be periodically replaced to ensure consistent peening results.
3. Types of Shot Peening Equipment
3.1 Static Shot Peening Machines
Static shot peening machines are designed for applications where the workpiece remains stationary during the peening process. These machines are typically used for large - sized components or components with complex geometries that are difficult to move. In a static machine, the shot is directed towards the workpiece using fixed nozzles or centrifugal wheels. The operator can adjust the position of the nozzles or the orientation of the wheel to ensure that all areas of the workpiece are properly peened. Static shot peening machines are often used in the manufacturing of large - scale industrial machinery, such as power generation equipment and heavy - duty construction machinery.
3.2 Rotary Shot Peening Machines
Rotary shot peening machines are suitable for components that can be rotated during the peening process. The workpiece is mounted on a rotating fixture, and the shot is directed towards the rotating component. This type of machine allows for uniform peening of the entire surface of the workpiece, as the rotation ensures that all areas are exposed to the shot stream. Rotary shot peening machines are commonly used in the automotive industry for peening components such as crankshafts, camshafts, and gears. The continuous rotation of these components enables efficient and consistent peening, improving their fatigue resistance and performance.
3.3 Automated Shot Peening Systems
Automated shot peening systems are becoming increasingly popular in modern manufacturing. These systems are equipped with advanced control technologies, such as programmable logic controllers (PLCs) and robotic arms. The PLC controls the operation of the shot peening equipment, including the shot propulsion, shot flow rate, and peening time. Robotic arms are used to handle the workpiece, moving it in and out of the peening area and positioning it precisely for optimal peening. Automated shot peening systems offer high - precision and repeatability, making them ideal for high - volume production and applications where consistent quality is crucial. They are widely used in industries such as aerospace, where the strictest quality standards must be met.
4. Applications across Industries
4.1 Aerospace Industry
In the aerospace industry, shot peening equipment is used extensively to enhance the performance and reliability of aircraft components. Turbine blades, which are subjected to extreme mechanical stresses, high temperatures, and corrosive environments, are shot - peened to improve their fatigue resistance and resistance to stress corrosion cracking. The compressive stresses induced by shot peening can prevent the formation of cracks that could lead to blade failure, ensuring the safety of the aircraft.
Aircraft structural components, such as wing spars and fuselage frames, also benefit from shot peening. These components are often made of lightweight alloys, which are more prone to fatigue. Shot peening can increase the fatigue life of these components, allowing for longer service intervals and reduced maintenance costs. In addition, shot peening can be used to improve the surface finish of aerospace components, reducing air resistance and improving fuel efficiency.
4.2 Automotive Industry
The automotive industry relies on shot peening equipment to improve the performance and durability of various components. Engine components, such as crankshafts, connecting rods, and valves, are shot - peened to enhance their fatigue strength. These components are subjected to high - stress cyclic loading during engine operation, and shot peening can significantly increase their lifespan. For example, a shot - peened crankshaft can withstand higher loads and rotational speeds, reducing the risk of failure and improving the overall performance of the engine.
Automotive suspension components, such as control arms and springs, also benefit from shot peening. The compressive stresses induced by shot peening can improve the fatigue resistance of these components, ensuring a smooth and safe ride. In addition, shot peening can be used to improve the surface quality of automotive components, enhancing their aesthetic appeal and corrosion resistance.
4.3 Metalworking and Manufacturing Industry
In the metalworking and manufacturing industry, shot peening equipment is used for a variety of applications. Metal forgings and castings often have surface imperfections and residual stresses. Shot peening can remove these imperfections and relieve the residual stresses, improving the mechanical properties of the components. For example, in the production of metal gears, shot peening can improve the tooth surface quality, reducing wear and improving the efficiency of power transmission.
Shot peening can also be used to enhance the bonding strength of coatings and adhesives. By creating a rough and compressive - stressed surface, shot peening can improve the adhesion of paints, primers, and other coatings, ensuring a more durable and long - lasting finish. This is particularly important in applications where the components are exposed to harsh environmental conditions.
5. Advantages of Shot Peening Equipment
5.1 Improved Fatigue Resistance
One of the most significant advantages of shot peening equipment is its ability to improve the fatigue resistance of components. The compressive stresses induced by shot peening act as a barrier to the initiation and propagation of fatigue cracks. This results in a significant increase in the fatigue life of the components, allowing them to withstand more cycles of stress before failure. For example, in a mechanical component that is subjected to cyclic loading, such as a bridge support or a wind turbine component, shot peening can extend its service life by several times, reducing the need for frequent replacements and maintenance.
5.2 Enhanced Stress Corrosion Cracking Resistance
Shot peening can also improve the resistance of components to stress corrosion cracking. In corrosive environments, tensile stresses can accelerate the formation and growth of cracks. The compressive stresses induced by shot peening counteract these tensile stresses, making it more difficult for cracks to form and propagate. This is particularly important in industries such as aerospace and marine, where components are often exposed to harsh corrosive environments. For example, in a ship's hull, which is constantly exposed to seawater, shot - peened components can resist stress corrosion cracking, ensuring the integrity of the vessel.
5.3 Surface Hardening and Work - Hardening
The impact of the shot on the surface of the workpiece causes work - hardening, which increases the hardness of the surface layer. This surface hardening can improve the wear resistance and scratch resistance of the components. For example, in a metal cutting tool, shot peening can harden the surface, allowing it to cut more efficiently and last longer. In addition, the work - hardening effect can also improve the surface finish of the components, making them more aesthetically pleasing.
5.4 Non - Destructive and Cost - Effective
Shot peening is a non - destructive surface treatment method, which means that it does not remove material from the workpiece. This is in contrast to other surface treatment methods, such as machining or grinding, which can reduce the thickness of the component. Shot peening is also a cost - effective method, as it can significantly improve the performance and lifespan of components, reducing the need for expensive replacements. In addition, the recycling of shot reduces the cost of the shot peening process, making it an environmentally friendly and cost - efficient option.
6. Challenges and Solutions in Shot Peening Equipment Operation
6.1 Shot Wear and Contamination
Over time, the shot used in shot peening equipment can become worn or contaminated. Worn shot may have a reduced impact energy, leading to inconsistent peening results. Contaminated shot, such as shot that has picked up debris or oil from the workpiece, can also affect the quality of the peening process. To address this challenge, regular inspection and maintenance of the shot are necessary. Shot should be periodically replaced when it shows signs of excessive wear or contamination. In addition, shot - cleaning systems can be used to remove debris and contaminants from the shot, ensuring its consistent performance.
6.2 Process Control and Quality Assurance
Maintaining consistent process control and quality assurance in shot peening can be challenging. Factors such as shot velocity, shot flow rate, and peening time can all affect the quality of the peening process. To ensure consistent results, it is important to use advanced control systems, such as PLCs and sensors. These systems can monitor and adjust the peening parameters in real - time, ensuring that the process is carried out within the specified tolerances. In addition, regular quality checks, such as hardness testing and surface roughness measurement, should be performed to verify the effectiveness of the shot peening process.
6.3 Equipment Maintenance and Safety
Shot peening equipment is subject to wear and tear due to the high - velocity impact of the shot. The components of the equipment, such as the shot - propulsion system, the shot - recovery system, and the nozzles or wheels, need to be regularly maintained and replaced when necessary. In addition, safety is a crucial aspect of shot peening equipment operation. The high - velocity shot can be dangerous if not properly contained. Equipment should be equipped with safety features, such as guards and interlocks, to prevent accidents. Operators should also be trained on proper safety procedures to ensure their own safety and the safety of others in the workplace.
7. Future Trends in Shot Peening Equipment Technology
7.1 Advanced Process Monitoring and Control
The future of shot peening equipment lies in advanced process monitoring and control technologies. Sensors will be used to monitor the shot velocity, shot flow rate, and the surface condition of the workpiece in real - time. This data will be used to adjust the peening parameters automatically, ensuring consistent and optimal peening results. In addition, artificial intelligence and machine learning algorithms may be applied to analyze the data and predict the performance of the shot peening process, allowing for proactive maintenance and process optimization.
7.2 Development of New Shot Materials
New shot materials with improved properties are likely to be developed in the future. These materials may have higher hardness, better wear resistance, or unique chemical properties that can enhance the shot peening process. For example, nanocomposite shot materials may be developed, which can combine the advantages of different materials at the nanoscale to achieve superior peening performance. The development of new shot materials will open up new possibilities for shot peening applications and improve the overall efficiency and effectiveness of the process.
7.3 Integration with Additive Manufacturing
As additive manufacturing (3D printing) continues to grow in popularity, shot peening equipment may be integrated with additive manufacturing processes. Components produced by additive manufacturing often have unique surface characteristics and residual stress distributions. Shot peening can be used to improve the surface quality and mechanical properties of these components. Integrating shot peening equipment into the additive manufacturing workflow can provide a seamless solution for surface treatment, ensuring the quality and performance of 3D - printed components.
In conclusion, shot peening equipment is a vital technology in modern manufacturing, offering a wide range of benefits in terms of surface enhancement and component performance improvement. While there are challenges associated with its operation, ongoing technological advancements are addressing these issues and driving the development of more efficient and effective shot peening solutions. As industries continue to demand higher - performance components, shot peening equipment will play an increasingly important role in meeting these requirements.