Hotline
+86-136 8495 9862
Email:cennia@szmizhi.com
Add::104,Building 27,Third Industrial Zone, Longxi Community,Longgang District,Shenzhen,China.
Coil Forming & Handling Equipment
Surface Treatment Equipment
Solutions
Application
About Us
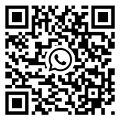
Welcome to MIZHI
For consultation/feedback, please call the service hotline: +86-136 8495 9862 Email:cennia@szmizhi.com
In the world of metal processing, slitting line machine manufacturers play a crucial role in providing advanced and efficient solutions for businesses across various industries. These manufacturers are constantly striving to innovate and improve their products to meet the evolving needs of their customers and keep up with the latest technological advancements.
I. Introduction to Slitting Line Machine Manufacturers
Slitting line machines are essential equipment in the metal processing industry, used for cutting large coils of metal into narrower strips. These machines are widely used in industries such as steel manufacturing, automotive, construction, and appliance production.
Slitting line machine manufacturers design, manufacture, and supply these machines to customers around the world. They offer a wide range of models and configurations to meet the specific requirements of different applications and production volumes.
These manufacturers employ a team of highly skilled engineers, technicians, and sales professionals who are dedicated to providing high-quality products and excellent customer service. They work closely with their customers to understand their needs and provide customized solutions that meet their specific requirements.
II. The Manufacturing Process of Slitting Line Machines
The manufacturing process of slitting line machines involves several stages, including design, engineering, fabrication, assembly, and testing.
1. Design and Engineering: The first stage in the manufacturing process is the design and engineering phase. Manufacturers use advanced computer-aided design (CAD) and computer-aided manufacturing (CAM) software to create detailed designs of the slitting line machines. These designs take into account factors such as the type of metal to be processed, the required strip widths and thicknesses, and the production volume.
2. Fabrication: Once the design is finalized, the fabrication process begins. This involves cutting, bending, and welding of steel and other materials to create the various components of the slitting line machine. Manufacturers use high-quality materials and advanced fabrication techniques to ensure the durability and reliability of their machines.
3. Assembly: After the fabrication process is complete, the components are assembled into a complete slitting line machine. This involves installing motors, gears, rollers, and other mechanical and electrical components. Manufacturers use precision assembly techniques to ensure that the machine operates smoothly and accurately.
4. Testing: Before the slitting line machine is shipped to the customer, it undergoes extensive testing to ensure that it meets the required performance and quality standards. This includes testing of the mechanical and electrical systems, as well as the cutting and slitting accuracy. Manufacturers use advanced testing equipment and procedures to ensure that their machines are reliable and perform as expected.
III. The Importance of Quality Control in Slitting Line Machine Manufacturing
Quality control is a critical aspect of slitting line machine manufacturing. Manufacturers must ensure that their machines are of the highest quality and meet the strictest industry standards to ensure reliable and efficient operation.
1. Material Selection: Manufacturers use high-quality materials such as steel, aluminum, and copper to ensure the durability and reliability of their machines. They source these materials from reliable suppliers and conduct rigorous quality checks to ensure that they meet the required specifications.
2. Manufacturing Processes: Manufacturers use advanced manufacturing processes such as laser cutting, CNC machining, and robotic welding to ensure precision and consistency in the production of their machines. They also implement strict quality control procedures at each stage of the manufacturing process to ensure that any defects are detected and corrected early on.
3. Testing and Inspection: Manufacturers conduct extensive testing and inspection of their machines before shipping them to the customer. This includes testing of the mechanical and electrical systems, as well as the cutting and slitting accuracy. They also perform visual inspections to ensure that the machine is free from any defects or damages.
4. Customer Feedback: Manufacturers value customer feedback and use it to continuously improve their products. They listen to their customers' concerns and suggestions and incorporate them into their design and manufacturing processes to ensure that their machines meet the evolving needs of their customers.
IV. The Role of Technology in Slitting Line Machine Manufacturing
Technology plays a crucial role in the manufacturing of slitting line machines. Manufacturers are constantly investing in research and development to incorporate the latest technological advancements into their products.
1. Automation: Automation is becoming increasingly important in slitting line machine manufacturing. Manufacturers are incorporating advanced automation systems such as programmable logic controllers (PLCs), human-machine interfaces (HMIs), and robotic systems to improve the efficiency and accuracy of their machines. These automation systems can perform tasks such as coil loading and unloading, strip cutting and slitting, and coil stacking, reducing the need for manual labor and increasing productivity.
2. Digitalization: Digitalization is also playing a significant role in slitting line machine manufacturing. Manufacturers are using digital technologies such as CAD/CAM software, 3D printing, and virtual reality to design, prototype, and test their machines. These technologies allow for faster and more accurate design and development, reducing the time and cost involved in the manufacturing process.
3. Internet of Things (IoT): The IoT is enabling manufacturers to connect their slitting line machines to the internet and collect real-time data on their performance. This data can be used to optimize the operation of the machines, predict maintenance needs, and improve overall productivity. Manufacturers are also using the IoT to provide remote monitoring and support to their customers, ensuring that their machines are operating smoothly and efficiently.
V. The Future of Slitting Line Machine Manufacturing
The future of slitting line machine manufacturing looks bright, with continued innovation and technological advancements expected in the coming years.
1. Increased Automation: Automation will continue to play a major role in slitting line machine manufacturing, with more advanced robotic systems and artificial intelligence (AI) being incorporated into the machines. These technologies will enable the machines to perform more complex tasks and improve productivity even further.
2. Digitalization and Connectivity: Digitalization and connectivity will become even more important, with manufacturers using advanced software and sensors to monitor and optimize the performance of their machines in real-time. The IoT will also enable manufacturers to provide more personalized and efficient customer service, as they will be able to remotely monitor and support their machines.
3. Sustainable Manufacturing: As the world becomes more focused on sustainability, slitting line machine manufacturers will need to develop more environmentally friendly and energy-efficient machines. This may involve the use of renewable energy sources, such as solar and wind power, as well as the implementation of energy-efficient manufacturing processes.
4. Customization and Flexibility: Customers will continue to demand more customized and flexible slitting line machines that can meet their specific needs. Manufacturers will need to be able to offer a wide range of options and configurations to meet these demands, while still maintaining high quality and reliability.
In conclusion, slitting line machine manufacturers play a crucial role in the metal processing industry. They are constantly striving to innovate and improve their products to meet the evolving needs of their customers and keep up with the latest technological advancements. With continued investment in research and development, these manufacturers are well-positioned to drive innovation and growth in the metal processing industry for years to come.
Title: Steel Slitting Line Machine: An In - depth Analysis
I. Introduction
A steel slitting line machine is a specialized piece of industrial equipment that plays a crucial role in the steel processing industry. It is designed to convert wide coils of steel into narrower coils or strips, which are more suitable for various applications. This process of slitting steel is essential in industries such as automotive, construction, and manufacturing, as it provides the necessary steel products in the desired widths and lengths.
II. Components of a Steel Slitting Line Machine
1. Uncoiling System
- The uncoiling system is the starting point of the steel slitting line machine. It is responsible for holding and unwinding the large steel coil. The uncoiling system typically consists of a mandrel, which is a shaft on which the coil is mounted. The mandrel must be strong enough to support the weight of the steel coil, which can be quite substantial depending on the size of the coil. There are also braking mechanisms associated with the uncoiling system. These brakes are used to control the unwinding speed of the coil. If the brakes are not functioning properly, the coil may unwind too quickly, leading to issues such as material slack or excessive tension. Tension control devices are also an important part of the uncoiling system. They ensure that the steel is under the correct tension as it is being unwound. This is crucial because improper tension can cause the steel to stretch or deform, which will affect the quality of the slitting process.
2. Slitting Section
- The slitting section is the heart of the steel slitting line machine. In this section, the wide steel coil is cut into narrower strips. There are different types of slitting methods used in this section. One common method is rotary slitting. In rotary slitting, circular blades are used to cut the steel. These blades are mounted on shafts and rotate at a high speed. The rotary slitting mechanism is suitable for slitting relatively thin steel sheets. Another method is shear slitting, which is more suitable for thicker steel sheets. In shear slitting, two blades move relative to each other in a shearing motion to cut through the steel. The slitting section also requires precise blade alignment. Any misalignment can result in inaccurate slitting, leading to strips with uneven widths or rough edges. To ensure accurate slitting, the slitting section may be equipped with alignment systems, such as laser - guided alignment or mechanical alignment devices.
3. Recoiling System
- After the steel has been slit, the recoiling system is responsible for winding the slit steel strips back into coils. The recoiling system consists of a mandrel on which the slit steel is wound. Similar to the uncoiling mandrel, the recoiling mandrel needs to be strong and well - designed. Tension control is also crucial in the recoiling system. If the tension is not properly maintained, the resulting coil may be loose or have an inconsistent winding density. There are various methods for tension control in the recoiling system, such as using load cells to measure the tension and adjusting the winding speed accordingly. Additionally, the recoiling system may include edge - guiding devices. These devices help to keep the slit steel centered during the recoiling process, ensuring that the coil is wound evenly across its width.
4. Material Handling and Conveying Components
- Between the uncoiling, slitting, and recoiling systems, there are material handling and conveying components. These include guide rollers, which help to guide the steel through the slitting line. The guide rollers are designed to minimize friction and ensure smooth movement of the steel. There are also conveyor belts or chains in some slitting lines, which are used to transport the steel from one section to another. In a steel slitting line machine, these components need to be able to handle the heavy and rigid nature of the steel without causing any damage or disruption. For example, the guide rollers need to be made of high - quality materials with a smooth surface finish to reduce friction and wear.
III. Control Systems in Steel Slitting Line Machines
1. Programmable Logic Controllers (PLCs)
- Programmable Logic Controllers (PLCs) play a vital role in the control of steel slitting line machines. PLCs are used to manage various aspects of the machine's operation. They can control the uncoiling speed, slitting speed, and recoiling speed. For example, a PLC can be programmed to adjust the uncoiling speed based on the diameter of the coil being unwound. As the coil diameter decreases, the uncoiling speed may need to be adjusted to maintain a constant feed rate to the slitting section. PLCs can also control the cutting parameters in the slitting section. They can ensure that the slitting blades are rotating at the correct speed and that the cutting force is appropriate for the steel being slit. In the recoiling system, PLCs can control the tension and the winding speed to produce high - quality coils. Additionally, PLCs are used for safety - related functions, such as emergency stop procedures and interlocking between different components to prevent accidental operation.
2. Human - Machine Interfaces (HMIs)
- Human - Machine Interfaces (HMIs) provide an interface between the operators and the steel slitting line machine. Through the HMI, operators can set various parameters for the slitting line. For example, they can set the desired slitting widths, the production speed, and the number of coils to be produced. The HMI also displays real - time information about the status of the slitting line. This includes information such as the current uncoiling speed, slitting speed, and recoiling speed. It can also show the status of each component, such as whether a blade needs to be replaced or if there is a problem with the tension control. Modern HMIs are often touch - screen based, making it easy for operators to interact with the slitting line and monitor its performance.
3. Sensor - based Feedback Control
- Sensor - based feedback control is essential for the accurate operation of steel slitting line machines. There are various types of sensors used in these machines. For example, photoelectric sensors are used to detect the presence and position of the steel. These sensors can be used to ensure that the steel is properly aligned during the slitting process. Load cells are used to measure the tension in the steel. The data from these sensors is fed back to the control system, usually the PLC. Based on this feedback, the control system can make real - time adjustments to optimize the operation of the slitting line. For example, if a load cell detects that the tension in the steel is too high, the PLC can adjust the speed of the uncoiling or recoiling system to reduce the tension.
IV. Advantages of Steel Slitting Line Machines
1. Customization of Steel Dimensions
- One of the main advantages of steel slitting line machines is their ability to customize the dimensions of steel. They can slit wide coils of steel into narrower strips of various widths according to the specific requirements of different industries. For example, in the automotive industry, different parts may require steel strips of different widths for manufacturing components such as car body panels or engine parts. In the construction industry, steel strips of specific widths may be needed for roofing or siding applications. This customization ability allows for more efficient use of steel and reduces waste.
2. High - quality Output
- Steel slitting line machines are designed to produce high - quality slit steel. The precise slitting mechanisms, along with the advanced control systems, ensure that the slit steel strips have accurate widths and smooth edges. This high - quality output is crucial in industries where the dimensional accuracy and surface finish of the steel are important. For example, in the manufacturing of precision machinery or high - end consumer products, the quality of the steel used can significantly affect the performance and appearance of the final product.
3. Cost - effectiveness
- Although the initial investment in a steel slitting line machine may be significant, in the long run, it can be cost - effective. The ability to customize steel dimensions reduces material waste, as only the required amount of steel in the desired widths is produced. Additionally, the high - quality output reduces the need for rework or rejection of products due to poor - quality steel. This saves on both material and labor costs in the long term.
V. Applications of Steel Slitting Line Machines in Different Industries
1. Automotive Industry
- In the automotive industry, steel slitting line machines are used extensively. They are used to slit steel coils for the production of various car components. For example, they can slit steel for car body panels, which require precise widths and high - quality surface finishes. The slit steel can also be used for manufacturing engine parts, such as crankshafts or camshafts, where the dimensional accuracy of the steel is crucial. Additionally, in the production of automotive interiors, steel slitting line machines can be used to produce steel strips for seat frames or dashboard components.
2. Construction Industry
- The construction industry is another major user of steel slitting line machines. They are used to slit steel for roofing and siding materials. For roofing, the steel needs to be slit into specific widths to fit the roof structure properly. In siding applications, the slit steel provides a durable and aesthetically pleasing material. Steel slitting line machines can also be used to slit steel for structural components in buildings, such as beams or columns, where the strength and dimensional accuracy of the steel are of utmost importance.
3. Manufacturing Industry
- In the manufacturing industry, steel slitting line machines are used for a wide variety of applications. They can be used to slit steel for the production of machinery parts, such as gears or shafts. The ability to produce steel strips of precise widths and high - quality is essential for the proper functioning of these parts. Additionally, in the production of consumer products, such as appliances or furniture, steel slitting line machines can be used to slit steel for components such as frames or panels.
VI. Challenges and Solutions in Steel Slitting Line Machine Operation
1. Blade Wear and Replacement
- One of the major challenges in steel slitting line machine operation is blade wear. The slitting blades are subject to significant wear due to the hardness of the steel being cut. Blade wear can lead to a decrease in slitting quality, such as producing strips with rough edges or inaccurate widths. To address this, high - quality blades made of durable materials should be used. For example, carbide - tipped blades are often used for slitting steel. Regular blade inspection and replacement are also necessary. Some steel slitting line machines are equipped with blade - monitoring systems that can detect when a blade needs to be replaced based on factors such as blade wear or vibration.
2. Tension Control
- Tension control is a crucial aspect of steel slitting line machine operation. Improper tension can cause a variety of problems, such as steel stretching, wrinkling, or misalignment. Maintaining the correct tension throughout the uncoiling, slitting, and recoiling processes is challenging. To address this, advanced tension control systems, such as those based on load cells and PID controllers, are used. These systems can measure the tension in real - time and make adjustments to the speed of the relevant components (such as the uncoiling or recoiling motors) to maintain the correct tension.
3. Alignment and Straightness of Steel
- Ensuring the alignment and straightness of the steel during the slitting process is also a challenge. If the steel is not properly aligned or straight, it can lead to inaccurate slitting and poor - quality output. To address this, the slitting line machine is equipped with alignment and guiding devices. For example, guide rollers are used to keep the steel in the correct position, and some machines may use laser - guided alignment systems to ensure precise alignment of the steel during slitting.
VII. Future Trends in Steel Slitting Line Machines
1. Automation and Robotics
- The future of steel slitting line machines will see increased automation and the integration of robotics. Robotic arms can be used for tasks such as loading and unloading steel coils, which can improve safety and efficiency. Automation can also be extended to the slitting process itself, with the ability to automatically adjust slitting parameters based on real - time data from sensors. This will further increase the precision and productivity of steel slitting line machines.
2. Integration with Industry 4.0
- Steel slitting line machines will be increasingly integrated with Industry 4.0 concepts. This means that they will be connected to the factory's overall network, allowing for real - time data sharing. Operators will be able to remotely monitor and control the slitting line, and predictive maintenance will become more common. Sensors on the line will be able to detect potential problems before they cause a breakdown, and the necessary maintenance can be scheduled in advance.
3. Advanced Materials and Slitting Technologies
- As new materials are developed in the steel industry, steel slitting line machines will need to adapt. For example, the development of high - strength and lightweight steels will require new slitting technologies. Laser - slitting technology may become more prevalent in steel slitting line machines as it offers high - precision slitting for a wide range of steels. Additionally, new blade materials and designs may be developed to improve slitting efficiency and quality.
In conclusion, steel slitting line machines are a vital part of the steel processing industry. Their ability to convert wide steel coils into narrower strips with high - quality and customization capabilities makes them indispensable in various industries. As technology continues to evolve, these machines will continue to improve and adapt to meet the ever - changing needs of the manufacturing world.