Hotline
+86-136 8495 9862
Email:cennia@szmizhi.com
Add::104,Building 27,Third Industrial Zone, Longxi Community,Longgang District,Shenzhen,China.
Coil Forming & Handling Equipment
Surface Treatment Equipment
Solutions
Application
About Us
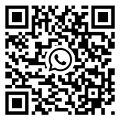
Welcome to MIZHI
For consultation/feedback, please call the service hotline: +86-136 8495 9862 Email:cennia@szmizhi.com
1. Introduction
In the dynamic world of industrial manufacturing, slitting line machines have emerged as indispensable tools. These machines play a pivotal role in transforming large coils of materials, such as metals, plastics, and paper, into narrower strips of specific widths. The slitting process is not only about cutting but also about ensuring precision, efficiency, and quality in the production of various products. From the automotive industry, where precision - cut metal strips are used for components, to the packaging industry, which relies on accurately slit paper and plastic films, slitting line machines are the workhorses behind the scenes.
2. Components of a Slitting Line Machine
2.1. Uncoiler
The uncoiler is the starting point of the slitting line process. It holds the large, heavy coil of material, which can range from a few hundred kilograms to several tons, depending on the industry and application. There are different types of uncoilers, including fixed - type and movable - type. Fixed uncoilers are suitable for operations where the coil size and weight are relatively consistent. They are cost - effective and easy to maintain. Movable uncoilers, on the other hand, offer greater flexibility. They can be adjusted to accommodate coils of different diameters and weights. This is particularly useful in industries with a wide variety of coil sizes, such as the steel service centers. Advanced uncoilers are equipped with automatic tension control systems. These systems ensure that the material is unwound at a constant speed and with the right amount of tension. If the tension is too high, the material may stretch or break; if it is too low, the material may sag, leading to inaccuracies in the slitting process.
2.2. Straightening and Leveling Units
Before the material reaches the slitting section, it often needs to be straightened and leveled. This is especially crucial for materials like metal coils, which may have some curvature or unevenness due to the coiling process or transportation. The straightening and leveling units consist of multiple rollers arranged in a specific pattern. As the material passes through these rollers, the rollers apply pressure to straighten and flatten the material. For example, in a steel slitting line, the straightening and leveling unit may have a series of hardened steel rollers. The number of rollers and their diameter can vary depending on the thickness and type of material. Thicker materials may require fewer but larger - diameter rollers, while thinner materials may need more rollers with smaller diameters to achieve the desired flatness. Some advanced straightening and leveling units also use sensors to detect any remaining imperfections in the material and make real - time adjustments to the roller pressure.
2.3. Slitter Head
The slitter head is the heart of the slitting line machine. It is responsible for making the precise cuts to divide the wide material into narrower strips. The slitter head typically consists of multiple sets of circular blades or rotary knives. These blades are made of high - quality materials, such as hardened steel or carbide, to ensure durability and sharpness. The number of blades and their spacing can be adjusted according to the desired width of the slit strips. For example, if a manufacturer needs to produce strips of different widths from a single coil of metal, the slitter head can be reconfigured by changing the position of the blades and adding or removing spacer rings. There are two main types of slitting methods: shear slitting and score slitting. Shear slitting involves the use of two sets of blades that shear the material as it passes through. This method is suitable for a wide range of materials, including metals, plastics, and paper. Score slitting, on the other hand, uses a single blade to score the material, which is then broken along the scored line. Score slitting is often used for more brittle materials, such as certain types of plastics.
2.4. Recoiler
After the material has been slit into the desired strips, the recoiler winds each strip into a smaller coil. The recoiler plays a crucial role in ensuring that the slit strips are wound neatly and tightly. It has a variable - speed motor that can adjust the winding speed according to the speed of the slitting process. This ensures that the tension in the strips is maintained during the winding process. The recoiler also has a mechanism to control the diameter of the wound coils. This is important because different applications may require coils of specific diameters. Some recoilers are equipped with an automatic coil - transfer system. Once a coil is fully wound, the system automatically transfers the coil to a pallet or another storage area, allowing the recoiler to start winding the next coil without interruption. This significantly increases the productivity of the slitting line.
2.5. Scrap Winder
During the slitting process, some material on the edges of the coil, known as trim or scrap, is removed. The scrap winder is responsible for collecting and compressing this scrap material for recycling or disposal. The scrap winder typically consists of a rotating drum or spool. As the scrap material is produced, it is guided onto the drum and wound around it. The drum is often powered by a motor, which can be adjusted to control the speed of the scrap winding. In some cases, the scrap winder may also be equipped with a cutting mechanism. This mechanism cuts the scrap material into smaller pieces, making it easier to handle and transport. For example, in a metal slitting line, the scrap winder may cut the metal scrap into small, manageable pieces that can be easily recycled.
2.6. Control System
Modern slitting line machines are equipped with sophisticated control systems. These control systems are typically based on programmable logic controllers (PLCs) or industrial computers. The control system allows operators to set various parameters, such as the width of the slit strips, the cutting speed, the tension of the material, and the winding speed of the recoiler. For example, an operator can input the desired strip width on a touch - screen interface, and the control system will automatically adjust the position of the blades in the slitter head. The control system also monitors the operation of the machine in real - time. It uses sensors to detect any abnormalities, such as changes in tension, speed, or temperature. If an issue is detected, the control system can automatically stop the machine or make adjustments to prevent damage to the machine or the material. Some advanced control systems also have remote - monitoring capabilities. This allows plant managers or maintenance personnel to monitor the performance of the slitting line machine from a remote location, such as an office or a control room.
3. Working Principles of Slitting Line Machines
3.1. Tension Control
Tension control is a critical aspect of the slitting process. The material needs to be fed through the machine with a consistent and appropriate level of tension. If the tension is too high, the material may stretch, which can affect its dimensional accuracy and mechanical properties. In the case of metal strips, excessive stretching can lead to a reduction in thickness and strength. On the other hand, if the tension is too low, the material may sag or wrinkle, causing problems in the slitting and winding processes. To achieve proper tension control, slitting line machines use a combination of sensors and actuators. Load cells are often used to measure the tension in the material. These sensors send signals to the control system, which then adjusts the speed of the uncoiler, the straightening and leveling units, and the recoiler to maintain the desired tension. For example, if the load cell detects that the tension is too high, the control system may increase the speed of the uncoiler or decrease the speed of the recoiler to reduce the tension.
3.2. Blade Configuration and Cutting Process
The configuration of the blades in the slitter head is carefully designed to ensure clean and accurate cuts. The blades are usually mounted on a shaft, and the distance between the blades is adjusted to match the desired width of the slit strips. The blades are sharpened to a high degree of precision to minimize the amount of burrs or rough edges on the cut material. In shear slitting, the two sets of blades work together to shear the material. The upper blade and the lower blade are offset slightly, creating a shearing action as the material passes through. The cutting force is carefully controlled to ensure that the material is cut cleanly without causing excessive stress or deformation. In score slitting, the single blade scores the material, creating a weak line. The material is then broken along this scored line, either by the tension in the material or by a separate breaking mechanism. The depth of the score is carefully adjusted to ensure that the material breaks cleanly without cracking or splintering.
3.3. Speed Synchronization
Speed synchronization is essential for the smooth operation of a slitting line machine. The uncoiler, straightening and leveling units, slitter head, and recoiler all need to operate at coordinated speeds. If the speeds are not synchronized, it can lead to problems such as material jams, inconsistent strip widths, or uneven winding. The control system of the slitting line machine is responsible for maintaining speed synchronization. It uses encoders, which are devices that measure the rotational speed of motors or shafts, to monitor the speeds of the different components. The control system then adjusts the speeds of the motors driving these components to ensure that they are in sync. For example, if the speed of the uncoiler starts to increase, the control system will also increase the speeds of the straightening and leveling units, the slitter head, and the recoiler to keep the material flowing smoothly through the machine.
4. Types of Slitting Line Machines
4.1. Light - Duty Slitting Line Machines
Light - duty slitting line machines are designed to handle thin and lightweight materials, such as paper, thin plastic films, and some lightweight metals. These machines are often used in industries such as packaging, printing, and electronics. For example, in the packaging industry, light - duty slitting line machines are used to slit rolls of paper or plastic films into narrower widths for use in making bags, labels, or wrapping materials. Light - duty slitting line machines are typically smaller in size and have lower power requirements compared to heavy - duty machines. They are also more affordable, making them suitable for small - to - medium - sized businesses. The cutting speed of light - duty slitting line machines can be relatively high, as the materials they process are easy to cut. However, they may not be able to handle materials with high tensile strength or thickness.
4.2. Medium - Duty Slitting Line Machines
Medium - duty slitting line machines are capable of handling a wider range of materials, including thicker papers, medium - gauge plastics, and some non - ferrous metals. These machines are used in industries such as furniture manufacturing, automotive parts production, and general metalworking. In the furniture industry, medium - duty slitting line machines may be used to slit wooden veneers or thin metal sheets for decorative purposes. In the automotive industry, they can be used to produce metal strips for various components, such as door panels or interior trim. Medium - duty slitting line machines are more robustly built than light - duty machines. They have higher - power motors and stronger cutting mechanisms to handle the increased thickness and toughness of the materials. The precision of medium - duty slitting line machines is also relatively high, as they need to meet the quality requirements of the industries they serve.
4.3. Heavy - Duty Slitting Line Machines
Heavy - duty slitting line machines are designed for processing thick and heavy materials, such as steel coils, aluminum plates, and heavy - gauge plastics. These machines are essential in industries such as steel manufacturing, construction, and large - scale automotive production. In the steel industry, heavy - duty slitting line machines are used to slit large coils of steel into narrower strips for further processing, such as making steel pipes or structural components. Heavy - duty slitting line machines are massive in size and require a significant amount of power to operate. They are built with heavy - duty frames, high - strength blades, and powerful motors to handle the high - stress cutting process. The control systems of heavy - duty slitting line machines are also more advanced, as they need to manage the complex operations involved in processing thick and heavy materials. These machines often have features such as automatic blade adjustment, high - precision tension control, and advanced safety systems.
4.4. Specialized Slitting Line Machines
In addition to the general - purpose light - duty, medium - duty, and heavy - duty slitting line machines, there are also specialized slitting line machines designed for specific applications. For example, there are slitting line machines for slitting non - metallic materials with unique properties, such as fiberglass or carbon fiber. These machines need to be designed to handle the abrasive nature of these materials without causing excessive wear to the blades. There are also slitting line machines for slitting materials with special coatings or finishes. These machines need to ensure that the cutting process does not damage the coating or finish. In the food and pharmaceutical industries, there are slitting line machines that are designed to meet strict hygiene and cleanliness requirements. These machines are made of materials that are easy to clean and sanitize, and they often have enclosed designs to prevent contamination.
5. Applications of Slitting Line Machines
5.1. Metalworking Industry
In the metalworking industry, slitting line machines are used in a wide variety of applications. They are used to produce metal strips for automotive components, such as car body panels, engine parts, and interior trim. The precision of the slitting process ensures that the metal strips fit together perfectly during the assembly of the automotive parts. In the construction industry, slitting line machines are used to produce metal strips for roofing, wall cladding, and structural components. The ability to slit metal coils into custom - sized strips allows for greater flexibility in construction projects. In the manufacturing of electrical appliances, slitting line machines are used to produce metal strips for components such as refrigerator doors, washing machine drums, and oven racks. The high - speed and high - precision cutting capabilities of slitting line machines enable manufacturers to meet the high - volume production requirements of the electrical appliance industry.
5.2. Packaging Industry
The packaging industry relies heavily on slitting line machines. They are used to slit rolls of paper, plastic films, and aluminum foils into narrower widths for use in making various packaging products. For example, slitting line machines are used to produce the paper strips for paper bags, the plastic films for food packaging, and the aluminum foils for pharmaceutical packaging. The ability to produce consistent and accurate strip widths is crucial in the packaging industry, as it ensures the proper fit and functionality of the packaging products. In addition, the high - speed operation of slitting line machines allows for efficient production, which is essential in meeting the high - volume demands of the packaging market.
5.3. Textile and Fibre Industry
In the textile and fibre industry, slitting line machines are used to slit rolls of fabrics, non - woven materials, and fibres into narrower widths. This is useful for producing materials for clothing, upholstery, industrial fabrics, and medical textiles. For example, slitting line machines can be used to slit large rolls of fabric into narrower strips for making clothing panels. In the production of non - woven materials, such as disposable wipes or filter materials, slitting line machines are used to cut the rolls into the desired widths. The precision of the slitting process in the textile and fibre industry is important to ensure the quality and appearance of the final products.
5.4. Electronics Industry
The electronics industry also benefits from the use of slitting line machines. They are used to slit materials such as copper foils, insulating films, and printed circuit board (PCB) materials. Copper foils are slit into narrow strips for use in the production of electrical conductors in electronic devices. Insulating films are slit to the appropriate widths for use in protecting and insulating electronic components. In the production of PCBs, slitting line machines are used to cut the large sheets of PCB materials into smaller, more manageable sizes. The high - precision cutting capabilities of slitting line machines are essential in the electronics industry, as even the slightest deviation in the width of the slit materials can affect the performance of the electronic devices.
6. Maintenance and Troubleshooting of Slitting Line Machines
6.1. Regular Maintenance
Regular maintenance is essential to keep a slitting line machine operating at peak performance. This includes routine inspection of all components, such as the uncoiler, straightening and leveling units, slitter head, recoiler, and scrap winder. The blades in the slitter head should be inspected regularly for sharpness and wear. Dull blades can cause poor - quality cuts, increased burrs, and higher energy consumption. When the blades are worn, they should be sharpened or replaced. The rollers in the straightening and leveling units and the recoiler should also be inspected for wear and misalignment. Worn rollers can cause the material to be unevenly straightened or wound. Lubrication of moving parts, such as bearings, gears, and shafts, is crucial. Proper lubrication reduces friction, extends the lifespan of the components, and improves the overall efficiency of the machine. The control system of the slitting line machine should also be maintained. This includes checking for software updates, ensuring that the sensors are working properly, and testing the emergency stop systems.
6.2. Troubleshooting Common Issues
Some common issues that may occur with a slitting line machine include inaccurate strip widths, burrs on the cut edges, material jams, and problems with the tension control. Inaccurate strip widths may be due to incorrect blade alignment, worn blades, or problems with the control system. If the blades are not aligned properly, the strips may be cut wider or narrower than the desired width. Worn blades can also cause inconsistent cutting widths. To troubleshoot this issue, the blades should be checked and realigned or replaced if necessary. Burrs on the cut edges can be caused by dull blades, incorrect blade clearance, or excessive cutting force. Dull blades do not cut the material cleanly, leaving burrs. Incorrect blade clearance can also lead to burrs, as the material may not be sheared properly. To solve this problem, the blades should be sharpened or replaced, and the blade clearance should be adjusted. Material jams can occur if the material is not fed properly through the machine, if there is debris in the machine, or if there is a problem with the speed synchronization of the components. To prevent material jams, the machine should be cleaned regularly, and the speed synchronization should be checked and adjusted. Problems with the tension control can lead to stretching or sagging of the material. If the tension is too high, the material may stretch, and if the tension is too low, the material may sag. To troubleshoot tension control issues, the sensors and actuators in the tension control system should be checked, and the control parameters should be adjusted.
7. Future Trends in Slitting Line Machines
7.1. Automation and Smart Technology Integration
The future of slitting line machines lies in increased automation and the integration of smart technologies. More advanced robotic systems will be used for tasks such as coil loading, unloading, and strip handling. Internet of Things (IoT) sensors will be installed throughout the machine to monitor the performance of each component in real - time. This data can be analyzed to predict maintenance needs,